Finishing Options
- sebastiaan56
- Blackwood
- Posts: 1274
- Joined: Sun Oct 28, 2007 5:23 am
- Location: Blue Mountains
Ive also had mixed results with Wattyl Estapol Tung Oil, I think its for floors, I swooged the first couple of coats with blonde shellac and really spirited off to get it nice and shiny and then overcoated with the Tung Oil. Four coats wiped on. It appears to be very hard, but a bit dull. I polished it with some Meguiars #7 and then Carnuba but its still a bit flat.
I think Tru Oil is great but a bit exy for me at the moment, I havent tried the revised Hard Shellac. I look forward to your comments Graham.
I think Tru Oil is great but a bit exy for me at the moment, I havent tried the revised Hard Shellac. I look forward to your comments Graham.
make mine fifths........
-
- Blackwood
- Posts: 115
- Joined: Tue Dec 09, 2008 1:15 pm
I had exactly the same question but, like Graham, was unable to get them on the phone, their preferred method of contact!It has a use-by date of 3/2010, and I was wondering in anybody knew when Ubeaut started using the new formula? No-one answering the phone there this morning.
My own bottle has the same use-by date as Graham's and after reading on their web site later that it has a shelf life of 18 months, I figure it must have been bottled in September 2008, well after the introduction of the plasticiser.
I was a little inattentive yesterday while spraying a 2 pound cut, and lingered momentarily with the gun over a very small area of the headstock. I knew at once that the finish had been laid on too thickly as it sagged there very slightly. Within minutes it had crazed! I managed a thin even coat over the rest of the neck and it looks just fine.
I'm not about blame the product for my sloppy technique yesterday. No product is entirely forgiving and I'm sure it'll be a matter of refining my spraying technique and getting to know what the Hard Shellac will and won't put up with. The jury is definitely still out, and will be for some time.
Last edited by Pete Brown on Mon Jan 12, 2009 6:32 pm, edited 1 time in total.
- ozziebluesman
- Blackwood
- Posts: 1554
- Joined: Wed Oct 10, 2007 9:12 am
- Location: Townsville
- Contact:
- graham mcdonald
- Blackwood
- Posts: 473
- Joined: Thu Oct 25, 2007 11:57 am
- Location: Canberra
- Contact:
I got onto Carol's woodwork supply who sold me the bottle, and they said it turns over pretty quickly and that batch would have only come in a few weeks ago. A good warning about spraying it on too thick. From memory I cut the last lot a fair bit with alcohol to spray it, probably to about 2 parts HS to 1 part alcohol. The trick with spraying ordinary shellac I have found in the past is to use minimum pressure, otherwise the alcohol could evaporate before it hit the surface and you end up with lots of little dried lumps of shellac and not much else.
I saw something recently about using acetone to thin shellac for spraying. Can't find the reference, but does anyone know anything about this?
cheers
graham
I saw something recently about using acetone to thin shellac for spraying. Can't find the reference, but does anyone know anything about this?
cheers
graham
Graham McDonald
http://www.mcdonaldstrings.com
http://www.mcdonaldstrings.com
- DarwinStrings
- Blackwood
- Posts: 1873
- Joined: Thu Nov 13, 2008 10:27 pm
- Location: Darwin
I agree with you here in part John. Also with Peters wife in that if you find a product that works, well, then sell it, after all you are the builder and should be prepared to stand behind your product.John FM wrote:I am reckoning that if it's good enough for preserving gun stocks that get a fair bit of rough treatment, why not apply it to instruments!!
Guns stock or solid body guitars. Same difference, a chunk of hardwood. My problem with oils is when you apply it to softwood acoustic soundboards.
I have been putting tung oil on coffee tables and kitchen bench tops for 17 years. Not the type of tung oil that Sebastiaan is talking about as most tung oils are mixed with linseed or other oils (to make them easier to use) then a solvent like mineral turps or naptha(white spirits). I buy pure tung oil which is nothing but oil straight from the nut and has no know toxicity. As a solvent I choose gum turps but you can use anything really, nasty old naptha seems to be a popular choice.
Tung oil is said to be the hardest and most water resistant of all wood finishing oils and is also easy to repair. Kitchen bench tops that i made 15 years ago are still in service as well as coffee tables that cop a beating.
Here is a solid body that I have used pure tung oil on. I sanded the wood then used a grain filler but wiped it back hard as I wanted the grain to show then put on 15 coats of the oil, one per day hand rubbed with no sanding or leveling between coats, you can get away with 5 coats but the more you put the harder it gets. I then let it harden and buffed it.
The pic with the tape in it is the gloss at 45 degrees and the other pic is about 30 degrees.
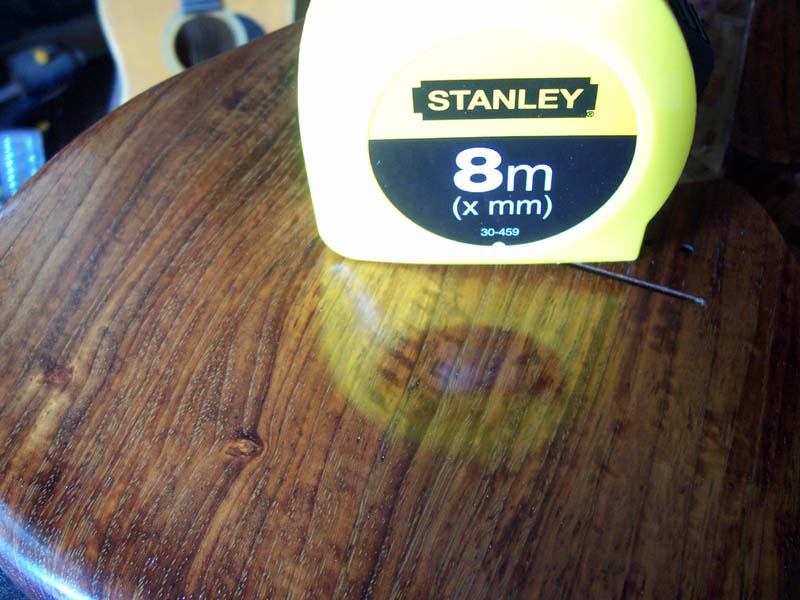
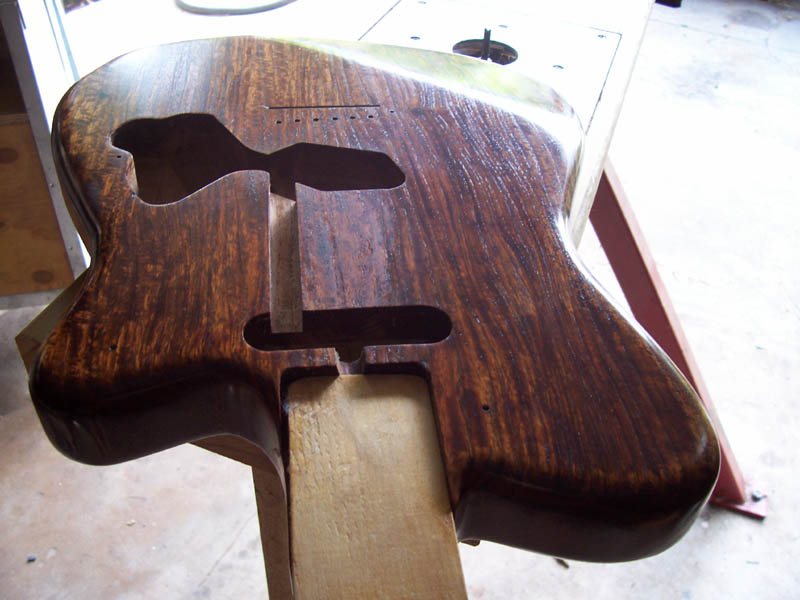
These new shellacs are sounding good too if they dont react with sweat and the humidity of the tropics.
Jim
Graham, you've stopped me in my tracks.
I'm off to Sydney on Saturday and was planning to stop by Durobond for NitroC & now I'm wondering if I should wait and see how the Ubeaut Hard Shellac turns out for you.
I'd like to see it get sprayed if I'm able. Are you cutting the Ubeaut with 95% metho or have you found a source of 100%.
By the way, I'm also planning on stopping at Gilet's on Monday if you need me to get you anything.
I'm off to Sydney on Saturday and was planning to stop by Durobond for NitroC & now I'm wondering if I should wait and see how the Ubeaut Hard Shellac turns out for you.
I'd like to see it get sprayed if I'm able. Are you cutting the Ubeaut with 95% metho or have you found a source of 100%.
By the way, I'm also planning on stopping at Gilet's on Monday if you need me to get you anything.
- Bob Connor
- Admin
- Posts: 3115
- Joined: Mon Jul 09, 2007 9:43 pm
- Location: Geelong, Australia
- Contact:
It was around Feb 2008 Graham.Graham McDonald wrote:I have got a new bottle of Hard Shellac and I will start on the mandolin in the next week or so. It has a use-by date of 3/2010, and I was wondering in anybody knew when Ubeaut started using the new formula? No-one answering the phone there this morning. It might well have been me who first asked the question about the crazing. It was mid 2007 and they sounded very surprized at the very idea that such crazing could happen. It had to be entirely my fault for spraying it too thickly. As you can imagine I was fairly underwhelmed by their attitude, but the potential for such a product is just too good to dismiss it. Someone did mention that Shines have a similar product out, but I haven't chased it down.
Another very simple finish to consider is Minwax Wipe-on Poly. Bunnings stock it! I used the satin version of it over zpoxy on a guitar with it recently and it is very simple to use. They suggest just using a piece of cloth to apply it and sanding between coats. That left noticeable scratches to I put it on with 600grit wet&dry and it came up very well. If anything a bit too flat, but that could be sorted with some wax I figure. Don't know about the gloss version.
cheers
graham
Here is a link to the post I put up shortly after meeting with Neil Ellis to discuss the problem with him.
viewtopic.php?t=414
They are not a large factory. There's just Neil and his wife so he is a bit hard to get hold of at times.
I had problems with it that became apparent some 12 months after applying it. We also tried all manner of thinning it before spraying but the crazing problem still occurred.
I had every intention of trying the new batches but got busy and the Mirotone was working well so I haven't revisited it. I will at some stage when I get unbusy.
- sebastiaan56
- Blackwood
- Posts: 1274
- Joined: Sun Oct 28, 2007 5:23 am
- Location: Blue Mountains
TruOil dries hard and doesnt seem to soak very deeply.Toejam wrote:My problem with oils is when you apply it to softwood acoustic soundboards.
Ive just been googling it and there is apparently a risk for those with nut allergies. I find this rather curious as allergenic reactions are normally to proteins, Ive never heard of them from pure oils. Is the oil you use clear Jim?I buy pure tung oil which is nothing but oil straight from the nut and has no know toxicity.
Im very interested to hear how the Hard Shellac performs,
make mine fifths........
-
- Blackwood
- Posts: 115
- Joined: Tue Dec 09, 2008 1:15 pm
TruOil dries hard and doesnt seem to soak very deeply.
My first introduction to Tru-Oil was in the old LMI catalogue which contained an in depth article on using Tru-Oil as an open pore finish, i.e., no pore fill at all on any part of the instrument.
The secret where soundboards is concerned is to wipe the oil onto a small area at a time and immediately wipe off as much as you can in an effort to minimise penetration - you are not trying for a finish build at all.
Much of that article is redundant now that epoxy pore fills are widely used, but for soundboards, it's still relevant.
As if there weren't enough products in the mix, the gunsmith who let me have a small quantity of Tru-Oil some time ago told me he much prefers the oil finishes made by Livos for his high-end gun stocks. I think he uses their Kunos product. They're completely non-toxic and non-allergenic and he reckons they're more durable than Tru-Oil.
Quite a while back someone at the OLF posted the results of an experiment measuring the penetration of True-Oil on spruce. They tried various application methods and then cut the spruce to try and measure the penetration in cross section.
From memory this experiment was done by one of our British friends, or it was one of them which had posted the results. Anyhow, the bottom line was that the penetration was minimal. It would appear that True-Oil is more incline to sit on rather than soak into spruce.
As a precaution, I wiped my top with a very thin wash coat of white dewaxed shellac prior to application and remain confident that the oil has not penetrated the soundboard at all. I have used Tung Oil before and I have used Tung Oil mixed in with polyurethane too, but True-Oil must have some special kind of driers added because it dries much quicker than any other rub finish I have used.
Cheers
Kim
From memory this experiment was done by one of our British friends, or it was one of them which had posted the results. Anyhow, the bottom line was that the penetration was minimal. It would appear that True-Oil is more incline to sit on rather than soak into spruce.
As a precaution, I wiped my top with a very thin wash coat of white dewaxed shellac prior to application and remain confident that the oil has not penetrated the soundboard at all. I have used Tung Oil before and I have used Tung Oil mixed in with polyurethane too, but True-Oil must have some special kind of driers added because it dries much quicker than any other rub finish I have used.
Cheers
Kim
- DarwinStrings
- Blackwood
- Posts: 1873
- Joined: Thu Nov 13, 2008 10:27 pm
- Location: Darwin
Hmmm interesting I guess that makes pure tung oil as dangerous as peanut butter
. Pure tung oil is FDA food contact approved what ever that means when its at home. I don't think you are supposed to drink it though.
Could I have the link to what you read about allergic reaction to tung oil please Sebastiaan, I had read something on it years ago but the jury was still out and I can't find anything at the moment.
The colour is like a light tan oil colour.
Tung oil also dries hard, much harder than linseed which is what Tru-oil is made from. For me they just are not hard enough to offer the sort of protection that Nitro or other lacquers offers for soundboards.
Jim


Could I have the link to what you read about allergic reaction to tung oil please Sebastiaan, I had read something on it years ago but the jury was still out and I can't find anything at the moment.
The colour is like a light tan oil colour.
Tung oil also dries hard, much harder than linseed which is what Tru-oil is made from. For me they just are not hard enough to offer the sort of protection that Nitro or other lacquers offers for soundboards.
Jim
-
- Blackwood
- Posts: 115
- Joined: Tue Dec 09, 2008 1:15 pm
- DarwinStrings
- Blackwood
- Posts: 1873
- Joined: Thu Nov 13, 2008 10:27 pm
- Location: Darwin
Oops, sorry Pete, I have been calling you "peter" as I thought your were "Peter Brown" from the woodwork forums
Kim, why don't you want the oil to penetrate the soundboard?
Even the solvents they put in many of those oil finishes help them to dry faster and also Tru-oil states that it is a mixture of linseed and "natural" oils and I know that some products use other oils to speed drying, orange oil is one that is used in some products.
Jim

Kim, why don't you want the oil to penetrate the soundboard?
Even the solvents they put in many of those oil finishes help them to dry faster and also Tru-oil states that it is a mixture of linseed and "natural" oils and I know that some products use other oils to speed drying, orange oil is one that is used in some products.
Jim
I was wondering if anyone has experimented with some of the old traditional varnishes? The old German luthier who got started used shellac as his standard finish but made a bunch of varnishes and finishing oils for special applications. Some, like the amber oil finish, were diabolical concoctions that took a lot of time and effort to make, but others, like copal varnish, weren’t much harder to brew up than shellac. Copal varnish (spirit based) would be harder than shellac and depending on the colour of the copal you use it would be between white and blonde shellac. Mixed 50/50 with white shellac it is as easy to rub on as a French polish.
Graham… The hide glue I got from Gerard last year was the less processed variety used for furniture construction. I guess it does the job but the 192 GS high clarity stuff is considered the best for stringed instruments. It has a bit longer open time, less smell and you aren’t as likely to notice glue lines on tops or backs. All in all I found it much better to use and well worth the few extra dollars. The only places I've found that sell this grade in Australia are Schreuders Music on Ebay or Australian Luthiers Supplies.
Graham… The hide glue I got from Gerard last year was the less processed variety used for furniture construction. I guess it does the job but the 192 GS high clarity stuff is considered the best for stringed instruments. It has a bit longer open time, less smell and you aren’t as likely to notice glue lines on tops or backs. All in all I found it much better to use and well worth the few extra dollars. The only places I've found that sell this grade in Australia are Schreuders Music on Ebay or Australian Luthiers Supplies.
Good question Jim,Toejam wrote: Kim, why don't you want the oil to penetrate the soundboard?
Jim
Being someone who has invested a lot of time and effort over the last few years trying to learn and understand all I can about building a steel stringed acoustic guitar, I feel that if I am going to take the time to carefully select, or in some instances, just dump cash on the table in the blind hope that I will be sent the best soundboard material for my guitars, and, then I am going to apply hard won knowledge and acquired skills to the best of my ability in hope that this combination of understanding, theories, and hand skills will allow me to judge the thinning and carving of a top and it's braces to reveal it's full potential. It seems counter productive to me to add yet another confounding variable into the mix which has the potential to not only add more mass than is absolutely necessary to protect my work, but also risk altering the responsiveness I most careful set out to achieve in the first instance.
Seriously not trying to be a smart arse here Jim, it's just honestly how I feel about the process.
Cheers M8
Kim
Last edited by Kim on Mon Jan 12, 2009 11:09 pm, edited 2 times in total.
- John Maddison
- Blackwood
- Posts: 354
- Joined: Tue Jun 03, 2008 11:15 pm
- Location: Albany, Western Australia
- Contact:
- DarwinStrings
- Blackwood
- Posts: 1873
- Joined: Thu Nov 13, 2008 10:27 pm
- Location: Darwin
- DarwinStrings
- Blackwood
- Posts: 1873
- Joined: Thu Nov 13, 2008 10:27 pm
- Location: Darwin
John it comes from,
http://www.thewoodworks.com.au/site/
They have stuff that I can't find anywhere else, even aniline dye which I almost gave up on finding in Australia.
Jim
http://www.thewoodworks.com.au/site/
They have stuff that I can't find anywhere else, even aniline dye which I almost gave up on finding in Australia.
Jim
-
- Blackwood
- Posts: 115
- Joined: Tue Dec 09, 2008 1:15 pm
Fair call Pete,Pete Brown wrote:C'mon guys - this is a finishing thread!
I have deleted those post from this thread which had gone off track about rabbit glue and moved them via quote to the new topic stated by Graham to keep the peace which is specifically about hide glue. Thanks Graham

viewtopic.php?p=15711#15711
Cheers
Kim
-
- Blackwood
- Posts: 115
- Joined: Tue Dec 09, 2008 1:15 pm
Graham, I did a search over on the OLF and found the following comments from Robbie O'Brien concerning the Miniwax poly:Another very simple finish to consider is Minwax Wipe-on Poly. Bunnings stock it! I used the satin version of it over zpoxy on a guitar with it recently and it is very simple to use.
Wipe on poly is the same thing as a danish oil but a lot less expensive. The advantage over polymerized oils is that it has polyurethane added as a resin and this gives you more protection. It also dries much harder. This is good on a guitar. It is easily applied, cost effective, adds good protection if built up and available in either gloss or satin.
Great, I thought, before reading the following response from Kevin Gallagher, another luthier whose opinions I always value:
The wipe applied poly is another great finish, but in another woodworking genre. It is soft and not very durable so it works off quickly under a few pick strokes or fingernail strikes.
More food for thought. As is the case with so many aspects of our craft, it all boils down to who you're willing to believe. Or, trying it for yourself and making up your own mind. I bought a tin of the gloss Miniwax this morning prior to reading these opinions and once again I'm scratching my head wondering what the best option is.

However, with four guitars and a mandolin at the finishing stage, or very close to it, I'm toying with the idea of experimenting a little: the little 12-fret 00 is currently under finish with Hard Shellac; the OM will probably end up with Tru-Oil after reading Kim's post; the Miniwax could go on one of the 000s; don't know yet about the other 000, and the mando will almost certainly be sprayed with Hard Shellac.
Both of the instruments I'll be finishing with Hard Shellac are for my own use, so I'll have plenty of opportunity to assess its durability as time goes on.
- graham mcdonald
- Blackwood
- Posts: 473
- Joined: Thu Oct 25, 2007 11:57 am
- Location: Canberra
- Contact:
Pete,
The great advantage of the wipe-on finishes is that another coat is simple to apply. I only used it on the classical guitar I built because I wanted a quick basic finish, just something to protect it a little. I got the guitar back yesterday from a friend who has been playing it and it does need something extra on it. The soundboard only has a couple of very thin coats and the whole thing needs a little more 'body' to it to get it up to a semi-gloss much like a danish oil finish, which was what I was hoping for.
It does depend on what you want as a final finish. A nitro lacquer is still the standard. You just have to be prepared to do a lot more work (or pay someone to do it for you) to get that look. I am just hoping that a cross-linked shellac can get close. If you don't have to have the smooth film of finish, unblemished by pores and other things that look like wood, the wipe-on oils are fine. It was good to see some confirmation that the stuff doesn't penetrate softwoods very much. I suspected they didn't but had no easy way to check.
We can both report in on progress with the hard shellac!
cheers
graham
The great advantage of the wipe-on finishes is that another coat is simple to apply. I only used it on the classical guitar I built because I wanted a quick basic finish, just something to protect it a little. I got the guitar back yesterday from a friend who has been playing it and it does need something extra on it. The soundboard only has a couple of very thin coats and the whole thing needs a little more 'body' to it to get it up to a semi-gloss much like a danish oil finish, which was what I was hoping for.
It does depend on what you want as a final finish. A nitro lacquer is still the standard. You just have to be prepared to do a lot more work (or pay someone to do it for you) to get that look. I am just hoping that a cross-linked shellac can get close. If you don't have to have the smooth film of finish, unblemished by pores and other things that look like wood, the wipe-on oils are fine. It was good to see some confirmation that the stuff doesn't penetrate softwoods very much. I suspected they didn't but had no easy way to check.
We can both report in on progress with the hard shellac!
cheers
graham
Graham McDonald
http://www.mcdonaldstrings.com
http://www.mcdonaldstrings.com
-
- Blackwood
- Posts: 115
- Joined: Tue Dec 09, 2008 1:15 pm
For anyone who is interested, the thread I quoted from over at the OLF is well worth reading.
http://www.luthiersforum.com/forum/view ... it=miniwax
http://www.luthiersforum.com/forum/view ... it=miniwax
Graham, how far down the track do you think it will be before you can put your hand on your heart and declare that the crazing problems have been solved? Note that I'm hanging onto the instruments I'm using it on just in case there's yet more tweaking to be done at U-Beaut HQ!We can both report in on progress with the hard shellac!
Who is online
Users browsing this forum: Google and 191 guests