What have you accomplished lately?
- Taffy Evans
- Blackwood
- Posts: 1077
- Joined: Wed Apr 30, 2008 6:54 pm
- Location: Charters Towers North Queensland
That guitars gonna look terrific when the finish is applied, it looks great now. I'm amazed at the timbers you guys find and use, I thought that tone wood was limited to the popular few. I've been given a few odd peices over the years I'm goning to have to dig it out and have another look.
Good stuff Bob.
Good stuff Bob.
Taff
- Stephen Kinnaird
- Blackwood
- Posts: 287
- Joined: Sun Oct 14, 2007 1:45 pm
- Location: Texas, USA
Hey A.P., thanks M8. (At least I hope I'm the Stephen to whom you are referring!) Actually, I thought it was the back inlay that continued onto the butt... but that's splitting purfling lines, isn't it?
Bob, that Tiger is gorgeous! WHO do you have to know to get wood that nice???
Also, I see that now I'm a Kea. Dare I ask what that is?
Steve
Bob, that Tiger is gorgeous! WHO do you have to know to get wood that nice???

Also, I see that now I'm a Kea. Dare I ask what that is?
Steve
There are some great woods, down under!
I managed to get the OM bound and sanded out and the first pore filling session done after I took a few pikkies. So here they are.
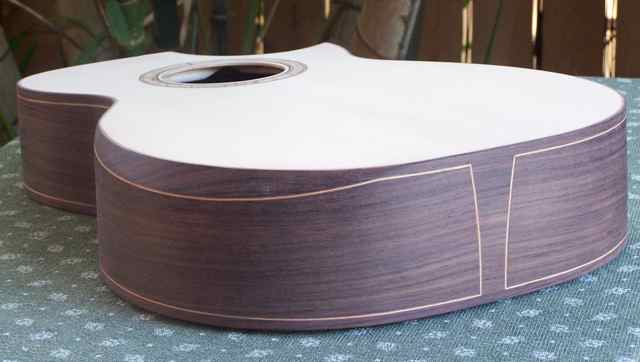
I went for Hesh's stealth bindings. just to try something else that was new on this one. Well, to tell the truth, it was the only wood that I had kicking around that I was going to be able to get a piece large enough for the armrest from what was in stock.
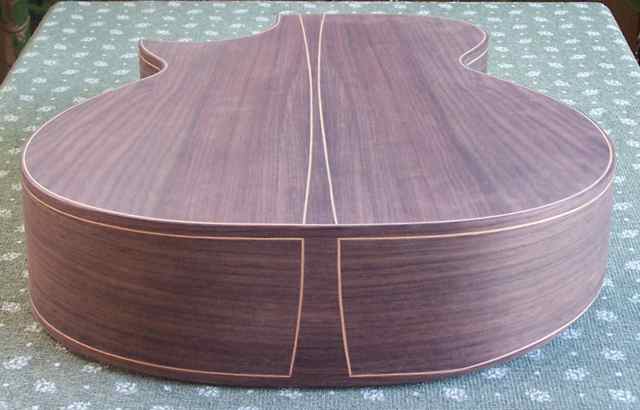
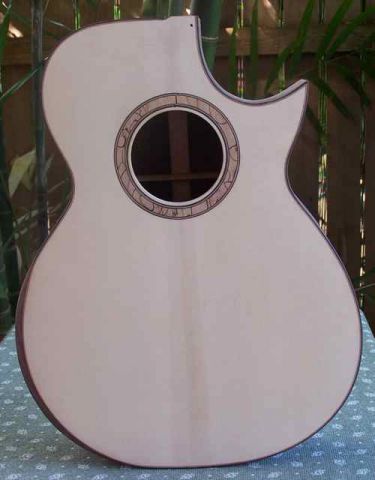
The first cutaway that I did was a real pain. This one turned out to be far more easy to do. It's still a heap more work to do a Florentine cutaway, but I love the look of them.
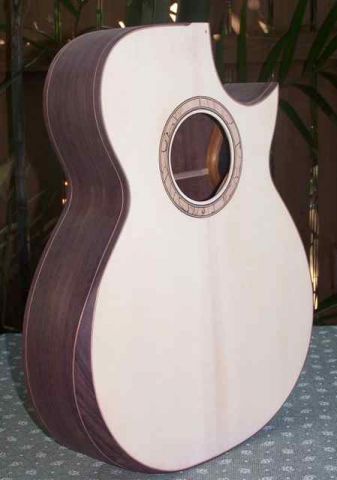
The arm rest was actually fairly easy to do, once I got my head around how I was going to tackle it. Yes, it's a heap of work to do as well, but again, I really love the look.
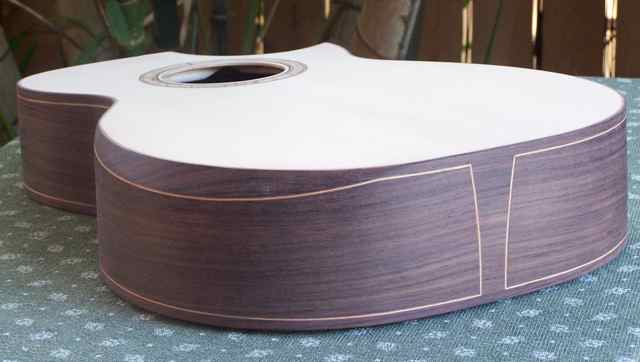
I went for Hesh's stealth bindings. just to try something else that was new on this one. Well, to tell the truth, it was the only wood that I had kicking around that I was going to be able to get a piece large enough for the armrest from what was in stock.

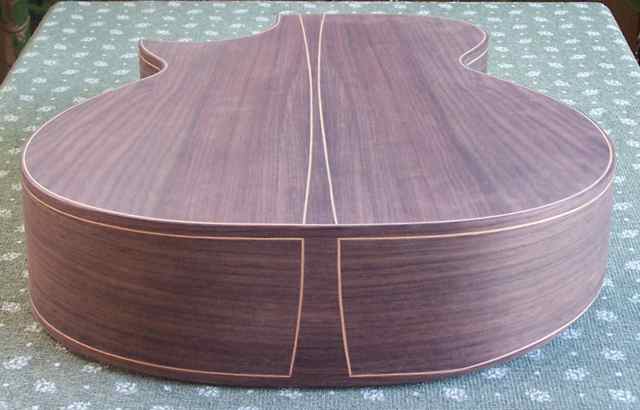
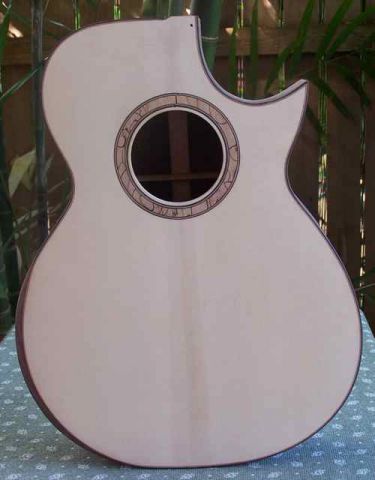
The first cutaway that I did was a real pain. This one turned out to be far more easy to do. It's still a heap more work to do a Florentine cutaway, but I love the look of them.
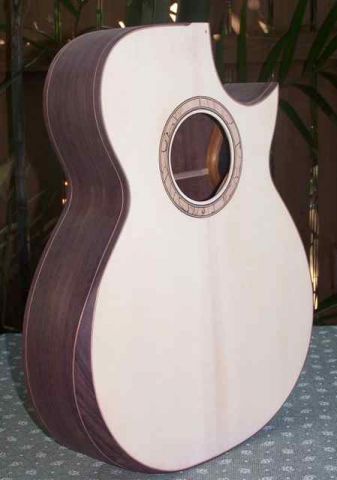
The arm rest was actually fairly easy to do, once I got my head around how I was going to tackle it. Yes, it's a heap of work to do as well, but again, I really love the look.
- Dennis Leahy
- Blackwood
- Posts: 872
- Joined: Wed Oct 10, 2007 12:32 am
- Location: Duluth, MN, US
- Contact:
Man oh man, I don't know if I dare to post in this thread. Look at the work that has been shown!
But, I have actually accomplished something lately. I punched four holes in my guitar. (This is my second guitar, a Cocobolo "stretched parlor" with a Lutzii top.)

Offset, elliptical soundhole with Amboyna burl soundhole ring (still covered with CA in this photo.)

A pair of elliptical ports, one for hot water; one for cold.

An access panel in the lower bout.
I'm trying to think of some other places to make holes in this guitar, but if I can't think of any, I may just call it ready for the soundboard.
Dennis
But, I have actually accomplished something lately. I punched four holes in my guitar. (This is my second guitar, a Cocobolo "stretched parlor" with a Lutzii top.)

Offset, elliptical soundhole with Amboyna burl soundhole ring (still covered with CA in this photo.)

A pair of elliptical ports, one for hot water; one for cold.

An access panel in the lower bout.
I'm trying to think of some other places to make holes in this guitar, but if I can't think of any, I may just call it ready for the soundboard.
Dennis
Another damn Yank!
- Bob Connor
- Admin
- Posts: 3115
- Joined: Mon Jul 09, 2007 9:43 pm
- Location: Geelong, Australia
- Contact:
Steve - I travel to Tasmania a couple of times a year to visit various sawmillers on the North West and West Coasts to source timber.Stephen Kinnaird wrote:Hey A.P., thanks M8. (At least I hope I'm the Stephen to whom you are referring!) Actually, I thought it was the back inlay that continued onto the butt... but that's splitting purfling lines, isn't it?
Bob, that Tiger is gorgeous! WHO do you have to know to get wood that nice???![]()
Also, I see that now I'm a Kea. Dare I ask what that is?
Steve
I can tell you it's the luck of the draw on what's available. On the last trip I spent only a third of the budget I had allocated simply because the quality wasn't there.
I buy most of it green and season it myself and Myrtle is quite a cantankerous wood so the yield is not great from it.
In fact I've got half a dozen sets that were cut from a billet that already had a crack in it and I've got the fingers crossed it isn't going to spread into the useable area of the back.
Myrtle of that quality is not the norm and when I bought that billet the sawmiller remarked that it was about as good as it gets.
Still theres all sorts of different patterns in the Tiger and some people will prefer different things.
I have seen some Tiger stumpwood with unbelievable figure and curl in it. Not big enough for guitars and probably too unstable but insane looking wood
A Kea is a New Zealand bird.
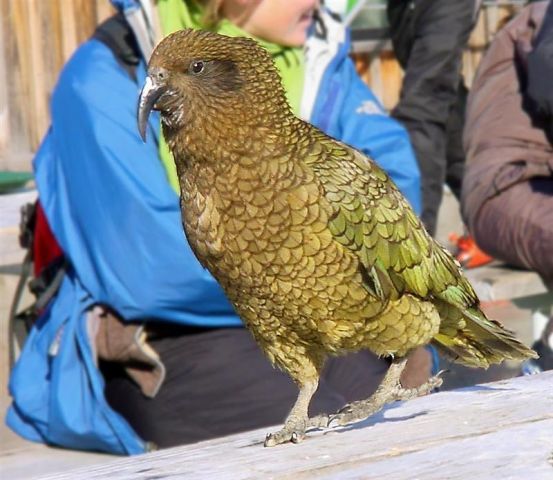
- graham mcdonald
- Blackwood
- Posts: 473
- Joined: Thu Oct 25, 2007 11:57 am
- Location: Canberra
- Contact:
- Stephen Kinnaird
- Blackwood
- Posts: 287
- Joined: Sun Oct 14, 2007 1:45 pm
- Location: Texas, USA
Bob, thanks for the info. (I just assumed you got the Tiger from Tim. How
resourceful to go get your own... I may have to come down sometime.)
Allen, I really, no really like what you've done there.
I was thinking of a tail wedge like yours, and you're going to push me
over the edge to do one like it. Nice work!
Dennis, fine looking stuff there bud. I'm looking forward to seeing the soundhole scraped clean. Should be fantastic.
Steve
resourceful to go get your own... I may have to come down sometime.)
Allen, I really, no really like what you've done there.
I was thinking of a tail wedge like yours, and you're going to push me
over the edge to do one like it. Nice work!
Dennis, fine looking stuff there bud. I'm looking forward to seeing the soundhole scraped clean. Should be fantastic.
Steve
There are some great woods, down under!
Gee, thanks guys. Kind of humbling to have such high praise from 2 really fine builders.
Steve, the curved end graft has turned into a bit of a feature on my guitars I suppose. This is my 9th guitar, and I think I've only built one without that style of end graft.
I really do like Bob's latest though. I might give one of those a go some time soon.
Steve, the curved end graft has turned into a bit of a feature on my guitars I suppose. This is my 9th guitar, and I think I've only built one without that style of end graft.
I really do like Bob's latest though. I might give one of those a go some time soon.
- Bob Connor
- Admin
- Posts: 3115
- Joined: Mon Jul 09, 2007 9:43 pm
- Location: Geelong, Australia
- Contact:
Masochist.Allen wrote:Gee, thanks guys. Kind of humbling to have such high praise from 2 really fine builders.
Steve, the curved end graft has turned into a bit of a feature on my guitars I suppose. This is my 9th guitar, and I think I've only built one without that style of end graft.
I really do like Bob's latest though. I might give one of those a go some time soon.

I got the idea from Howard Klepper who has done one with a mitred rectangle that does not connect with the bindings. It also looks great but there's only 4 mitres to do - not 12.
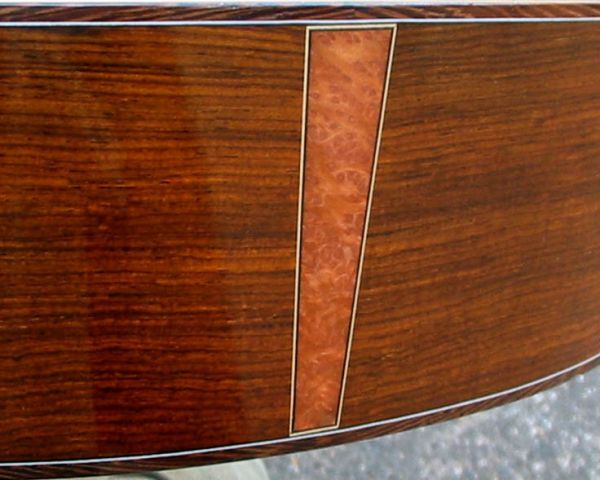
Ive just spent the day re-sizing wood for necks on my new table saw and doing other woody things I had a day off work
.
A while ago a friend of mine sent me a couple of boxes of amazing wood he had collected and I have been trying to make a guitar out of it for him.
It is very challenging because nothing is standard. He insisted I make the sides out of this native pear. Amazing figure, (photos not real great) and rich brown colour but the bookmatched pieces were too narrow. So I joined them using epoxy figureing it would be better than nothing while bending. Well it didn't hold but it came out pretty clean, I glued it back up and looked for some veneer to support the side. I used this amazing stuff he also sent. I assume it is sapele but I don't know. I just glued it up and put it back in my bender with solid mold and turnbuckles and tighten the begeezers out of it. It worked great.
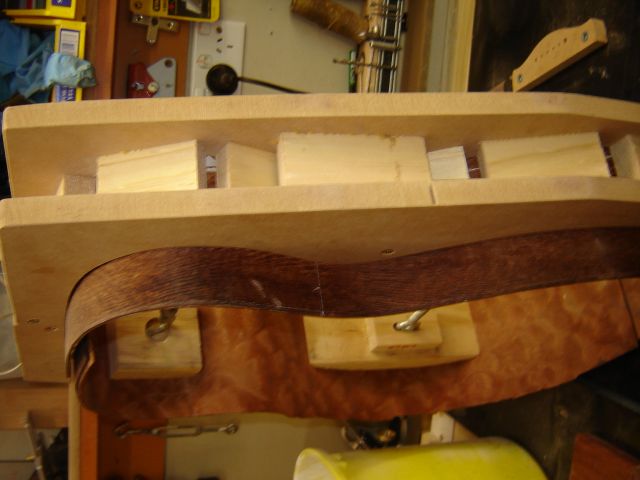
The next thing was the back, he had sent this nice huon pine, 3 rough sawn boards about 900mm by 200mm by about 15mm. I wanted to resaw them to get 6 bookmatched bits but I needed to be really careful because I could have ended up with a pile of nice smelling sawdust. I thought about it and looked around and ended up ordering a thin kirf resaw blade for my 14inch BS called a Woodsaver from the US. Amazing blade. I ended up with 6 bookmatched boards. The back needed to be 4 pieces. I put them all through the sander today and things are looking good. There is enough to left for another B&S side set (bottom photo)
Here are some of the sticks I cut up for the laminated neck. The light wood is curly Marri and the the other is curly Jarrah. The neck will be Marri, Jarrah Marri. The fretboards are are for my RG seven string and a my thunderbird bass.
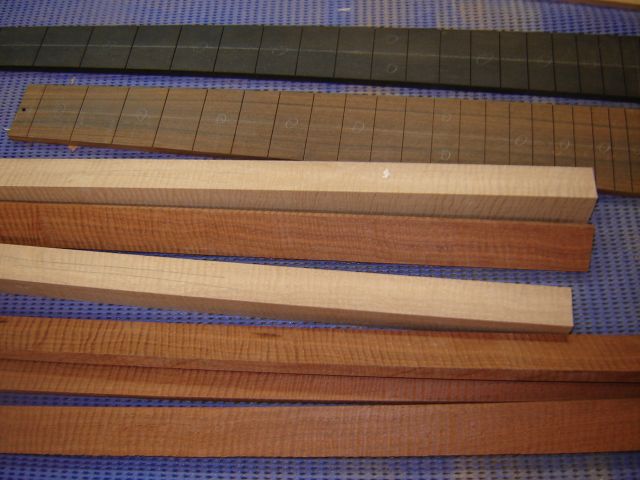
The last thing i did today was cut and glue up the scarf joints on two necks, One for my seven string electrtic and one for my bass. There are various other project scattered around my workshop.
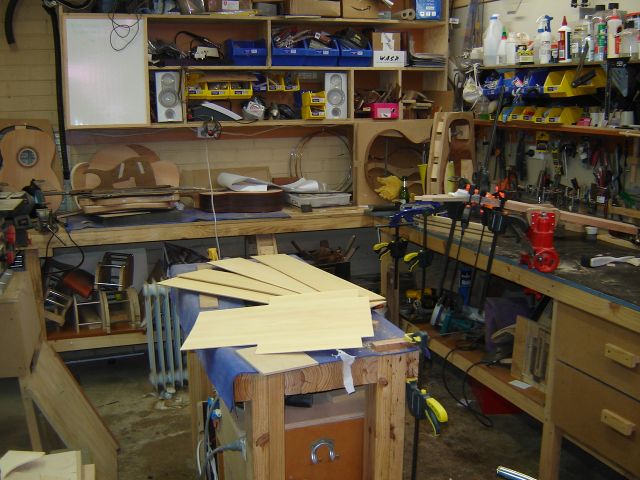
Dom

A while ago a friend of mine sent me a couple of boxes of amazing wood he had collected and I have been trying to make a guitar out of it for him.
It is very challenging because nothing is standard. He insisted I make the sides out of this native pear. Amazing figure, (photos not real great) and rich brown colour but the bookmatched pieces were too narrow. So I joined them using epoxy figureing it would be better than nothing while bending. Well it didn't hold but it came out pretty clean, I glued it back up and looked for some veneer to support the side. I used this amazing stuff he also sent. I assume it is sapele but I don't know. I just glued it up and put it back in my bender with solid mold and turnbuckles and tighten the begeezers out of it. It worked great.
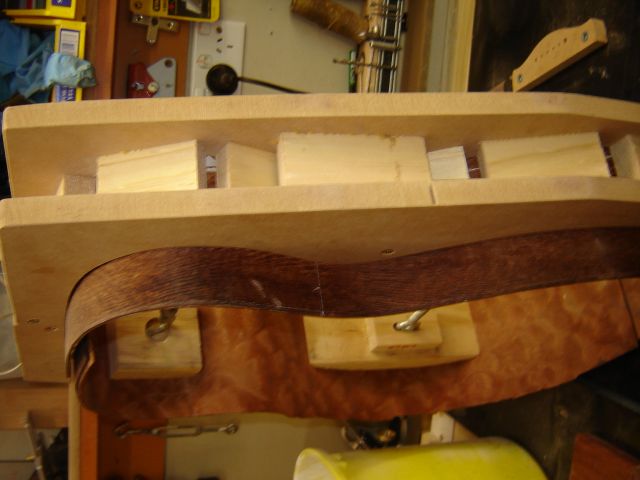
The next thing was the back, he had sent this nice huon pine, 3 rough sawn boards about 900mm by 200mm by about 15mm. I wanted to resaw them to get 6 bookmatched bits but I needed to be really careful because I could have ended up with a pile of nice smelling sawdust. I thought about it and looked around and ended up ordering a thin kirf resaw blade for my 14inch BS called a Woodsaver from the US. Amazing blade. I ended up with 6 bookmatched boards. The back needed to be 4 pieces. I put them all through the sander today and things are looking good. There is enough to left for another B&S side set (bottom photo)
Here are some of the sticks I cut up for the laminated neck. The light wood is curly Marri and the the other is curly Jarrah. The neck will be Marri, Jarrah Marri. The fretboards are are for my RG seven string and a my thunderbird bass.
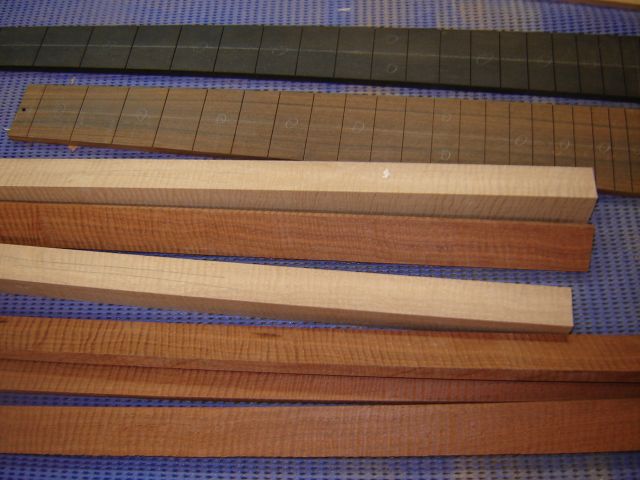
The last thing i did today was cut and glue up the scarf joints on two necks, One for my seven string electrtic and one for my bass. There are various other project scattered around my workshop.
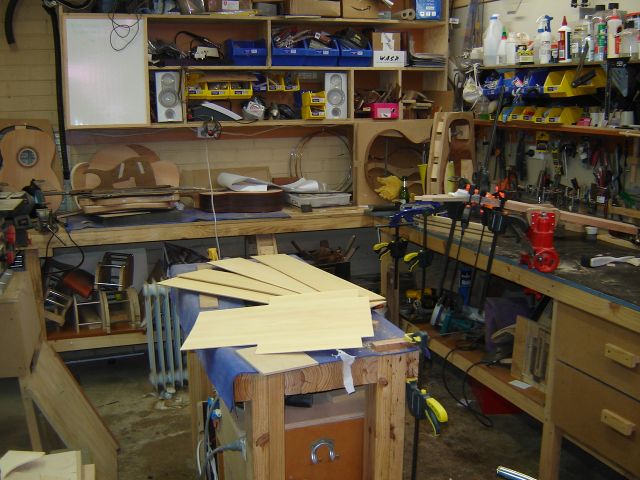
Dom
You can bomb the world to pieces,
but you can't bomb the world to peace!
but you can't bomb the world to peace!
A trip to Bunnies this morning saw me start work on building a small partition (about 2x3m) in one corner of my shop that will be properly humidity and temperature controlled for assembly and storage. No pics yet but I'll try and get some shortly.
I'm really looking forward to the prospect of being about to work whenever I want as thanks to drought-breaking weather, the past 9 months or so have been far wetter than usual. Should hopefully have it mostly complete over the weekend (I'll save insulating it etc. until closer to summer when that'll be crucial).
There's nothing more frustrating than having three or four half-built guitars sitting around waiting for things to clear up before I can do critical steps like bracing and closing the boxes.
I'm really looking forward to the prospect of being about to work whenever I want as thanks to drought-breaking weather, the past 9 months or so have been far wetter than usual. Should hopefully have it mostly complete over the weekend (I'll save insulating it etc. until closer to summer when that'll be crucial).
There's nothing more frustrating than having three or four half-built guitars sitting around waiting for things to clear up before I can do critical steps like bracing and closing the boxes.
- Stephen Kinnaird
- Blackwood
- Posts: 287
- Joined: Sun Oct 14, 2007 1:45 pm
- Location: Texas, USA
Thanks Steve,
It sure is chaos but it is also organised. I have 7 guitars at various stages jammed into my little corner. You can probably count them all in the photo.
The organised bit comes because I have worked out places for all my tools and I always put them back in the same spot. And I read in a woodworking book a thing called the rule of 10. That is, you must put away 10 things everytime you come into the shop. Works for me but it has to be more like 20 things.
I will start a new thread for the bitsa guitar. Thanks for the interest.
Cheers
Dom
It sure is chaos but it is also organised. I have 7 guitars at various stages jammed into my little corner. You can probably count them all in the photo.
The organised bit comes because I have worked out places for all my tools and I always put them back in the same spot. And I read in a woodworking book a thing called the rule of 10. That is, you must put away 10 things everytime you come into the shop. Works for me but it has to be more like 20 things.
I will start a new thread for the bitsa guitar. Thanks for the interest.
Cheers
Dom
You can bomb the world to pieces,
but you can't bomb the world to peace!
but you can't bomb the world to peace!
Thought I'd share the (nearly) end result of my recent work...
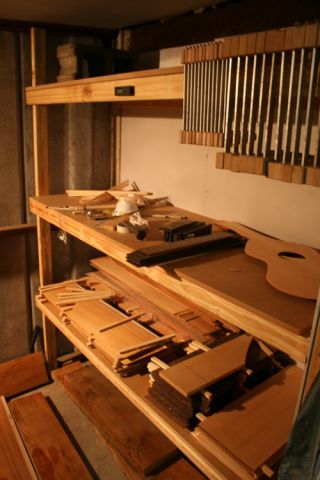
Shelving has always been a problem for me, as there's only so much you can use the $20 steel shelves from Bunnings/Mitre 10 for, especially with oversized tonewood. One main priority for my new humidity controlled workshop was nice BIG shelves. 3 600x1800mm (2'x6') shelves takes care of that problem. My current small stash only takes up about 1/4 of one shelf so with storage space taken care of, the WAS has no excuse. I'm also thinking of putting a gobar deck on the second shelf to free up bench space.
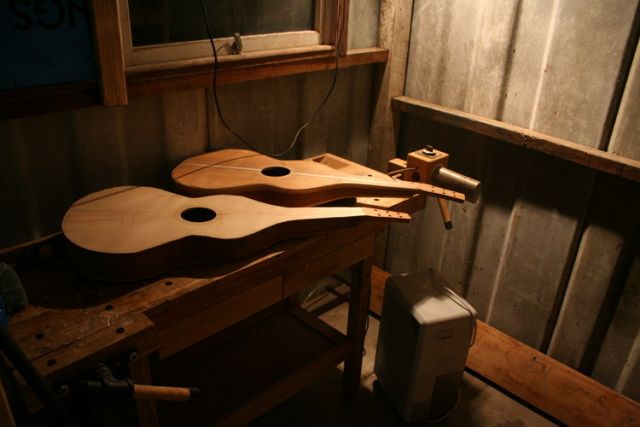
Small bench in place until I get around to buying or building a larger one.
Quite pleased that everything's working nicely. With the dehumidifier on and the door closed it's hovering nicely on about 48% compared with 72% outside, so I'm looking forward to a lot more building time.
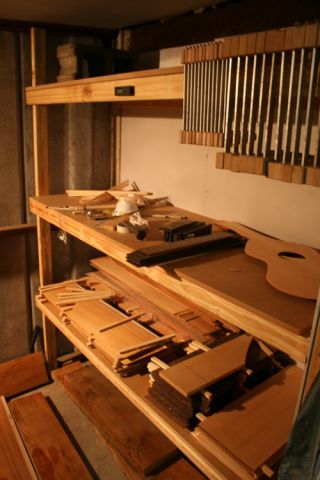
Shelving has always been a problem for me, as there's only so much you can use the $20 steel shelves from Bunnings/Mitre 10 for, especially with oversized tonewood. One main priority for my new humidity controlled workshop was nice BIG shelves. 3 600x1800mm (2'x6') shelves takes care of that problem. My current small stash only takes up about 1/4 of one shelf so with storage space taken care of, the WAS has no excuse. I'm also thinking of putting a gobar deck on the second shelf to free up bench space.
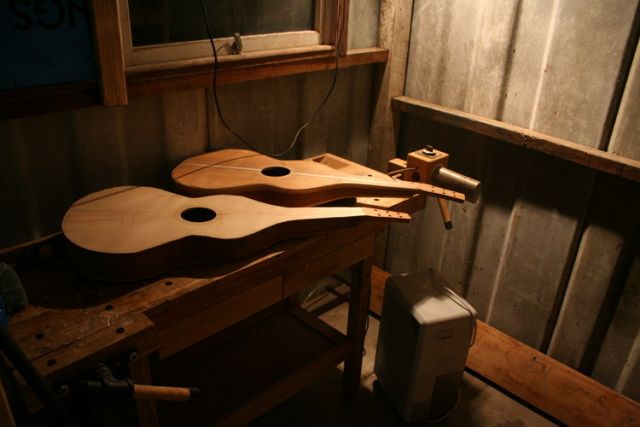
Small bench in place until I get around to buying or building a larger one.
Quite pleased that everything's working nicely. With the dehumidifier on and the door closed it's hovering nicely on about 48% compared with 72% outside, so I'm looking forward to a lot more building time.
You bet... in summer the tin roof gets to around 60ºC and higher, which makes it a nice 40-50º at head-level. I've insulated the walls and ceiling of the controlled area but I've decided to start saving now for a small air conditioner for 3-4 months time because I'm pretty sure it'll be painful in there otherwise.
- Bob Connor
- Admin
- Posts: 3115
- Joined: Mon Jul 09, 2007 9:43 pm
- Location: Geelong, Australia
- Contact:
- sebastiaan56
- Blackwood
- Posts: 1274
- Joined: Sun Oct 28, 2007 5:23 am
- Location: Blue Mountains
Who is online
Users browsing this forum: Google and 102 guests