Here is a new topic about flying bracings: To start the topic I will do a very short history of them:
-To my knowledge the first to use such a thing was Scherzer in the 1850’s. He used a rod of steel from neck-block to tail-block secured by a screw in the tail-block; you could adjust the tension with a flat screwdriver to compensate string tension. Remember Scherzer made a lot of guitars with more than 6 strings (up to 12 floating basses!), you clearly can see the device on this photo:
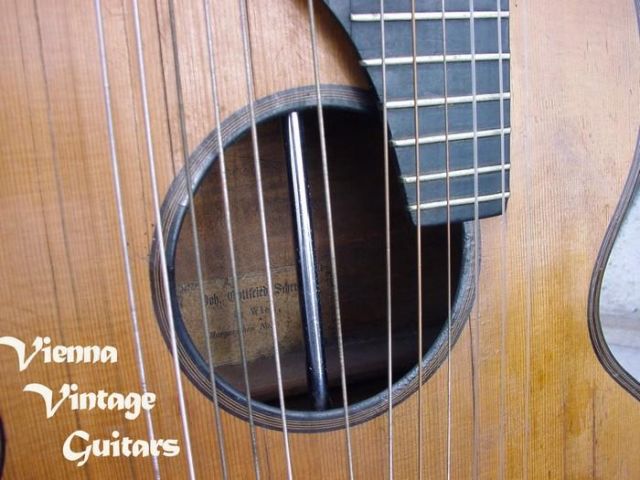
A lot of makers from Germany and Austria followed this maker: Resinger, Brauer, Raab and much more. Surprisingly even Fender used a similar system in some folks from the 60’s! Some modern makers, like myself use them with one difference: Usually new makers just glue the bar in place (made ot of maple, spruce, fiberglass or graphite) , I prefer to leave it floating in between 2 supports with an Allen to adjust tension on the device. Matanya Ophee made an entire experiment with one of his Scherzers adjusting the tension to see the influence in the sound. You can read that on the Google newsgroup here:
http://groups.google.be/group/rec.music ... bar&lnk=ol&
-Another approach of that are the flying braces used by Steve Klein on his guitars but in that case the bars just hold the bridge-plate in position…
Best regards
Benoit