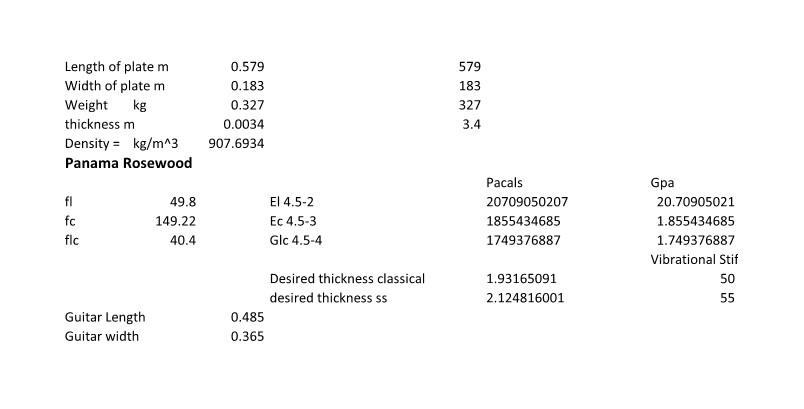
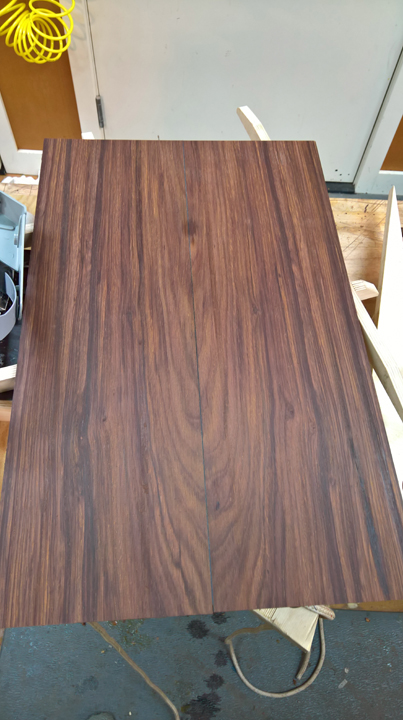
I bent the sides in a side bander and installed a heel block to make a bolt on blot off neck.
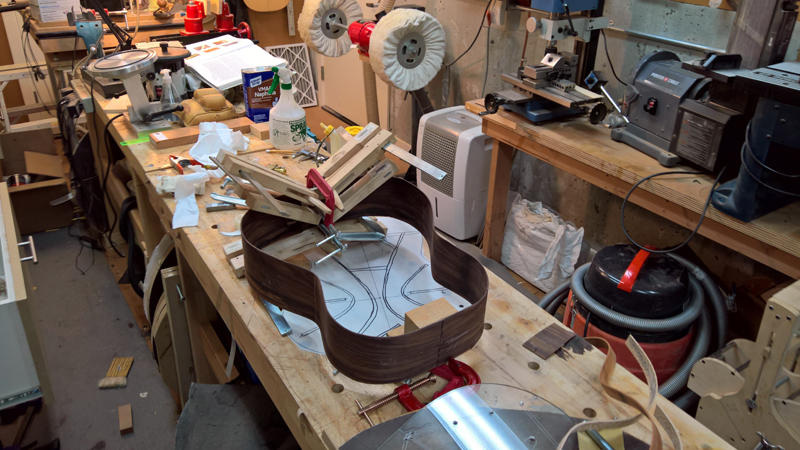
I cut out a bunch of 1.7 mm strips for solid linings. I have made them by just laminating them right to the rims. This time I decided to make the linings off of the guitar. I bent a strip of wood thicknessed like my sides, bent to shape of the rims. I used that strip and a half of a outside mold as the mole to laminate the strips into a solid lining. My though was that I could clean up the bottom of the linings with a round over router bit. Later it occured to me that I could cut inlets for the mass block and the side supports. I was happy about the way it cam together.
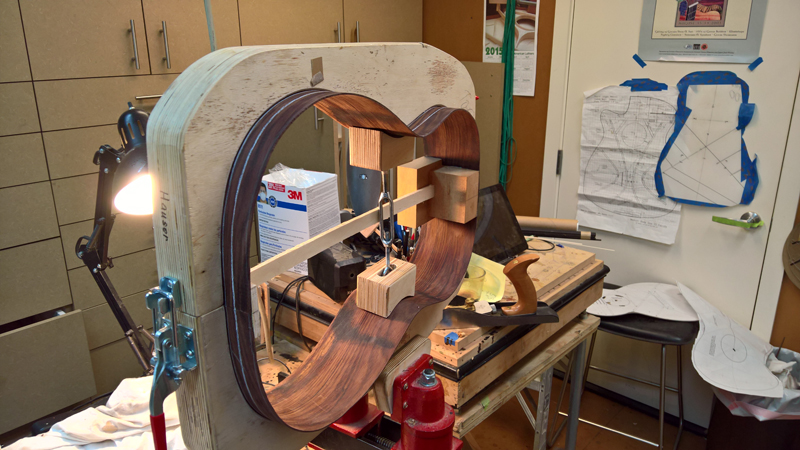
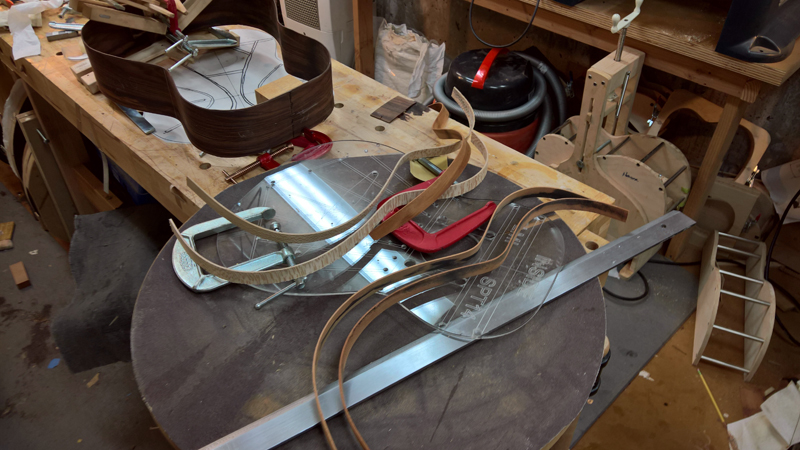
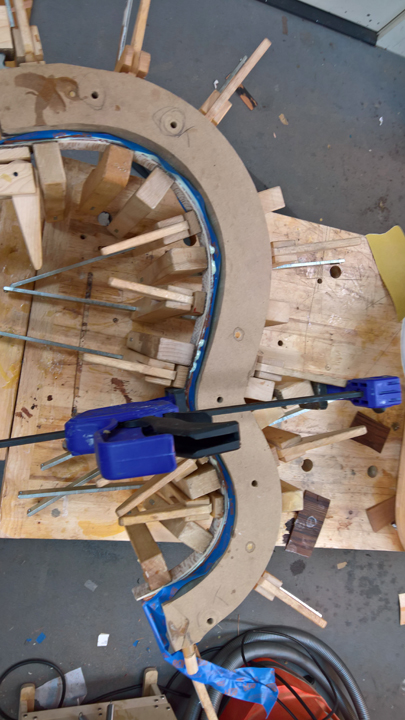
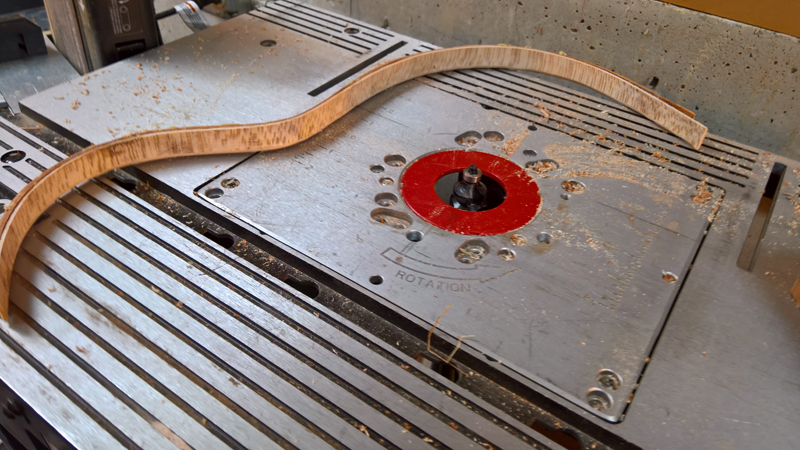
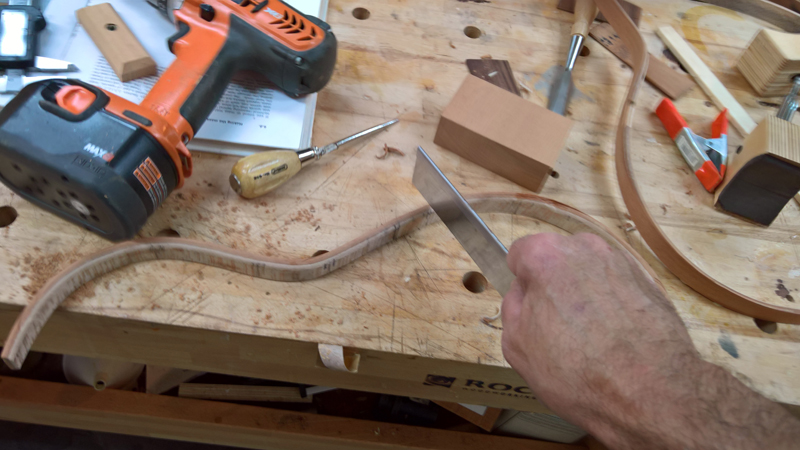
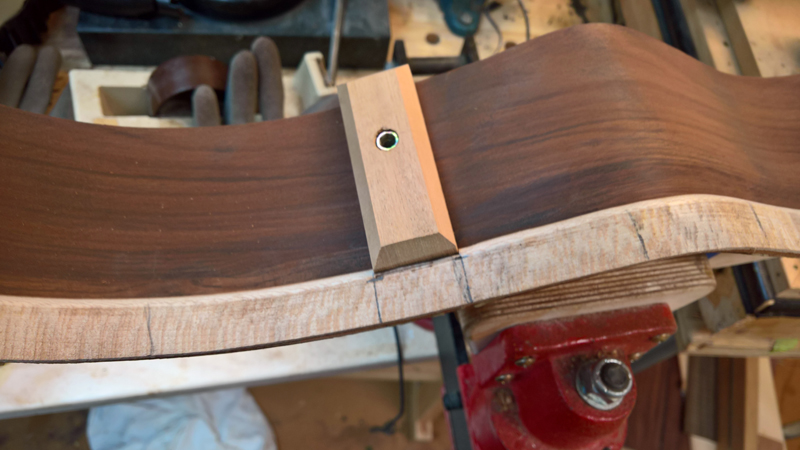
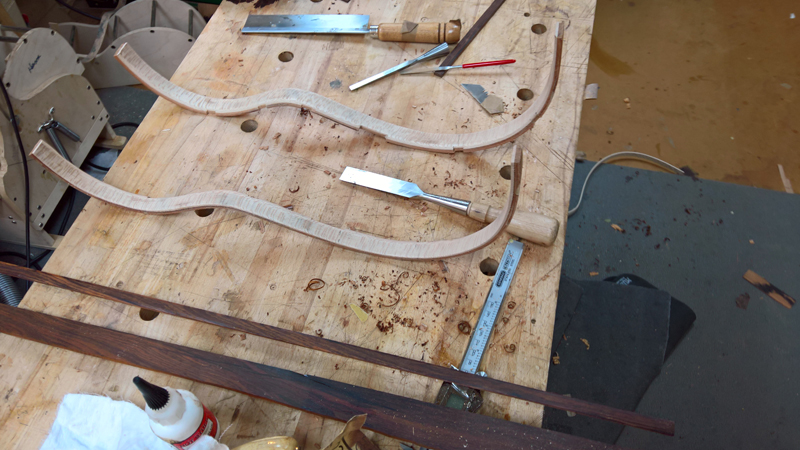
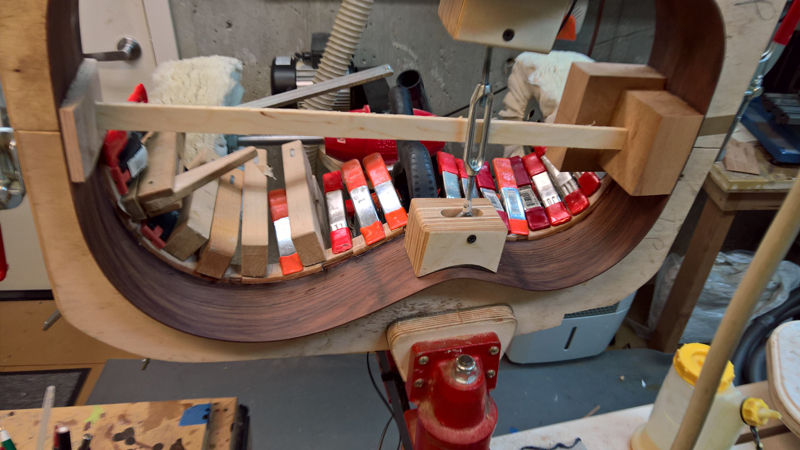
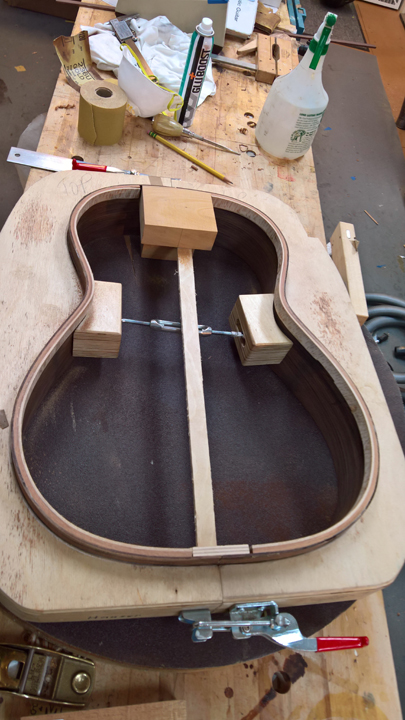
I cut out a bunch of stock for back braces and used the 17.5 degree router bit to make the gable on top of the brace.
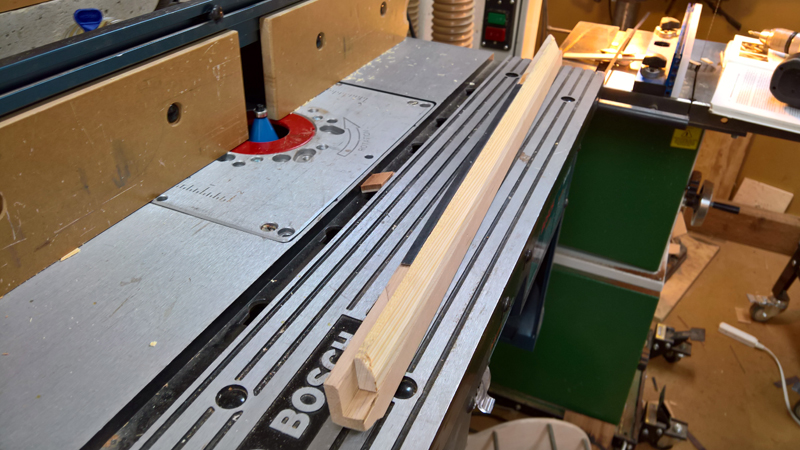
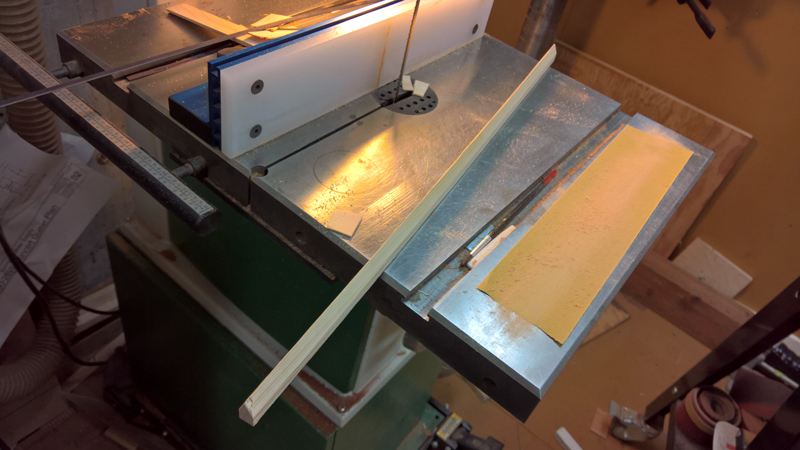
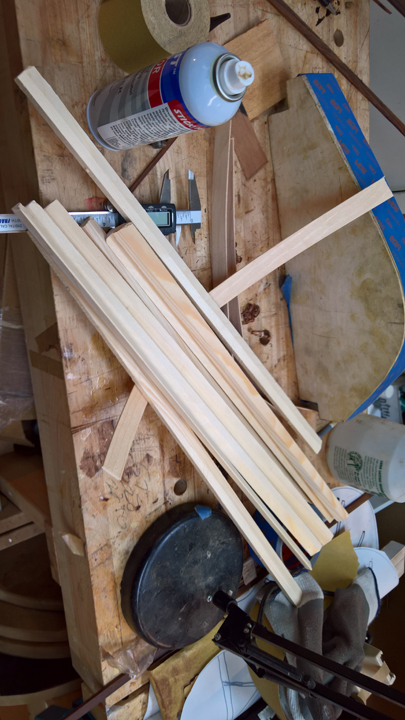
I laid out the braces cut the rebate in the center strips and used a couple of sessions to glue them to the back in a gobar deck.
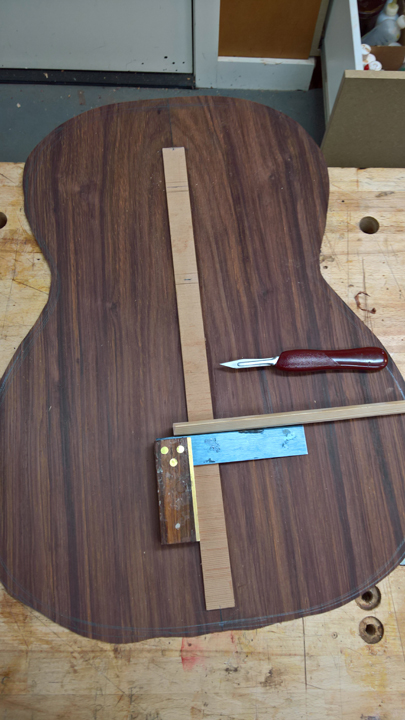
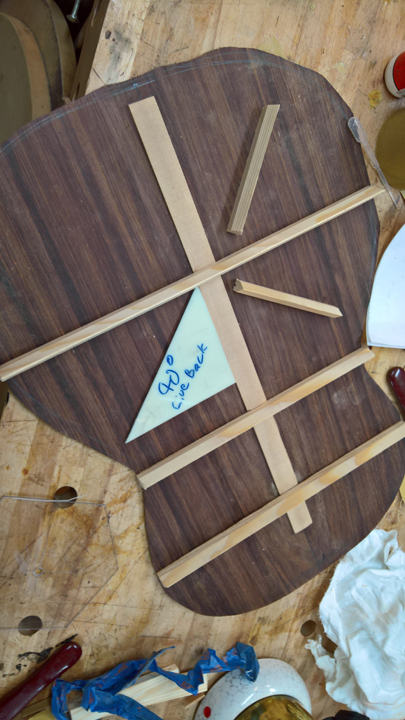
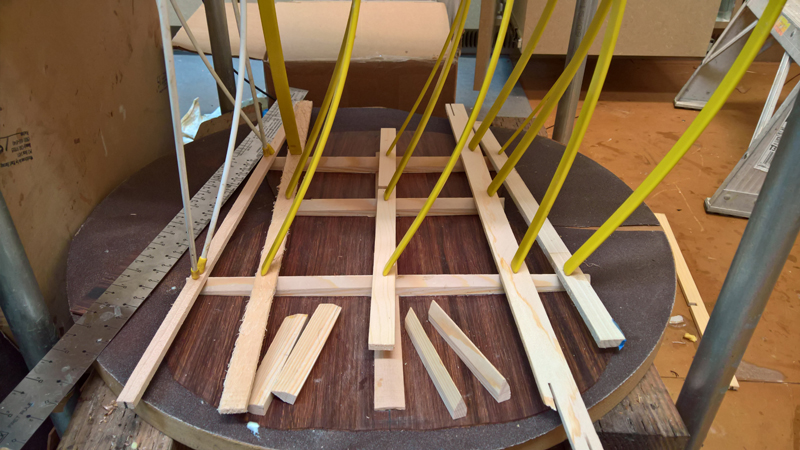
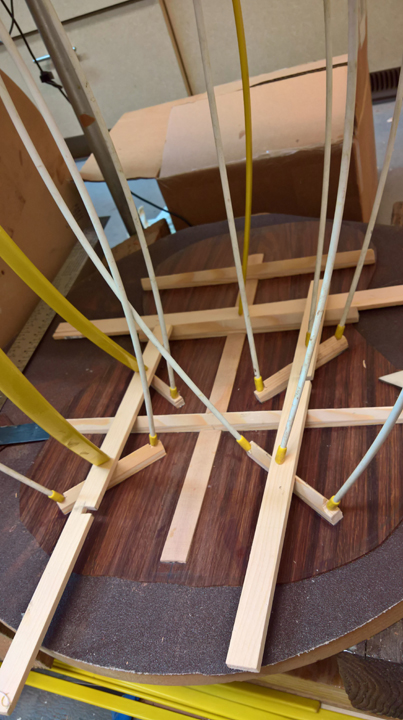
I also did some of the layout and prep for the bolt on bolt off neck
THe only new thing was to rig up a finger chopper offer to make the cut of the scarf joint on the neck. It came out clean and square needing almost no work with a plane.
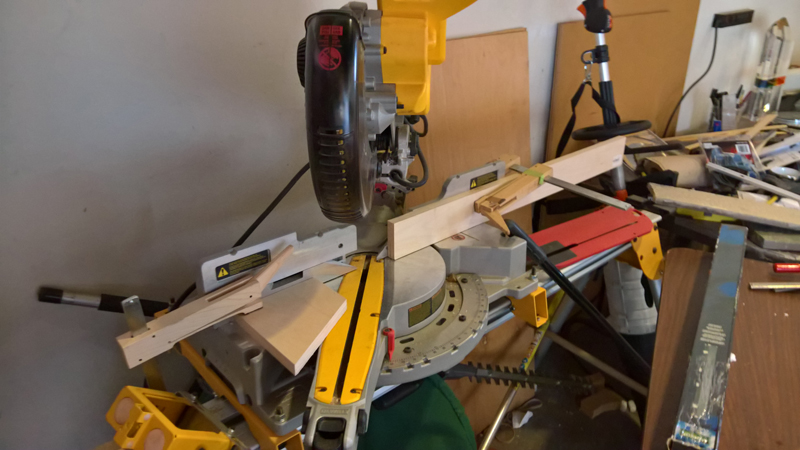
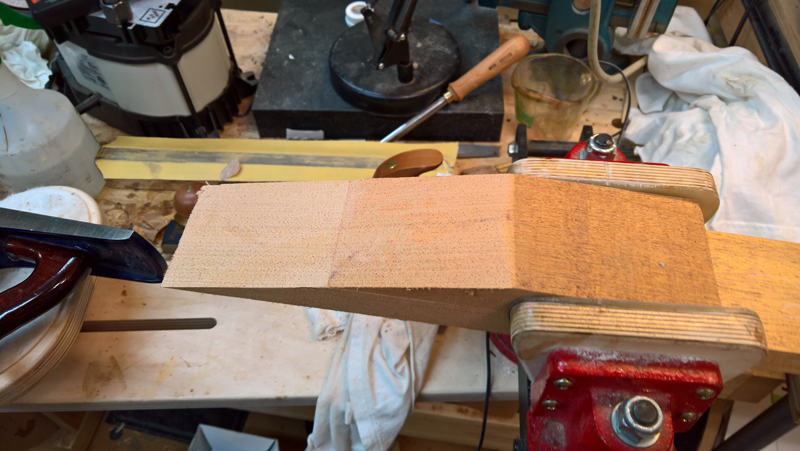
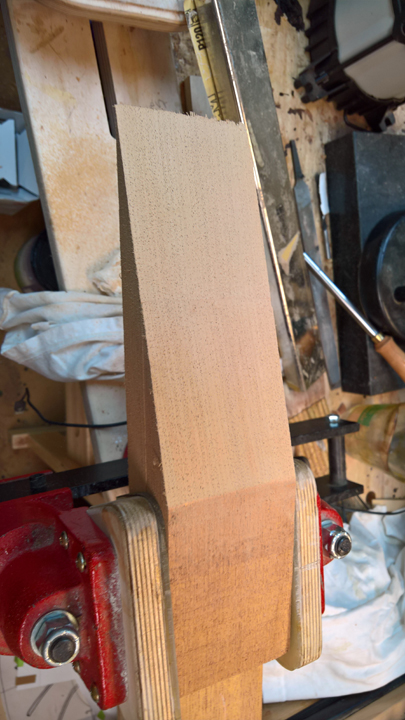
It glued up with no drama
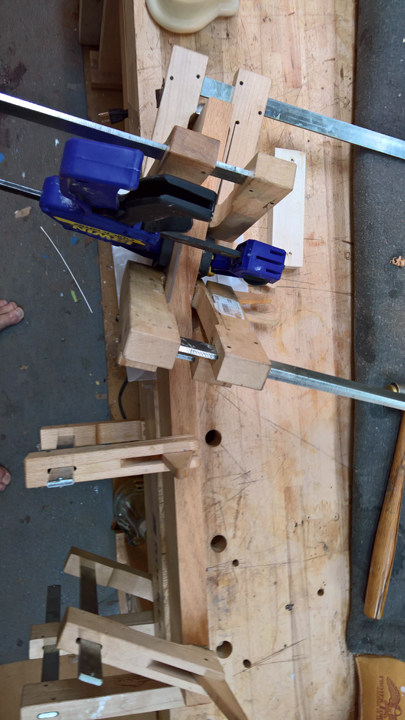
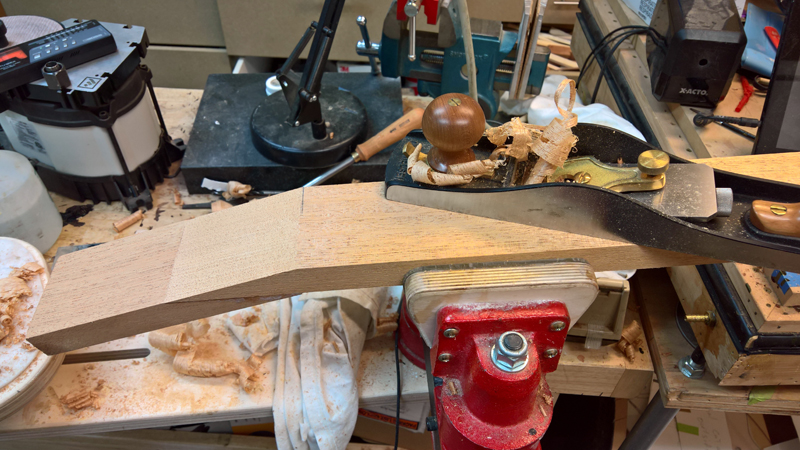
I used a 4 mm strip to set the angle for the truss rod.

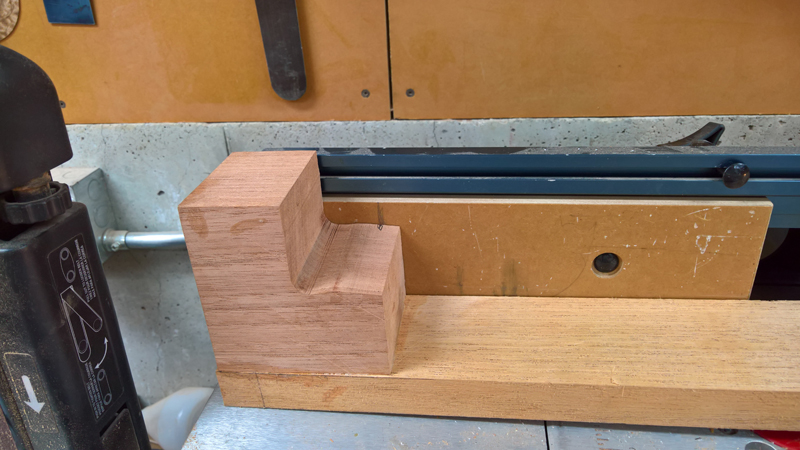
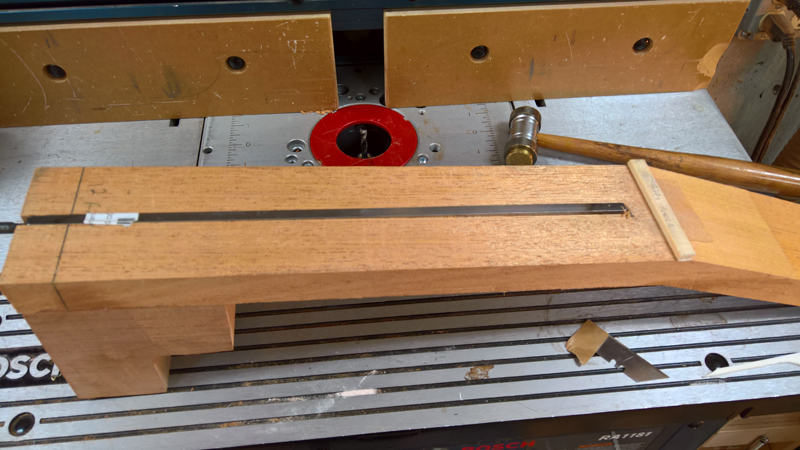
I have a fancy 24" radius bit that I used radius the fretboard.
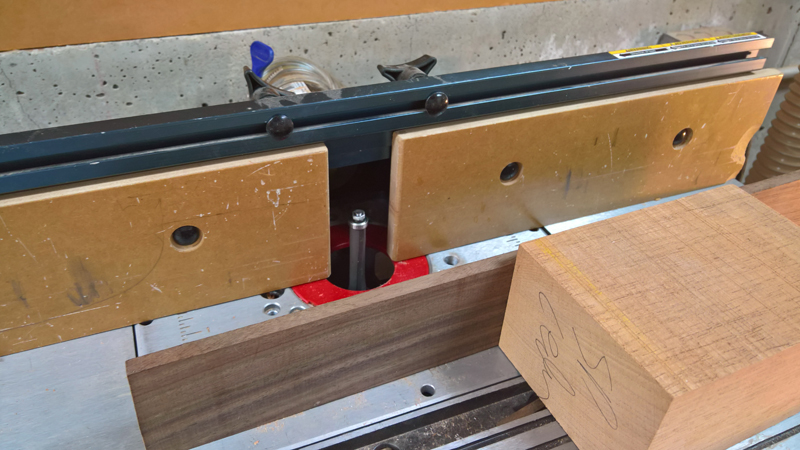
I cut the frets and laminated on a 4 mm thick strip of mahogany to the underside of the fret board.
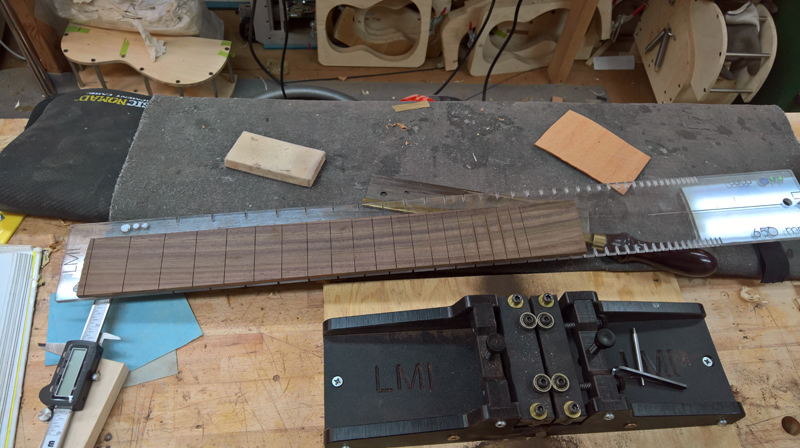
But foolish me I tapered the fretboard before I router the truss rod slot into the what will be the widge. So I cut it out with a scalpel and a chisel.
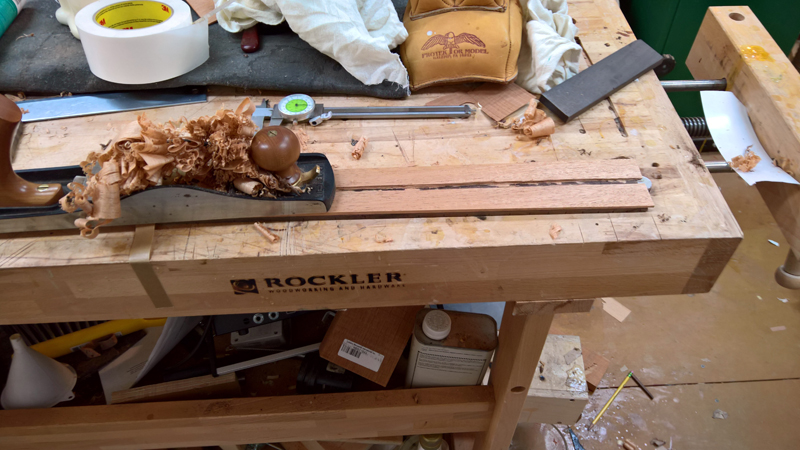
I also made the falcate braces laminating Lutz spruce strips that I bend on a hot pipe using molds I made for previous guitars
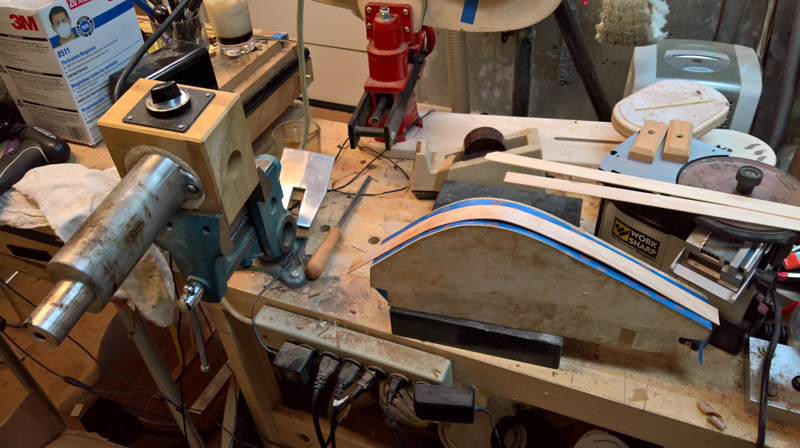
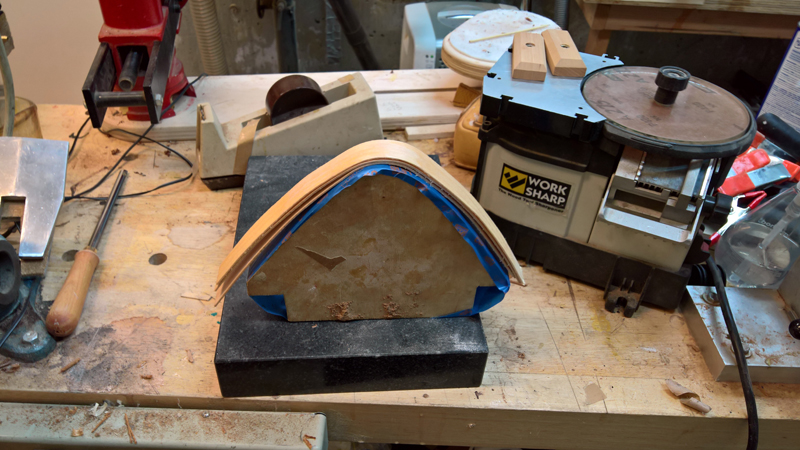
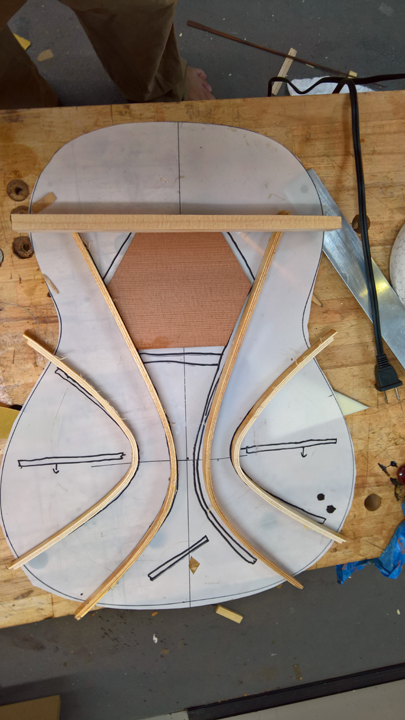
All caught up with the new blog.