ANZLF Adjustable Neck Joint Group Discussion
- Dennis Leahy
- Blackwood
- Posts: 872
- Joined: Wed Oct 10, 2007 12:32 am
- Location: Duluth, MN, US
- Contact:
Rick,
I'm still looking at inside (hidden) solutions partly because all of my guitar designs have offset soundholes - specifically to have more of the top vibrating. I have no upper transverse brace either. The offset soundhole gives access to a fully strung up guitar, strung to pitch.
I believe ya on your research with many players that could care less if the adjuster is visible or hidden. It is my own prejudice that I want it internal. And yes, if someone really wants a Martin, then Martin makes pretty good Martins, and a thousand other luthiers can do a pretty good job of cloning one.
I have not yet figured out how to make a fully cantilevered fingerboard, without a block beneath the extension, and without lifting it 3/4" above the soundboard. I've thought about laminated fingerboards, and drilling through the fingerboard endgrain and inserting metal rods. I'm not convinced that CF can provide the mass necessary above the 14th fret. I'll bet you're past conjecture on that point.
When I look at your current offering of Renaissance guitars, I see acoustic electrics that have evolved to become hollowbody electrics, not really acoustics any more. (Not knocking your line, just seeing the difference of where you are and what I am designing.) I hope you can see that an acoustic that is closer to "traditional" proportions may get a different reaction, with external hardware, compared to your current guitars.
Dennis
I'm still looking at inside (hidden) solutions partly because all of my guitar designs have offset soundholes - specifically to have more of the top vibrating. I have no upper transverse brace either. The offset soundhole gives access to a fully strung up guitar, strung to pitch.
I believe ya on your research with many players that could care less if the adjuster is visible or hidden. It is my own prejudice that I want it internal. And yes, if someone really wants a Martin, then Martin makes pretty good Martins, and a thousand other luthiers can do a pretty good job of cloning one.
I have not yet figured out how to make a fully cantilevered fingerboard, without a block beneath the extension, and without lifting it 3/4" above the soundboard. I've thought about laminated fingerboards, and drilling through the fingerboard endgrain and inserting metal rods. I'm not convinced that CF can provide the mass necessary above the 14th fret. I'll bet you're past conjecture on that point.
When I look at your current offering of Renaissance guitars, I see acoustic electrics that have evolved to become hollowbody electrics, not really acoustics any more. (Not knocking your line, just seeing the difference of where you are and what I am designing.) I hope you can see that an acoustic that is closer to "traditional" proportions may get a different reaction, with external hardware, compared to your current guitars.
Dennis
Another damn Yank!
-
- Blackwood
- Posts: 310
- Joined: Sun Jan 13, 2008 10:22 am
- Location: Santa Cruz, Ca.
- Contact:
Ahhh, but whose tradition?
From my point of view, what I'm doing has at least 100 years of tradition behind it, and that's not going back to Stauffer, Schertzer, Christan Frederick Martin, Zimmerman, etc. who were doing tilt neck guitars...with cantilevered fingerboards...in the early and mid 19th century.
You see, we're just reinventing and hopefully improving upon "the wheel" here. This is old, old stuff. It goes back to before de Torres, before Orville Gibson, before the Larsons, and before the introduction of the 2-17 Martin (their first production steel string model). So when you talk "tradition", what you're really saying is "my own particular take on tradition that happens to be based in the 1930s "Golden Era" that has narrowly defined the steel string guitar". I'd like to open the tradition back up and include more historical examples of innovation. I believe that the true tradition IS innovation, not ossification of ideas and aesthetics.
"Form follows function"...and when it does so purely and honestly, a new aesthetic emerges that neither hides nor compromises full functionality. We can then integrate the visuals, decorate, embellish, etc., but to make something less useful while trying to keep it looking like a less functional predecessor is to deny that we can make improvements upon designs of the past.

From my point of view, what I'm doing has at least 100 years of tradition behind it, and that's not going back to Stauffer, Schertzer, Christan Frederick Martin, Zimmerman, etc. who were doing tilt neck guitars...with cantilevered fingerboards...in the early and mid 19th century.
You see, we're just reinventing and hopefully improving upon "the wheel" here. This is old, old stuff. It goes back to before de Torres, before Orville Gibson, before the Larsons, and before the introduction of the 2-17 Martin (their first production steel string model). So when you talk "tradition", what you're really saying is "my own particular take on tradition that happens to be based in the 1930s "Golden Era" that has narrowly defined the steel string guitar". I'd like to open the tradition back up and include more historical examples of innovation. I believe that the true tradition IS innovation, not ossification of ideas and aesthetics.
"Form follows function"...and when it does so purely and honestly, a new aesthetic emerges that neither hides nor compromises full functionality. We can then integrate the visuals, decorate, embellish, etc., but to make something less useful while trying to keep it looking like a less functional predecessor is to deny that we can make improvements upon designs of the past.
Rick Turner
Guitar Maker, Experimenter, Diviner
www.renaissanceguitars.com
www.d-tar.com
Guitar Maker, Experimenter, Diviner
www.renaissanceguitars.com
www.d-tar.com
-
- Blackwood
- Posts: 310
- Joined: Sun Jan 13, 2008 10:22 am
- Location: Santa Cruz, Ca.
- Contact:
Dennis, if you're looking at my Renaissance guitar designs, you're looking at totally the wrong instruments for this discussion. They have very little in common with the acoustics I build other than the peghead shape and the fact that they're mostly made out of wood. One of the confounding things about me is that I'm all over the map when it comes to guitar designs, and consequently many if not most folks zero in on a particular thing I do, and they think that's all I do. I make solid body guitars and basses, semi-hollow acoustic electrics, and full bodied acoustic guitars and ukuleles. The designs are all very different from one another in most details including some very basic construction principles. When I'm talking tilt-neck, the thing to do is to find a copy of American Lutherie from the 2001 vintage that has my first tilt neck guitar (that I made for Henry Kaiser to take to Antarctica) on the cover. If you're looking at my Renaissance semi-hollow guitars, you're looking at a completely different animal.
Rick Turner
Guitar Maker, Experimenter, Diviner
www.renaissanceguitars.com
www.d-tar.com
Guitar Maker, Experimenter, Diviner
www.renaissanceguitars.com
www.d-tar.com
- Dave White
- Blackwood
- Posts: 452
- Joined: Mon Nov 12, 2007 3:10 am
- Location: Hughenden Valley, England
- Contact:
Dennis,Dennis Leahy wrote: I have not yet figured out how to make a fully cantilevered fingerboard, without a block beneath the extension, and without lifting it 3/4" above the soundboard. I've thought about laminated fingerboards, and drilling through the fingerboard endgrain and inserting metal rods. I'm not convinced that CF can provide the mass necessary above the 14th fret.
You slope the upper bout area downwards - longitudinal arching. Check out the pictures on Howard Kleppers website.You probably don't need 3/4" under the fingerboard and could get away with less - I'm not sure about the "mass" argument". I think the stiffness and impact on the neck's impedance are more important. If you make stacked heels you can have the extension/cantilever as the same piece as the main neck shaft and the cf rods can go the whole length of the fingerboard in there.
Why do you think you need mass?
Dave White
[url=http://www.defaoiteguitars.com]De Faoite Stringed Instruments[/url]
[url=http://www.defaoiteguitars.com]De Faoite Stringed Instruments[/url]
- Dave White
- Blackwood
- Posts: 452
- Joined: Mon Nov 12, 2007 3:10 am
- Location: Hughenden Valley, England
- Contact:
Rick,
I agree with you 100%. I think that makers who have a proper view of "tradition" are evaluating the whole continuum and process and also recognise that it is an evolutionary process that moves and changes through time. Very little is fundimentally new but small changes and adaptations can have huge impacts and we do have the benefit of modern materials and techniques that had they been available in the past, the main shapers of "tradition" would also have been trying and using.
I find the "definition" of "tradion" as being just Martin and Gibson very narrow and xenophobic.
I agree with you 100%. I think that makers who have a proper view of "tradition" are evaluating the whole continuum and process and also recognise that it is an evolutionary process that moves and changes through time. Very little is fundimentally new but small changes and adaptations can have huge impacts and we do have the benefit of modern materials and techniques that had they been available in the past, the main shapers of "tradition" would also have been trying and using.
I find the "definition" of "tradion" as being just Martin and Gibson very narrow and xenophobic.
Dave White
[url=http://www.defaoiteguitars.com]De Faoite Stringed Instruments[/url]
[url=http://www.defaoiteguitars.com]De Faoite Stringed Instruments[/url]
I agree totally re tradition with both Rick and Dave. There is no doubt about the fact that most every thing has been done before and done quite well. The problem is with perceived tradition out in the market place. Most players are not aware of the fact that adjustable necks have been around for a long time. They are more incline to assume that anything with exposed hardware is a new concept. I take on board Rick's comment that most players use to your run of the mill Martin are happy to accept the benefits that an adjustable neck will offer once explained to them, but it must surely be an easier sell when any exposed hardware looks cool and fruidy too.
Cheers
Kim
Cheers
Kim
- Dennis Leahy
- Blackwood
- Posts: 872
- Joined: Wed Oct 10, 2007 12:32 am
- Location: Duluth, MN, US
- Contact:
Rick, In an attempt to study your neck joint and exposed hardware, I went to your website and found some cool electrics and very modern looking hollow-body electric "semi-acoustic" guitars. Due to the thin bodies, I saw nothing that looks like a "typical" modern steelstring guitar. I only use the word "tradition" (in this discussion) in the sense of body depth and neck heel style on a steelstring guitar. In other words, I wanted to visualize what your adjustable neck hardware solution would look like on a guitar like Bob Connor's OM and dred guitars. I don't want to discount or dismiss your hardware solution - I want to see it, and did not find any example there. I can see a hint of it here, but can't see how you adjust the upper pivot points.
I don't want to fly off in a tangent too far in this thread about what "tradition" means. I promise, you would find me much more willing than 90% of luthiers to alter or abandon any tradition if I saw a reason to do it (or even on a whim.)
"...a new aesthetic emerges that neither hides..." Again, I can't visualize what you are doing in exposing the two upper setscrews (or their equivalent.) I might agree or disagree with your aesthetic on the hardware - if I saw it. But, I think that (for example) for luthiers that build with a truss rod nut erupting through the headstock of an acoustic steelstring, it would be a hard sell to get them to abandon truss rod covers - even though it does make it easier to adjust the truss rod.
If you read and fall under the spell of Babicz, you might believe in an adjustable neck where a player raises or lowers the action between songs in a set. That's not how I am thinking about the utility of an adjustable neck. My take on an adjustable neck is that it is a much easier way to allow a luthier to build a guitar where the neck angle is dead-nuts perfect, and thus the bridge and especially the saddle height can be optimized (at whatever height the luthier feel is optimum), and the string action can be set to a player's preference. Then, over the course of the life of the instrument, the neck angle can be altered back to *perfect* as the guitar soundboard shape (and body shape to a much lesser degree) distorts, or if there is a need for an action height change.
Now, I have already abandoned X-braces and stop bridges in my engineering mindset. I am going to use a variant of Tilton's Improvement: tunnel bridges, tailpieces, and rods from neck block to tail block. I mention that simply to say that I am convinced that soundboard bellying is not an inevitable outcome of a lightly braced, very active top. So, for me, an adjustable neck is not so much a failsafe against neck resets due to soundboard bellying.
[my opinion] To me, the adjustable neck joint would not be used to make a minor adjustment between songs in a set, and not even seasonally, but rather upon occasion over the years of life of the instrument. To me, that defines hardware that should be hidden. For me, if something needs to be tweaked frequently, then the hardware should be exposed. If the instrument is to live in a climate with big humidity swings and the instrument does require two seasonal neck angle changes, that is still not frequent enough to warrant external hardware. [/my opinion]
Dave, I have seen Howard Klepper's (and MacPherson's, and a few others) cantilevered fingerboard extensions, and just haven't either locked in with "that's it", nor have I figured out something myself. One problem is the truss rod nut (since, as you would already guess about my design aesthetic, I don't want the truss rod nut erupting through the headstock.)
Maybe this is fine:

(from Frank Ford's FRETS site)
Maybe having mass under the fingerboard extension (to make the fretted and "tapped" notes intensity and sustain sound similar to notes on the rest of the neck) is a myth. If so, I admit I have bought into it. I have about a dozen Katalox (Swartzia cubensis) fingerboard blanks that are close to 5/16" (about 8mm) thick, so maybe the fingerboard can be cantilevered without adding anything under it (but I still want to, for peace of mind.) Since I'm not using an upper transverse brace at all, my soundboard geometry can follow a dome ("longitudinal arching".) However, with the small radial soundboard braces I'm using, my top relaxed (flattened) itself a bit near the neck block (unlike the theoretical arcs in my CAD program!
) Using a variant of Grant Goltz's adjustable neck engineering, my first guitar has a fingerboard that appears to be glued to the soundboard, to a casual observer. A fully cantilevered fingerboard will lose that stealth aesthetic. Not a big deal, I guess. I do want notes above 14 to ring out - I would consider it an engineering flaw if they do not.
" It would be a shame to lose the yaw adjustment Dennis" Craig, I actually like the triangulated setscrew platform as the most versatile, and fully adjustable system. You just got me thinking about captured screws, so I mocked one up, thinking what if... and simply added it to the discussion. For some luthier who sees that thousands (maybe millions) of necks have been attached in a mortise without need for yaw adjustment, maybe that luthier might look on the double captured bolt with crossdowels and see something worth pursuing.
I for one will be patient and watch to see all the ideas on adjustable necks as this thread develops.
Dennis
I don't want to fly off in a tangent too far in this thread about what "tradition" means. I promise, you would find me much more willing than 90% of luthiers to alter or abandon any tradition if I saw a reason to do it (or even on a whim.)
"...a new aesthetic emerges that neither hides..." Again, I can't visualize what you are doing in exposing the two upper setscrews (or their equivalent.) I might agree or disagree with your aesthetic on the hardware - if I saw it. But, I think that (for example) for luthiers that build with a truss rod nut erupting through the headstock of an acoustic steelstring, it would be a hard sell to get them to abandon truss rod covers - even though it does make it easier to adjust the truss rod.
If you read and fall under the spell of Babicz, you might believe in an adjustable neck where a player raises or lowers the action between songs in a set. That's not how I am thinking about the utility of an adjustable neck. My take on an adjustable neck is that it is a much easier way to allow a luthier to build a guitar where the neck angle is dead-nuts perfect, and thus the bridge and especially the saddle height can be optimized (at whatever height the luthier feel is optimum), and the string action can be set to a player's preference. Then, over the course of the life of the instrument, the neck angle can be altered back to *perfect* as the guitar soundboard shape (and body shape to a much lesser degree) distorts, or if there is a need for an action height change.
Now, I have already abandoned X-braces and stop bridges in my engineering mindset. I am going to use a variant of Tilton's Improvement: tunnel bridges, tailpieces, and rods from neck block to tail block. I mention that simply to say that I am convinced that soundboard bellying is not an inevitable outcome of a lightly braced, very active top. So, for me, an adjustable neck is not so much a failsafe against neck resets due to soundboard bellying.
[my opinion] To me, the adjustable neck joint would not be used to make a minor adjustment between songs in a set, and not even seasonally, but rather upon occasion over the years of life of the instrument. To me, that defines hardware that should be hidden. For me, if something needs to be tweaked frequently, then the hardware should be exposed. If the instrument is to live in a climate with big humidity swings and the instrument does require two seasonal neck angle changes, that is still not frequent enough to warrant external hardware. [/my opinion]
Dave, I have seen Howard Klepper's (and MacPherson's, and a few others) cantilevered fingerboard extensions, and just haven't either locked in with "that's it", nor have I figured out something myself. One problem is the truss rod nut (since, as you would already guess about my design aesthetic, I don't want the truss rod nut erupting through the headstock.)
Maybe this is fine:

(from Frank Ford's FRETS site)
Maybe having mass under the fingerboard extension (to make the fretted and "tapped" notes intensity and sustain sound similar to notes on the rest of the neck) is a myth. If so, I admit I have bought into it. I have about a dozen Katalox (Swartzia cubensis) fingerboard blanks that are close to 5/16" (about 8mm) thick, so maybe the fingerboard can be cantilevered without adding anything under it (but I still want to, for peace of mind.) Since I'm not using an upper transverse brace at all, my soundboard geometry can follow a dome ("longitudinal arching".) However, with the small radial soundboard braces I'm using, my top relaxed (flattened) itself a bit near the neck block (unlike the theoretical arcs in my CAD program!

" It would be a shame to lose the yaw adjustment Dennis" Craig, I actually like the triangulated setscrew platform as the most versatile, and fully adjustable system. You just got me thinking about captured screws, so I mocked one up, thinking what if... and simply added it to the discussion. For some luthier who sees that thousands (maybe millions) of necks have been attached in a mortise without need for yaw adjustment, maybe that luthier might look on the double captured bolt with crossdowels and see something worth pursuing.
I for one will be patient and watch to see all the ideas on adjustable necks as this thread develops.
Dennis
Another damn Yank!
-
- Blackwood
- Posts: 310
- Joined: Sun Jan 13, 2008 10:22 am
- Location: Santa Cruz, Ca.
- Contact:
Dennis, you'll not find my acoustics on my website easily. Once again, be patient and wait for the Summer issue of Fretboard Journal to come out to see almost all of what I'm doing these days with acoustic guitars.
Mass under the fingerboard is not needed if you stiffen it up sufficiently.
I'll get some more photos going later...but for now:
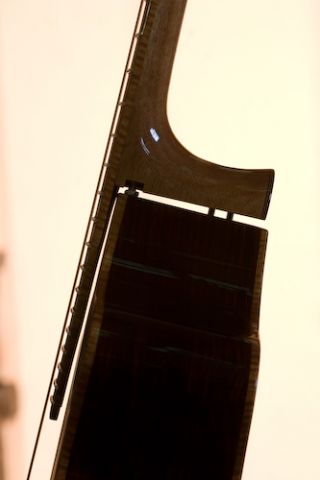
Mass under the fingerboard is not needed if you stiffen it up sufficiently.
I'll get some more photos going later...but for now:
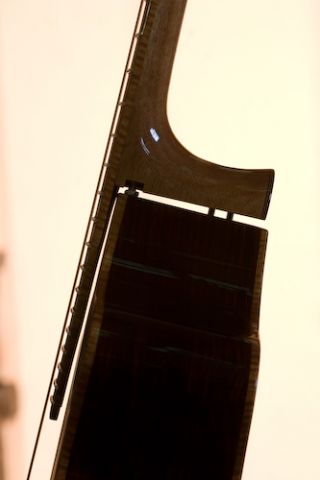
Rick Turner
Guitar Maker, Experimenter, Diviner
www.renaissanceguitars.com
www.d-tar.com
Guitar Maker, Experimenter, Diviner
www.renaissanceguitars.com
www.d-tar.com
-
- Blackwood
- Posts: 310
- Joined: Sun Jan 13, 2008 10:22 am
- Location: Santa Cruz, Ca.
- Contact:
That's from the treble side and clearly shows off the gaps between fingerboard and top and heel and body as well as showing the hex head pivot/yaw bolt on the treble side, the adjustment screw, and the locking screw (closest to the heel).
Let's see about an internal shot: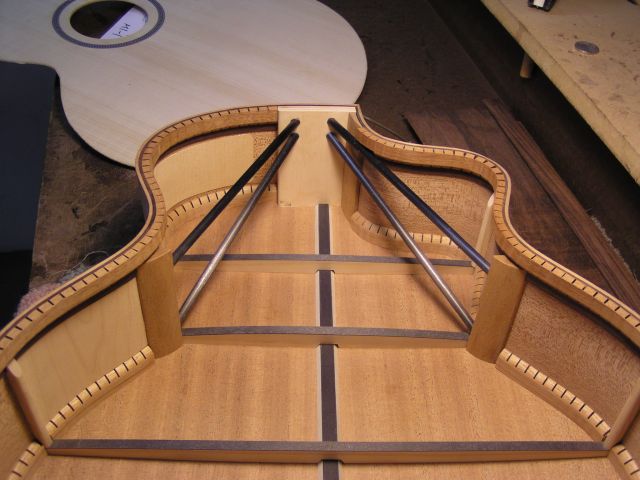
That's a different guitar, but it shows most of my internal build system including the flying buttress bracing, the side doubler, and then the reverse kerfing on top of that. Now I add a layer of CF to the reverse kerfing to stiffen it up even more, and on one guitar (that I really like), I used CF for binding.
And here are some truss rods: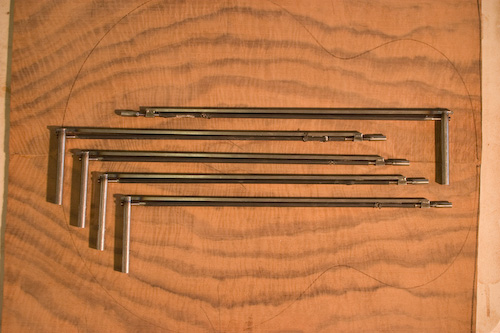
Let's see about an internal shot:
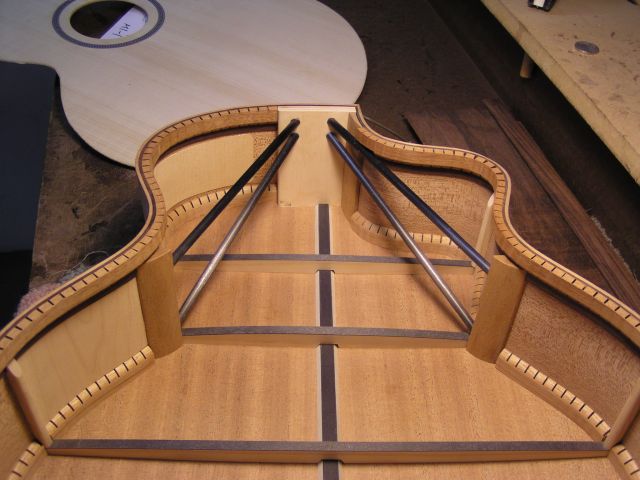
That's a different guitar, but it shows most of my internal build system including the flying buttress bracing, the side doubler, and then the reverse kerfing on top of that. Now I add a layer of CF to the reverse kerfing to stiffen it up even more, and on one guitar (that I really like), I used CF for binding.
And here are some truss rods:
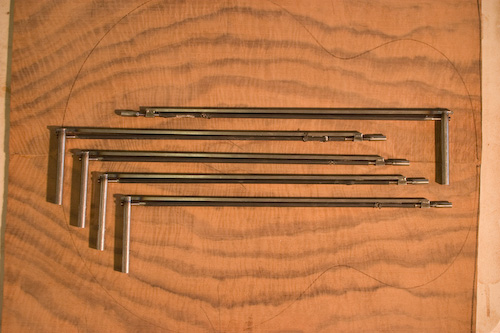
Rick Turner
Guitar Maker, Experimenter, Diviner
www.renaissanceguitars.com
www.d-tar.com
Guitar Maker, Experimenter, Diviner
www.renaissanceguitars.com
www.d-tar.com
- Dennis Leahy
- Blackwood
- Posts: 872
- Joined: Wed Oct 10, 2007 12:32 am
- Location: Duluth, MN, US
- Contact:
Hey Rick, there seems to be some shelf bracketsRick Turner wrote: And here are some truss rods:

So, you drill down into the heel. Hmmmm... what the heck is holding the cantilevered fretboard? From fret 15 and on, is it just CF? And if so, it does not appear to stick down, so it must not be the 1/2" CF bars stuff you use on the rest of the fingerboard.
Thanks for the extra photos.
Dennis
Jeff, I should say I'm most interested in concealed fasteners/adjusters, but I am warming somewhat to the idea of external/visible hardware. I do think that luthiers that plan to use a central soundhole (meaning the strings need to be slacked to access internal hardware) are probably going to get more excited about external hardware.jeffhigh wrote:How would those of you who do not like the idea of exposed fasteners on the heel feel about just having two 4mm dia holes.
I am tossing around an idea for concealing the fastening and adjusting bolts that ric's setup uses at the base of the heel with just an access hole for an allan key.
Jeff
Dennis
Another damn Yank!
-
- Blackwood
- Posts: 310
- Joined: Sun Jan 13, 2008 10:22 am
- Location: Santa Cruz, Ca.
- Contact:
The cantilevered fingerboard has two CF rods dadoed up into it, and then there's a tongue of CF between them from the truss rod dowel on out. I know it's very counterintuitive, but it works just fine. Notes played up over the cantilever don't sound any different than they do on the main part of the fingerboard other than the strings getting pretty short there. Because I dado the CF up into the fingerboard and down into the neck, I can use 1/2" tall by 1/8" wide pieces, and that extra height gives a geometric increase in stiffness.
Yes, that was a "marbled" Claro walnut back that went onto a guitar that came out very nice.
Also note the CF topped back center seam reinforcement with the CF topped back braces bridging over the center seam. That way the seam reinforcement becomes a true back brace; it isn't just reinforcing the glue joint. And you can see the minimalist 1/2" Baltic Birch neck block.
I'm telling you, guitarists do not mind the exposed hardware nearly as much as luthiers do. What does that tell me? That many luthiers are even more bound up in their concepts of traditional appearances than their potential customers... The other thing is that here we are putting these issues under a microscope...witch hunting, as it were. When I hand one of my guitars to a player, it takes a while for them to even notice the hardware; they're looking at the guitar as a whole. Then the first thing they tend to notice is the cantilevered fingerboard, and the reaction is immediately favorable. Then I demo the neck tilt, and all is well. I've never had a customer not buy one of my guitars because of the visible hardware. They may not like the guitar for some other reason, but it's not for a bit of stainless steel. Might as well complain about mechanical guitar tuners. Violin pegs look much better!
Yes, that was a "marbled" Claro walnut back that went onto a guitar that came out very nice.
Also note the CF topped back center seam reinforcement with the CF topped back braces bridging over the center seam. That way the seam reinforcement becomes a true back brace; it isn't just reinforcing the glue joint. And you can see the minimalist 1/2" Baltic Birch neck block.
I'm telling you, guitarists do not mind the exposed hardware nearly as much as luthiers do. What does that tell me? That many luthiers are even more bound up in their concepts of traditional appearances than their potential customers... The other thing is that here we are putting these issues under a microscope...witch hunting, as it were. When I hand one of my guitars to a player, it takes a while for them to even notice the hardware; they're looking at the guitar as a whole. Then the first thing they tend to notice is the cantilevered fingerboard, and the reaction is immediately favorable. Then I demo the neck tilt, and all is well. I've never had a customer not buy one of my guitars because of the visible hardware. They may not like the guitar for some other reason, but it's not for a bit of stainless steel. Might as well complain about mechanical guitar tuners. Violin pegs look much better!
Rick Turner
Guitar Maker, Experimenter, Diviner
www.renaissanceguitars.com
www.d-tar.com
Guitar Maker, Experimenter, Diviner
www.renaissanceguitars.com
www.d-tar.com
-
- Blackwood
- Posts: 310
- Joined: Sun Jan 13, 2008 10:22 am
- Location: Santa Cruz, Ca.
- Contact:
I just wanted to let you all know that Tom's idea about how to drill a centered hole in a brass dowel is terrific.
One tip that I will add, is that if you chuck the brass dowel in your drill press and then bring the end down onto the flat of a file or similar, you will be left with a nice circular pattern that makes it very easy to pick out the center when it comes time to drilling.
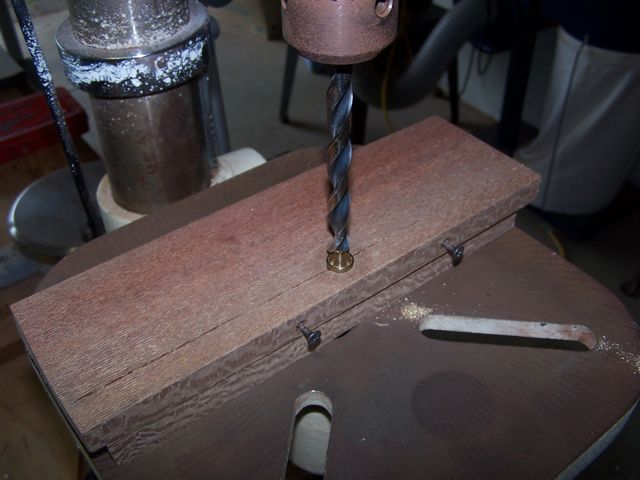
One tip that I will add, is that if you chuck the brass dowel in your drill press and then bring the end down onto the flat of a file or similar, you will be left with a nice circular pattern that makes it very easy to pick out the center when it comes time to drilling.
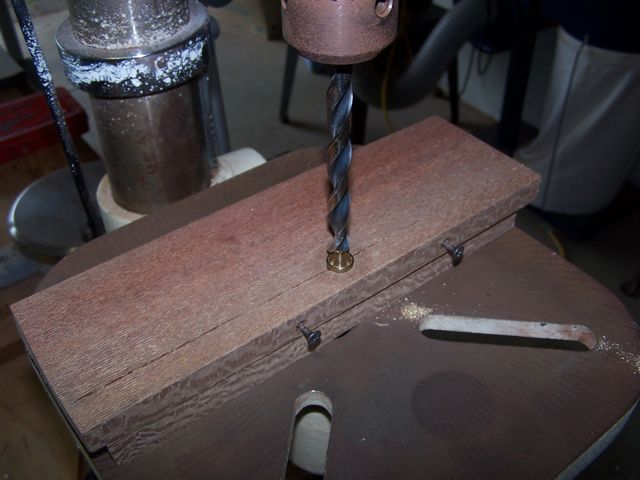
If that's working for you Allen , that's great . Thanks to Tom. I would clamp it to the table Allen .
I use a drill press vice that I bolt to the table and have a depth stop on the drill press . A 13/32 " ( 10.32 mm. ) for the screw head hole and 15/64 " ( 5.95 mm. ) for the screw shank.
Leave 4 mm. for the floor of the ferrule and make it over length ( 20 to 25 mm. ) so you can trim it to match your heel profile.
Once you have your heel profile , insert the ferrule and draw a line around it flush to the heel . Trim off to within a 1/32 " or so and round over the edges with wet and dry wrapped around a little dowel . Go to finer grades and finally , give it a really good session rubbing it on a felt block or cotton cloth with Brasso.
The smaller 3/8 " ( 9.5 mm ) ferrule has a 9/32 hole drilled straight through with no floor . It need only be about 1/2 " to 3/4 " in length . ( ignore the extra length it has in the pic. )
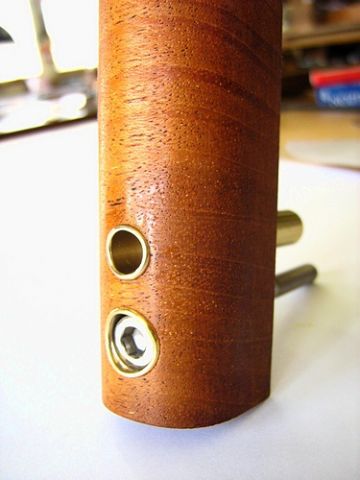
I 'm still thinking which one should be at the bottom of the heel . If I put the smaller setscrew on the bottom of the heel , it would allow me to trial doing without the top bolt altogether . I do however , like the added security of having a top bolt , for those guys who really yank at the neck whilst playing ,or just handling the instrument. Especially considering the neck has a floating fretboard extension
The top bolt assembly weighs about 18 grams which doesn't seem a whole lot of extra weight
It's only just dawned on me that it's actually the same sort of system Dave uses except mine is adjusted externally and has a T-Nut in the headblock. I think it's going to be a good solid reliable system , WITHOUT COMPROMISE TO FUNCTION OR AESTHETICS. Also easily made by the average Luthier.
I'll post my final plans within a couple of days.
Cheers , Craig
I use a drill press vice that I bolt to the table and have a depth stop on the drill press . A 13/32 " ( 10.32 mm. ) for the screw head hole and 15/64 " ( 5.95 mm. ) for the screw shank.
Leave 4 mm. for the floor of the ferrule and make it over length ( 20 to 25 mm. ) so you can trim it to match your heel profile.
Once you have your heel profile , insert the ferrule and draw a line around it flush to the heel . Trim off to within a 1/32 " or so and round over the edges with wet and dry wrapped around a little dowel . Go to finer grades and finally , give it a really good session rubbing it on a felt block or cotton cloth with Brasso.
The smaller 3/8 " ( 9.5 mm ) ferrule has a 9/32 hole drilled straight through with no floor . It need only be about 1/2 " to 3/4 " in length . ( ignore the extra length it has in the pic. )
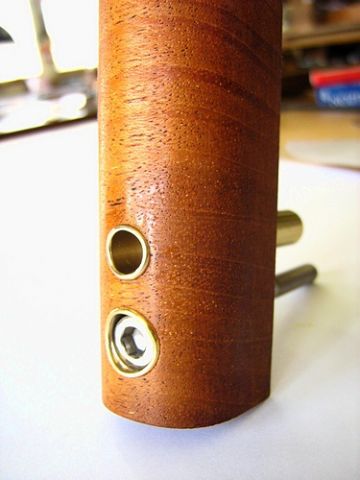
I 'm still thinking which one should be at the bottom of the heel . If I put the smaller setscrew on the bottom of the heel , it would allow me to trial doing without the top bolt altogether . I do however , like the added security of having a top bolt , for those guys who really yank at the neck whilst playing ,or just handling the instrument. Especially considering the neck has a floating fretboard extension
The top bolt assembly weighs about 18 grams which doesn't seem a whole lot of extra weight
It's only just dawned on me that it's actually the same sort of system Dave uses except mine is adjusted externally and has a T-Nut in the headblock. I think it's going to be a good solid reliable system , WITHOUT COMPROMISE TO FUNCTION OR AESTHETICS. Also easily made by the average Luthier.
I'll post my final plans within a couple of days.
Cheers , Craig
- Dennis Leahy
- Blackwood
- Posts: 872
- Joined: Wed Oct 10, 2007 12:32 am
- Location: Duluth, MN, US
- Contact:
Hi Craig,
Give it a go with a pointed (almond, stiletto) heel and see what you think. I think you've done a great job showing luthiers what it will look like in a rounded heel, but I think there are still a lot more luthiers using a pointy heel. Please don't use any more Tiger Myrtle for the test, though. Too precious!
Dennis
Give it a go with a pointed (almond, stiletto) heel and see what you think. I think you've done a great job showing luthiers what it will look like in a rounded heel, but I think there are still a lot more luthiers using a pointy heel. Please don't use any more Tiger Myrtle for the test, though. Too precious!

Dennis
Another damn Yank!
Dennis Leahy wrote:Hi Craig,
I think you've done a great job showing luthiers what it will look like in a rounded heel, but I think there are still a lot more luthiers using a pointy heel. Please don't use any more Tiger Myrtle for the test, though. Too precious!![]()
Dennis


I'll make up a stiletto type and see how it comes up . I was going to anyway, as I prefer them to the large width round ones. No Tiger ,,,,,I promise !

Cheers , Craig
-
- Blackwood
- Posts: 310
- Joined: Sun Jan 13, 2008 10:22 am
- Location: Santa Cruz, Ca.
- Contact:
- Tom Morici
- Blackwood
- Posts: 103
- Joined: Thu Nov 01, 2007 5:46 pm
- Location: Montana, USA
- Contact:
Allen,
I am glad the simple drilling jig worked for you. Im sure you will find ways to improve it.
Craig,Dennis,
Some of us prefer the look of the wide rounded heel (like me)
Is it better than the stiletto style? No, it is just what I like.
Dennis likes them because they remind him of a women's high heel shoe.
It may be why I don't like them, women that wear high heels, and the matching "bling" apparal, tend to be high maintenance. I prefer women
that are a little more down to earth. Pun intended.
Rick,
Of course the lathe is the best tool for making ferrules, or for other
odd's and ends. I own one and I would think that many others here
would like to own one at some point. Many do own a drill press, my intent
was to show a easier way to make a ferrule or two, with a drill press.
This may come as a shock to you, but there are a few, that live on a budget. Say Uncle Rick if you ever want to "Gift" some R&D funds to your
favorite Nephew Tom, I won't be insulted.
Tom
I am glad the simple drilling jig worked for you. Im sure you will find ways to improve it.
Craig,Dennis,
Some of us prefer the look of the wide rounded heel (like me)
Is it better than the stiletto style? No, it is just what I like.
Dennis likes them because they remind him of a women's high heel shoe.
It may be why I don't like them, women that wear high heels, and the matching "bling" apparal, tend to be high maintenance. I prefer women
that are a little more down to earth. Pun intended.
Rick,
Of course the lathe is the best tool for making ferrules, or for other
odd's and ends. I own one and I would think that many others here
would like to own one at some point. Many do own a drill press, my intent
was to show a easier way to make a ferrule or two, with a drill press.
This may come as a shock to you, but there are a few, that live on a budget. Say Uncle Rick if you ever want to "Gift" some R&D funds to your
favorite Nephew Tom, I won't be insulted.

Tom
Adding to what Tom said; most of the El Cheapo (toy) metal lathes, less than a couple grand, say, (what most of us can afford) are pieces of crap that I wouldn't waste one friggin cent on. After the $150k+ cnc metal lathes that I used to run (back in the olden days, before science took over my life) it'd be kinda embarrassing to own one of the cheapies. Wasting an endless amount of time trying to make tools run the way they should, right-out-of-the-box, isn't for me. I'm just too bloody old for shit like that.
Hello, I'm ranting again....
If I had a spare 8 grand or so, well then, that's another matter entirely
Hello, I'm ranting again....

If I had a spare 8 grand or so, well then, that's another matter entirely

Because I haven't got one RickRick Turner wrote:Why not use a metal lathe? They're terrific for all kinds of tasks.

The ones I have made on the drillpress have come up good ,so it's an alternative for some of the guys. It would be nice to be able to make the complete adjustable system without relying on an engineer to help out . That's what I had in mind from the start of this thread
Bob's engineering mate , Rick ( who is a member here), has offered to make up some for the guys who aren't tooled up enough to fabricate them . Our plan was to have a show of hands as to who needs them upon a final type plan. The independence of making your own would be good though, as the rest of the hardware are available off the shelf.
Tom , I know the type of woman you're referring to . Stiletto's eh,,




I agree Paul , Setting up machinery is very time consuming and sometimes frustrating. ( i.e. prick of a job ! ) Don't want to go there again in the very near future , if I can get away with it. ( i.e. lazy prick !

Cheers Craig
- Bob Connor
- Admin
- Posts: 3115
- Joined: Mon Jul 09, 2007 9:43 pm
- Location: Geelong, Australia
- Contact:
Which is one of the main reasons we set up this forum Craig. To allow us few blokes who could be considered "boutique builders" to share ideas and resources and costs to make the whole thing affordable enough so that we can develop innovations and share ideas, yet still stay within the realms of what would be considered "traditional instrument building".Craig L wrote: Bob's engineering mate , Rick (who is a member here), has offered to make up some for the guys who aren't tooled up enough to fabricate them .
Cheers Craig
Bob
- Dennis Leahy
- Blackwood
- Posts: 872
- Joined: Wed Oct 10, 2007 12:32 am
- Location: Duluth, MN, US
- Contact:
Tom,
It is true that I GREATLY prefer women that wear high heels to men that wear high heels.
Let's face it, those poor women in high heels are killing their feet - it is certainly a fashion for prurient reaction - and yes, I admit, it works on me. But my preference for a woman to be with rather than just look at is most certainly not high-maintenance. I'd much rather be with a woman with a big heart, a big smile, and a big laugh.
BTW, I don't dislike rounded heels on guitars - in fact, I have stabbed my hand on a few pointy ones and thought that the luthier got excessive, making a heel as deadly in a bar fight as a Florentine cutaway.
Dennis
It is true that I GREATLY prefer women that wear high heels to men that wear high heels.

Let's face it, those poor women in high heels are killing their feet - it is certainly a fashion for prurient reaction - and yes, I admit, it works on me. But my preference for a woman to be with rather than just look at is most certainly not high-maintenance. I'd much rather be with a woman with a big heart, a big smile, and a big laugh.
BTW, I don't dislike rounded heels on guitars - in fact, I have stabbed my hand on a few pointy ones and thought that the luthier got excessive, making a heel as deadly in a bar fight as a Florentine cutaway.
Dennis
Tom Morici wrote:...Dennis,
Some of us prefer the look of the wide rounded heel (like me)
Is it better than the stiletto style? No, it is just what I like.
Dennis likes them because they remind him of a women's high heel shoe.
It may be why I don't like them, women that wear high heels, and the matching "bling" apparal, tend to be high maintenance. I prefer women
that are a little more down to earth. Pun intended.
Tom
Another damn Yank!
Who is online
Users browsing this forum: No registered users and 3 guests