hey guys just a few more pics and good news its not swine flue!
Ive been feeling and still am feeling like death warmed up but you'd need a wrecking ball through my shed before i decide to hang up the tools on holidays. Anyway only a bit of progress this week so far but im now waiting on supplies before i start building again so here it is. Feel free to sledge or comment, its always good to see what people think.
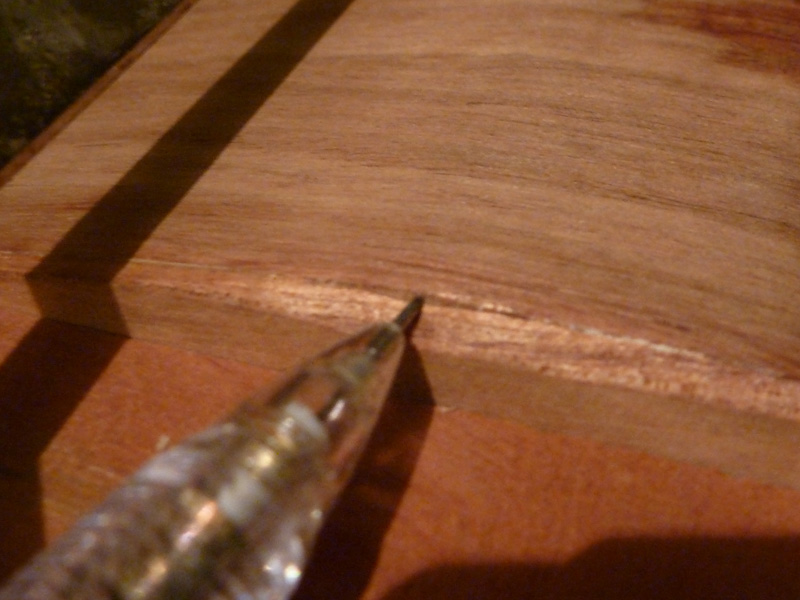
this is the chipout that i referred to last post, very fixable with binding.
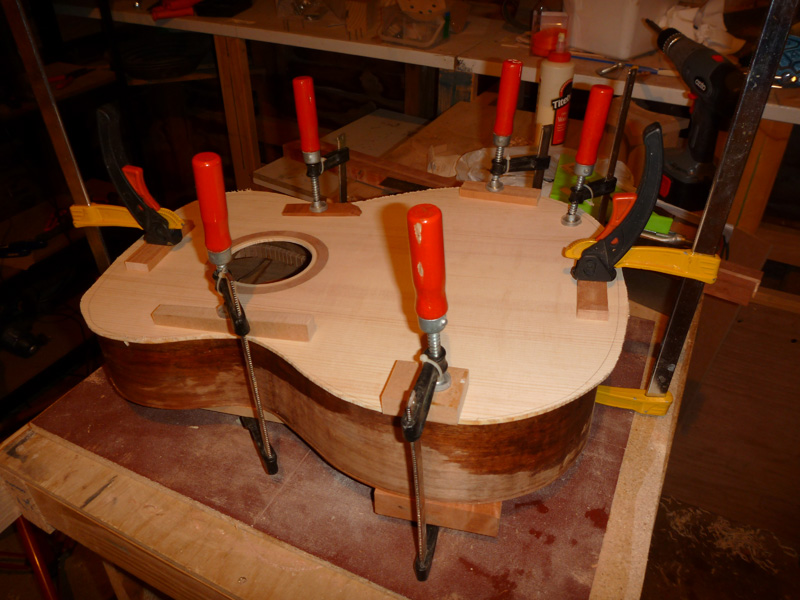
This is not as good as the rubber stretching method but i havn't had a puncture lately so it will do.

This is the first guitar ive built where there have been no gaps on the soundboard join to the sides and kerfing. Im as proud as punch with this one.
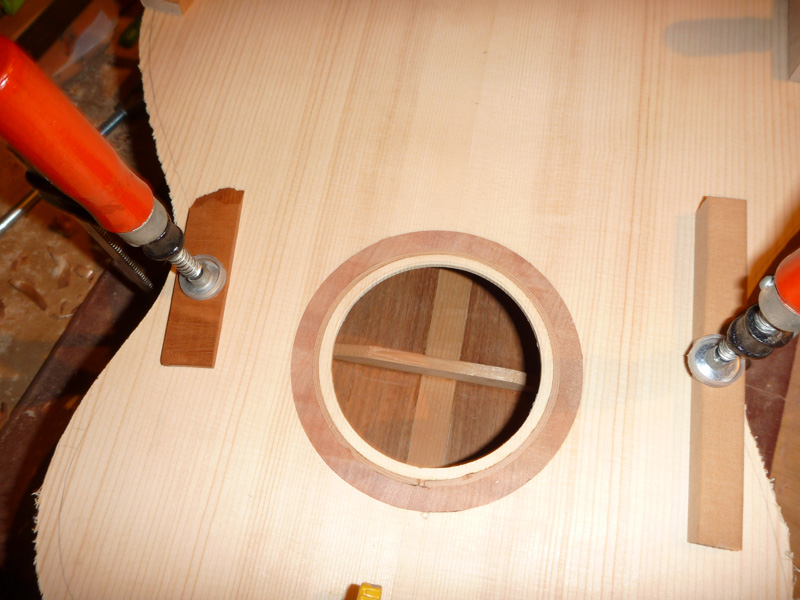
i didn't really sand the corners off the bracing here because i saw some cole clark bracing not long ago and i think it kinda looks tough. i may change my mind here what do you think?
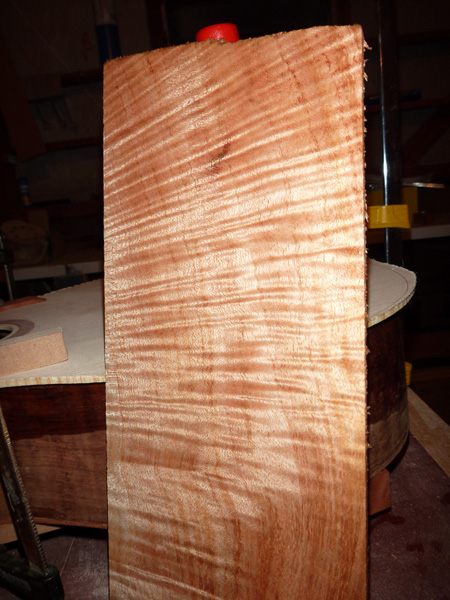
This is going to be the headstock material that i am using, it is some of my fiddleback qld maple that austen wants me to burn because it is not any good.
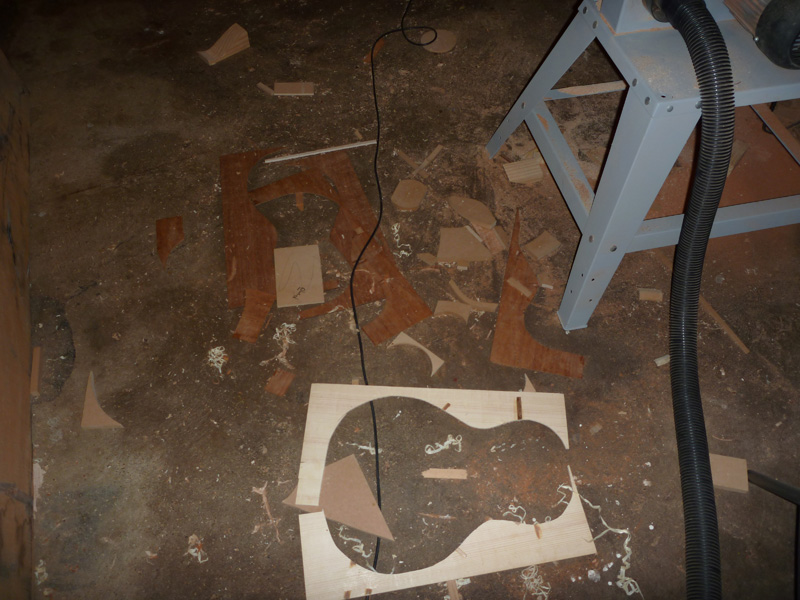
This one is for our friend Hesh. I call this photo "can hardly breathe at the moment so f?*k it, ill do it later". This is the worst my shed has looked ever. That makes me think how often do you clean the scraps and dust up in your shed hesh? Also if you have any spare leaves can i have one out of your book?
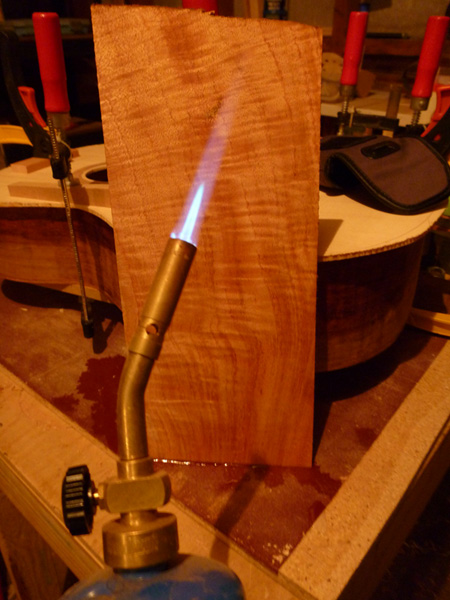
This one is for my jerk friend who may need cheering up at the moment. I told you i tried but it just didnt burn. so what now? hope yopu feel better soon buddy. Untill next time hoo roo xray.