Before i go using some of my really cool/ expensive timber i am going to keep using the plain boring blackwood with no figure and slightly backsawn. This is okay though because it has some interesting patterns towards the edge. The materials:
Top 1= Adirondack spruce from tim spittle
Bracing is all western red cedar on first guitar + back and side bracing
Top 2= AA Grade Engleman Spruce from Michael
Bracing is all Engleman on second guitar + back and side bracing
Neck on number 1 is Silky Oak+ Blackwood strip in middle
Back and sides on both is Tasmanian Blackwood but very plain.
Heres some pics for starters.
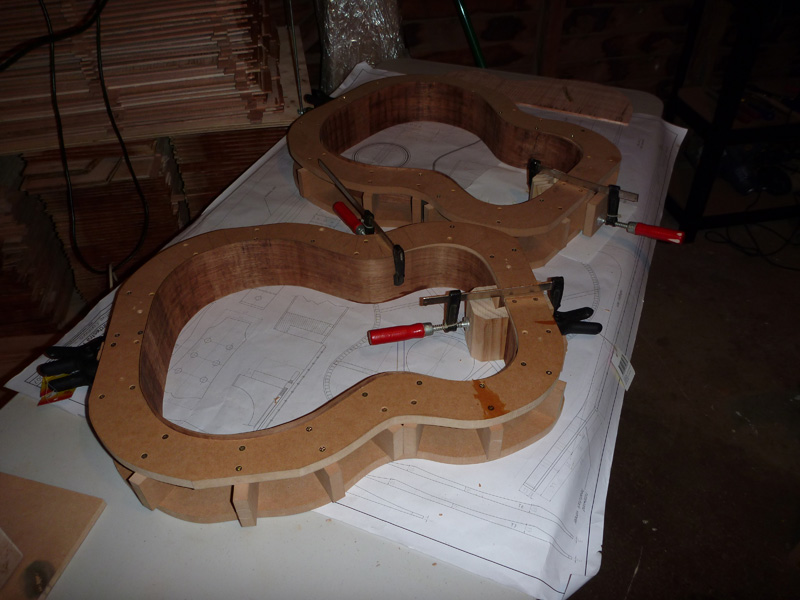
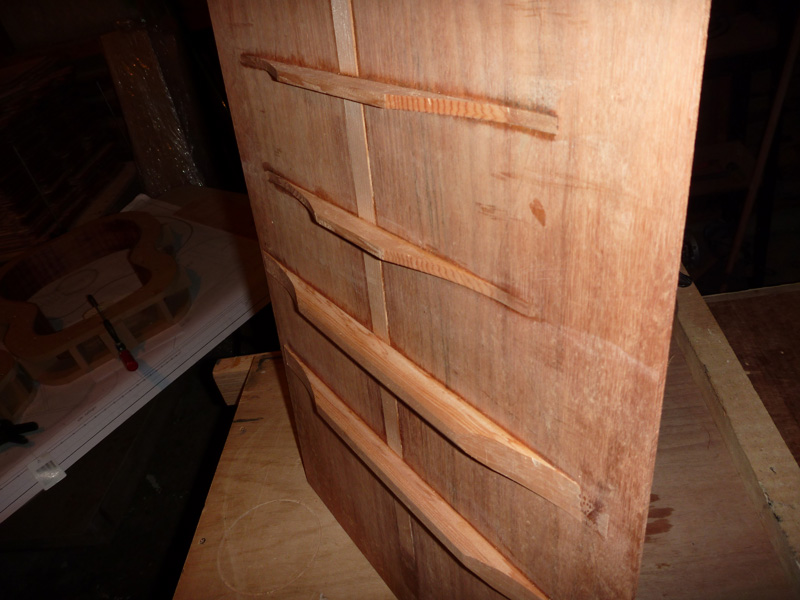
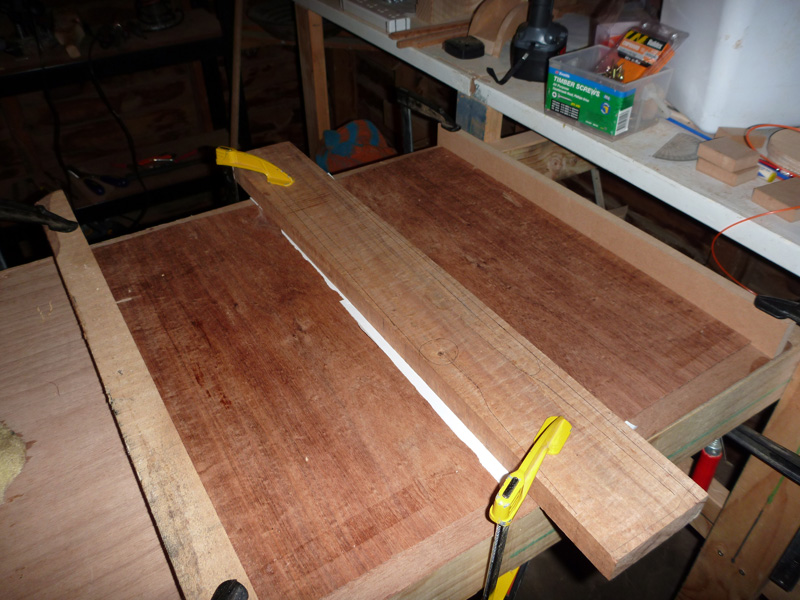
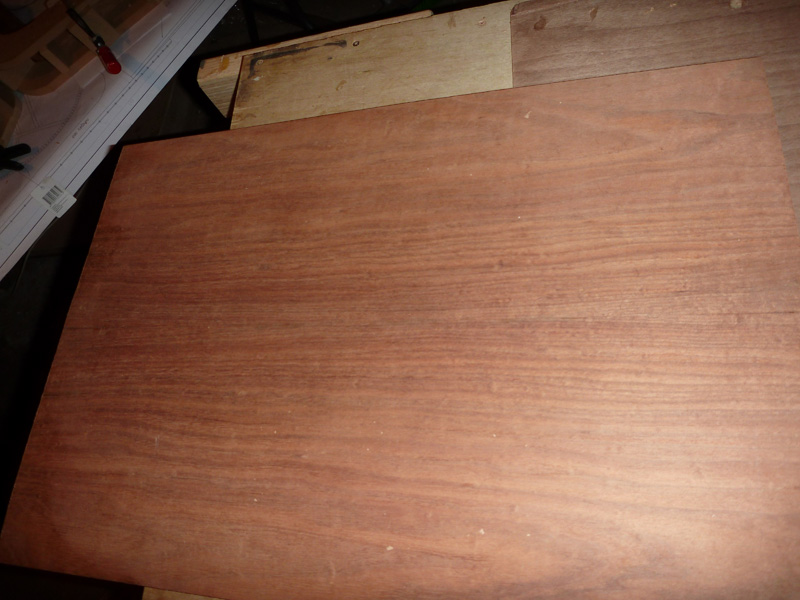
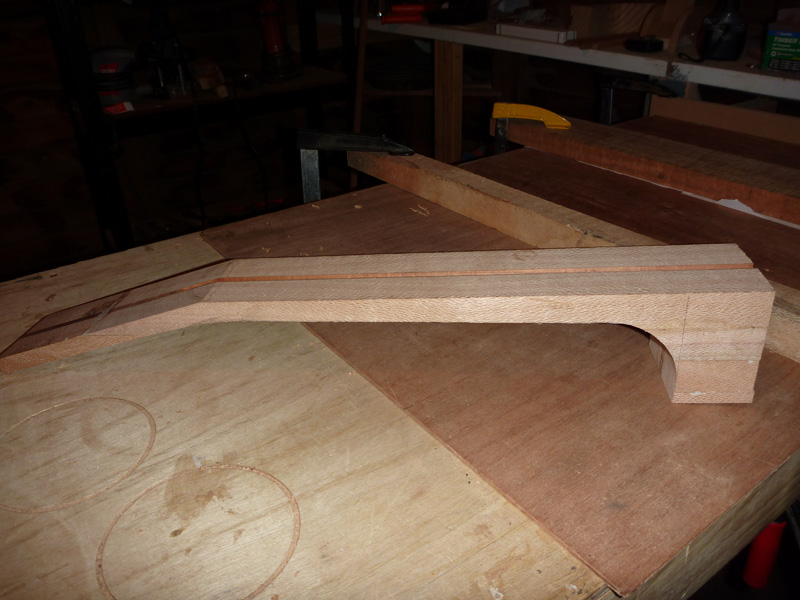
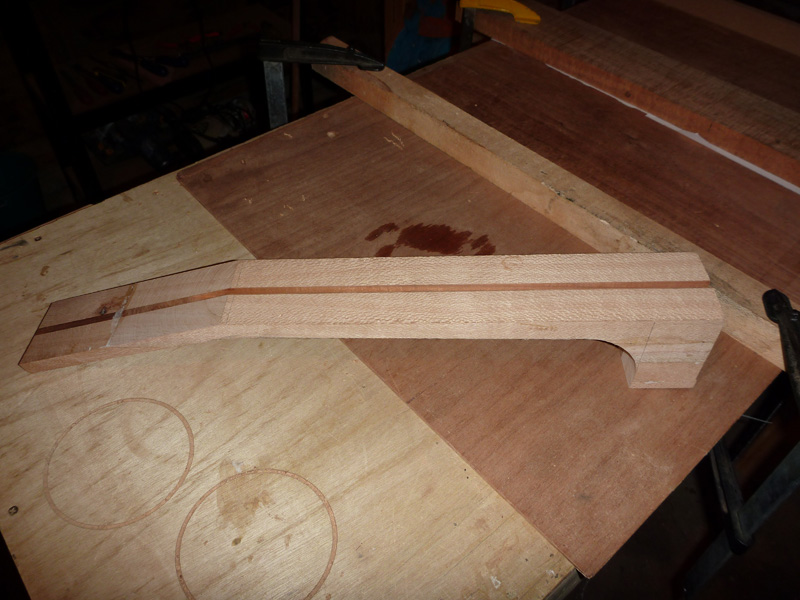
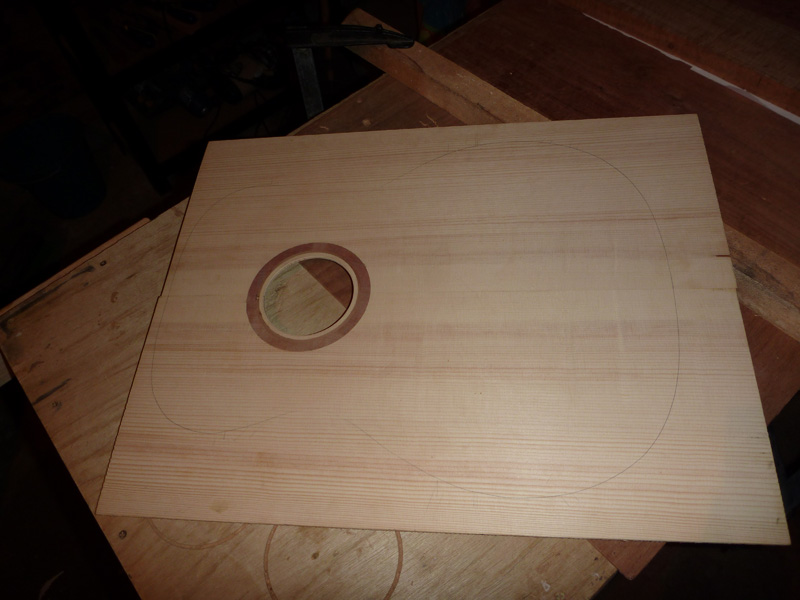
please feel free to comment and ill have more pics soon