Flat top guitar mould
Flat top guitar mould
Hi
I have noticed on some of the pictures posted on this and other forums the different types of guitar body moulds used by builders.
I have begun my first guitar build which is a kit from Stewart Macdonald and while I am happy with this basic approach I am now thinking about the next project.
Do you have any advice as to the type and style of mould I should be thinking about and its advantages/disadvantages?
I have noticed on some of the pictures posted on this and other forums the different types of guitar body moulds used by builders.
I have begun my first guitar build which is a kit from Stewart Macdonald and while I am happy with this basic approach I am now thinking about the next project.
Do you have any advice as to the type and style of mould I should be thinking about and its advantages/disadvantages?
- graham mcdonald
- Blackwood
- Posts: 473
- Joined: Thu Oct 25, 2007 11:57 am
- Location: Canberra
- Contact:
It rather depends on how you go about building your guitars. A solid mould for holding the sides is excellent if you are going to make a few of a particular style (or just like making moulds and other jigs) An alternative to consider is the adjustable workboard as described in Jim Williams' book which can be altered to just about any shape.
good luck
graham
good luck
graham
Graham McDonald
http://www.mcdonaldstrings.com
http://www.mcdonaldstrings.com
G'day Drjay.
First off, can I ask you to either sign your posts so we can learn your name, so to address you with some sort of respect, or better yet, go into your profile settings and set a signature there.
Now on to your question. Lot's of types of molds, and it sort of depends on the type of instrument that you're looking at building. For acoustic steel string guitars, the most popular way now is a solid outside form.
This is the type that I'm using, as well as many of the members here. There are heaps of variations on how to build them, but they all pretty well accomplish the same thing. That is hold the rims in shape and hopefully square. They also will last for years with proper care, and build many instruments. One of the advantages is that you can vary the amount of dome that you put on your top without any modification to the mold at all. If you require to clamp the rims to the mold, this is something that is also easy to do. Most will use spreaders to press the rims snug against the mold during the construction process, then pull the spreaders out through the sound hole once the body is closed up.
They do cost a bit to make, and you do need to make new molds for each body style that you wish to make. It's amazing how quickly you can acquire several different molds.
They also provide these nice off cuts that just happen to be the right size and shape to build bending forms for the side bender. A very big advantage and great use of otherwise waist material.
There is the Spanish Plantilla / adjustable work board that is more popular with the Classical building crowd using a Spanish Heel. I've not built like this, so perhaps those that have will be able to comment further.
From the examples that I've seen, you do have the option of being able to change the shape of the dowels that define the shape of the body quiet easily. Something not possible with a solid mold. I think that you will either be building with a totally flat top, or design the work-board in such a manner to give some dome to the top, but not something that is easily changed.
I believe that Stew Mac's kits call for a inside mold made from cardboard? It obviously works, but probably is really only good for one or two builds, then you need to make another. The obvious advantages are cost, and easy construction of the form.
And then there are a few builders that build without molds at all. But they're few and far between. Obvious advantage is lack of cost, and saved space. It works for them, but I'm not lining up to try their method.
First off, can I ask you to either sign your posts so we can learn your name, so to address you with some sort of respect, or better yet, go into your profile settings and set a signature there.
Now on to your question. Lot's of types of molds, and it sort of depends on the type of instrument that you're looking at building. For acoustic steel string guitars, the most popular way now is a solid outside form.
This is the type that I'm using, as well as many of the members here. There are heaps of variations on how to build them, but they all pretty well accomplish the same thing. That is hold the rims in shape and hopefully square. They also will last for years with proper care, and build many instruments. One of the advantages is that you can vary the amount of dome that you put on your top without any modification to the mold at all. If you require to clamp the rims to the mold, this is something that is also easy to do. Most will use spreaders to press the rims snug against the mold during the construction process, then pull the spreaders out through the sound hole once the body is closed up.
They do cost a bit to make, and you do need to make new molds for each body style that you wish to make. It's amazing how quickly you can acquire several different molds.
They also provide these nice off cuts that just happen to be the right size and shape to build bending forms for the side bender. A very big advantage and great use of otherwise waist material.
There is the Spanish Plantilla / adjustable work board that is more popular with the Classical building crowd using a Spanish Heel. I've not built like this, so perhaps those that have will be able to comment further.
From the examples that I've seen, you do have the option of being able to change the shape of the dowels that define the shape of the body quiet easily. Something not possible with a solid mold. I think that you will either be building with a totally flat top, or design the work-board in such a manner to give some dome to the top, but not something that is easily changed.
I believe that Stew Mac's kits call for a inside mold made from cardboard? It obviously works, but probably is really only good for one or two builds, then you need to make another. The obvious advantages are cost, and easy construction of the form.
And then there are a few builders that build without molds at all. But they're few and far between. Obvious advantage is lack of cost, and saved space. It works for them, but I'm not lining up to try their method.
Re: Guitar Mold
Thank you Graham and thank you Allen. I appreciate your advice and will give the whole process some thought. I have looked at different designs in the books and get put off with this point abount 15' and 25'radius boards required to construct a dome on the top and bottom or are these not needed in flat top construction?
I am leaning towards an adjustable mold so that it can accommodate different models but suspect that they are expensive items. Does anyone have any pictures or tutorials on this topic?
Sorry for leaving out my name (us newbies have to make mistakes before we become established)
Cheers
I am leaning towards an adjustable mold so that it can accommodate different models but suspect that they are expensive items. Does anyone have any pictures or tutorials on this topic?
Sorry for leaving out my name (us newbies have to make mistakes before we become established)
Cheers
Jim Latham
Tecoma
Tecoma
While you'll hear your standard acoustic guitar referred to as a flat top, they are in most cases not a true flat top. They will have a dome built into the top and back plates. Generally somewhere in the range of the numbers you gave. Many good reasons for doing this, and very few reasons not to. It's most common to use a radius dish to glue the braces on to the top and back plates to create this radius, but there are other methods as well.
Graham has a very good tutorial on building one style of radius dish in our Tutorial Section. I built mine out of 2 layers of MDF that I built a jig to dish out the center with my router. My method makes a nice dish, but the amount of dust it creates is something you have to see to believe. If I had known about Grahams method, then I would have gone with his.
As you're first one is a StewMac Kit, you might find the Kit Guitar Forum helpfull.
Read heaps and ask lots of questions. There aren't any dumb questions. In fact we like the questions, as it stimulates discussion on various aspects of building.
Graham has a very good tutorial on building one style of radius dish in our Tutorial Section. I built mine out of 2 layers of MDF that I built a jig to dish out the center with my router. My method makes a nice dish, but the amount of dust it creates is something you have to see to believe. If I had known about Grahams method, then I would have gone with his.
As you're first one is a StewMac Kit, you might find the Kit Guitar Forum helpfull.
Read heaps and ask lots of questions. There aren't any dumb questions. In fact we like the questions, as it stimulates discussion on various aspects of building.
- graham mcdonald
- Blackwood
- Posts: 473
- Joined: Thu Oct 25, 2007 11:57 am
- Location: Canberra
- Contact:
Here is my universal guitar workboard. 3/4" ply with some 2x1 underneath so it can go into a vice.
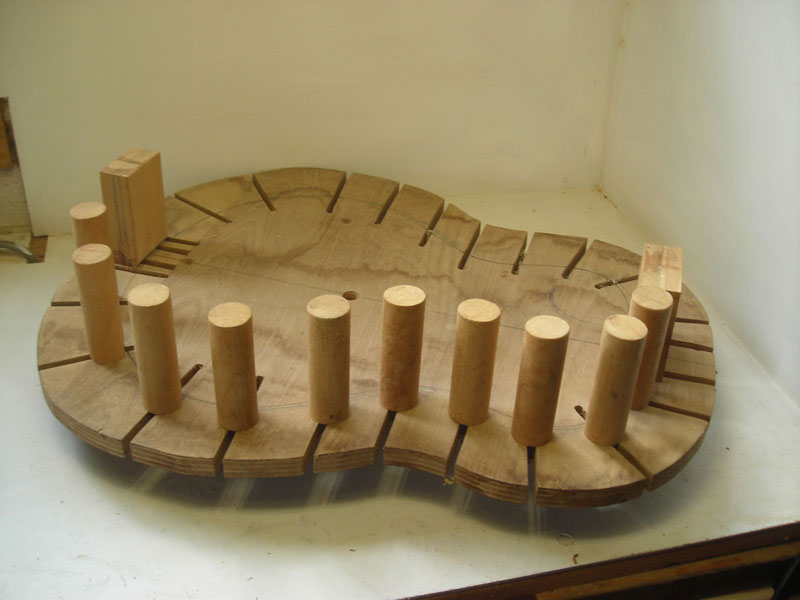
The end blocks are attached with lag bolts and wing-nuts
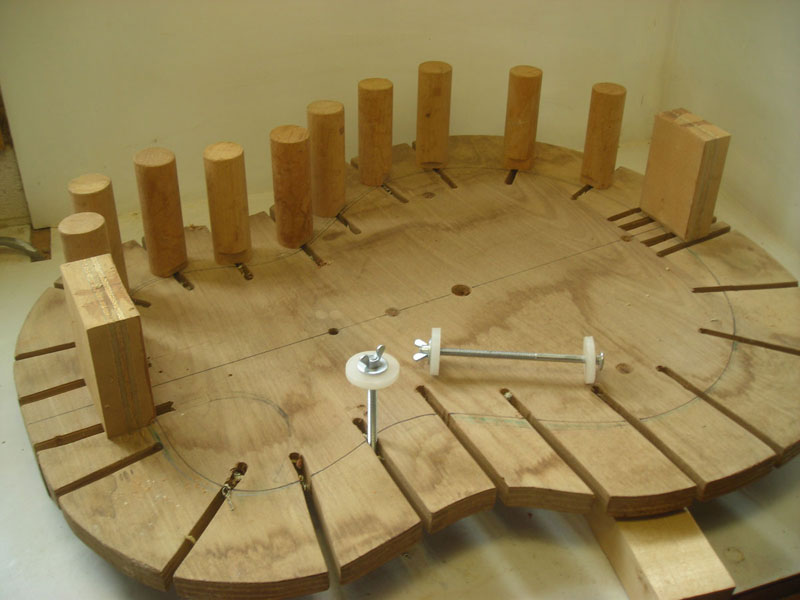
Using long bolts with big polyethelene (kitchen chopping board material) washers the workboard can also be used for gluing the back with the soundboard supported in its slight arching
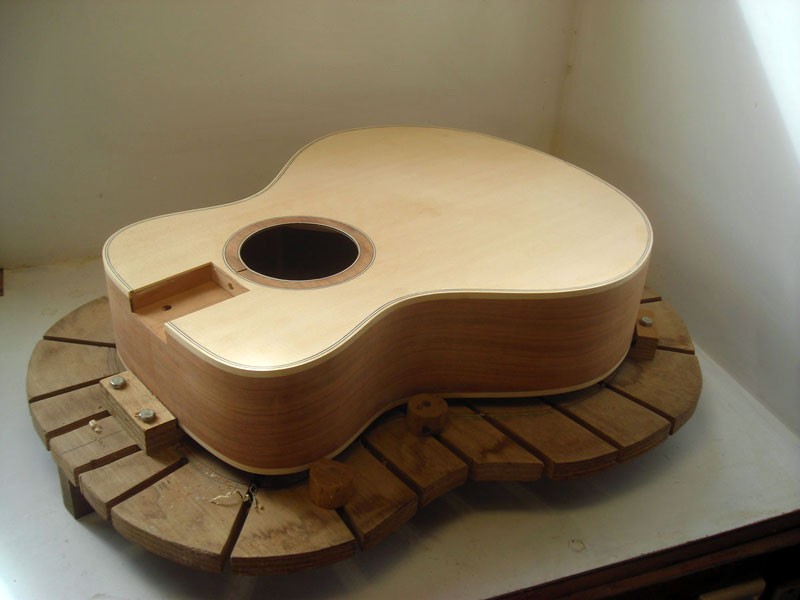
And with a couple of extra little brackets it holds the body for sanding as well
Hope that is a little useful
graham[/img]
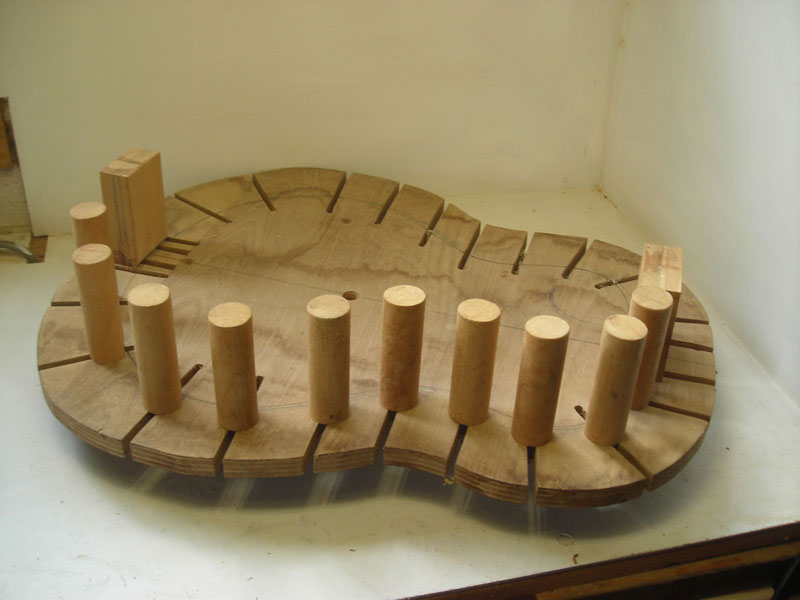
The end blocks are attached with lag bolts and wing-nuts
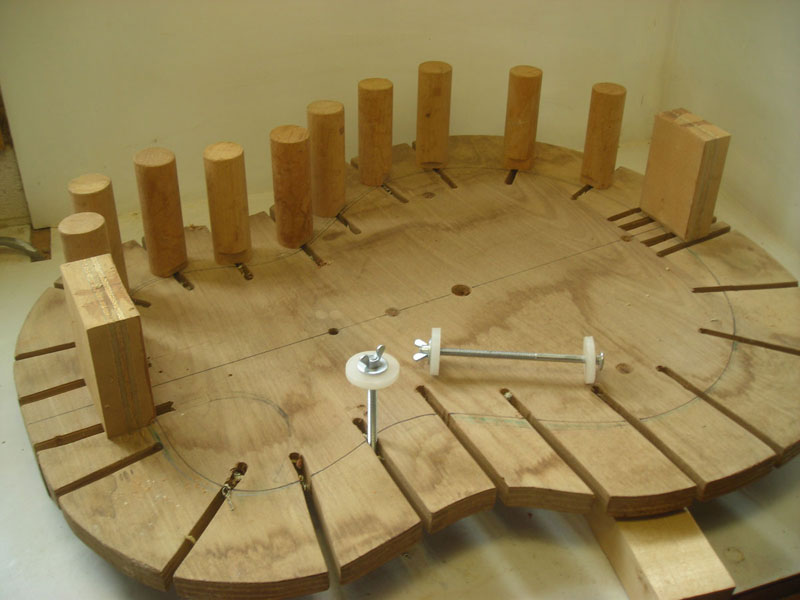
Using long bolts with big polyethelene (kitchen chopping board material) washers the workboard can also be used for gluing the back with the soundboard supported in its slight arching
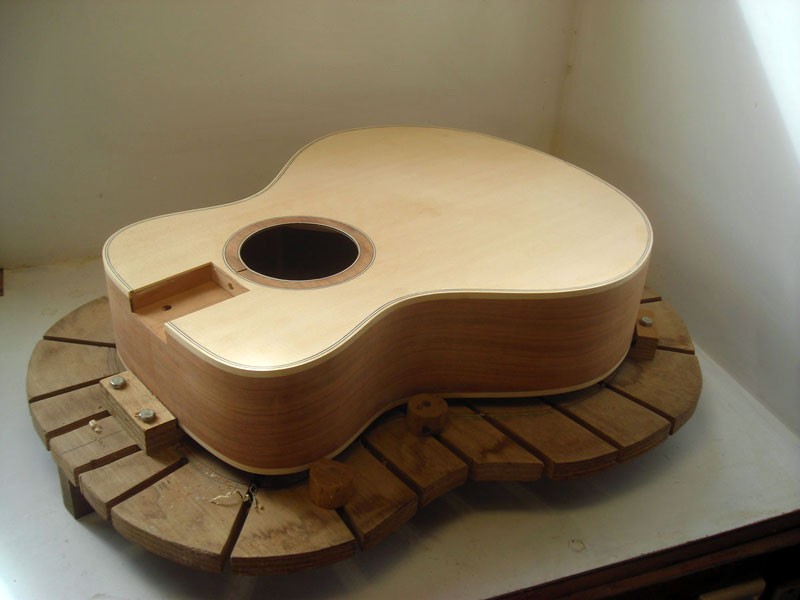
And with a couple of extra little brackets it holds the body for sanding as well
Hope that is a little useful
graham[/img]
Graham McDonald
http://www.mcdonaldstrings.com
http://www.mcdonaldstrings.com
- DarwinStrings
- Blackwood
- Posts: 1873
- Joined: Thu Nov 13, 2008 10:27 pm
- Location: Darwin
Jim,
Graham's board looks flat. This is where the universal work board differs from the traditional solera used when constructing using the Spanish Method. Using the latter method the neck and top are one unit and lie face down on the solera. You then build up the sides and add the back before the guitar comes of the solera.
Cheers Martin
Graham's board looks flat. This is where the universal work board differs from the traditional solera used when constructing using the Spanish Method. Using the latter method the neck and top are one unit and lie face down on the solera. You then build up the sides and add the back before the guitar comes of the solera.
Cheers Martin
- graham mcdonald
- Blackwood
- Posts: 473
- Joined: Thu Oct 25, 2007 11:57 am
- Location: Canberra
- Contact:
This one is flat, though I have another with a scoop in the lower bout that I modified for a classical I recently built following Eugene Clark's methodology that was written up a year or so ago in American Lutherie. The guitar in the pic was built on the workboard with the arch on the soundboard supported by two crescents of thick card that extend around the edge of the lower bout to the waist. The soundboard above the waist is essentially flat with the 25' curve in the X braces only sanded in below the crossover. On this instrument I built it like a Spanish classical, but without the integral neck. The soundboard and sides are animal glued together with tentalones and then the back added.
This sort of jig can also be used in the same way as a solid mould to put together the sides, blocks and linings. I don't radius the soundboard edge of the sides, just keep them flat, but the back edge gets radiused to 15' with a piece of tubing inserted into the large hole in the middle of the lower bout and the sandpaper covered radiused dish rotated around it . I find this a versatile and flexible approach for a mould, especially if you don't want to go into production with a particular body shape. Mine kee4p evolving so this works well. It works for both guitars and my guitar bodied bouzoukis and I have a couple more for different bouzouki types.
cheers
graham
This sort of jig can also be used in the same way as a solid mould to put together the sides, blocks and linings. I don't radius the soundboard edge of the sides, just keep them flat, but the back edge gets radiused to 15' with a piece of tubing inserted into the large hole in the middle of the lower bout and the sandpaper covered radiused dish rotated around it . I find this a versatile and flexible approach for a mould, especially if you don't want to go into production with a particular body shape. Mine kee4p evolving so this works well. It works for both guitars and my guitar bodied bouzoukis and I have a couple more for different bouzouki types.
cheers
graham
Graham McDonald
http://www.mcdonaldstrings.com
http://www.mcdonaldstrings.com
Who is online
Users browsing this forum: No registered users and 90 guests