
Its raining in Canberra so I can't do any gluing. Thought I'd show you what I am working on.
Someone posted a lovely Spalt maple CS336 a while ago and I instantly wanted one.
I have a nice piece of maple from Perry Ormsby for the top and I have a 3m slab of Sapele which I use for bodies. Here I have glued up the maple top and roughed out the Sapele body. I still need to make the routing templates.
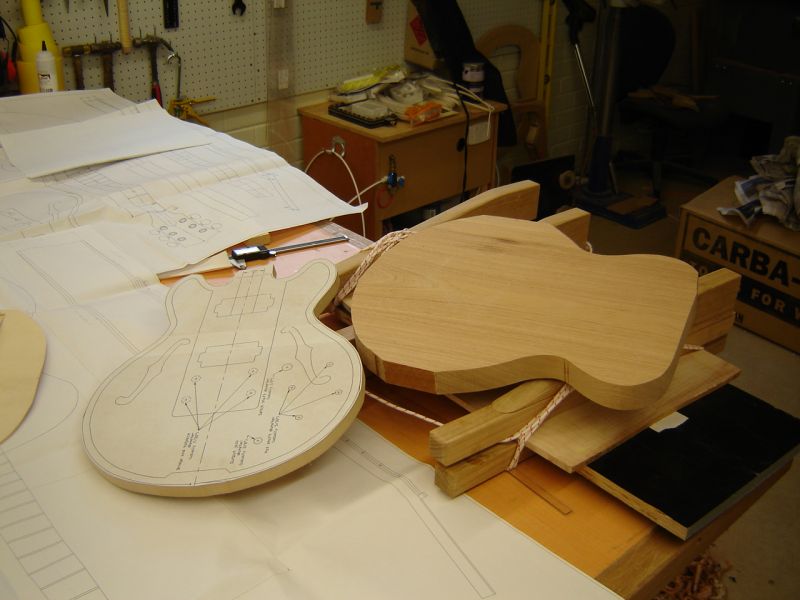
Here is the maple top. This will look great with a stain. The Gibson web site has an up speced CS356 in red with gold hardware that looks great.
http://www.gibsoncustom.com/flash/produ ... S-356.html
I could go for something like that.
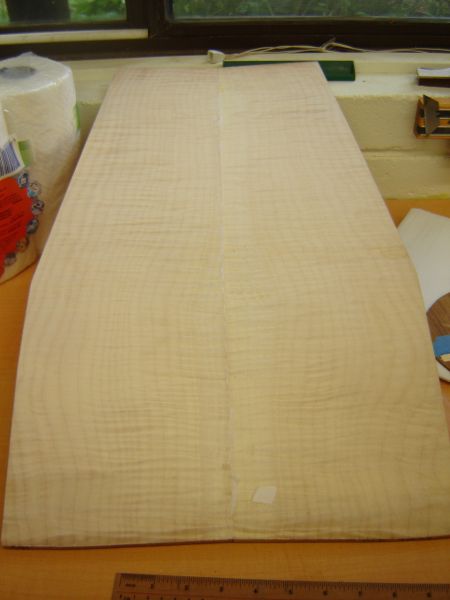
I have also been making an MJ. Carp spruce top and blackwood B&S. I have followed the plans very closely including the brace scalloping.
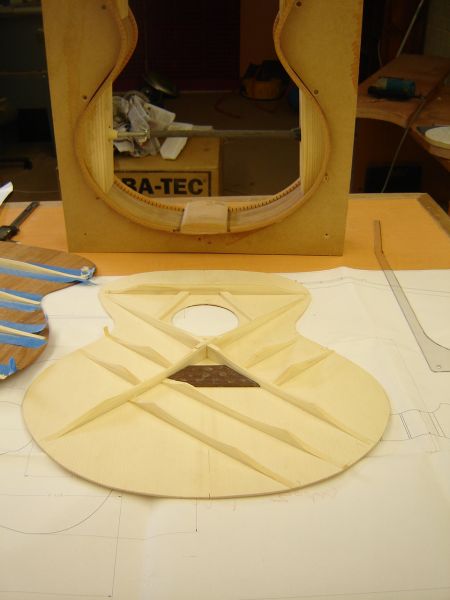
But I have used a large foot on the head block that is dovetailed into the block to increase glue surface. The idea to stabilise the neck block area with a foot is from an article in the Winter 2007 GAL journal on Eugene Clark. Very interesting article btw.
In theory it is trying to do that same thing as flying braces like Mr Turner et al. The end of the foot will meet up with the upper cross brace to help distribute the force from the strings over a larger area and prevent the neck pulling up over time. That's the theory anyway!
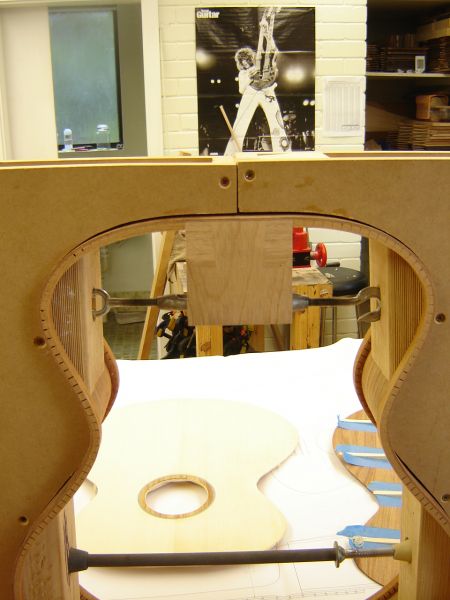
Dom