I finally got back out there in the past few days. After preparing the sides I began the bending today with my first side and the new system - but all was in vain.
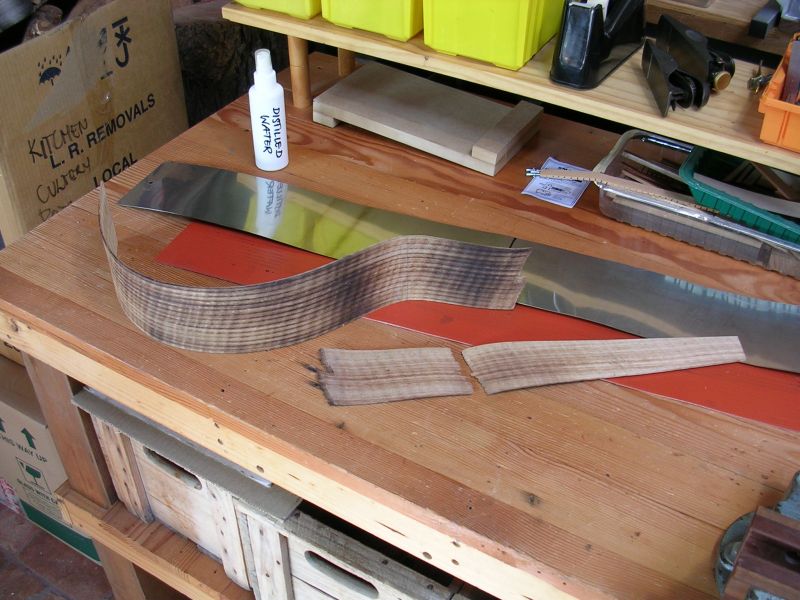
I sprayed both sides of the timber and layed the blanket on top followed by a stainless steel sheet. I turned it all on and after 2 - 3 minutes there was a lot of steam.
I turned off the blanket as I thought it was getting too hot and began the bending process. Centre partly down, then large bout, followed by the small bout.
The wood still seemed a little stiff so turned on the blanket again for another 2-3 minutes. I again began tightening everything up and turned off blanket. However, I heard cracking and realised the side had broken and part of the side was burnt.
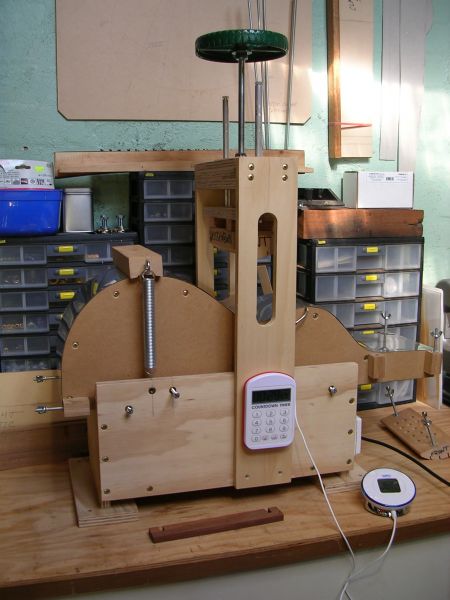
Above is a pic of my bender.
I am now at a loss to know what to do differently with the other remaining side. I should at least sacrifice this to hopefully get a little closer to getting the bend right.
Any advice gratefully appreciated.