Finishing by hand...what to use?
Finishing by hand...what to use?
First off , let me say . I have no experience in applying finish.
I want to do a finish by hand...especially hand rubbed.. I don't have spray facilities and i don't really want to use a brush.
I have been looking at either french polish/hard shellac type finish or tru-oil.
I've been reading the Milburn tutorial and it looks pretty comprehensive.
Some things I have been wondering are..
Is it better to seal with z-poxy and then maybe french polish with ubeaut hard shellac? will these products work together.?
or is it better to use the old method of pumice as outlined in the tutorial.?
Tru-oil has me intrigued but I'm wondering how it goes using it on an oily timber like rosewood? and I'm not so sure about using it on a soundboard?
While I'm waiting for some bridge tools to turn up I may as well get the ball rolling with practising my finish on some scrap.
cheers Grant
I want to do a finish by hand...especially hand rubbed.. I don't have spray facilities and i don't really want to use a brush.
I have been looking at either french polish/hard shellac type finish or tru-oil.
I've been reading the Milburn tutorial and it looks pretty comprehensive.
Some things I have been wondering are..
Is it better to seal with z-poxy and then maybe french polish with ubeaut hard shellac? will these products work together.?
or is it better to use the old method of pumice as outlined in the tutorial.?
Tru-oil has me intrigued but I'm wondering how it goes using it on an oily timber like rosewood? and I'm not so sure about using it on a soundboard?
While I'm waiting for some bridge tools to turn up I may as well get the ball rolling with practising my finish on some scrap.
cheers Grant
Hi Grant,
Im a hand finish man....all instruments to date have been French polished. The first classical was pore filled using pumice as per the Milburn tutorial and turned out ok. Pumice filling is a laborious method of pore filling and is a pain when you get too much pumice building up. One thing I found also was that if you spend too much time working pumice you get leaching of the colour out of rosewoods.
Subsequent guitars have been pore filled using Z-poxy. Two coats neat and a final coat thinned 50% with alcohol. All coats sanded back to bare wood. Z-Poxy is now my preferred pore filling method.
U-beaut hard shellac? I have to say I didnt have much luck French polishing with HS. I was however using the old formula...Neil from Ubeaut changed the formula a bit after talking with a few luthiers who were using his product.
Cheers Martin
Im a hand finish man....all instruments to date have been French polished. The first classical was pore filled using pumice as per the Milburn tutorial and turned out ok. Pumice filling is a laborious method of pore filling and is a pain when you get too much pumice building up. One thing I found also was that if you spend too much time working pumice you get leaching of the colour out of rosewoods.
Subsequent guitars have been pore filled using Z-poxy. Two coats neat and a final coat thinned 50% with alcohol. All coats sanded back to bare wood. Z-Poxy is now my preferred pore filling method.
U-beaut hard shellac? I have to say I didnt have much luck French polishing with HS. I was however using the old formula...Neil from Ubeaut changed the formula a bit after talking with a few luthiers who were using his product.
Cheers Martin
- sebastiaan56
- Blackwood
- Posts: 1274
- Joined: Sun Oct 28, 2007 5:23 am
- Location: Blue Mountains
Hi Grant,
Like Kiwi I have gone to Zpoxy for pore filling and then a hand rubbed finish. I have used also Hard Shellac with good results. I used BLO as the lubricant for the rubber so maybe thats why its worked well for me.
My latest instrument was finished with Tru-Oil and i have to say Im delighted. I think the secret of hand applied finishes is lots of layers applied real thin. I sanded to 1200, applied three lots of hard shellac and then 8 of Tru Oil. It came up really well. I used NGR. I cant see it being a problem on other rosewoods.
May I also recommend Neil's book http://www.ubeaut.com.au/book.html he really knows his stuff.
Sebastiaan
Like Kiwi I have gone to Zpoxy for pore filling and then a hand rubbed finish. I have used also Hard Shellac with good results. I used BLO as the lubricant for the rubber so maybe thats why its worked well for me.
My latest instrument was finished with Tru-Oil and i have to say Im delighted. I think the secret of hand applied finishes is lots of layers applied real thin. I sanded to 1200, applied three lots of hard shellac and then 8 of Tru Oil. It came up really well. I used NGR. I cant see it being a problem on other rosewoods.
May I also recommend Neil's book http://www.ubeaut.com.au/book.html he really knows his stuff.
Sebastiaan
make mine fifths........
I have french polished my first and pore filled with egg white and it worked real nice...I like to use egg because it is cheap and non toxic..I got hungry and ate some of the pore filler
Seriously I live in an apartment so the lack of fumes from the egg pore filler is great and the shellac is very mild smelling compared to most other finishes. Plus once finished it look glorious.

Ukuleles will take OVER!
I hate pore filling so much it influences my wood choices, but I’m using blackwood and silky oak on an all aust flamenco so have been playing around with a few different methods. What I was happiest with was a combination of pumice and egg white. The best and easiest result I got was to use egg white with 400 grit wet and dry with just a little dusting of very fine pumice. It filled much quicker with the pumice in the mix.
I like French polish (years of furniture restoration will do that) and hate the smell of epoxy. I had a try of the hard shellac and didn’t like it much, didn’t seem to attain the same depth and shine with the hand rubbing method. I’m also not sure if they have overcome the crazing problems they were having with it (anyone have any feedback on this?).
About the only thing I do differently than the tutorials I’ve read is that I use up to 10% gum rosin (gum sandarac) in the shellac. Doing this makes the finish harder and a little more scratch resistant without compromising the finish. I use buttonlac where I don’t mind adding colour to the timber, it isn’t so orange as the basic orange shellac and it is a much harder finish. Best place I’ve found to get gum rosin (and a bunch of other timber finishing supplies) is goods and chattels in Brisbane ($11.45 a kg plus postage).
Cheers
James
I like French polish (years of furniture restoration will do that) and hate the smell of epoxy. I had a try of the hard shellac and didn’t like it much, didn’t seem to attain the same depth and shine with the hand rubbing method. I’m also not sure if they have overcome the crazing problems they were having with it (anyone have any feedback on this?).
About the only thing I do differently than the tutorials I’ve read is that I use up to 10% gum rosin (gum sandarac) in the shellac. Doing this makes the finish harder and a little more scratch resistant without compromising the finish. I use buttonlac where I don’t mind adding colour to the timber, it isn’t so orange as the basic orange shellac and it is a much harder finish. Best place I’ve found to get gum rosin (and a bunch of other timber finishing supplies) is goods and chattels in Brisbane ($11.45 a kg plus postage).
Cheers
James
Thanks guys,
Martin and Sebastiaan Did you guys seal the soundboard with z-poxy also?
and
Sebastiaan, with your tru-oil finish...did you use it on the soundboard? and did you go for a gloss finish ? If I can get a gloss finish with tru-oil i may be tempted to use it.
James..thanks for the info..I haven't found much info on applying hard shellac by hand but the best finish photos I've seen have been when people spray it ...which i think Bob from memory has done and they look great.
What colour shellac would give a cedar faced guitar a vintage look? or what brings out the best depth in rosewood also?
Cheers Grant
Martin and Sebastiaan Did you guys seal the soundboard with z-poxy also?
and
Sebastiaan, with your tru-oil finish...did you use it on the soundboard? and did you go for a gloss finish ? If I can get a gloss finish with tru-oil i may be tempted to use it.
James..thanks for the info..I haven't found much info on applying hard shellac by hand but the best finish photos I've seen have been when people spray it ...which i think Bob from memory has done and they look great.
What colour shellac would give a cedar faced guitar a vintage look? or what brings out the best depth in rosewood also?
Cheers Grant
I think Bob was talking with neil from Ubeaut on this issue at one stage. I believe Neil rejigged the formula for the hard shellac but I havent heard any feedback on results of same.James Mc wrote: I had a try of the hard shellac and didn’t like it much, didn’t seem to attain the same depth and shine with the hand rubbing method. I’m also not sure if they have overcome the crazing problems they were having with it (anyone have any feedback on this?).
Cheers
James
I had alot of problems french polishing IRW with Hard Shellac on my last classical and havent used the stuff since.
Cheers Martin
- Bob Connor
- Admin
- Posts: 3115
- Joined: Mon Jul 09, 2007 9:43 pm
- Location: Geelong, Australia
- Contact:
I did talk to Neil and he did change the formula but I haven't been game to try it since. We've shifted to Mirotone pre-cataysed laquer and are just about to try the Mirotone Polyurethane. Both of which I know have been tested on instruments.
I did see on the Ubeaut forums that Neil thought it may be either the Maguiers or Menzerna that we buff with causing the crazing. It's possible I guess but it doesn't seem to have an effect on any other finishes.
I did see on the Ubeaut forums that Neil thought it may be either the Maguiers or Menzerna that we buff with causing the crazing. It's possible I guess but it doesn't seem to have an effect on any other finishes.
I didnt use any polishing agents on my classical....the shellac started crazing during bodying sessions. I replaced the back on the instrument and started from scratch and got the same result.bob wrote:I did talk to Neil and he did change the formula but I haven't been game to try it since. We've shifted to Mirotone pre-cataysed laquer and are just about to try the Mirotone Polyurethane. Both of which I know have been tested on instruments.
I did see on the Ubeaut forums that Neil thought it may be either the Maguiers or Menzerna that we buff with causing the crazing. It's possible I guess but it doesn't seem to have an effect on any other finishes.
- ozziebluesman
- Blackwood
- Posts: 1554
- Joined: Wed Oct 10, 2007 9:12 am
- Location: Townsville
- Contact:
G'day Grant,
Mate, I'm a beginner builder but thought I would share my hand finish experiences with you. Like you I prefer a hand finish!
On my two weissenborn copies I used Ubeaut Hard Shellac (new formula). I sealed the guitars with 3 coats of one part Ubeaut, 8 parts metholated spirits. I didn't pore fill the sassafrass and was quite happy that the blackwood didn't require filling. Time will tell if the finish sinks into the pores. That dosen't overly worry me. I then applied six coats, one each day with a rubber of a 2 pound cut with Ubeat. Then the last coat was straight from the bottle. I then finished off by hand with some Renaissence Wax. I used Beez Wax on my Concert Uke and thought that was a good finish too. Actually I prefer the Beez Wax.
Cheers
Alan
ps I let the sassafrass weiss dry for three weeks. The blackwood dried for four weeks and I think that the extra week of drying make a difference to end result. Depends on humidity levels I think!
Mate, I'm a beginner builder but thought I would share my hand finish experiences with you. Like you I prefer a hand finish!
On my two weissenborn copies I used Ubeaut Hard Shellac (new formula). I sealed the guitars with 3 coats of one part Ubeaut, 8 parts metholated spirits. I didn't pore fill the sassafrass and was quite happy that the blackwood didn't require filling. Time will tell if the finish sinks into the pores. That dosen't overly worry me. I then applied six coats, one each day with a rubber of a 2 pound cut with Ubeat. Then the last coat was straight from the bottle. I then finished off by hand with some Renaissence Wax. I used Beez Wax on my Concert Uke and thought that was a good finish too. Actually I prefer the Beez Wax.
Cheers
Alan
ps I let the sassafrass weiss dry for three weeks. The blackwood dried for four weeks and I think that the extra week of drying make a difference to end result. Depends on humidity levels I think!
- sebastiaan56
- Blackwood
- Posts: 1274
- Joined: Sun Oct 28, 2007 5:23 am
- Location: Blue Mountains
hi Grant,
I used Tru-Oil for the soundboard, works a treat. IMHO the big advantage of Tru-Oil over hard shellac is that you can get thicker coats on with Tru-Oil. The disadvantage is that there is a four hour minimum between coats. As the coats got thicker I left it overnight. It took about a week for the smell to fade. Hard shellac takes time to hardern, 3 weeks, but being ethanol based you can get a lot of coats on. It also swooges really well with BLO, but then Tru-Oil tends to lay flatter as it dries. Both are the same to use but my next instrument will be done in Tru-Oil.
Sebastiaan
I used Tru-Oil for the soundboard, works a treat. IMHO the big advantage of Tru-Oil over hard shellac is that you can get thicker coats on with Tru-Oil. The disadvantage is that there is a four hour minimum between coats. As the coats got thicker I left it overnight. It took about a week for the smell to fade. Hard shellac takes time to hardern, 3 weeks, but being ethanol based you can get a lot of coats on. It also swooges really well with BLO, but then Tru-Oil tends to lay flatter as it dries. Both are the same to use but my next instrument will be done in Tru-Oil.
Sebastiaan
make mine fifths........
- sebastiaan56
- Blackwood
- Posts: 1274
- Joined: Sun Oct 28, 2007 5:23 am
- Location: Blue Mountains
ozziebluesman, thanks for sharing that.. I'll definitely look into the hard shellac more.
Sebastiaan, the simplest finish that also looks/ sounds good really appeals to me. tru-oil could be the answer...Is your finish gloss?
I was also just checking out the ubeaut website and was wondering
what the difference in products like
shellac flakes
white shellac
french polish
?
are they all applied in a similar fashion i.e. french polishing
Cheers Grant
Sebastiaan, the simplest finish that also looks/ sounds good really appeals to me. tru-oil could be the answer...Is your finish gloss?
I was also just checking out the ubeaut website and was wondering
what the difference in products like
shellac flakes
white shellac
french polish
?
are they all applied in a similar fashion i.e. french polishing
Cheers Grant
- sebastiaan56
- Blackwood
- Posts: 1274
- Joined: Sun Oct 28, 2007 5:23 am
- Location: Blue Mountains
Hi Grant,
The Ubeaut liquid products are shellac dissolved in ethanol, all except the Hard Shellac which is Shellac with a polymer that cross links over time. Apparently it is a monomer similar to Melamine.
If you buy flakes you will need to dissolve them in Industrial metho (ie >99% ethanol). The big advantage of flakes is the shelf life, almost indefinite in good conditions. The liquids however are only good for about 18 months. So it depends on how long you want to hold stocks for.
There are a number of different types of Shellac flakes around, Orange, Dewaxed, Ruby, Blonde, White etc. The colours are derived when the shellac is being purified. Google shellac processing and you will find heaps of interesting stuff out there.
Tru-Oil finishes to a gloss,
Sebastiaan
The Ubeaut liquid products are shellac dissolved in ethanol, all except the Hard Shellac which is Shellac with a polymer that cross links over time. Apparently it is a monomer similar to Melamine.
If you buy flakes you will need to dissolve them in Industrial metho (ie >99% ethanol). The big advantage of flakes is the shelf life, almost indefinite in good conditions. The liquids however are only good for about 18 months. So it depends on how long you want to hold stocks for.
There are a number of different types of Shellac flakes around, Orange, Dewaxed, Ruby, Blonde, White etc. The colours are derived when the shellac is being purified. Google shellac processing and you will find heaps of interesting stuff out there.
Tru-Oil finishes to a gloss,
Sebastiaan
make mine fifths........
Grant,gratay wrote:
I was also just checking out the ubeaut website and was wondering
what the difference in products like
shellac flakes
white shellac
french polish
Cheers Grant
French Polishing is not a product....it's one of many ways of applying shellac. In a nutshell it involves applying hundreds of layers of thin layers of shellac using a pad usually lubricated with an oil of some sort.
Shellac flakes are just that...flakes of shellac. The flakes are dissolved in alcohol (IMS meths) before application. The ratio of flakes to meths is referred to as the "cut". Eg a 4lb cut is 4lbs of shellac flakes to 1 gallon of alcohol. I generally use a 2lb cut for bodying sessions and cut back to a 1lb cut for the glaze coats when french polishing my instruments.
White Shellac is dewaxed shellac. If you add raw shellac flakes to alcohol and let it sit for a few days you'll see the wax and other solids settle out.
Martin,kiwigeo wrote:Grant,gratay wrote:
I was also just checking out the ubeaut website and was wondering
what the difference in products like
shellac flakes
white shellac
french polish
Cheers Grant
French Polishing is not a product....it's one of many ways of applying shellac. In a nutshell it involves applying hundreds of layers of thin layers of shellac using a pad usually lubricated with an oil of some sort.
Shellac flakes are just that...flakes of shellac. The flakes are dissolved in alcohol (IMS meths) before application. The ratio of flakes to meths is referred to as the "cut". Eg a 4lb cut is 4lbs of shellac flakes to 1 gallon of alcohol. I generally use a 2lb cut for bodying sessions and cut back to a 1lb cut for the glaze coats when french polishing my instruments.
White Shellac is dewaxed shellac. If you add raw shellac flakes to alcohol and let it sit for a few days you'll see the wax and other solids settle out.
Ubeaut have a product in their catalogue called 'French Polish'
scroll down this page
http://www.ubeaut.com.au/flakes.html#fp1
I was just wondering what the difference is between the liquid forms might be?..
mainly what they sell as white shellac and this 'french polish' product as they call it. Its all a bit confusion.
Sebastiaan, thanks ...even though its probably not a big deal disolving the flakes , the white shellac product sounds like it may be a good way to go to if its pre-mixed ?
Here are some pics and a bit of basic info on the kinds of shellac that are commonly available. I've tried to explain the differences between them as best as I could from my personal experience, so is subjective rather than scientific.
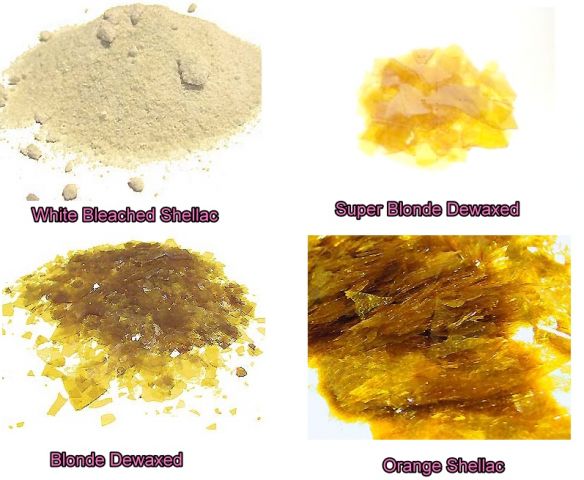
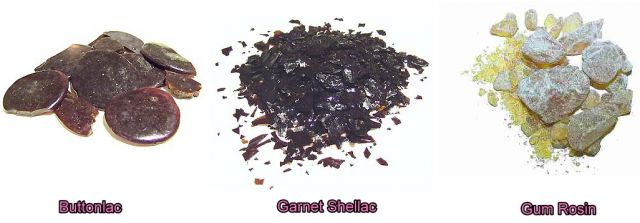
White shellac has been chemically bleached then dried and ground. It is almost totally clear when applied, you use it just like shellac flakes. It is sometimes used as a base for pre mixed white polish or coloured shellac.
Dewaxed Super Blonde flakes are the most processed form of natural shellac and give an almost clear finish with just a little yellow tint. It has a higher resin content that blonde shellac so you use less in your standard mix (a 2 pound mix using blonde flakes is about the same as a 1.75 mix using super blonde flakes). I don’t know if it is just me but super blonde seems a have a harder finish than normal blonde shellac but seems a little harder to apply.
Dewaxed Blonde flakes give a little more tint than super blonde and would be the most commonly used for a clear finish.
Lemon Shellac is a less processed form of blonde shellac and gives a yellow/brown tint to pale timbers.
Orange shellac flakes are available as both standard and dewaxed, and is the most common and cheapest of the shellacs. It is what most antique furniture was originally finished with. Gives an orange amber finish on pale timbers (which I don’t like much) and adds warmth to darker timbers.
Buttonlac is shellac that has been heat-treated which polymerizes the shellac making it much harder. The tint it gives timber is more brown than the amber/orange you get with orange shellac. Buttonlac is also very good as a pore filler for darker timbers and as a general purpose varnish for brushing or spraying (I consider it to be one of the most underrated and under utilised products in woodworking).
Garnet Shellac is the darkest natural shellac and gives nice rich brown finish, great if you want a vintage look. My experience has been that using up to 15% gum rosin in the garnet shellac mix gives it much more luster and depth when applied using French polishing methods.
Black Polish is often made by adding a black stain to blonde or white shellac (possibly spirit soluble nigrosine, it could also have a hardener added). You use it just like shellac but it is for ebonising and totally obscures the grain. I’ve never used it myself but I saw a cheap pine coffee table that a friend French polished using Liberon black polish. Looked fantastic but I suspect it would show every scratch (but I could be wrong).
Gum rosin and Sandarac (often the same thing sold under different names). This is made from solids produced from the distillation of pine sap (usually white pine) from living trees, (not the same as wood rosin that comes from dead wood). Sandarac was a common ingredient in traditional varnish mixes, it is almost clear and adds hardness to shellac finishes. I dissolve it as a 2 pound mix in metho then let it settle before adding a 5 to 10% mix to shellac (removes the chance of adding any impurities to the shellac).
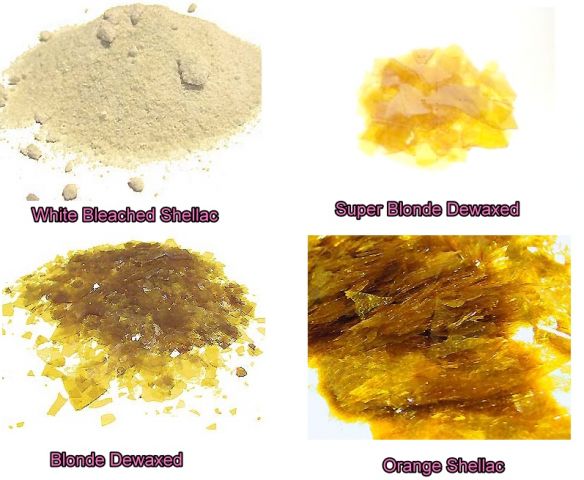
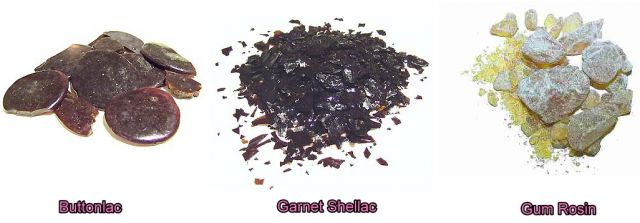
White shellac has been chemically bleached then dried and ground. It is almost totally clear when applied, you use it just like shellac flakes. It is sometimes used as a base for pre mixed white polish or coloured shellac.
Dewaxed Super Blonde flakes are the most processed form of natural shellac and give an almost clear finish with just a little yellow tint. It has a higher resin content that blonde shellac so you use less in your standard mix (a 2 pound mix using blonde flakes is about the same as a 1.75 mix using super blonde flakes). I don’t know if it is just me but super blonde seems a have a harder finish than normal blonde shellac but seems a little harder to apply.
Dewaxed Blonde flakes give a little more tint than super blonde and would be the most commonly used for a clear finish.
Lemon Shellac is a less processed form of blonde shellac and gives a yellow/brown tint to pale timbers.
Orange shellac flakes are available as both standard and dewaxed, and is the most common and cheapest of the shellacs. It is what most antique furniture was originally finished with. Gives an orange amber finish on pale timbers (which I don’t like much) and adds warmth to darker timbers.
Buttonlac is shellac that has been heat-treated which polymerizes the shellac making it much harder. The tint it gives timber is more brown than the amber/orange you get with orange shellac. Buttonlac is also very good as a pore filler for darker timbers and as a general purpose varnish for brushing or spraying (I consider it to be one of the most underrated and under utilised products in woodworking).
Garnet Shellac is the darkest natural shellac and gives nice rich brown finish, great if you want a vintage look. My experience has been that using up to 15% gum rosin in the garnet shellac mix gives it much more luster and depth when applied using French polishing methods.
Black Polish is often made by adding a black stain to blonde or white shellac (possibly spirit soluble nigrosine, it could also have a hardener added). You use it just like shellac but it is for ebonising and totally obscures the grain. I’ve never used it myself but I saw a cheap pine coffee table that a friend French polished using Liberon black polish. Looked fantastic but I suspect it would show every scratch (but I could be wrong).
Gum rosin and Sandarac (often the same thing sold under different names). This is made from solids produced from the distillation of pine sap (usually white pine) from living trees, (not the same as wood rosin that comes from dead wood). Sandarac was a common ingredient in traditional varnish mixes, it is almost clear and adds hardness to shellac finishes. I dissolve it as a 2 pound mix in metho then let it settle before adding a 5 to 10% mix to shellac (removes the chance of adding any impurities to the shellac).
Grant,gratay wrote: Martin,
Ubeaut have a product in their catalogue called 'French Polish'
scroll down this page
http://www.ubeaut.com.au/flakes.html#fp1
I was just wondering what the difference is between the liquid forms might be?..
mainly what they sell as white shellac and this 'french polish' product as they call it. Its all a bit confusion.
Sebastiaan, thanks ...even though its probably not a big deal disolving the flakes , the white shellac product sounds like it may be a good way to go to if its pre-mixed ?
As far as I can ascertain Neil's 'French Polish" is shellac flakes dissolved in alcohol. Not sure what the cut would be....probably about a 4lb cut but don't quote me on that.
Making up your own shellac solution is no big deal....just follow the instructions in the Milburn tutorial. I generally make up my shellac at 2lb cut and use that for body sessions. I then cut it back to a 1lb cut for the final glaze coats. I use a blonde shellac which I buy from a supplier here in Adelaide. The flakes supplied by Ubeaut will darken lighter wood like spruce. If youre after an aged look for your top then the Ubeaut flakes might be ok.
The bottom line..premixed shellac will have a shorter shelf life than dry flakes. Also note that myself and a few other people prefer a bit of wax in the shellac so for that reason prefer to make up our own shellac.
I tried the white polish from bunnies (just needed to know). It smells great like lemon pie. It covers well rubbed on as a couple of coats but when I tried building it up as you would with shellac it went blotchy on me, most likely due to the amount of wax it seems to have in it. I did do a good job of restoring the shine on an old scratched up french polished picture frame.
One thing I would recommend if you use the tru-oil is their sealer and filler product especially if you are using it on a light colured wood like a spruce soundboard or on endgrain like a neckblock. without it the tru-oil may absorb unevenly in the endgrain and come out blotchy and dark (sanded off my neckblock and started again with the sealer)
Also stopped the tru-oil penetrating too far into the spruce and allowed me to scrape a bridge gluing area easily
Also stopped the tru-oil penetrating too far into the spruce and allowed me to scrape a bridge gluing area easily
- sebastiaan56
- Blackwood
- Posts: 1274
- Joined: Sun Oct 28, 2007 5:23 am
- Location: Blue Mountains
Would silica powder mixed in with the egg white do the same job? I mention that only because I don't have any pumice, but I do have silica powder. Will try it out on an offcut.James Mc wrote: What I was happiest with was a combination of pumice and egg white. The best and easiest result I got was to use egg white with 400 grit wet and dry with just a little dusting of very fine pumice. It filled much quicker with the pumice in the mix.
This topic has been very helpful to me. finishing is not my strong point.
Who is online
Users browsing this forum: No registered users and 72 guests