Is that all? I spend 90 minutes on average each way to work every day (Como West to Macquarie Uni for you Sydney siders). I used to be able to do it in 50 minutes on the bike, but that was the fastest time ever and I had to ride like a mad bastard on a race track. The last trip on the bike took an extra couple weeks in a pit stop at the hospital, and now the bike is a hunk of twisted metal (recycled into fry pans by now I guess). So the buses and trains will do me fine, and I won't complain, much. I'm a good rider but boy it hurts when some idiot taxi driver knocks you over at 80-90km/hr (again!). Bugger that for a lark, I'll buy a book and catch the bus, and try not to whine about it.matthew wrote:I drive 40 minutes across Sydney every day to get to work. I figure that's a day's work a week in the car. But no choice for me. If I didn't travel to that work, I wouldn't be able to afford to build basses for a HOBBY!
What have you got done this weekend?
And while I try to stop whining about it, I'll post a couple pix of my latest - #5.
An OLF SJ, b&s blistered Sapele from Don Williams when he was New England Tonewoods (matching boards to the stuff you got of Don, Heshtone).
The top is Lutz from Mario via Barry at Woodtone Guitars.
The linings and neck block are New Guinea Rosewood (Narra) 'cause I had some and I want to hear what happens when you use woods with a high 'Q' value instead of woods that tend to dampen tone. This stuff really rings...
The tail block is Fijian plantation mahogany plywood, which looks really crap with that void in it, but it'll do the job.
Back braces are Adi.
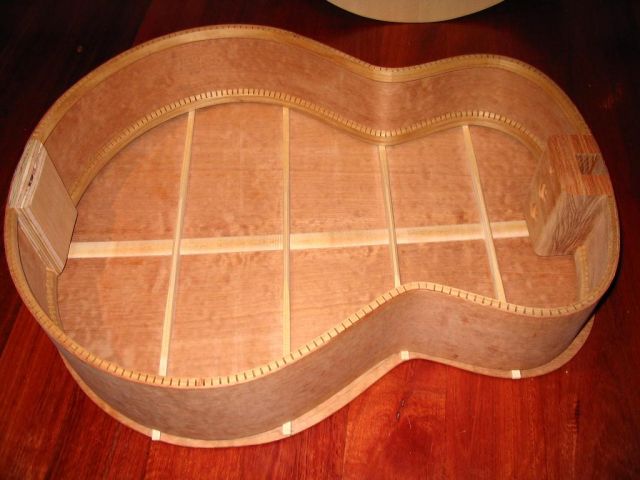
Rims sitting on the braced back.
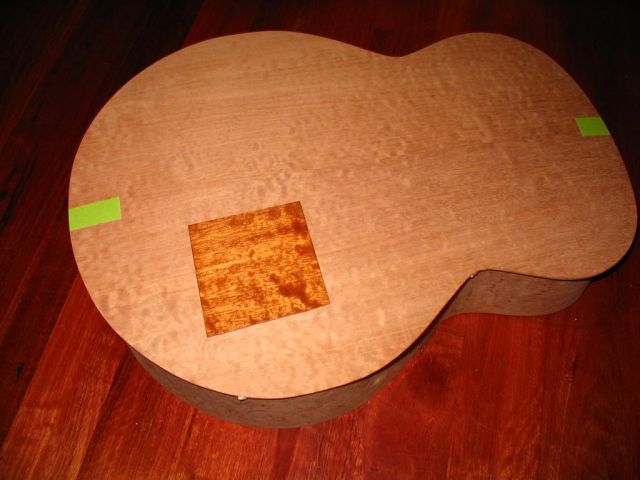
Blistered Sapele, the little square is an off-cut from the sides that I threw a bit of shellac on to see what I'd see.
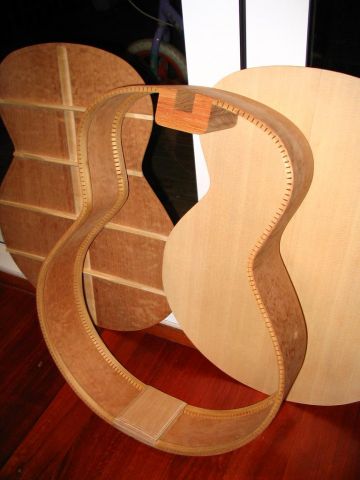
All the bits and pieces.
Oh, and this is the first guitar that I've used hot hide glue on. Man, I don't know what I was stressing about - I love this stuff!
Cheers,
Paul
An OLF SJ, b&s blistered Sapele from Don Williams when he was New England Tonewoods (matching boards to the stuff you got of Don, Heshtone).
The top is Lutz from Mario via Barry at Woodtone Guitars.
The linings and neck block are New Guinea Rosewood (Narra) 'cause I had some and I want to hear what happens when you use woods with a high 'Q' value instead of woods that tend to dampen tone. This stuff really rings...
The tail block is Fijian plantation mahogany plywood, which looks really crap with that void in it, but it'll do the job.
Back braces are Adi.
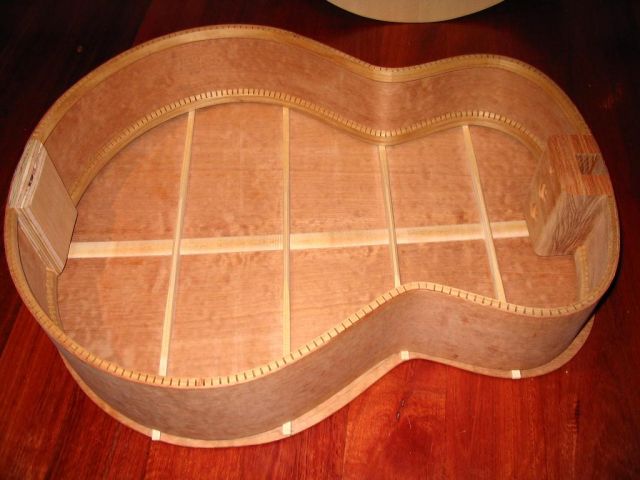
Rims sitting on the braced back.
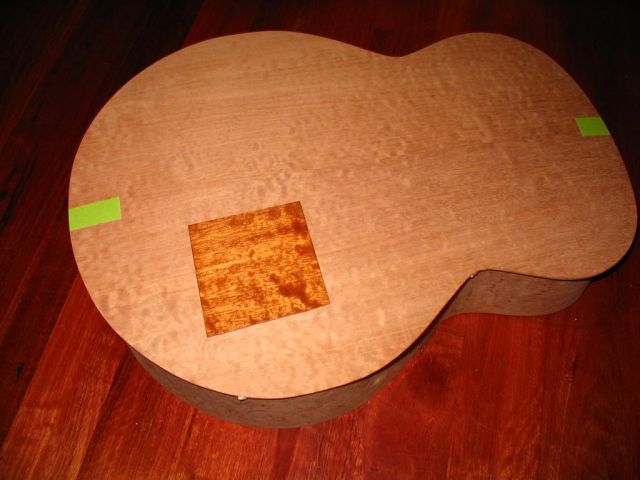
Blistered Sapele, the little square is an off-cut from the sides that I threw a bit of shellac on to see what I'd see.
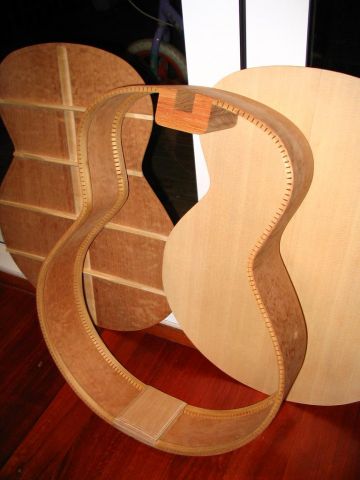
All the bits and pieces.
Oh, and this is the first guitar that I've used hot hide glue on. Man, I don't know what I was stressing about - I love this stuff!
Cheers,
Paul
Last edited by Paul B on Mon Aug 11, 2008 8:51 pm, edited 1 time in total.
Hi John,
Looks like youre making some progress there.
Just one thing....I may be seeing things but that scarf joint on that neck doesnt look quite right. On my scarf jointed headstocks the cut is angled the opposite way to what youve done..... ie the joint appears on the headstock and is covered by the headstock veneer.
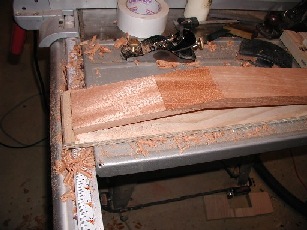
What do the rest of you guys think?
Cheers Martin
Looks like youre making some progress there.
Just one thing....I may be seeing things but that scarf joint on that neck doesnt look quite right. On my scarf jointed headstocks the cut is angled the opposite way to what youve done..... ie the joint appears on the headstock and is covered by the headstock veneer.
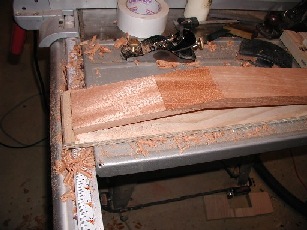
What do the rest of you guys think?
Cheers Martin
Hesh, thank you for the well wishes. I do appreciate them. My apologies for missing your comment the first time.
John, the first neck I put together as a practice exercise I did the same thing you did. I can't remember if I read it in Campiano's book or if it was pointed out to me by someone at MIMF, but gluing it up this way could lead to a possible hump under the fretboard that could react to humidity changes. Maybe and possible. If you can get the joint apart with heat, I'd flip it and reglue it. I was going to be using mine for kindling any way so I wasn't worried about it.
Your 5th is looking great Paul. That Sapele is gorgeous. I really like it.
Unfortunate for me, but I have you all trumped for commute time. Since driving is too costly these days, I take buses. I leave at 5 am and get into Seattle, stand around for about 10 minutes than catch another one into Everett. An hour and 45 later, barring any traffic issues, I'm at work. Getting home takes between 2 and a half to 3 hours, depending on if I'm lucky enough to make it into Seattle in time to catch the last express home. If not, I stand around and take the milk run bus home. So I average 4 and a half hours a day commuting. Get home, eat go to bed and get up 6 hours later to do it again. Dr said change jobs or move now. I can't find another position like this one, especially with the economy the way it is, so we are moving.
John, the first neck I put together as a practice exercise I did the same thing you did. I can't remember if I read it in Campiano's book or if it was pointed out to me by someone at MIMF, but gluing it up this way could lead to a possible hump under the fretboard that could react to humidity changes. Maybe and possible. If you can get the joint apart with heat, I'd flip it and reglue it. I was going to be using mine for kindling any way so I wasn't worried about it.
Your 5th is looking great Paul. That Sapele is gorgeous. I really like it.
Unfortunate for me, but I have you all trumped for commute time. Since driving is too costly these days, I take buses. I leave at 5 am and get into Seattle, stand around for about 10 minutes than catch another one into Everett. An hour and 45 later, barring any traffic issues, I'm at work. Getting home takes between 2 and a half to 3 hours, depending on if I'm lucky enough to make it into Seattle in time to catch the last express home. If not, I stand around and take the milk run bus home. So I average 4 and a half hours a day commuting. Get home, eat go to bed and get up 6 hours later to do it again. Dr said change jobs or move now. I can't find another position like this one, especially with the economy the way it is, so we are moving.
Not quite all of us Lillian. Heres how I get to work:Lillian wrote:
Unfortunate for me, but I have you all trumped for commute time.
Day one: fly Adelaide to Perth - 3 1/2 hours
Overnight Perth in crap hotel on Great Eastern Highway
Day two: 5am check in for a 2 1/2 hour flight from Perth to Broome.
Straight from the plane onto a Sikorsky S-92 helicopter for a 3 hour flight from Broome to the rig including a 1/2 hour stop at Lombadina to pick up fuel.
- Dennis Leahy
- Blackwood
- Posts: 872
- Joined: Wed Oct 10, 2007 12:32 am
- Location: Duluth, MN, US
- Contact:
Martin, I hope they pay you for travel time, and then pay you REALLY well for your time on that rig!
Lillian, I know that no one is paying your commute time, so I applaud your move. Moving is hell, but hopefully this move will have a huge payoff: TIME! (more valuable than money, sometimes)
Dennis
p.s. What I have done in lutherie lately: bupkis, nada, zero, zilch. Depressing! I might finally have a real shop area in late fall or early winter (er, for you Southern Hemispherians, that would be end of October to beginning of December - definitely not the beginning of your winter.)
Lillian, I know that no one is paying your commute time, so I applaud your move. Moving is hell, but hopefully this move will have a huge payoff: TIME! (more valuable than money, sometimes)
Dennis
p.s. What I have done in lutherie lately: bupkis, nada, zero, zilch. Depressing! I might finally have a real shop area in late fall or early winter (er, for you Southern Hemispherians, that would be end of October to beginning of December - definitely not the beginning of your winter.)
Another damn Yank!
Yes guys didn't know at the time I'd made the mistake with the neck, but it's gonna stay that way now as it works and I haven't the length to undo it and swap it round. Should of added a big thanks to Joel Thompson who helped me voice the bracing.
Just another mistake to remember not to do in number 2!
Cheers
John
Just another mistake to remember not to do in number 2!
Cheers
John
Hey Paul, I've got a couple of those sets but for a Size 5 Parlor. The "Brain Sapele" was from Don as well. Beautiful stuff to work with.
This last weekend, and well, several of the previous weekends have been pretty hectic. Fund raising for clubs, helping M8's move.... very little time for the things I prefer to do. I did manage to get the last of the finish applied to the 0M cutaway, so it'll get buffed out later in the week and assembled. Managed to get a neck blank laminated up as well for the current project. Not much to see in the way of pictures.
I also did a complete rebuild on my website, which for any of you that have done that will realize is a heap of work that you don't want to have to do all that often.
This last weekend, and well, several of the previous weekends have been pretty hectic. Fund raising for clubs, helping M8's move.... very little time for the things I prefer to do. I did manage to get the last of the finish applied to the 0M cutaway, so it'll get buffed out later in the week and assembled. Managed to get a neck blank laminated up as well for the current project. Not much to see in the way of pictures.
I also did a complete rebuild on my website, which for any of you that have done that will realize is a heap of work that you don't want to have to do all that often.
Hi John, go and look at any Ibanez electric (and probably many brand name acoustics as well), they all have the neck like you have done.
I am sure Martin won't mind me saying that you have not made a mistake as such, you have just done it differently.
One reason i have heard not to do it like you have done is that over time (a long time) the joint can creep and put a slight hump under the fingerboard and this effects playability. But if its good enough for Ibanez why should you worry.
Onward.
Dom
I am sure Martin won't mind me saying that you have not made a mistake as such, you have just done it differently.
One reason i have heard not to do it like you have done is that over time (a long time) the joint can creep and put a slight hump under the fingerboard and this effects playability. But if its good enough for Ibanez why should you worry.
Onward.
Dom
You can bomb the world to pieces,
but you can't bomb the world to peace!
but you can't bomb the world to peace!
Dom,
There are also asthetic reasons why I do my scarf joint differently from the way John's done his. IMO it looks neater having the joint visible over the nut/headstock section of the neck rather than further down the neck. On a classical the side plate on the tuners neatly cover the splice and its not really noticeable at all.
As for Ibanez guitars...I tend to aspire to make something a little better when I make my instruments. The Ibanez's I see in the shops of late arent that great and theyre factory built which means time spent making sure that joints look tidy gets sacrificed for speed of construction.
Cheers Martin
There are also asthetic reasons why I do my scarf joint differently from the way John's done his. IMO it looks neater having the joint visible over the nut/headstock section of the neck rather than further down the neck. On a classical the side plate on the tuners neatly cover the splice and its not really noticeable at all.
As for Ibanez guitars...I tend to aspire to make something a little better when I make my instruments. The Ibanez's I see in the shops of late arent that great and theyre factory built which means time spent making sure that joints look tidy gets sacrificed for speed of construction.
Cheers Martin
- Taffy Evans
- Blackwood
- Posts: 1077
- Joined: Wed Apr 30, 2008 6:54 pm
- Location: Charters Towers North Queensland
- cactus bum
- Myrtle
- Posts: 72
- Joined: Tue Jun 10, 2008 3:19 am
- Location: Arizona
I am new to this lutherie game, but have been woodworking and making fine furniture as a hobbyist for a long time. I have plans to build two guitars, both with the same outside dimensions. The first will follow plans for a size 5 Martin. I plan on building a guitar pretty true to these plans.
However, the secong guitar will have several different specifications. I hope to do a variation of the small Brunner outdoor guitar with a detachable neck and less bracing than the traditional size 5. You can see the Brunner at www.brunner-guitars.com. When at their website go to "shop" for a good look at the design of this innovative guitar. The photos below are from more than one weekend of work. I hope to use some Alligator Juniper I resawed from a tree I cut down several years ago for the top of the Brunner type guitar. The Alligator seems very much like Western Red Cedar, but nobody I have talked with has used this wood. The photos below are from more than one weekend of work.
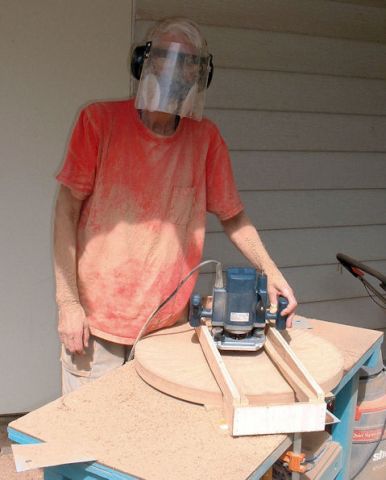
Allen warned me about the great amount of dust created in making the radius dishes. Guess what? He was spot on.
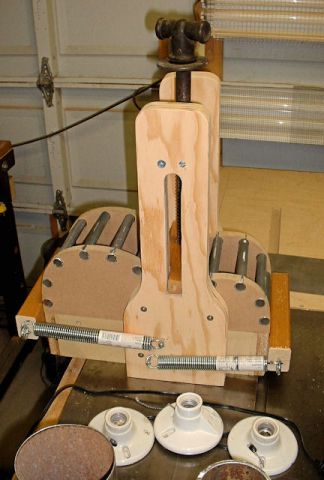
This bender is the size of a size 5 Martin. I may use lightbulbs or I may buy a silicone blanket. As yet to be determined.
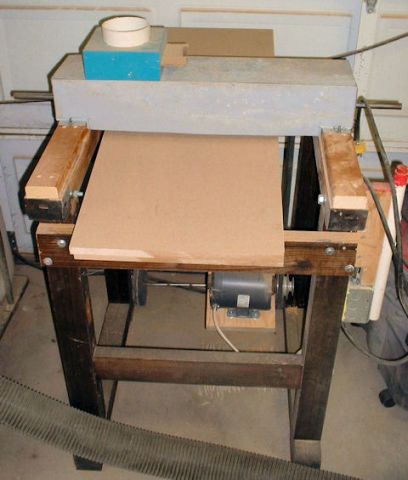
My drum sander was made mostly from material I had laying around the shop. The washing machine motor will probably need to be replaced after it boggs down enough times to motivate me to buy a different motor. The stand was an old workbench from my father's shop that was collecting dust and wasting space where it was.

This guitar mold speaks for itself.
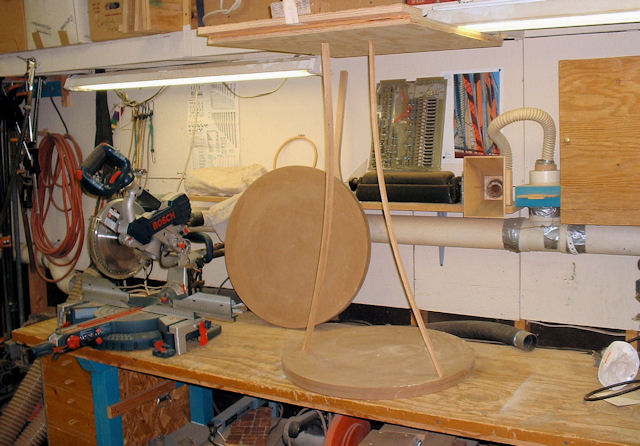
I extended the bottom of the shelf, and it is now the top of the go-bar deck. I will cut my go-bars out of scrap. I love low tech solutions to age old problems. Any feedback is appreciated. Thanks for looking, Michael Pollard
However, the secong guitar will have several different specifications. I hope to do a variation of the small Brunner outdoor guitar with a detachable neck and less bracing than the traditional size 5. You can see the Brunner at www.brunner-guitars.com. When at their website go to "shop" for a good look at the design of this innovative guitar. The photos below are from more than one weekend of work. I hope to use some Alligator Juniper I resawed from a tree I cut down several years ago for the top of the Brunner type guitar. The Alligator seems very much like Western Red Cedar, but nobody I have talked with has used this wood. The photos below are from more than one weekend of work.
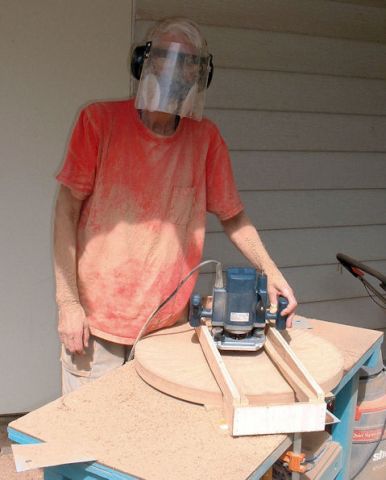
Allen warned me about the great amount of dust created in making the radius dishes. Guess what? He was spot on.
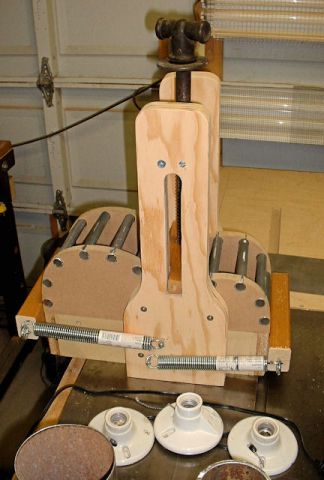
This bender is the size of a size 5 Martin. I may use lightbulbs or I may buy a silicone blanket. As yet to be determined.
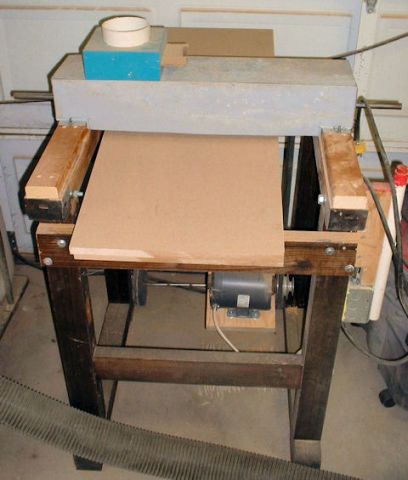
My drum sander was made mostly from material I had laying around the shop. The washing machine motor will probably need to be replaced after it boggs down enough times to motivate me to buy a different motor. The stand was an old workbench from my father's shop that was collecting dust and wasting space where it was.

This guitar mold speaks for itself.
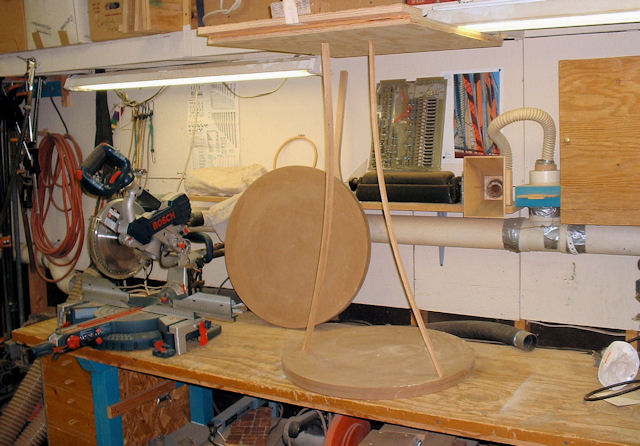
I extended the bottom of the shelf, and it is now the top of the go-bar deck. I will cut my go-bars out of scrap. I love low tech solutions to age old problems. Any feedback is appreciated. Thanks for looking, Michael Pollard
- cactus bum
- Myrtle
- Posts: 72
- Joined: Tue Jun 10, 2008 3:19 am
- Location: Arizona
Hey Allen, I told my wife you would be the first to respond. You must have a blackberry glued to your wrist or something. It looks like doing the prep for the lengthy India trip will take priority over beginning the guitar build. It will have to suffice for me to just get materials organized, mold etc. made, and wood prepared and stickered before blastoff. We go bye bye on Oct 8. But hey, it's the process that's supposed to be important, not the product. I will enjoy it just as much in March, when we return, as now.
By the way mate, congradulations on your new table saw. I think Jet is the most reliable of the "Asian" names. Enjoy every bit of sawdust you inhale. I love the smell of sawdust in the morning. Cheers, Michael
By the way mate, congradulations on your new table saw. I think Jet is the most reliable of the "Asian" names. Enjoy every bit of sawdust you inhale. I love the smell of sawdust in the morning. Cheers, Michael
What the heck is a Blackberry
That was what we got paid $1 a gallon bucket to pick when we were kids, so mom could make jam. No really Michael, I'm up at 5 am and have a cuppa and read the forum before I'm off to work.
So far the saw is just a dream. Sliced up some Kauri Pine for linings. Cut 1.5 mm strips 50 mm tall and off the blade they were ready to bend and laminate. Gotta go and glue the next set up.

So far the saw is just a dream. Sliced up some Kauri Pine for linings. Cut 1.5 mm strips 50 mm tall and off the blade they were ready to bend and laminate. Gotta go and glue the next set up.
Last edited by Allen on Mon Aug 25, 2008 5:18 pm, edited 1 time in total.
- Taffy Evans
- Blackwood
- Posts: 1077
- Joined: Wed Apr 30, 2008 6:54 pm
- Location: Charters Towers North Queensland
Who is online
Users browsing this forum: No registered users and 78 guests