Finishing Options
-
- Blackwood
- Posts: 115
- Joined: Tue Dec 09, 2008 1:15 pm
Finishing Options
I have a backlog of instruments waiting for a finish at present: two 000s, an OM, a 12-fret 00 as well as an F5 mandolin.
The reason for the backlog is that it's taken me forever to decide on my preferred finishing material going forward. I've been down the Tru-Oil path in the past and have achieved good results, but I've come to the conclusion that if I'm to sell my instruments, buyer expectations make it an unacceptable choice, regardless of what I might think about it. Any comments?
I have no desire to spray nitrocellulose again without adequate spraying and extraction facilities and, although I have an unopened can of KTM9 ready for use, the negative reports seem to outweigh the positive reports two to one; the consensus seems to be that it's just not hard enough or durable enough in the long term. I'm sure some of you will disagree, but that's the conclusion I've come to based on the opinions expressed on the various forums. I really wish one of the water-based finishes was the answer, but I don't believe they are - again based on other's opinions.
Anyway, after much deliberation, the current plan is to pore fill backs and sides with epoxy then spray several coats of a 2 pound cut of U-Beaut Hard Shellac. Tops will be french polished using the same product. I know some of you have had less-than-wonderful results with the Hard Shellac, but I'm hoping that with careful preparation and application it'll turn out OK. I look forward to reporting on the outcome in due course. Of course, if you think I'm headed for disaster, please let me know!
By the way, I noticed an interesting product on The Woodworks Book and Tool Company's web site (they're in Sydney) which they describe as follows:
This Hard Shellac additive preserves the food safe rating and delivers a finish which is comparable with synthetic modern day 2 pack catalysed finishes. It cross links over 20 or so days following application.
Hmmm... the blurb has a familiar ring to it, doesn't it? Sounds like it's sold in powder form - $15 for 150gm, which they say is enough for 500ml of shellac. Have any of you used it?
The reason for the backlog is that it's taken me forever to decide on my preferred finishing material going forward. I've been down the Tru-Oil path in the past and have achieved good results, but I've come to the conclusion that if I'm to sell my instruments, buyer expectations make it an unacceptable choice, regardless of what I might think about it. Any comments?
I have no desire to spray nitrocellulose again without adequate spraying and extraction facilities and, although I have an unopened can of KTM9 ready for use, the negative reports seem to outweigh the positive reports two to one; the consensus seems to be that it's just not hard enough or durable enough in the long term. I'm sure some of you will disagree, but that's the conclusion I've come to based on the opinions expressed on the various forums. I really wish one of the water-based finishes was the answer, but I don't believe they are - again based on other's opinions.
Anyway, after much deliberation, the current plan is to pore fill backs and sides with epoxy then spray several coats of a 2 pound cut of U-Beaut Hard Shellac. Tops will be french polished using the same product. I know some of you have had less-than-wonderful results with the Hard Shellac, but I'm hoping that with careful preparation and application it'll turn out OK. I look forward to reporting on the outcome in due course. Of course, if you think I'm headed for disaster, please let me know!
By the way, I noticed an interesting product on The Woodworks Book and Tool Company's web site (they're in Sydney) which they describe as follows:
This Hard Shellac additive preserves the food safe rating and delivers a finish which is comparable with synthetic modern day 2 pack catalysed finishes. It cross links over 20 or so days following application.
Hmmm... the blurb has a familiar ring to it, doesn't it? Sounds like it's sold in powder form - $15 for 150gm, which they say is enough for 500ml of shellac. Have any of you used it?
- John Maddison
- Blackwood
- Posts: 354
- Joined: Tue Jun 03, 2008 11:15 pm
- Location: Albany, Western Australia
- Contact:
Hi Pete,
Good post! ... welcome!
Each to their own I guess - but am glad I'm beyond breeding.
Recommend you read Kim's post on this forum about health risks of prolonged use of epoxy.
Cheers
Good post! ... welcome!
Tru-Oil as a petroleum distillate has it's place in the scheme of things, e.g. relative ease of application if you take adequate precautions, but as a first-time user have found it can be time-consuming to get 5 or 6 coats on, leave for a month to harden, then do the final cut & polish ... nice glossy finish, great sheen but it can be a bit 'delicate' to bumps & scratches, though relatively easy to repair. The label on my bottle made by Birchwwod-Casey says "This product contains a chemical known to the State of Califormia to cause cancer and birth defects or other reproductive harm."Pete Brown wrote: I've been down the Tru-Oil path in the past and have achieved good results, but I've come to the conclusion that if I'm to sell my instruments, buyer expectations make it an unacceptable choice, regardless of what I might think about it. Any comments?
Each to their own I guess - but am glad I'm beyond breeding.
Recommend you read Kim's post on this forum about health risks of prolonged use of epoxy.
Cheers
Last edited by John Maddison on Sun Jan 11, 2009 8:09 pm, edited 1 time in total.
John M
- hilo_kawika
- Blackwood
- Posts: 144
- Joined: Mon Oct 13, 2008 10:29 am
- Location: Hilo, Hawaii
- Contact:
I may have mentioned this earlier but the problem I had with French Polish is that a certain percentage of folks out there have perspiration which effectively removes the shellac over a few weeks time during the playing process.
Needless to say this put big holes in the limited lifetime warranty that I offered with my instruments...
aloha,
Dave Hurd
www.ukuleles.com
Needless to say this put big holes in the limited lifetime warranty that I offered with my instruments...

aloha,
Dave Hurd
www.ukuleles.com
How to become a millionaire? Start with $2 million and become a luthier...
Re: Finishing Options
Yes the blurb does sound familiar . I'd also be interested on how it performs , but after getting my fingers severely burnt with U-Beaut's hard shellac crazy cracking , guess who's NOT going to give it a try !Pete Brown wrote:
Anyway, after much deliberation, the current plan is to pore fill backs and sides with epoxy then spray several coats of a 2 pound cut of U-Beaut Hard Shellac. Tops will be french polished using the same product. I know some of you have had less-than-wonderful results with the Hard Shellac, but I'm hoping that with careful preparation and application it'll turn out OK. I look forward to reporting on the outcome in due course. Of course, if you think I'm headed for disaster, please let me know!
By the way, I noticed an interesting product on The Woodworks Book and Tool Company's web site (they're in Sydney) which they describe as follows:
This Hard Shellac additive preserves the food safe rating and delivers a finish which is comparable with synthetic modern day 2 pack catalysed finishes. It cross links over 20 or so days following application.
Hmmm... the blurb has a familiar ring to it, doesn't it? Sounds like it's sold in powder form - $15 for 150gm, which they say is enough for 500ml of shellac. Have any of you used it?

I wouldn't use their product again despite them coming out with a new formula which may , or maynot curb the crazy cracking ( see my post on the current 'SoundBoard Finishing " thread
In my opinion , french polished shellac is THE best finish . It inhibits the soundboards performance less than other finishes , and won't try to kill you !

I have been using Z-Poxy as a filler , but now have second thoughts about it after reading of Kim's experience. A slurry of wood dust rubbed in with shellac may be a whole lot safer
I have used Tru-oil also. Easy to apply and seems ideal . I have applied it to necks and despite what others have said about it's durability , it seems to hold up well I.M.O.
Unfortunatley it has a chemical in it known to cause Cancer ( warning is on the pack ) .As I now have Cancer , I'm inclined to stay well away from it from now on as you'd understand

Good old French polished Shellac is my answer . You can even eat the stuff . Is the least inhibiting finish tonally, and to me, is the sort of finish you'd expect on a hand crafted instrument of quality. Sprayed shellac tends to end up with a thicker finish I.M.O. and not as hard
Craig Lawrence
-
- Blackwood
- Posts: 115
- Joined: Tue Dec 09, 2008 1:15 pm
Thanks for the responses so far.
Dave, supposedly, the U-Beaut Hard Shellac contains a melamine co-polymer which cross-links over a few weeks and is impervious to alcohol and perspiration, the traditional enemies of a french polished shellac finish. If there's a question mark, it's therefore over how successfully it can be repaired in the future. I'm also aware that when a product sounds too good to be true, it often is!
I may have mentioned this earlier but the problem I had with French Polish is that a certain percentage of folks out there have perspiration which effectively removes the shellac over a few weeks time during the playing process.
Dave, supposedly, the U-Beaut Hard Shellac contains a melamine co-polymer which cross-links over a few weeks and is impervious to alcohol and perspiration, the traditional enemies of a french polished shellac finish. If there's a question mark, it's therefore over how successfully it can be repaired in the future. I'm also aware that when a product sounds too good to be true, it often is!
Craig, I've seen some really impressive results on this forum, and I also remember someone reporting crazing problems after spraying two full strength coats 15 minutes apart, an approach which would seem to be inviting trouble. How did you use the U-Beaut, and was the problem immediately apparent or did it appear some time afterwards?after getting my fingers severely burnt with U-Beaut's hard shellac crazy cracking , guess who's NOT going to give it a try !
Pete ,
I agree that a sprayed on finish invites more possibility of crazy cracking , and is in fact how I applied it . Others however, have laid the U-Beaut Hard shellac on french polish fashion and still got crazy cracking. I think Martin was one of these. The cracking doesn't take too long to appear ( a few weeks )
Just a bad untested product . Stay well away !
I maintain a french polished ( unhardened) shellac finish is the way to go .The least inhibiting finish tonally and the sort of finish you'd expect on a hand built instrument of quality . A good wax over the finish will help protect the shellac until it hardens up further over time. Given enough time , a shellac finish is VERY durable
I agree that a sprayed on finish invites more possibility of crazy cracking , and is in fact how I applied it . Others however, have laid the U-Beaut Hard shellac on french polish fashion and still got crazy cracking. I think Martin was one of these. The cracking doesn't take too long to appear ( a few weeks )
Just a bad untested product . Stay well away !
I maintain a french polished ( unhardened) shellac finish is the way to go .The least inhibiting finish tonally and the sort of finish you'd expect on a hand built instrument of quality . A good wax over the finish will help protect the shellac until it hardens up further over time. Given enough time , a shellac finish is VERY durable
Craig Lawrence
- DarwinStrings
- Blackwood
- Posts: 1873
- Joined: Thu Nov 13, 2008 10:27 pm
- Location: Darwin
The first response from me is a big sigh. I would love to say that the stuff I've just used is every thing I want it to be and although it is close it doesn't win the prize, actually it is not even close, that was just wishful thinking. I was going to let it harden a few more weeks before making any comment but may as well do it now Allen has reminded me of my disappointment.
Just briefly Peter the product is a water based polyurethane made in Australia to which a crosslinking additive is added making it a little like the difference between white and yellow glue.
It sprays fine, buffs fine but when I apply the thumb nail test it is not as hard as I would like, that is to say that less pressure is needed to dent it than nitro or acid catalyzed lacquer. It also has the horrible blue hue. I guess what I want is something as hard as polyester but water based and low or no VOC. Maybe I'm just dreaming.
Shellac is great but as Dave says it can be broken down by just about anything including water or sweat. Which renders it useless in the tropics.
I know you have used the Stewy Mac finish Peter and wonder why you don't like that, is it too soft as well, does it have the same durability reports as the KTM9.
One other product from the USA that may be worth looking at is Oxford USL, their claim is....."Oxford Ultima Spray Lacquer (USL) represents a major break through in water-based coatings technology. USL is the first water-based lacquer to generate 100% burn-in regardless of the age or cure time of the previous coat. Even more remarkable, we are seeing burn-in into cured nitrocellulose lacquers and other less chemical resistant finishes. Secondly, the clarity, depth-of-image and buffability of USL is unlike any other water-based lacquer currently available. The durability and chemical resistance of USL is equal to high-end solvent-based catalyzed lacquers. Oxford USL is non-flammable, VOC compliant and HAPS Free. If you are looking for an easy-to-use, high performance water-based coating system, we suggest Oxford Ultima Spray Lacquer."
I found this one recently after my latest disappointment, here is their site if you want a look and if anyone wants to try it before me then please let me know if you are going to purchase some because I'll put off trying it until someone else does.
http://www.targetcoatings.com/shop/prod ... 86-24.html
So that was my last great hope of finding something in Australia. I will go to the USA if need be although I hate to pay all that freight on a can of mainly water if not I will bite the bullet and set up a small spray booth and use Mirotone as Allen does.
Jim
Just briefly Peter the product is a water based polyurethane made in Australia to which a crosslinking additive is added making it a little like the difference between white and yellow glue.
It sprays fine, buffs fine but when I apply the thumb nail test it is not as hard as I would like, that is to say that less pressure is needed to dent it than nitro or acid catalyzed lacquer. It also has the horrible blue hue. I guess what I want is something as hard as polyester but water based and low or no VOC. Maybe I'm just dreaming.
Shellac is great but as Dave says it can be broken down by just about anything including water or sweat. Which renders it useless in the tropics.
I know you have used the Stewy Mac finish Peter and wonder why you don't like that, is it too soft as well, does it have the same durability reports as the KTM9.
One other product from the USA that may be worth looking at is Oxford USL, their claim is....."Oxford Ultima Spray Lacquer (USL) represents a major break through in water-based coatings technology. USL is the first water-based lacquer to generate 100% burn-in regardless of the age or cure time of the previous coat. Even more remarkable, we are seeing burn-in into cured nitrocellulose lacquers and other less chemical resistant finishes. Secondly, the clarity, depth-of-image and buffability of USL is unlike any other water-based lacquer currently available. The durability and chemical resistance of USL is equal to high-end solvent-based catalyzed lacquers. Oxford USL is non-flammable, VOC compliant and HAPS Free. If you are looking for an easy-to-use, high performance water-based coating system, we suggest Oxford Ultima Spray Lacquer."
I found this one recently after my latest disappointment, here is their site if you want a look and if anyone wants to try it before me then please let me know if you are going to purchase some because I'll put off trying it until someone else does.
http://www.targetcoatings.com/shop/prod ... 86-24.html
So that was my last great hope of finding something in Australia. I will go to the USA if need be although I hate to pay all that freight on a can of mainly water if not I will bite the bullet and set up a small spray booth and use Mirotone as Allen does.
Jim
-
- Blackwood
- Posts: 115
- Joined: Tue Dec 09, 2008 1:15 pm
I guess the obvious solution when a professional level of finish is required which meets the expectations of prospective customers, is to set up a spray booth and spray nitro, urethane, or whatever.
I'm emphasisng the point here and in my initial post that customers are likely to have certain expectations and, although I might think Tru-Oil is the way to go or that a traditional french-polished finish is the best option tonally, I suspect that the guitar-buying public isn't always so well informed or as forgiving of a less than rock-hard, permanent finish. From what I've read, the water-based finishes can be ruled out for the same reasons, particularly when it comes to finishing necks.
It's my view that there's a world of difference between what's an acceptable finish for a personal guitar, or for those freely given away to friends, neighbours or relatives, and the needs that have to be met should you ever aspire to ask for serious money for your instruments.
The most frustrating aspect of all this is that I feel I'm a couple of guitars away from being able to market my instruments, but without the means to address the necessary spraying and ventilation requirements, and with the shortcomings of the more easily applied finishes so obvious, I'm pretty much snookered.
I can see the need for an Aussie version of Addam Stark, or Joe White - it'd be a no-brainer for me then!
I'm emphasisng the point here and in my initial post that customers are likely to have certain expectations and, although I might think Tru-Oil is the way to go or that a traditional french-polished finish is the best option tonally, I suspect that the guitar-buying public isn't always so well informed or as forgiving of a less than rock-hard, permanent finish. From what I've read, the water-based finishes can be ruled out for the same reasons, particularly when it comes to finishing necks.
It's my view that there's a world of difference between what's an acceptable finish for a personal guitar, or for those freely given away to friends, neighbours or relatives, and the needs that have to be met should you ever aspire to ask for serious money for your instruments.
The most frustrating aspect of all this is that I feel I'm a couple of guitars away from being able to market my instruments, but without the means to address the necessary spraying and ventilation requirements, and with the shortcomings of the more easily applied finishes so obvious, I'm pretty much snookered.
I can see the need for an Aussie version of Addam Stark, or Joe White - it'd be a no-brainer for me then!
- Bob Connor
- Admin
- Posts: 3115
- Joined: Mon Jul 09, 2007 9:43 pm
- Location: Geelong, Australia
- Contact:
-
- Myrtle
- Posts: 87
- Joined: Tue Jun 10, 2008 9:31 am
- Location: Canberra

You know what would happen Bob, I'd have to sell my wood stash, 'cause I'd run out of time to build anything myself.

Seriously though. if someone was really wanting a lacquer finish, then I could probably accommodate them, but I don't want to turn it into a full time job.
Right now I'm not interested in going into Polyester. I don't have access to the spray booths at work on a reliable basis to make it a viable option, and besides, lacquer has stood the test of time on guitars. I don't need to keep looking for a better finish.
-
- Blackwood
- Posts: 115
- Joined: Tue Dec 09, 2008 1:15 pm
Well, as everyone has been put off the U-Beaut Hard Shellac by Version 1.0 of the stuff, I guess I'll have to volunteer to be the mug that tries out the new formula. The scare tactics didn't work Craig.
With the addition of a plasticiser, hopefully it'll be more forgiving of movement in the wood. Mind you, it's interesting to note that the few people in the US who have tried the original formula have nothing but good things to say about it, either as a sprayed or french polished finish.
Anyway, whatever the outcome, I'll keep you all posted. Thanks for the opinions.
With the addition of a plasticiser, hopefully it'll be more forgiving of movement in the wood. Mind you, it's interesting to note that the few people in the US who have tried the original formula have nothing but good things to say about it, either as a sprayed or french polished finish.
Anyway, whatever the outcome, I'll keep you all posted. Thanks for the opinions.
-
- Blackwood
- Posts: 115
- Joined: Tue Dec 09, 2008 1:15 pm
I was having a gripe about all this to my partner when she arrived home from work, with reference to finding a finishing process which will meet what I perceive to be the expectations of the guitar-buying public.
Her take on the subject is that I should go with what has worked for me in the past, i.e. Tru-Oil, or try a traditional french polish, and take steps up front to manage the buyer's expectations. For instance, if I choose to go with a traditional french polish, use its advantages as a selling point rather than apologising for its apparent weaknesses. Smart lady that one!
Martin, what was your experience with the musicians playing your guitars? Do they recognise and accept that the finish is likely to need some upkeep? Were they knowledgeable in this regard or did you have to give them a good talking to?
Her take on the subject is that I should go with what has worked for me in the past, i.e. Tru-Oil, or try a traditional french polish, and take steps up front to manage the buyer's expectations. For instance, if I choose to go with a traditional french polish, use its advantages as a selling point rather than apologising for its apparent weaknesses. Smart lady that one!
Martin, what was your experience with the musicians playing your guitars? Do they recognise and accept that the finish is likely to need some upkeep? Were they knowledgeable in this regard or did you have to give them a good talking to?
- graham mcdonald
- Blackwood
- Posts: 473
- Joined: Thu Oct 25, 2007 11:57 am
- Location: Canberra
- Contact:
Despite having suffered an interesting 'antique' finish on a mandolin from V.1 of the Hard Shellac and having my queries about the problems dismissed in a cursory fashion when I raised them with the Ubeaut folks at a Working With Wood Show a couple of years ago, I am going to try it again. It is just such a Good Idea that I think we should try to make it work. If people are not willing to deal with spraying nitro lacquers (and I still am), Hard Shellac seems to be the only other way of getting a smooth glossy finish on a musical instrument other than ordinary French Polish (and that has its problems as well!) Getting the hardness/brittleness balance in any thin film finish seems to be a tricky job. In the 25 years or so that I have been playing around with nitro lacquer I have heard of various batches from respected manufacturers which ended up to hard and crazed. If Ubeaut can get this right we have a really good finish. It is interesting to note that others are experimenting with it as well. A bit of competition can only be of advantage to us.
I will report in once I have this next mando sprayed in a week or two
cheers
graham
I will report in once I have this next mando sprayed in a week or two
cheers
graham
Graham McDonald
http://www.mcdonaldstrings.com
http://www.mcdonaldstrings.com
-
- Blackwood
- Posts: 115
- Joined: Tue Dec 09, 2008 1:15 pm
Therein lies the problem. Craig has noticed crazing within a few weeks which at least gives the builder some hope of remedying the situation and to either reassess their finishing schedule or dismiss the product for future use. Looking back through the archives, however, I find that this has been known to happen up to twelve months after application - I think it was Graham himself who experienced this. Perhaps this is due to seasonal temperature variations, perhaps not, but does highlight the difficulties in assessing a new finishing product, not to mention our own individual skill in applying it.I will report in once I have this next mando sprayed in a week or two
Yesterday, I started french polishing the top of a guitar and spraying the neck with Hard Shellac - so far so good. Assuming all goes well, I may be tempted to post pictures of my shiny new guitar as evidence of my success, but as another person wrote somewhere, you're effectively playing russian roulette for the nine to twelve months after finishing with any product - even something as widely used as nitro - if the product and/or the method of applying it is new to you.
There are a number of reports of failures with U-Beaut Hard Shellac - and just as many success stories - but I haven't found any reports of success or otherwise from anyone who has used the new formula and that's a good enough reason for me to give it a try. If the plasticiser they've added is the solution to the problems of crazing, we can finally say goodbye to the perennial "what's the best finish" threads started by people like myself who don't have the means or the desire to spray the nasty stuff.
- ozziebluesman
- Blackwood
- Posts: 1554
- Joined: Wed Oct 10, 2007 9:12 am
- Location: Townsville
- Contact:
G'day Pete,
I have used the new formula Ubeaut Hard shellac on both my weissenborn copy guitars. The finish has been on since october last year and shows no signs of degredation. Each guitar received a few wash coats of the new formula hard shellac, then six 2 pound cut and then two straight from the bottle. I applied with a rubber lightly sanding between each coat. After the last two coats the guitars where left to dry and cross link for a month before sanding down to 600 grit and then polishing. I used renaissence wax and hand polished out the final finish.
I think the finish is nice and hard and it looks good. It is only satin and it was my first go at a serious finish. I did carfully prepare making sure the guitars where completely dry between each coat. I do reckon that the humidity levels have to be right when applying the hard shellac. Here in North Queensland I have to choose my days carefully.
I am very much a beginner builder and by no means an expert on the subject. This is just my opinion and what I found using the product.
Here are two pics of the Ubeat.


Cheers
Alan
I have used the new formula Ubeaut Hard shellac on both my weissenborn copy guitars. The finish has been on since october last year and shows no signs of degredation. Each guitar received a few wash coats of the new formula hard shellac, then six 2 pound cut and then two straight from the bottle. I applied with a rubber lightly sanding between each coat. After the last two coats the guitars where left to dry and cross link for a month before sanding down to 600 grit and then polishing. I used renaissence wax and hand polished out the final finish.
I think the finish is nice and hard and it looks good. It is only satin and it was my first go at a serious finish. I did carfully prepare making sure the guitars where completely dry between each coat. I do reckon that the humidity levels have to be right when applying the hard shellac. Here in North Queensland I have to choose my days carefully.
I am very much a beginner builder and by no means an expert on the subject. This is just my opinion and what I found using the product.
Here are two pics of the Ubeat.


Cheers
Alan
Alan, I think Ubeaut Hard Shellac straight out of the bottle is about a 4lb cut isnt it? Thats pretty thick for application with a pad. Looks like it went ok though.ozziebluesman wrote:Each guitar received a few wash coats of the new formula hard shellac, then six 2 pound cut and then two straight from the bottle. I applied with a rubber lightly sanding between each coat.
Cheers Martin
-
- Blackwood
- Posts: 115
- Joined: Tue Dec 09, 2008 1:15 pm
Great result Alan, and nice to see something encouraging for a change!
At the end of the day, your opinion is just as valid as the next persons, particularly if you have the practical results to back it up.am very much a beginner builder and by no means an expert on the subject. This is just my opinion and what I found using the product.
- ozziebluesman
- Blackwood
- Posts: 1554
- Joined: Wed Oct 10, 2007 9:12 am
- Location: Townsville
- Contact:
Martin, when I applied the last two coats of the Ubeaut it was very think and difficult to apply. In the end i just I slapped it on liberally and the guitars looked like the finish had been plastered on with a trowel. I was a little concerned about the high spots but they sanded back to a fine. I forgot to say in the last post that I used steel wool first before going to the fine sand papers. The finish may be thicker and thinner in spots but it did come up good!
Cheers
Al
Cheers
Al
That looks great Alan. 
As a few of you know I had a disagreement with Zpoxy and the Zpoxy won. I developed a rather nasty sensitivity to epoxy just as I was about finished grain filling some EIR. The problem for me was that I needed to sand off the last filler coat I had applied just before I became ill and then apply a final wash coat if I was to avoid patchiness.
Well if you seen the images of my arm in my epoxy warning thread, you will fully understand why that was never going to happen
. So this left me with a bit of a problem. When I sanded back the Zpoxy and leveled things out, as you would expect there were a few patches where some remained. Sanding it all out completely would have meant sanding out the filler in other areas and starting the whole grain filling process again form scratch.
I am all set up to spray nitro now, got the compressor, got the gun, got the pre-cat and water trap etc, etc, but nitro would have really highlighted those remaining patches of Zpoxy. So what to do?? I read somewhere that True-Oil is a good way to over come this problem so I decided to give it a go.
I must say that so far, this stuff looks very promising. I sanded back to 240 and wiped on a thinned down wash coat of white dewaxed shellac. I very lightly sanded this out from 240 thru 600 and applied a thin coat of True-Oil without wiping off the excess and left this sit overnight.
This morning I sanded out 240 thru 800 and reapplied True-Oil wiping off any excess to leave only an ultru thin coat. This arvo I very lightly rubbed back the surface with 0000 steelwool and blew everything clear with air. I then reapplied True-Oil and rubbed off the excess. It was stink'in hot when I was doing this, about 45C in my shed so the oil was drying very quickly. I kept at it with a clean bit of white bed sheet (she'll never know
) and burnished the oil as it continued to dry. I working one area at a time, say 1/2 of a side and then burnish lightly, do the other half the same, back to the first and burnish harder and then blend the two work areas together.
Here it is so far straight off the rag, no polish or buffing, just 3 coats of true oil and a bit of rubbing with a clean rag in between. Sorry about the poor quality images, it really does look much more impressive in real life.

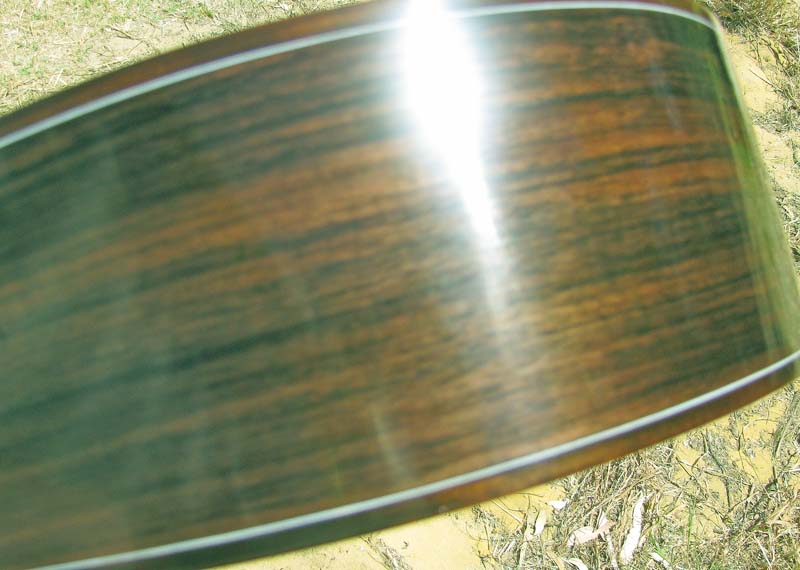
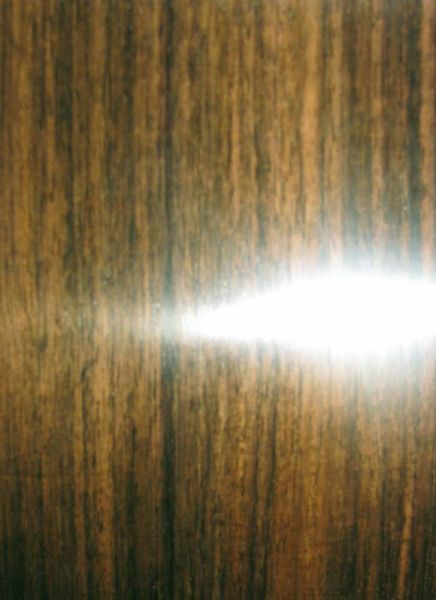
I will do a few more coats tomorrow but so far, so good. I must say that this is pretty impressive stuff to use and dead easy too. I would think that a few more coats, let it harden up for a couple of weeks, micromesh from 6000 to 12000 and then some McGuire's, and this will be an ultra thin, acoustically transparent finish with great depth and a very acceptable gloss level that is easy to repair. An if that is the case, I would not hesitate to buy a guitar coated with True-Oil.
Cheers
Kim

As a few of you know I had a disagreement with Zpoxy and the Zpoxy won. I developed a rather nasty sensitivity to epoxy just as I was about finished grain filling some EIR. The problem for me was that I needed to sand off the last filler coat I had applied just before I became ill and then apply a final wash coat if I was to avoid patchiness.
Well if you seen the images of my arm in my epoxy warning thread, you will fully understand why that was never going to happen

I am all set up to spray nitro now, got the compressor, got the gun, got the pre-cat and water trap etc, etc, but nitro would have really highlighted those remaining patches of Zpoxy. So what to do?? I read somewhere that True-Oil is a good way to over come this problem so I decided to give it a go.
I must say that so far, this stuff looks very promising. I sanded back to 240 and wiped on a thinned down wash coat of white dewaxed shellac. I very lightly sanded this out from 240 thru 600 and applied a thin coat of True-Oil without wiping off the excess and left this sit overnight.
This morning I sanded out 240 thru 800 and reapplied True-Oil wiping off any excess to leave only an ultru thin coat. This arvo I very lightly rubbed back the surface with 0000 steelwool and blew everything clear with air. I then reapplied True-Oil and rubbed off the excess. It was stink'in hot when I was doing this, about 45C in my shed so the oil was drying very quickly. I kept at it with a clean bit of white bed sheet (she'll never know

Here it is so far straight off the rag, no polish or buffing, just 3 coats of true oil and a bit of rubbing with a clean rag in between. Sorry about the poor quality images, it really does look much more impressive in real life.

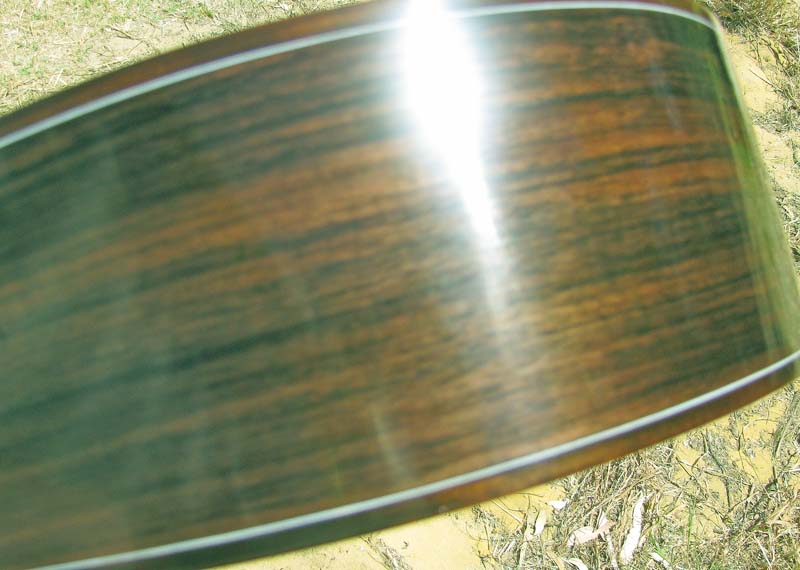
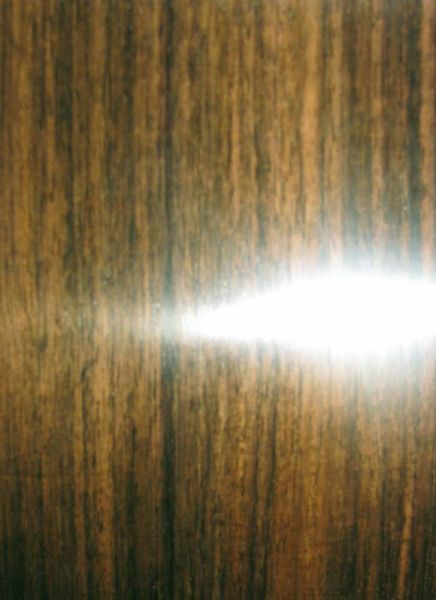
I will do a few more coats tomorrow but so far, so good. I must say that this is pretty impressive stuff to use and dead easy too. I would think that a few more coats, let it harden up for a couple of weeks, micromesh from 6000 to 12000 and then some McGuire's, and this will be an ultra thin, acoustically transparent finish with great depth and a very acceptable gloss level that is easy to repair. An if that is the case, I would not hesitate to buy a guitar coated with True-Oil.
Cheers
Kim
- John Maddison
- Blackwood
- Posts: 354
- Joined: Tue Jun 03, 2008 11:15 pm
- Location: Albany, Western Australia
- Contact:
This is turning into an enlightening thread, Pete!
Thanks for that post, Kim ... you've restored my faith in being a convert to Tru-Oil. I am reckoning that if it's good enough for preserving gun stocks that get a fair bit of rough treatment, why not apply it to instruments!!
Have only had one go at using it, on a Tenor Uke of high-figured Tassie Blackwood w/Tiger Myrtle bindings from TimS. This finishing process was very much trial & error, with several helpful hints from Dave Hurd, and I made sure to try the technique out on a sample board first to build confidence.
I sanded the surface to 600grit after pore filling with some watery pre-coloured timber putty from Bunnings. Six coats of Tru-Oil was applied (importantly, with 'smooth' rag e.g. T-Shirt material that needs to be clean and LINT FREE), each coat a day apart and rubbed with 0000 steel wool between coats. I didn't try to burnish each coat as you've suggested Kim, just applied it evenly and stopped rubbing after a few minutes when the oil became tacky. Because it was on a uke I did a whole surface in one go but on a larger bodied instrument your idea of doing a panel in stages is a good one.
After 6 coats I let the uke sit for 5 weeks to harden off, then did a light rubbing with wet 4000 Micromesh, then treated it with a coat of 02B ultra-fine cutting compound all over.
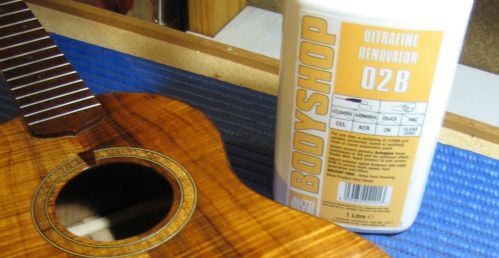
To finish the process I did a coat or two of Feats-Watson Carnauba Wax (brown) and rubbed like hell to a fairly fine gloss.
View down the neck, OrganOil applied to fingerboard, and yeah - the bindings ARE too fat - the routing bit in the Dremel slipped - but that's a whole other story:
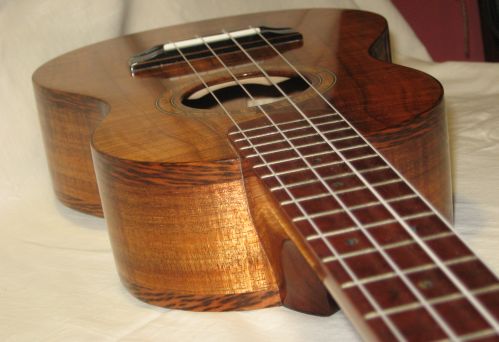
View of back:
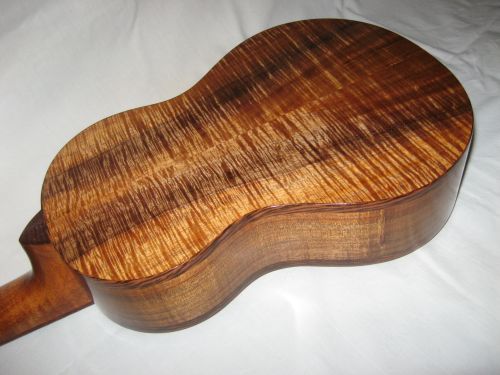
I still have reservations about the carcenogenicity of this product but like any modern-day chemical I think it's important to observe good OH&S practices i.e. use kitchen gloves and/or wash hands after use, and dispose of rags appropriately (let 'em dry first!). One other thing I did was not to re-use the rag from previous coat - throw it way and get a new bit. Also, KEEP THE LID ON the bottle, this stuff develops a skin when in contact with air. In fact David Hurd made a good suggestion to me to just prick the foil seal with a panel pin when opening for the first time, and apply the oil as drops.
Kim - what is "McGuires"?
Cheers
Thanks for that post, Kim ... you've restored my faith in being a convert to Tru-Oil. I am reckoning that if it's good enough for preserving gun stocks that get a fair bit of rough treatment, why not apply it to instruments!!
Have only had one go at using it, on a Tenor Uke of high-figured Tassie Blackwood w/Tiger Myrtle bindings from TimS. This finishing process was very much trial & error, with several helpful hints from Dave Hurd, and I made sure to try the technique out on a sample board first to build confidence.
I sanded the surface to 600grit after pore filling with some watery pre-coloured timber putty from Bunnings. Six coats of Tru-Oil was applied (importantly, with 'smooth' rag e.g. T-Shirt material that needs to be clean and LINT FREE), each coat a day apart and rubbed with 0000 steel wool between coats. I didn't try to burnish each coat as you've suggested Kim, just applied it evenly and stopped rubbing after a few minutes when the oil became tacky. Because it was on a uke I did a whole surface in one go but on a larger bodied instrument your idea of doing a panel in stages is a good one.
After 6 coats I let the uke sit for 5 weeks to harden off, then did a light rubbing with wet 4000 Micromesh, then treated it with a coat of 02B ultra-fine cutting compound all over.
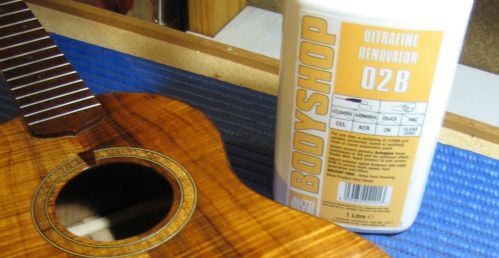
To finish the process I did a coat or two of Feats-Watson Carnauba Wax (brown) and rubbed like hell to a fairly fine gloss.
View down the neck, OrganOil applied to fingerboard, and yeah - the bindings ARE too fat - the routing bit in the Dremel slipped - but that's a whole other story:
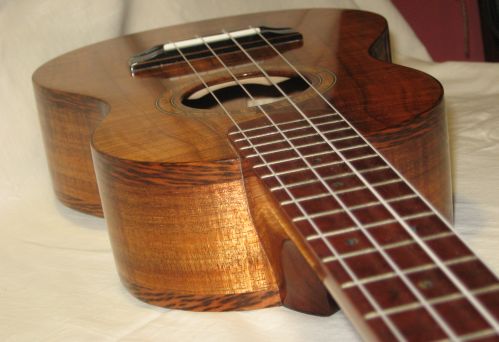
View of back:
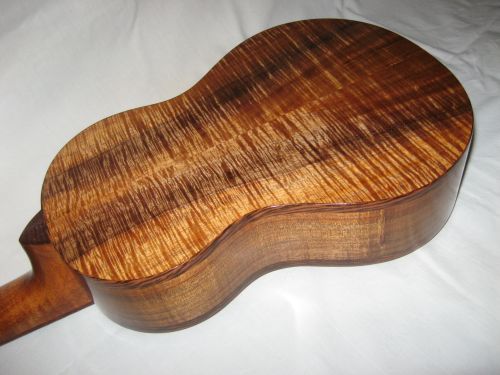
I still have reservations about the carcenogenicity of this product but like any modern-day chemical I think it's important to observe good OH&S practices i.e. use kitchen gloves and/or wash hands after use, and dispose of rags appropriately (let 'em dry first!). One other thing I did was not to re-use the rag from previous coat - throw it way and get a new bit. Also, KEEP THE LID ON the bottle, this stuff develops a skin when in contact with air. In fact David Hurd made a good suggestion to me to just prick the foil seal with a panel pin when opening for the first time, and apply the oil as drops.
Kim - what is "McGuires"?
Cheers
John M
Just my dig at the McDonald's of car polishing products John, what you finish with is pretty much the the same dog with a different leg action.John FM wrote: Kim - what is "McGuires"?
Cheers
http://www.meguiars.com/
No big secret on process, LMI has reasonable instructions on the site http://www.lmii.com/CartTwo/TruOil.htm I just adjusted to suit myself. As for the True-Oil skinning over in the bottle, it help to keep some marbles handy, as the bottle empties, top it up with marbles to keep the liquid up in the neck and exclude air.
Cheers
Kim.
- graham mcdonald
- Blackwood
- Posts: 473
- Joined: Thu Oct 25, 2007 11:57 am
- Location: Canberra
- Contact:
I have got a new bottle of Hard Shellac and I will start on the mandolin in the next week or so. It has a use-by date of 3/2010, and I was wondering in anybody knew when Ubeaut started using the new formula? No-one answering the phone there this morning. It might well have been me who first asked the question about the crazing. It was mid 2007 and they sounded very surprized at the very idea that such crazing could happen. It had to be entirely my fault for spraying it too thickly. As you can imagine I was fairly underwhelmed by their attitude, but the potential for such a product is just too good to dismiss it. Someone did mention that Shines have a similar product out, but I haven't chased it down.
Another very simple finish to consider is Minwax Wipe-on Poly. Bunnings stock it! I used the satin version of it over zpoxy on a guitar with it recently and it is very simple to use. They suggest just using a piece of cloth to apply it and sanding between coats. That left noticeable scratches to I put it on with 600grit wet&dry and it came up very well. If anything a bit too flat, but that could be sorted with some wax I figure. Don't know about the gloss version.
cheers
graham
Another very simple finish to consider is Minwax Wipe-on Poly. Bunnings stock it! I used the satin version of it over zpoxy on a guitar with it recently and it is very simple to use. They suggest just using a piece of cloth to apply it and sanding between coats. That left noticeable scratches to I put it on with 600grit wet&dry and it came up very well. If anything a bit too flat, but that could be sorted with some wax I figure. Don't know about the gloss version.
cheers
graham
Graham McDonald
http://www.mcdonaldstrings.com
http://www.mcdonaldstrings.com
Who is online
Users browsing this forum: No registered users and 211 guests