Should we inlet the X-Braces?
-
- Blackwood
- Posts: 310
- Joined: Sun Jan 13, 2008 10:22 am
- Location: Santa Cruz, Ca.
- Contact:
The most moisture resistant of the modern polymers we use on wood are epoxies, hence their use in boat building. Not even polyester can prevent moisture migration and is itself degraded when in water...the dreaded fiberglass/polyester blistering that happens on boats.
Hadn't though of that re. super-caps, but of course, you want the interiors of those things to be at zero humidity or the dilectric layers are just going to go to hell in a handbasket, and you're trying to store some real voltage and current capacity there. Interesting new applications in the burgeoning plug-in hybrid automotive world... There's a company that claiming incredible capacity using barium titanate, one of the compounds that when doped with lead also exhibits piezoelectric properties.
Hadn't though of that re. super-caps, but of course, you want the interiors of those things to be at zero humidity or the dilectric layers are just going to go to hell in a handbasket, and you're trying to store some real voltage and current capacity there. Interesting new applications in the burgeoning plug-in hybrid automotive world... There's a company that claiming incredible capacity using barium titanate, one of the compounds that when doped with lead also exhibits piezoelectric properties.
Rick Turner
Guitar Maker, Experimenter, Diviner
www.renaissanceguitars.com
www.d-tar.com
Guitar Maker, Experimenter, Diviner
www.renaissanceguitars.com
www.d-tar.com
- matthew
- Blackwood
- Posts: 1193
- Joined: Mon Oct 08, 2007 1:16 pm
- Location: Sydney, Inner West
- Contact:
and I have a number of times tried to bring Munster and Camembert from France into England, and the last time I sealed everything into 5 nested ziplock bags, some taped up ... and my backpack STILL reeked like teenage sneakers in the train ...Paul B wrote:I spent 4 years in R&D trying to prevent moisture ingress into supercapacitors.
Sealing inside as an RH buffer
I dug this thread back up because of an interesting post by Colin Symonds over at the OLF that I thought had relevance. Not that there is anything unusual about Colin's post being interesting, in fact that is the norm and I see that our newest member is indeed a ColinS. It would be great if they are one and the same, but either way, a very big welcome to the ANZLF ColinS.
Back to topic, Colin Symonds mentions that he uses Egg White as a base coat prior to an oil varnish or shellac based finish and I think this could be a great idea to employ on the inside of an instrument when applying a finish as an RH buffer as discussed above.
If nothing else, at least this method may prevent colour leeching from EIR etc into the spruce components and may also work well over your label.
http://www.luthiersforum.com/forum/view ... &sk=t&sd=a
Any Thoughts?
Cheers
Kim
Back to topic, Colin Symonds mentions that he uses Egg White as a base coat prior to an oil varnish or shellac based finish and I think this could be a great idea to employ on the inside of an instrument when applying a finish as an RH buffer as discussed above.
If nothing else, at least this method may prevent colour leeching from EIR etc into the spruce components and may also work well over your label.
http://www.luthiersforum.com/forum/view ... &sk=t&sd=a
Any Thoughts?
Cheers
Kim
- matthew
- Blackwood
- Posts: 1193
- Joined: Mon Oct 08, 2007 1:16 pm
- Location: Sydney, Inner West
- Contact:
Egg white size is a very old technique and has been used for years in violin making. Some people think its a great idea and others hate it. Another protein based size is weak hide glue. Same principle i think. Others use sodium silicate (waterglass) to achieve the same result.
personally, i don't know how things stick to egg white. I guess i know that dried egg white on a glass bowl can be scratched off with a fingernail, whereas hide glue stays put.
I used shellac as a ground and sealer for my bass sides and back (silky oak) and wiped on cabots danish oil. The shellac stopped the oil from soaking into the wood. I didn't use tung oil because no matter what I did, it soaked deep into the wood. I wiped danish oil directly onto the cedar top; didn't seem to soak in at all.
I also used weak shellac to lightly seal the interior of the bass to slow moisture uptake. No idea if this has helped or not, but I hardly notice any changes due to humidity.
personally, i don't know how things stick to egg white. I guess i know that dried egg white on a glass bowl can be scratched off with a fingernail, whereas hide glue stays put.
I used shellac as a ground and sealer for my bass sides and back (silky oak) and wiped on cabots danish oil. The shellac stopped the oil from soaking into the wood. I didn't use tung oil because no matter what I did, it soaked deep into the wood. I wiped danish oil directly onto the cedar top; didn't seem to soak in at all.
I also used weak shellac to lightly seal the interior of the bass to slow moisture uptake. No idea if this has helped or not, but I hardly notice any changes due to humidity.
- sebastiaan56
- Blackwood
- Posts: 1274
- Joined: Sun Oct 28, 2007 5:23 am
- Location: Blue Mountains
Joshua French and Colin Symonds use plain egg white separated from the yolk. No beating. Joshua in a Tequila glass, Colin in a Highball glass.
I used a Salsa jar. Guess that puts me in the right league!
I used a Salsa jar. Guess that puts me in the right league!

Waddy
Build Albums 12 done - 1 in process
Clip for #1 Barrios' "Una Limosna por el Amor de Dios" - Not me playing
Build Albums 12 done - 1 in process
Clip for #1 Barrios' "Una Limosna por el Amor de Dios" - Not me playing
Kim, yes it is me! At least last time I looked it was, Dave told me about the forum so I thought I'd check it out, recognise a lot of the people here.
As to the original question I do tuck the upper bout legs of the X but taper away the lower bout arms to nothing about 3mm from the linings. This is for a flexibility reason not fear of failing joint.
As some of you will know, one of the things I do is restoration work on historic instruments for several museums. Most if not all of these were put together with a collagen glue of some sort, and probably not of the purity we use now. It's very rare for a joint to come apart on these without there having been some sort of mechanical cause. The oldest instrument I've worked on dated back to the late 16th century and a good threequarters of the joints were as strong as the day they were made, probably stronger.
Egg white? well yes I do use it on all of my tops particularly, The chemists at my university have analysed a lot of finishes on instruments over the years and a lot of the old Spanish, Italian and German instruments has an egg size. On many German lutes it was in fact the only treatment applied to the top. On this particular Brunner lute that I worked on it was the tops only finish.
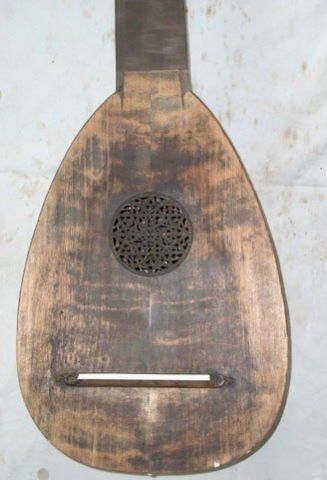
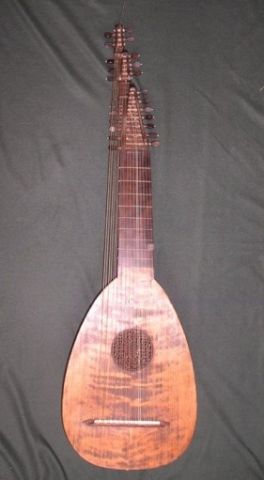
As to the original question I do tuck the upper bout legs of the X but taper away the lower bout arms to nothing about 3mm from the linings. This is for a flexibility reason not fear of failing joint.
As some of you will know, one of the things I do is restoration work on historic instruments for several museums. Most if not all of these were put together with a collagen glue of some sort, and probably not of the purity we use now. It's very rare for a joint to come apart on these without there having been some sort of mechanical cause. The oldest instrument I've worked on dated back to the late 16th century and a good threequarters of the joints were as strong as the day they were made, probably stronger.
Egg white? well yes I do use it on all of my tops particularly, The chemists at my university have analysed a lot of finishes on instruments over the years and a lot of the old Spanish, Italian and German instruments has an egg size. On many German lutes it was in fact the only treatment applied to the top. On this particular Brunner lute that I worked on it was the tops only finish.
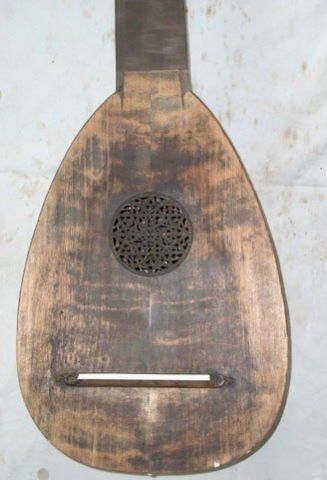
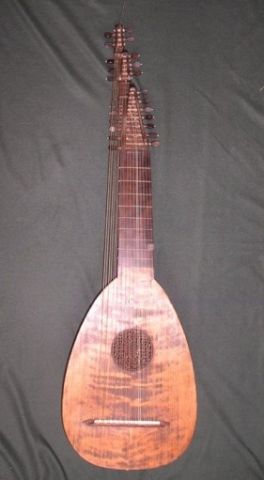
Last edited by Colin S on Thu Apr 24, 2008 6:05 pm, edited 1 time in total.
- sebastiaan56
- Blackwood
- Posts: 1274
- Joined: Sun Oct 28, 2007 5:23 am
- Location: Blue Mountains
I don't think it would add any mechanical strength, but it does seen to 'tighten' up the wood giving the impression of a hardened surface. The egg size will also raise the grain on the wood, which rather than sand off I hand buff with a course cloth.sebastiaan56 wrote:Colin,
Do you think the size added strength around the rosette? Im up to that bit in Robert Lundberg's book. My personal project is a cittern after 16C English style,
Sebastiaan
Don't forget that the rose will have small braces added on the inderside, good tip to stain the gluing surface of these prior to gluing to the underside so that they are not obvious from the top. If you look at the underside of this lute top you'll see a number of braces crossing the back of the rose. But they are not visible, runining tha pattern on the finished instrument.
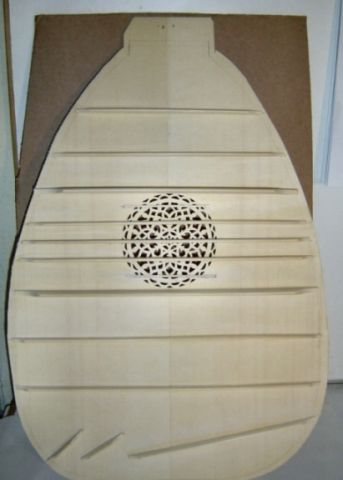
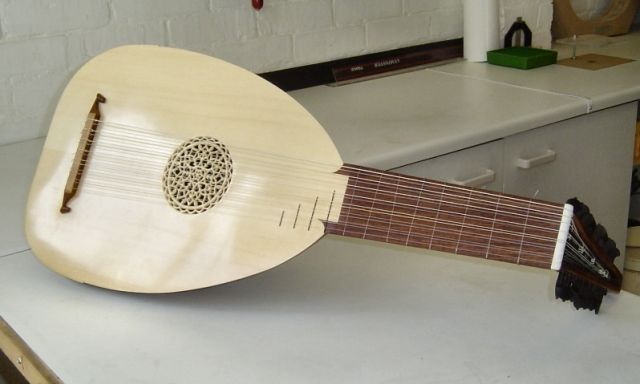
Colin
Who is online
Users browsing this forum: No registered users and 74 guests