Recently, alongside some serious thinking about reducing the weight of basses I build, it occurred to me that half the issue is too much weight in headstocks. Ie. we've got a stack of timber and metal tied up, where it becomes a problem for balance and weight.
There are answers to the metal weight problem in hipshot ultralights and Wilkinson Deco rotomatic guitar tuners like I've used on my recent 6 string.
http://www.ebay.com.au/itm/Guitar-Parts ... 0871654657
So I took it all to the next logical point and started looking at reducing the amount of timber in the headstock. I figured, "neck timber is usually heavy. If I can use less timber, the headstock will get even lighter". Which got me looking at string tensions...
http://www.kevinkastning.com/D'Addario_ ... _chart.pdf
These are the figures for D'addario XL 34" 45-105 gauges strings at regular EADG tuning;
G - 42.8 newtons
D - 51.3 newtons
A - 48.2 newtons
E - 40.3 newtons
It was when I saw these figures that I realized most of the designs we use for headstocks put the tuners for highest tension strings a long distance from the nut.
Specifically, traditional headstock designs are all wrong for the forces they encounter.
My wife warned me, "I hope you're right. That's a pretty arrogant claim." She's right, but indulge me. I think I'm onto something... Here's my 6 string headstock.

The highest tension strings are D and A respectively... FURTHEST AWAY from the nut.
That is to say, more than doubling the leverage on the headstock than the B and C strings (34.5 and 38.9 newtons respectively).

So, no wonder Gibsons with mahogany necks keep snapping their headstocks off when dropped backwards. The two strings pulling the hardest are pulling up near the end of the headstock.

Fenders are little better really with the D string even further up the headstock than the A. So a fall that might not result in a crack without the strings, is exacerbated with the string tension on the neck causing structural cracks.
[FONT="Arial Black"]Solutions[/FONT]
When I started to consider a good engineering solution for this problem, I realised the issue was getting the D and A tuners as close the nut as possible. This is counter-intuitive to 500 years of guitar design. However, people have done it. I'll show you two headstocks that feature what I'd call a "low tension" headstock.
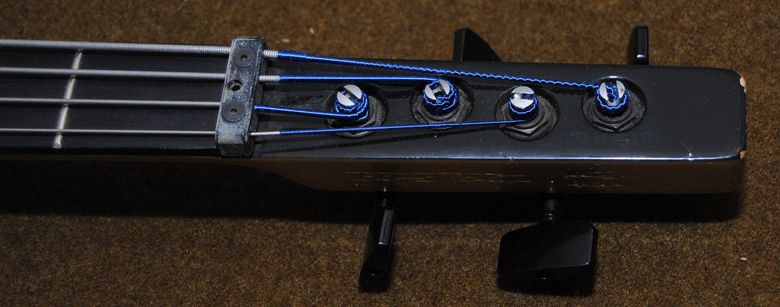
Gibson's 20/20 compact headstock.

Atlansia Stealth.
I'm not entirely sure if these guys figured out the tension issues I did, but in the case of Atlansia, it's entirely possibly. The guy is awesome and his designs are decades ahead the rest of us.
Anyway, I hope this will be the stimulus for some discussions on building stronger, lighter headstocks and basses for players to enjoy in the years to come.
Cheers,
Pete
As a post script, I came across Philip Kubicki's article on the first headless bass built at fender and it's effect on cancelling out deadspots... Fascinating reading! :hyper:
http://www.vintageguitar.com/1772/fender-headless-bass/