With this in mind, and after repeated requests to show some interested folks at the Cairns and District Woodworkers Guild were I'm a member on how to build an instrument, I decided that my level of competency was at a point that I'd be able to take on the challenge.
I put a proposal together and let the membership know that I'd co-ordinate the purchasing of materials etc. in order to keep costs under control. The economy of bulk purchases, and my experience in whom to ask and where to go for the best value for the dollar. I had intended on only allowing 6 people to participate, but that quickly filled up, and I ended up with a waiting list for the next class. Didn't know that I might be making a bit of a career out of it.

Long story short, I finally ended up with 8 participants who have varying degrees of woodworking experience, but none of them have built anything like a ukulele, except for Liam who is a member of our forum here and recently completed a ladder braced parlor guitar.
I contacted Tim Spittle at Australian Tonewoods many weeks ago and arranged for some high figured Tassy Blackwood for Tenor sized ukes. Tim sent some really spectacular wood with several different figure patterns. It was interesting to see what people who really don't know much about instruments picked as their preferred pattern. It's been my experience that the wood with some sap wood highlights is usually the first to go when offered to luthiers. This was the last to go however with the participants in the class.
When I build at home, I usually have lots of leeway in length and width of stock, and when I stuff something up, it's not that big of a deal to go and find another piece. With other peoples wood that is fairly closely dimensioned its a different matter. And I've been known to have dyslexic moments....haven't most of us.

I thought that the best way of tackling this was to do a mock up of the parts, dimensions similar to the smallest pieces that we were supplied. I did these in New Guinea Rosewood, as I've got some sides and back all ready to go on another instrument, so a neck is just what I need. I haven't got any pictures of this part yet, but will soon.
The other part of the day was to shoot the back and top joints, and get them glued up. This was a real eye opener for everyone in the class. How to get a light tight joint with minimal effort. Thankfully the first couple of pieces that I demonstrated on were dead easy, to make me look like I knew what I was doing.

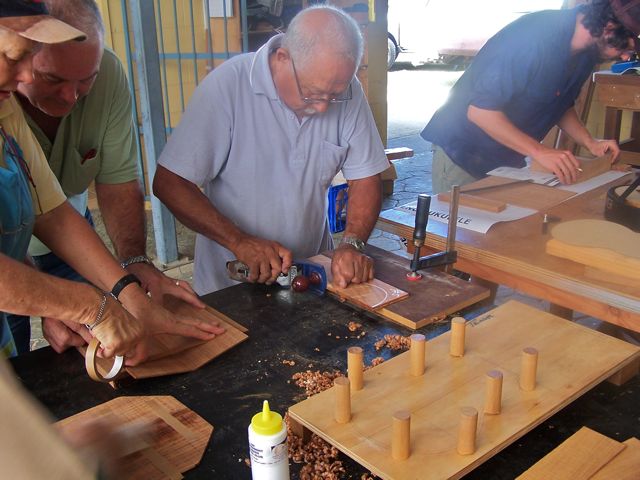
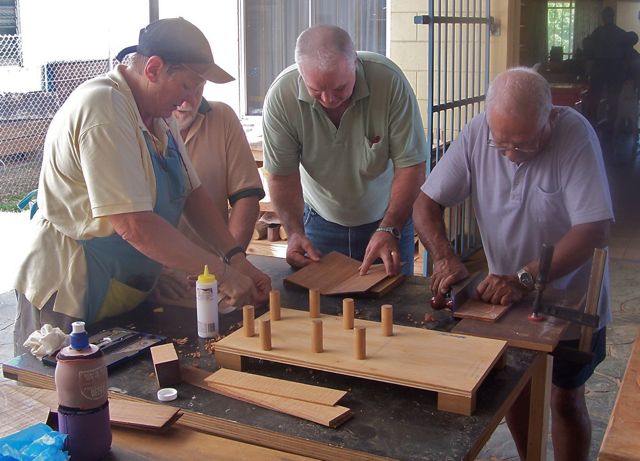
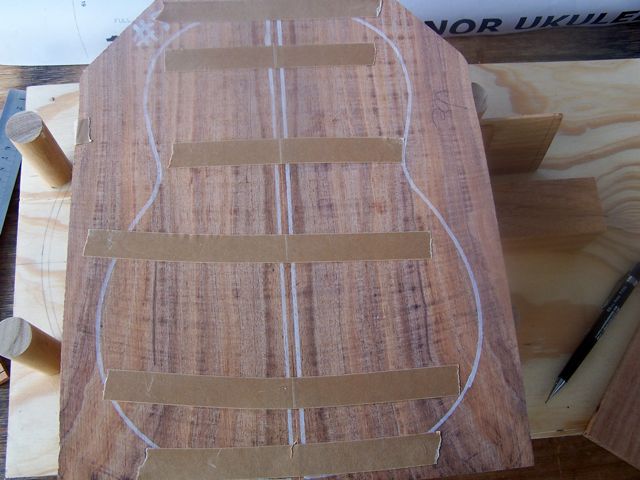
The class is scheduled for weekends, and some evening work, to accommodate my day job. So additions to this thread will be a little intermittent, but I hope that some of you will find it of interest.