There are some interesting articles on luthiers and luthiery in general which I'll post from time to time.
If there are any copyright issues or anyone would like these articles removed I'm more than happy to remove them.
This first article is about the sawmilling operations at the CF Martin Factory.
Check out the long hair on the operator. No OHS issues with that in those days.

============================================
C.F. Martin Wood Mill
Nazareth (P.A.)
By Jim Hatlo
Frets August 1979
============================================
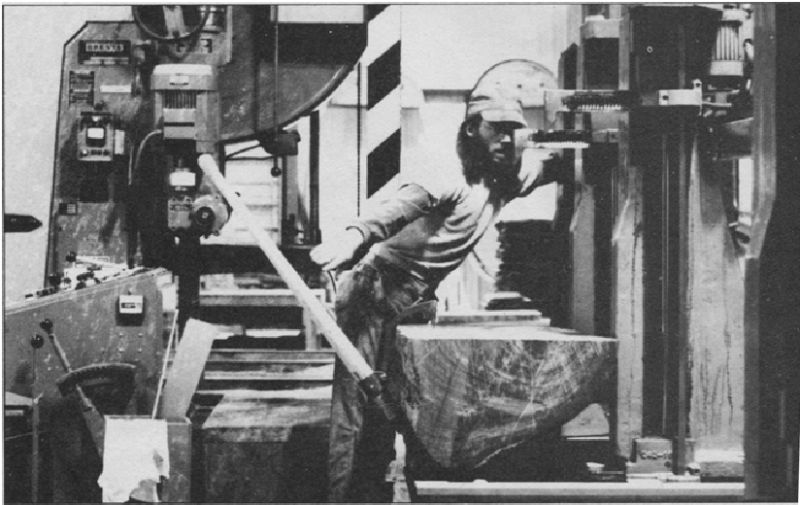
WITHOUT WOOD, what form would the predecessors of todays' stringed instruments have taken? Wood is still the primary material used in the construction of stringed instruments. We usually see only the end product, lacquered and shining, the grains and textures rich with color. Sometimes we forget that it originally had to be sawn out of a log.
Instrument makers think of wood in three main categories: as ready-to-use instrument tops, backs, and sides; as boards that must be "re-sawn" into smaller units; or as longs that must be "broken down" into board lumber. Most limited-production makers (those producing up to 100 instruments per year), purchase their woods in pre-cut pieces. Tops and backs are purchased in "matched sets" and need only to be sanded to final thicknesses, glued together, and cut to shape. Neck stock is purchased as boards, which can be handled on a small band saw capable of cutting through two or three inch stock.
All major manufacturers are prepared to buy large boards for tops and backs and re-saw — that is, re-cut the boards into thinner and smaller pieces. This "mill room" type of operation requires a powerful bandsaw with a large work surface, a planer with rotary blades to smooth the boards and make them square, and thickness sanders—revolving drum sanders that sand the thinner woods to their final thickness and smoothness. Few manufacturers, however, have ventured into the "breakdown" side of lumber handling: taking full-size logs and cutting them into workable boards.
In 1975, the C.F. Martin Organisation erected a building adjoining its modern factory in Nazareth, Pennsylvania, and installed new, modern log-handling and log-sawing equipment to ensure full control over the selection and grading of woods to be used in Martin guitars. The new mill allowed Martin to follow a piece of wood through from log to finished product, giving the company complete supervision over its raw materials and the cost of processing them. While Sitka spruce for tops continued to be purchased pre-cut from outside sources, rosewood and mahogany for backs and sides were handled exclusively by the mill, which was devoted 100 percent to Martin wood production.
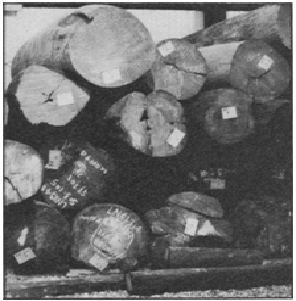
Back when Martin could still import whole logs, piled Indian rosewood logs awaited their turn at the band saw. The smaller logs in the foreground are ebony.
"Most of the time we bought logs at foreign government auctions," says Martin operations manager Joe Steinbach. "We would personally inspect them, and sometimes we'd even have a piece cut off to check the color, grade, and sap content. Through these personal inspections we kept waste resulting from bad logs down to perhaps two percent. Most of the time, by looking at the ends and looking down the length, we had a pretty good idea of what was in any log."
The logs would go from their country of origin (Brazil or India for rosewood, and usually Honduras for mahogany) to Martin's Nazareth facility. There they would be examined by the chief saw operator, or "sawyer," for grain pattern, blemishes, and other features, with the same thoroughness that a diamond cutter would examine an uncut stone. The sawyer then carefully placed ("laid out") the log on the saw carriage and began the process of cutting it lengthwise into smaller sections.
"First you have to figure out which way the heartwood twists through the log," says Bill Hall, Martin's sawmill production manager and the mill's first sawyer. "The best thing you can do when you open the log up is to open it where most of the defects are. You try to expose those on the first cut. Then you get your size, get the grain straight, and try to get a good quarter cut so that you have a nice grain stripe and can bend the sides properly."
After the mill processed the logs into lumber, it cut the boards into rough-shaped blanks for tops and sides and then dried the blanks in its lumber kiln. That inventory of dressed and seasoned material supplied the neighboring Martin instrument factory.
Why all these references in the past tense? Because several years ago, major wood-supplying nations decided that they wanted a bigger share of the instrument manufacturing action. Such countries as Brazil and India reasoned that they were giving away too much of the profit on their native woods by allowing raw logs to be exported for milling elsewhere. They then clamped an embargo on such exports, in effect telling their former customers, "If you want lumber for your instruments, you'll have to buy it here and pay our workers for milling it."
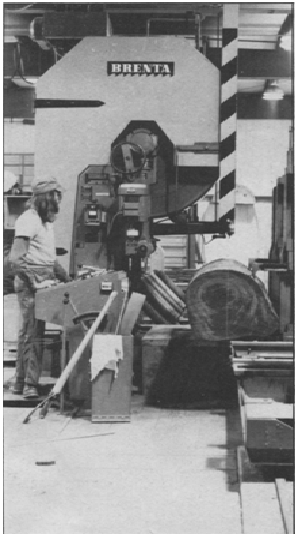
The operator of a mill's cutting saw is called a "sawyer." Martin uses a band saw in place of the traditional circular saw because (among other technical advantages) the "kerf," or total cut width, is less. The smaller cut leaves more wood and less sawdust.
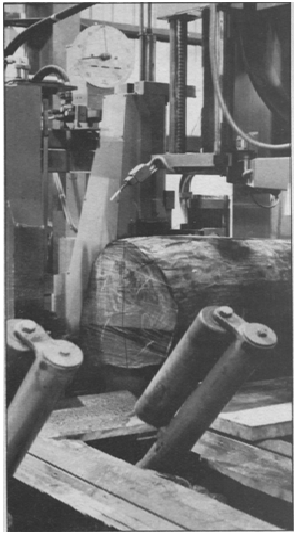
Martin's saw is a precision tool. The logs are held in place with special clamps and the entire log-holding frame is moved laterally, directed from a set of controls on the sawyer's panel.
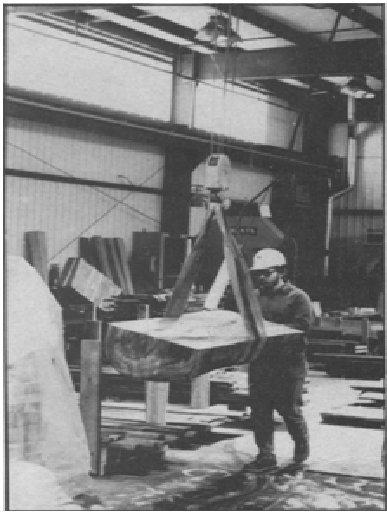
The "cant," or half-log, is carried back to the storage area with the aid of an electrically operated overhead crane.
That action had a far-reaching effect on the instrument-making business. "No one has been getting any Indian rosewood logs out of India for the last two years," says Steinbach. "Everything has to be bought in India already cut. You can't bring mahogany logs into the country anymore, either; Martin buys mahogany in plank form for necks. We use Indian ebony for fretboards, but the blanks are cut there, too. I now travel to India to inspect the pre-cut backs, sides, and fretboard blanks, because we get better quality control by examining them there piece by piece. Two years ago, when I joined the company, Martin saw this coming, and we decided to expand the capabilities of the sawmill into other areas. Today, Martin instruments are no longer 100 percent of the mill's business."
Martin has kept its mill open and profitable by branching into outside sales, both export and domestic, and by turning to other kinds of woods—African woods, South American woods, and some domestic woods. The logs are cut into lumber and sawn veneer, with much of that output sold to European furniture producers. Since last fall, most of the mill's involvement with Martin instrument woods has been limited to re-inspecting and kiln processing precut materials coming from abroad.
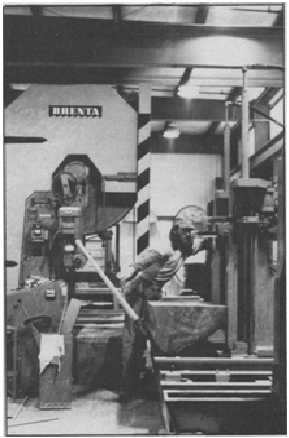
The sawyer then rotates the log 90 degrees and positions it with the aid of a "cant hook," a wooden-handled bar with steel hooks
The precision capabilities built into the mill for its instrument-wood applications make it ideal for milling other varieties of fine lumber. Bill Hall and his assistant, sawyer John Ventin, can cut wood to tolerances within a tenth of a millimeter. The saw itself is a band saw, rather than the large circular saw usually associated with sawmills, because the band saw blade's narrower "kerf"(cutting width) creates less waste. The carriage that feeds logs and lumber into the blade is hydraulically operated and can handle logs weighing thousands of pounds as gingerly as a seamstress at a sewing machine would handle pieces of silk. An electrically operated over-head crane with a five-ton capacity transports logs from their storage piles to the saw carriage.
"All logs are different," says Hall. "You have to look at each one to figure out what it has inside it. I've taken eight or nine logs and marked them all out ahead of time for cutting, but I've found that doesn't work as well as just taking one log, looking it over and checking it out, and then sawing it."
Sawing different types of wood requires special skills. Rosewood, for example, offers some special problems. "We had one ten-foot, four-ton log here that we recently custom-cut into table tops," says Steinbach, "and it took eight saw blades to go through that log. Other times, a blade could be used for two or three logs."
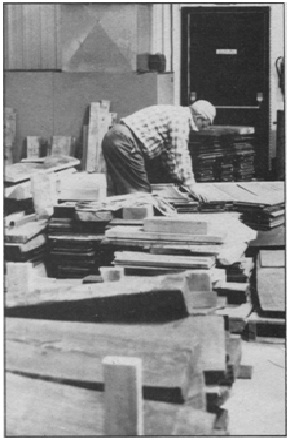
When the pieces have been sliced from the cant, they are inspected, numbered in pairs, and placed in Martin's kiln for seasoning.
"There are mineral deposits in rosewood that look kind of like limestone, except they're harder," explains Hall. "You hit a patch of that and you can dull a blade in one shot, even though the teeth on our blades have special hardened tips. But we've changed blades enough now that we can put a new one on in five minutes, so we don't lose much time."
Martin is currently looking at new sources of rosewood logs and evaluating their potential. It is conceivable that someday the main thrust of the mill's production will again be wood for Martin guitars, but the days when its output was exclusively for Martin instruments appear to be gone for good.
"We would have a problem with over-production if the mill went back to doing nothing but guitar woods," says Martin sales representative Eddie Master. "We were still honing the operation at the time the mill was doing Martin production alone. Now that we've got it down, it would take a new instrument factory four times the size of our present one to handle all the wood that the mill can turn out."