grain on soundboards - wide on the outside, or the centre?
- Mark McLean
- Blackwood
- Posts: 1174
- Joined: Thu Apr 10, 2008 2:03 pm
- Location: Sydney
grain on soundboards - wide on the outside, or the centre?
I recently got an Adirondack board from Tim Spittle. I am going to use it with a set of mahogany B&S for my Nick Lucas style L-00 project. Like most Adi it has very visible grain which is fairly tight on one edge and wider grained on the other. Most guitar tops seem to be bookmatched with the wider grain towards the outside and the narrower grain in the centre, although I have seen some notable exceptions including some old Gibson and Martins. Is it important?
I am asking because this a narrow board and there is some runout towards one end on the edges with the tight grain. If I put the wide grain in the centre I can have this runout in the waste - but if I put the tight grain along the centre join this bad area will be right in the middle. Tim sent me the board set up to join the good (wide grained) side, with an outline already penciled on and an almost perfect jointing edge (God bless him).
Bob, I notice that your current Coco/Adi build also has the soundboard with wider grain in the centre. Why did you choose to join it like that? I think it looks great. Can anybody give me a reason not to do it that way?
cheers
Mark
I am asking because this a narrow board and there is some runout towards one end on the edges with the tight grain. If I put the wide grain in the centre I can have this runout in the waste - but if I put the tight grain along the centre join this bad area will be right in the middle. Tim sent me the board set up to join the good (wide grained) side, with an outline already penciled on and an almost perfect jointing edge (God bless him).
Bob, I notice that your current Coco/Adi build also has the soundboard with wider grain in the centre. Why did you choose to join it like that? I think it looks great. Can anybody give me a reason not to do it that way?
cheers
Mark
- Bob Connor
- Admin
- Posts: 3115
- Joined: Mon Jul 09, 2007 9:43 pm
- Location: Geelong, Australia
- Contact:
I don't totally agree with you Matthew in respect to a correlation between growth lines per inch and stiffness.
I think you'd have to assess each piece of wood on it's merits.
Some of the tighter grained Sitka I've used was like cardboard whereas the Red Spruce I've got is stiffer in the wide grained area of the board.
It MAY be an advantage on a steel string acoustic to put the floppy wood in the centre as this area has significant bracing and bridge plates attached to it. That would leave the stiffer material on the edge of the soundboard so you could thin it more and make the whole top lighter.
I guess this would apply to double bass tops as well.
I'd be inclined to join whichever way you want and voice it accordingly.
If you could build two identical guitars with the same piece of wood for the top, but reversed, I doubt that anyone would be able to pick which is which.
Mostly it is down to how the builder voices the top once you have braces and bridge plate attached and knowing that there has to be another brace glued on later - the bridge.
I think you'd have to assess each piece of wood on it's merits.
Some of the tighter grained Sitka I've used was like cardboard whereas the Red Spruce I've got is stiffer in the wide grained area of the board.
It MAY be an advantage on a steel string acoustic to put the floppy wood in the centre as this area has significant bracing and bridge plates attached to it. That would leave the stiffer material on the edge of the soundboard so you could thin it more and make the whole top lighter.
I guess this would apply to double bass tops as well.
I'd be inclined to join whichever way you want and voice it accordingly.
If you could build two identical guitars with the same piece of wood for the top, but reversed, I doubt that anyone would be able to pick which is which.
Mostly it is down to how the builder voices the top once you have braces and bridge plate attached and knowing that there has to be another brace glued on later - the bridge.
- Mark McLean
- Blackwood
- Posts: 1174
- Joined: Thu Apr 10, 2008 2:03 pm
- Location: Sydney
I figured that stiffness would be the main variable that might be affected. It makes sense that it could be adjusted for in the bracing. I am happy with the way that it looks, so I will go ahead and joint it with the wide grain in the centre. When it comes to the 'tuning' of the top there are a whole lot of mysteries for me! I might bring that up in another thread when I get to that stage
One reason to joint at the finer grain edge is that it makes the glue line harder to detect. On that point the term "Runout" does not refer to the alignment of grain lines visible upon the surface of the top. Rather it is a term used to describe the angulation, or shortness of grain running 'through' the plate, from the underside to the top surface of the board.
This is the reason you see dark and light halves on some guitar tops. This contrasting is an effect of light refraction of the short grain. As proof you will notice that the light side will become the dark side should you turn the guitar around and view from the original aspect, the greater the contrast, the greater the runout in the top.
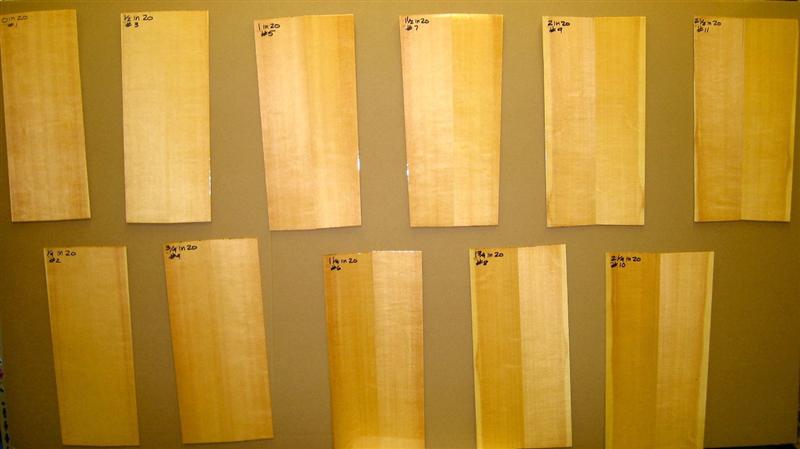
This is all well and good once you have a finish on the guitar but runout is quite hard to detect otherwise. This post from Craig Carter does remove some of the mystery however.
Hope this was somewhat helpful,
Cheers
Kim
This is the reason you see dark and light halves on some guitar tops. This contrasting is an effect of light refraction of the short grain. As proof you will notice that the light side will become the dark side should you turn the guitar around and view from the original aspect, the greater the contrast, the greater the runout in the top.
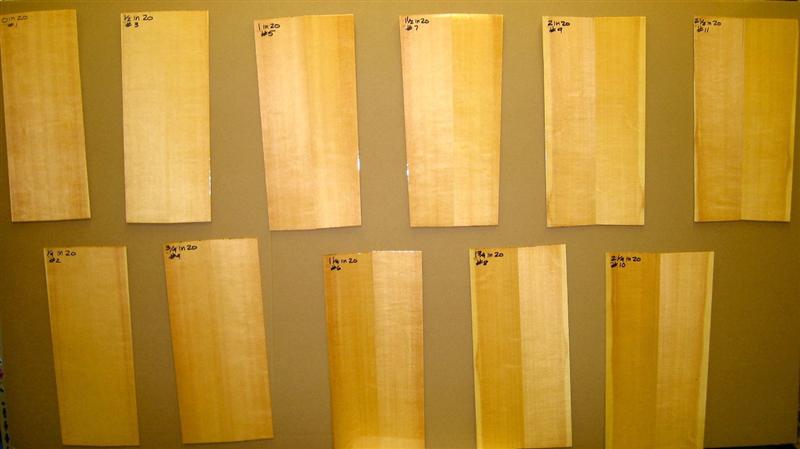
This is all well and good once you have a finish on the guitar but runout is quite hard to detect otherwise. This post from Craig Carter does remove some of the mystery however.
That now said, really I don't think it will matter that much which edge you joint, and this especially so on a small body guitar like a OO. Also the stiffness in the Adi itself will give you more than enough scope to work with either way.Craig Carter wrote: Detecting Runout
by Craig Carter
I thought I would submit the following information regarding detecting runout in soundboard blanks. Believe it or not, I did not figure this out until recently, when I milled the billets of fir. I went at the tree the way I usually do with redwood; that is, I bucked the log into rounds and then split the rounds into billets on the spot. I thought the wood split nicely, but the process was not quire as cushy as some of the better redwood I split. A few of the billets had a slight twist. These I noted, and when I milled them I aligned the billet with the saw so that the narrow grain, where the glue joint would be, was oriented so that there would be no run out there. Runout from the twist would be somewhere in the far reaches of the upper bout. Anyway, the point is that while I was stickering the cut blanks, some people were talking to me and I mixed up those sets with the regular sets. I couldn't really tell visually which were the twist sets and which were the regular ones. So after some heavy thinking and looking at offcuts, I came up with this way of seeing runout in the blanks. For all I know, everyone else already knows this, but Steve Henderson at Breedlove Guitars says "not true" and it was he who suggested that I send it in to you. Here are two common ways to detect runout:
1) Look for a difference in the darkness between the halves of a finished guitar top. Rising grain reflects grain differently than falling grain. If the top has runout one side will necessarily have rising grain and the other will have falling grain.
2) If the top is still in rough-sawn form, look for a difference in "fuzziness" between the front and back of the same piece of wood, or between different areas of the same side. This can be an indicator of gernal runout or localized short grain.
For the builder, the first method is kind of late, and the second ethod is kind of iffy.
ANOTHER WAY, if your blanks have a little width to spare, is to plane a 45 degree bevel along both long edges of one of the bookmatched halves. Now look at the planed edge from the side. Any runout or localized short grain will e obvious. I recommend planing BOTH edges, because if the billet had twist the resulting runout may appear in one edge and not the other. With very close grained wood, such as redwood or cedar it is enough to plane a very small bevel.
Hope this was somewhat helpful,
Cheers
Kim
- TimS
- ANZLF Approved Supplier
- Posts: 210
- Joined: Thu Sep 27, 2007 8:16 pm
- Location: Perth, Western Australia
- Contact:
Hi Mark,
I thought I would add a comment regarding Red Spruce (Adirondack) . In my limited experience red spruce grain count per inch is less critical given its superior strength. Some builders in fact look for wide even grain rather than the fine grain associated with master grade sets.
regards
Tim
I thought I would add a comment regarding Red Spruce (Adirondack) . In my limited experience red spruce grain count per inch is less critical given its superior strength. Some builders in fact look for wide even grain rather than the fine grain associated with master grade sets.
regards
Tim
[url]http://www.australiantonewoods.com[/url]
- DarwinStrings
- Blackwood
- Posts: 1873
- Joined: Thu Nov 13, 2008 10:27 pm
- Location: Darwin
Generally the slower a tree grows the stronger and more stable the wood is but it has been observed (plantations etc) that there are exception and for some species the opposite is true. Seems like nothing is concrete when it comes to wood.bob/TimS wrote: Bob
I think you'd have to assess each piece of wood on it's merits.
Some of the tighter grained Sitka I've used was like cardboard whereas the Red Spruce I've got is stiffer in the wide grained area of the board.
TimS
I thought I would add a comment regarding Red Spruce (Adirondack) . In my limited experience red spruce grain count per inch is less critical given its superior strength. Some builders in fact look for wide even grain rather than the fine grain associated with master grade sets.
Jim
- sebastiaan56
- Blackwood
- Posts: 1274
- Joined: Sun Oct 28, 2007 5:23 am
- Location: Blue Mountains
- Mark McLean
- Blackwood
- Posts: 1174
- Joined: Thu Apr 10, 2008 2:03 pm
- Location: Sydney
Thanks for the great contribution about runout, Kim. Personally, I don't mind seeing the difference in the two bookmatched halves of a soundboard, but I don't know if it has any implications for acoustic performance. I agree that tight grain hides the centre join better and that is an important consideration for fine grained timbers like cedar, sitka or european spruce species. I guess if you don't like the appearance of obvious grain lines you shouldn't choose Adirondack anyway. This has been a very informative discussion.
Mark
Mark
- DarwinStrings
- Blackwood
- Posts: 1873
- Joined: Thu Nov 13, 2008 10:27 pm
- Location: Darwin
Wood with runout is weaker, think of it this way...a extreme example of a piece of wood with runout is if you slice a piece of wood off the end of a length so that you have a piece that is 3mm thick but on its face all you can see is end grain, try snapping that compared to a piece 3mm thick from the same species that has been cleaved out along the grain.Mark McLean/Sebastiaan wrote: Mark McLean
Personally, I don't mind seeing the difference in the two bookmatched halves of a soundboard, but I don't know if it has any implications for acoustic performance.
Sebastian
One simple question, does run out affect the tone of an instrument?
This is why it is best to cleave out sound boards and braces. From this I think it is safe to assume you can thin a well cleaved board more than a board with bad run out. It doesnt mean you can't make a fine guitar with a soundboard that has runout though IMO.
Jim
- Bob Connor
- Admin
- Posts: 3115
- Joined: Mon Jul 09, 2007 9:43 pm
- Location: Geelong, Australia
- Contact:
Who is online
Users browsing this forum: No registered users and 149 guests