I’ve been tempted to stray from tradition in the one area I didn’t think I was ever likely to do so, the soundboard. I recently threw in an impulse bid on some King William Pine that Barry was selling on ebay and ended up getting it. I didn’t really have any plan for using it except for maybe as an interesting soundboard on a harp. But when I unwrapped it I was instantly enamoured by both the look and feel of it, so decided to glue on a couple of wings to get the width I need to and give it a go on the Huon pine flamenco I’m working on. The grain isn’t very straight but is well enough quartered on the main working part of the top so I’m not too concerned.
This got me to wondering how far you could go using less than well quartered top woods with the odd flaw (or fifty). I’m very tempted to use the offcuts from the more figured part of the boards on a little steel string.
The question is how much would it hurt the sound to do so???
Couple of pics… Top is half the top for the flamenco and below is the bit I’m thinking about using for a small steel string.
P.S. The strange little knots are totally sound and not much harder than the timber.
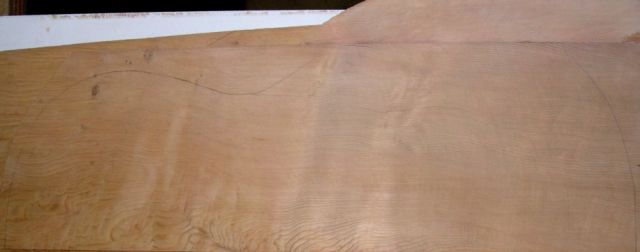
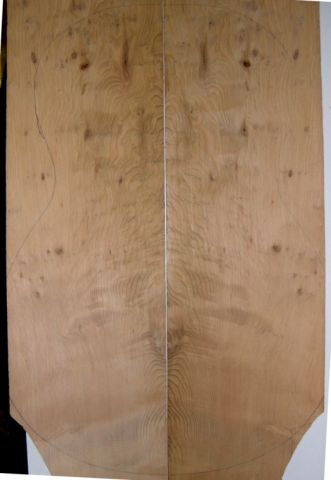