Graphite Required Urgently (A Graphite Discussion ;-)
Graphite Required Urgently (A Graphite Discussion ;-)
Folks,
I have a project on and need some graphite sheet stock suitable to laminate between spruce for braces ASAP, .020" is good .030"is better. I only need 1 bit about 300mm long x 1/2". If anyone has some local they would be willing to part with I will pay cash and postage or replace what ever is sent as I will be placing an order with Jim Watts @ Los Alamos Composites shortly http://www.jameswattsguitars.com/LAC.htm
I know Jim will ship pronto if I ask but I really would prefer not wait for shipping from USA if someone has some sitting spare here in AU.
Cheers
Kim
I have a project on and need some graphite sheet stock suitable to laminate between spruce for braces ASAP, .020" is good .030"is better. I only need 1 bit about 300mm long x 1/2". If anyone has some local they would be willing to part with I will pay cash and postage or replace what ever is sent as I will be placing an order with Jim Watts @ Los Alamos Composites shortly http://www.jameswattsguitars.com/LAC.htm
I know Jim will ship pronto if I ask but I really would prefer not wait for shipping from USA if someone has some sitting spare here in AU.
Cheers
Kim
Last edited by Kim on Wed May 06, 2009 7:12 pm, edited 1 time in total.
- John Maddison
- Blackwood
- Posts: 354
- Joined: Tue Jun 03, 2008 11:15 pm
- Location: Albany, Western Australia
- Contact:
- John Maddison
- Blackwood
- Posts: 354
- Joined: Tue Jun 03, 2008 11:15 pm
- Location: Albany, Western Australia
- Contact:
Re: Graphite Required Urgently
Kim, I woudnt mind seeing a tutorial at some stage on how you make up those braces.Kim wrote:Folks,
I have a project on and need some graphite sheet stock suitable to laminate between spruce for braces ASAP
Cheers Martin
I will only be doing the one brace on a beater Martin but will be taking some images this time round as in the end it certainly will be a different guitar to what I started out with.
Many thanks again to John, this is indeed what the ANZLF is all about, AU was a lonely place to be lute'in before this forum started up.
Cheers
Kim
Many thanks again to John, this is indeed what the ANZLF is all about, AU was a lonely place to be lute'in before this forum started up.
Cheers
Kim
- Dennis Leahy
- Blackwood
- Posts: 872
- Joined: Wed Oct 10, 2007 12:32 am
- Location: Duluth, MN, US
- Contact:
John, thanks for the link to the Composites Store. I had a look around the site...
Kim, I'm guessing this would be for composite bracing, which is something I have started to investigate.
This may not be a great place (in your "urgently needed" thread) to discuss this, but it appears that there are at least three variations on how carbon fibers are laid up in sheet form: unidirectional, each layer at 90°, and each layer at 45°. Some seem to be designed to handle shear (and possibly compression) loads (unidirectional fibers.) I would think that for something like a rectangular rod to go into a neck to prevent bowing, that the ideal would be to use material that was not unidirectional, to provide maximum stiffness and not even worry about shear or compression.
And that leads me to the thin sheet used in a sandwich in braces. Different luthiers may have different engineering ideas about CF laminated braces, but for me, the ideal would be a brace that was shaped into a 25 foot radius would permanently hold that radius. So, I would think the least unidirectional fibers the better, so that the 45° web design in John's link should outperform the 90° fibers in this carbon plate (half of which would be unidirectional.)
I note that Los Alamos Composites mentions on their site that their products (rod and sheet) employ all unidirectional fibers. Again, to me, that does not seem ideal for neck reinforcement, so it must be true that when enough unidirectional fibers are laid up (actually, I think the fibers are unidirectional because they are extruded/'pultruded' and are not really laid-up), the rods get plenty stiff enough to do the job. But, wouldn't the ideal be bias web sheets, cut into rectangular rods?
Sorry if this seems rambling, but I do think that at least theoretically, the bias web designed sheets that John linked to make the most sense to me, as the CF I would want in laminated braces.
Thanks, John! And David Hurd!
Dennis
Kim, I'm guessing this would be for composite bracing, which is something I have started to investigate.
This may not be a great place (in your "urgently needed" thread) to discuss this, but it appears that there are at least three variations on how carbon fibers are laid up in sheet form: unidirectional, each layer at 90°, and each layer at 45°. Some seem to be designed to handle shear (and possibly compression) loads (unidirectional fibers.) I would think that for something like a rectangular rod to go into a neck to prevent bowing, that the ideal would be to use material that was not unidirectional, to provide maximum stiffness and not even worry about shear or compression.
And that leads me to the thin sheet used in a sandwich in braces. Different luthiers may have different engineering ideas about CF laminated braces, but for me, the ideal would be a brace that was shaped into a 25 foot radius would permanently hold that radius. So, I would think the least unidirectional fibers the better, so that the 45° web design in John's link should outperform the 90° fibers in this carbon plate (half of which would be unidirectional.)
I note that Los Alamos Composites mentions on their site that their products (rod and sheet) employ all unidirectional fibers. Again, to me, that does not seem ideal for neck reinforcement, so it must be true that when enough unidirectional fibers are laid up (actually, I think the fibers are unidirectional because they are extruded/'pultruded' and are not really laid-up), the rods get plenty stiff enough to do the job. But, wouldn't the ideal be bias web sheets, cut into rectangular rods?
Sorry if this seems rambling, but I do think that at least theoretically, the bias web designed sheets that John linked to make the most sense to me, as the CF I would want in laminated braces.
Thanks, John! And David Hurd!
Dennis
Another damn Yank!
- John Maddison
- Blackwood
- Posts: 354
- Joined: Tue Jun 03, 2008 11:15 pm
- Location: Albany, Western Australia
- Contact:
- hilo_kawika
- Blackwood
- Posts: 144
- Joined: Mon Oct 13, 2008 10:29 am
- Location: Hilo, Hawaii
- Contact:
Aloha Dennis,
I'm a big fan of the 45 degree layed up sheets for bridge plates. I think I had a brief tutorial about it here somewhere. And I agree that using it flat or on edge would be quite useful - especially on edge where the fibers would always be in tension. And the folks at the composites store have always been good to deal with as well.
When I built my 18' long fishing boat using the stitch-n-glue method I used a triple overlap of biaxial woven roving on each seam inside and out for the same reason - fibers would always be in tension during any possible flexing. The boat's pretty stiff I must say. Here I am at the helm with a friend along for fishing yesterday:
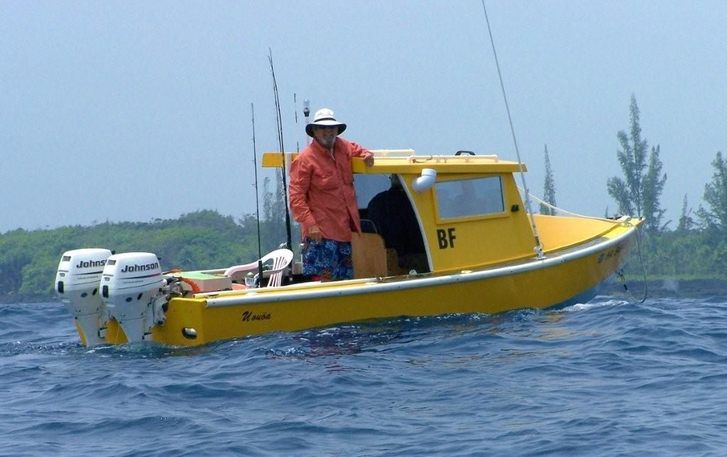
aloha,
Dave Hurd
http://www.ukuleles.com
I'm a big fan of the 45 degree layed up sheets for bridge plates. I think I had a brief tutorial about it here somewhere. And I agree that using it flat or on edge would be quite useful - especially on edge where the fibers would always be in tension. And the folks at the composites store have always been good to deal with as well.
When I built my 18' long fishing boat using the stitch-n-glue method I used a triple overlap of biaxial woven roving on each seam inside and out for the same reason - fibers would always be in tension during any possible flexing. The boat's pretty stiff I must say. Here I am at the helm with a friend along for fishing yesterday:
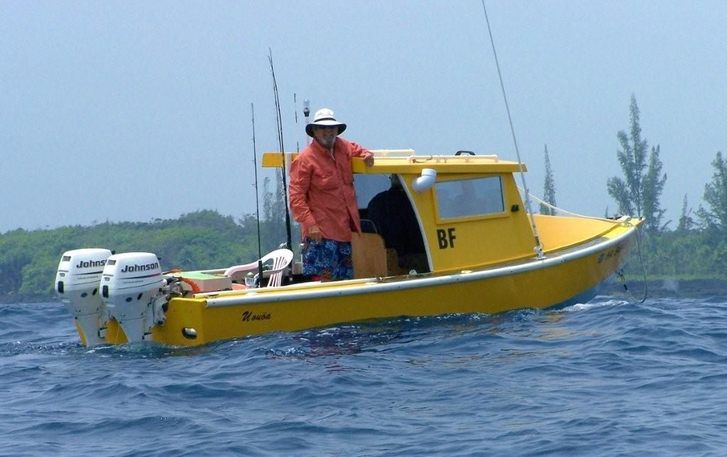
aloha,
Dave Hurd
http://www.ukuleles.com
How to become a millionaire? Start with $2 million and become a luthier...
- John Maddison
- Blackwood
- Posts: 354
- Joined: Tue Jun 03, 2008 11:15 pm
- Location: Albany, Western Australia
- Contact:
- Mike Thomas
- Blackwood
- Posts: 228
- Joined: Fri Jan 30, 2009 1:34 pm
- Location: Adelaide
Dennis, as I understand it, unidirectional carbon provides maximum resistance to bending along its length i.e. a carbon rod used as neck reinforcement needs to be unidirectional since the main force being countered is the tension of the strings. And because carbon works most effectively in tension. the rod needs to be inset into the neck as far away from the strings as possible i.e inset as deeply as possible. If however the force to be resisted is torsional i.e. a twisting force, then 45 degree woven carbon is what you need. Or even better two layers of unidirectional carbon laminated at 45 degrees to each other.
Mike Thomas
"There are some enterprises in which a careful disorderliness is the true method"
"There are some enterprises in which a careful disorderliness is the true method"
Most kind of you to offer Jeff however I believe John already has some .020" in the mail which should do the trick. I will use two layers as part of a 5 ply layup. The 2mm would have been very good though and I really do appreciate your most generous offer.jeffhigh wrote:Kim,
I have a length of 12mm x2mm that I could cut you off 300mm no problems
Let me know.
Must confess that I did not give too much thought to unidirectional v 45° woven and orientation, I just need a very strong upper transverse brace on this one because it will be required to support the butt end of a heelless neck which will be let into the brace by about 3mm (yes I know? but that's just how it is this time

Anyhow, thanks everyone for the input and please do continue this conversation re unidirectional v 45° web. The more clarity the better so please feel free to elaborate if you have thoughts or experience with CF.
Cheers
Kim
Kim , in the situation you are describing I would do a horizontal lamination rather than vertical for strength.
From guitar top inwards
3mm spruce ( to accomodate the neck inset)
CF (full width not notched
12mm spruce
CF full width
A capped brace is much stronger than a vertically laminated one for the same volume.
From guitar top inwards
3mm spruce ( to accomodate the neck inset)
CF (full width not notched
12mm spruce
CF full width
A capped brace is much stronger than a vertically laminated one for the same volume.
Hi All
I'm not sure how the price stacks up with having CF sent from the US (seems to me that US postage charges have gone up lately), but I recently got a couple of lengths of 5mm solid CF rod from a Brisbane supplier. A 1m length was $15.75 and while they don't have a huge range, they have a number of shapes and sizes that may be of use in guitar building.
This is the link to the CF on their site, also worth checking out their other stuff if you are after bearings or CA glue http://www.hobbyparts.com.au/store/cate ... bon+fibre/
Cheers
James
I'm not sure how the price stacks up with having CF sent from the US (seems to me that US postage charges have gone up lately), but I recently got a couple of lengths of 5mm solid CF rod from a Brisbane supplier. A 1m length was $15.75 and while they don't have a huge range, they have a number of shapes and sizes that may be of use in guitar building.
This is the link to the CF on their site, also worth checking out their other stuff if you are after bearings or CA glue http://www.hobbyparts.com.au/store/cate ... bon+fibre/
Cheers
James
- hilo_kawika
- Blackwood
- Posts: 144
- Joined: Mon Oct 13, 2008 10:29 am
- Location: Hilo, Hawaii
- Contact:
It's often useful to actually do simple deflection or vibration testing of the CF material to determine how stiff the material really is. When I started using CF in ukulele necks about 8-9 years ago I'd ask suppliers how stiff their CF was. Usually the answer was something like: " Wow, man, I mean like it's reely, reely, stiff man".
Deflection testing on my part usually came up with a number on the order of 10 million psi, clearly not space station grade which I believe is ~6-8 times higher. In any case it turns out that regular aluminum bar has the same stiffness and is only a little more dense.
I'm not suggesting that aluminum be used in brace lamination situations, but it may well be useful for neck stiffening, at least for ukuleles. Simple testing procedures will allow you to make such decisions in a more rational manner.
aloha,
Dave Hurd
http://www.ukuleles.com
Deflection testing on my part usually came up with a number on the order of 10 million psi, clearly not space station grade which I believe is ~6-8 times higher. In any case it turns out that regular aluminum bar has the same stiffness and is only a little more dense.
I'm not suggesting that aluminum be used in brace lamination situations, but it may well be useful for neck stiffening, at least for ukuleles. Simple testing procedures will allow you to make such decisions in a more rational manner.
aloha,
Dave Hurd
http://www.ukuleles.com
How to become a millionaire? Start with $2 million and become a luthier...
- Dennis Leahy
- Blackwood
- Posts: 872
- Joined: Wed Oct 10, 2007 12:32 am
- Location: Duluth, MN, US
- Contact:
Hi David,hilo_kawika wrote:... it turns out that regular aluminum bar has the same stiffness and is only a little more dense.
...aluminum ... may well be useful for neck stiffening, at least for ukuleles.
aloha,
Dave Hurd
http://www.ukuleles.com
Will aluminum eventually take on a "memory" of the bend, and thus lose some of the desired characteristic? CF has a reputation (I don't know if it is justified or mythical) to return completely to the original shape after deflection.
Just wondering aloud.
Dennis
Another damn Yank!
- hilo_kawika
- Blackwood
- Posts: 144
- Joined: Mon Oct 13, 2008 10:29 am
- Location: Hilo, Hawaii
- Contact:
Hi Dennis,
I think you've asked a great question. Here's a reference to a brief article dealing with metal creep as a function of temperature:
http://www.tech.plym.ac.uk/sme/mats340/cpintro.pdf
Aluminum Melting Point: 660.37 °C (933.52 K, 1220.666 °F), so from the article 0.5 x melting point ( K ) would give ~165-170 °C - somewhat hotter than I would like to have a guitar or ukulele neck. So I think aluminum would be o.k. with respect to creep issues at least for the practical lifetime of the instrument and the stresses involved. Ah, for access to a materials testing lab...
aloha,
Dave Hurd
http://www.ukuleles.com
I think you've asked a great question. Here's a reference to a brief article dealing with metal creep as a function of temperature:
http://www.tech.plym.ac.uk/sme/mats340/cpintro.pdf
Aluminum Melting Point: 660.37 °C (933.52 K, 1220.666 °F), so from the article 0.5 x melting point ( K ) would give ~165-170 °C - somewhat hotter than I would like to have a guitar or ukulele neck. So I think aluminum would be o.k. with respect to creep issues at least for the practical lifetime of the instrument and the stresses involved. Ah, for access to a materials testing lab...
aloha,
Dave Hurd
http://www.ukuleles.com
How to become a millionaire? Start with $2 million and become a luthier...
- Dennis Leahy
- Blackwood
- Posts: 872
- Joined: Wed Oct 10, 2007 12:32 am
- Location: Duluth, MN, US
- Contact:
Yeah, but if I play Superman, and simply take the rectangular rod in my mighty hands, it will bend (without even using my heat vision.) And, once I let go, it might spring back a bit, but I'd never get it straight again. That's the kind of memory I'm speaking about.hilo_kawika wrote:Hi Dennis,
I think you've asked a great question. Here's a reference to a brief article dealing with metal creep as a function of temperature:
http://www.tech.plym.ac.uk/sme/mats340/cpintro.pdf
Aluminum Melting Point: 660.37 °C (933.52 K, 1220.666 °F), so from the article 0.5 x melting point ( K ) would give ~165-170 °C - somewhat hotter than I would like to have a guitar or ukulele neck. So I think aluminum would be o.k. with respect to creep issues at least for the practical lifetime of the instrument and the stresses involved. Ah, for access to a materials testing lab...
aloha,
Dave Hurd
http://www.ukuleles.com
Dennis
Another damn Yank!
Dennis,
Aly's aint Aly's depends what it is alloyed with and can give huge increases in strength over plan aluminium.
Been a while since I worked as an engineer and steel was more familiar to me but I will try to explain.
Most metals, including steel and aluminium have both a yeild strength(or elastic limit) and an ultimate tensile strength (where it breaks)
This is a separate property to it's stiffness which is how much it deflects for a given load.
Deflect an object within it's elastic limit and it will return to original. Deflect it past this point and it will deform permanantly.
Steel and aluminium generally have a large gap between yeild and failure which I suspect CF does not.
In your example you have taken the aluminium bar past its yeild point so it has permanantly deformed. To get it to that point though you have probably deflected it much more than would ever be acheived in service ( if designed properly)
I
Aly's aint Aly's depends what it is alloyed with and can give huge increases in strength over plan aluminium.
Been a while since I worked as an engineer and steel was more familiar to me but I will try to explain.
Most metals, including steel and aluminium have both a yeild strength(or elastic limit) and an ultimate tensile strength (where it breaks)
This is a separate property to it's stiffness which is how much it deflects for a given load.
Deflect an object within it's elastic limit and it will return to original. Deflect it past this point and it will deform permanantly.
Steel and aluminium generally have a large gap between yeild and failure which I suspect CF does not.
In your example you have taken the aluminium bar past its yeild point so it has permanantly deformed. To get it to that point though you have probably deflected it much more than would ever be acheived in service ( if designed properly)
I
- Mike Thomas
- Blackwood
- Posts: 228
- Joined: Fri Jan 30, 2009 1:34 pm
- Location: Adelaide
Selmer Maccaferri guitars (i.e. the grande bouche steel string) made in the early 1930's, had necks reinforced with four 12mmx2mm dural bars. Dural is a hard alloy of aluminium with copper, manganese, and magnesium, and was used in the aircraft industry at the time. Apparently, those necks were very stable. According to Wikipedia, the modern aluminium equivalent of Dural (a trade name), is AA 2024.
Mike Thomas
"There are some enterprises in which a careful disorderliness is the true method"
"There are some enterprises in which a careful disorderliness is the true method"
- Dennis Leahy
- Blackwood
- Posts: 872
- Joined: Wed Oct 10, 2007 12:32 am
- Location: Duluth, MN, US
- Contact:
OK, Thanks, Jeff. That makes perfect sense.
Dennis
p.s. BTW, I just ordered some CF round tubes for my next two guitars (neck block to tail block "suspended bracing"), as well as 45° Carbon Shear Web for brace lamination from The Composites Store. Thanks again to David via John , spurred by Kim.
Dennis
p.s. BTW, I just ordered some CF round tubes for my next two guitars (neck block to tail block "suspended bracing"), as well as 45° Carbon Shear Web for brace lamination from The Composites Store. Thanks again to David via John , spurred by Kim.

Another damn Yank!
Who is online
Users browsing this forum: No registered users and 105 guests