ANZLF Adjustable Neck Joint Group Discussion
-
- Blackwood
- Posts: 311
- Joined: Sun Jan 13, 2008 10:22 am
- Location: Santa Cruz, Ca.
- Contact:
One other comment on guitar weight...
If anyone knows about how good some heavy guitars can be, it should be you Aussies! Two names: Greg Smallman and Jim Redgate...
The classical guitar lutherie world has learned a lot, as traditionally bound as their aesthetics may remain. One of the things they've learned is how to make guitars project without amplification. By not being afraid to add stiffness and mass to some parts of the guitar...sides, back, and yes, neck...luthiers like Smallman and Redgate have leaped ahead of most steel string makers in getting more out of so little.
If anyone knows about how good some heavy guitars can be, it should be you Aussies! Two names: Greg Smallman and Jim Redgate...
The classical guitar lutherie world has learned a lot, as traditionally bound as their aesthetics may remain. One of the things they've learned is how to make guitars project without amplification. By not being afraid to add stiffness and mass to some parts of the guitar...sides, back, and yes, neck...luthiers like Smallman and Redgate have leaped ahead of most steel string makers in getting more out of so little.
Rick Turner
Guitar Maker, Experimenter, Diviner
www.renaissanceguitars.com
www.d-tar.com
Guitar Maker, Experimenter, Diviner
www.renaissanceguitars.com
www.d-tar.com
Hi All
Sorry I haven’t been more engaged in this thread… Things are going from bad to worse with Garrett as minister so I’m up to my ears in work stuff.
My interest runs mostly towards classical and flamenco guitars and I keep coming back to swapping out the saddle to adjust the hight if needed. The reason for this is mostly what old Vic drummed into me about neck joints in the little formal training I was lucky enough to have received. He stressed to me over and over the importance of a good connection between the neck, body and soundboard. His view was that the neck made a small but important contribution to the sound of the guitar and if the neck didn’t have a good connection to the body then you lost that part of the package and the guitar could never reach the full potential of the timbers it had been constructed from (epoxy glue was a big no no).
He demonstrated this to me by giving me a stethoscope and having me listen to the sound on the neck, top of the soundboard and side next to the heal while he played his personal guitar. He then had me do it again while he played a cheap no brand guitar with a bad neck joint. The difference in the amount of sound and vibration in the upper body of his guitar was remarkable. The difference between a classical and a steel string is like comparing a small 3 cylinder to a V8. With a classical you have to eek out every bit of performance you can from the underpowered nylon strings.
That said, I will be building a steel string and like the concept of an adjustable neck so I’m still following this thread with interest and still tampering with ideas.
Tom… I played with the idea of a scissor jack type set-up, but it had too many pivot points (failure points) for my liking. The concept was to make a mini scissor jack (like the car jack) and attach it between the neck and body. The problem is making something like this small enough to fit in the space we have to play with while being strong enough to pull or push over 300 kg (the 80kg string tension is at the long end of the lever about 360mm from the pivot point. We’re trying to pull against this at a point 80mm from the pivot so leverage is against us).
Rather than give up, I took the concept and dumbed it down to make it simpler and more robust. What I ended up with was a truss rod like set-up, a captured bolt in a u bracket so that when you turn the bolt it compresses the bracket causing the back to bow. Fit the neck to the guitar then screw in the grub screw from the neck block so it picks up the threads in the back of the u bracket then lock it in place with a lock nut. When you turn the bolt in the u bracket the back of the bracket will bow outwards forcing the heel of the guitar away from the body. I came up with a number of compression fittings that would do the same thing but this is the only one I got around to doing drawing for.
Food for thought
James
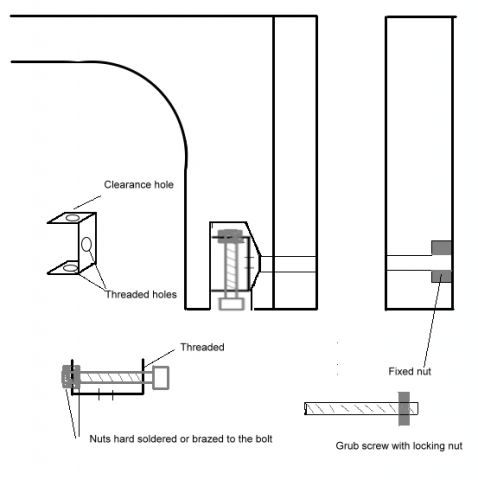
Sorry I haven’t been more engaged in this thread… Things are going from bad to worse with Garrett as minister so I’m up to my ears in work stuff.
My interest runs mostly towards classical and flamenco guitars and I keep coming back to swapping out the saddle to adjust the hight if needed. The reason for this is mostly what old Vic drummed into me about neck joints in the little formal training I was lucky enough to have received. He stressed to me over and over the importance of a good connection between the neck, body and soundboard. His view was that the neck made a small but important contribution to the sound of the guitar and if the neck didn’t have a good connection to the body then you lost that part of the package and the guitar could never reach the full potential of the timbers it had been constructed from (epoxy glue was a big no no).
He demonstrated this to me by giving me a stethoscope and having me listen to the sound on the neck, top of the soundboard and side next to the heal while he played his personal guitar. He then had me do it again while he played a cheap no brand guitar with a bad neck joint. The difference in the amount of sound and vibration in the upper body of his guitar was remarkable. The difference between a classical and a steel string is like comparing a small 3 cylinder to a V8. With a classical you have to eek out every bit of performance you can from the underpowered nylon strings.
That said, I will be building a steel string and like the concept of an adjustable neck so I’m still following this thread with interest and still tampering with ideas.
Tom… I played with the idea of a scissor jack type set-up, but it had too many pivot points (failure points) for my liking. The concept was to make a mini scissor jack (like the car jack) and attach it between the neck and body. The problem is making something like this small enough to fit in the space we have to play with while being strong enough to pull or push over 300 kg (the 80kg string tension is at the long end of the lever about 360mm from the pivot point. We’re trying to pull against this at a point 80mm from the pivot so leverage is against us).
Rather than give up, I took the concept and dumbed it down to make it simpler and more robust. What I ended up with was a truss rod like set-up, a captured bolt in a u bracket so that when you turn the bolt it compresses the bracket causing the back to bow. Fit the neck to the guitar then screw in the grub screw from the neck block so it picks up the threads in the back of the u bracket then lock it in place with a lock nut. When you turn the bolt in the u bracket the back of the bracket will bow outwards forcing the heel of the guitar away from the body. I came up with a number of compression fittings that would do the same thing but this is the only one I got around to doing drawing for.
Food for thought
James
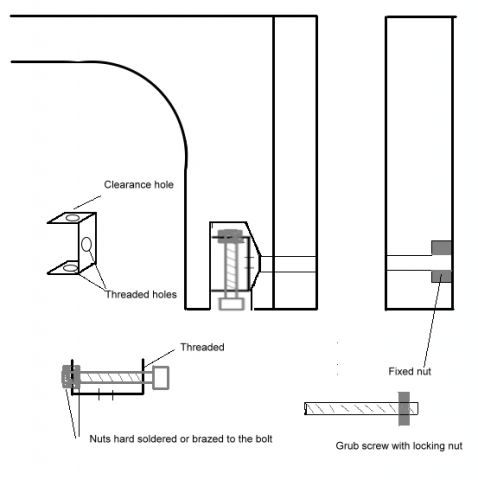
James,
In one of the recent-ish GAL journals, Mike Doolin discusses his neck joint and in a seminar mentions that a blind tester of his classical with adjustable neck could not tell the difference between a classical with tradional neck joint. From memory, I think he takes a question from the floor and discusses this point.
Dom
In one of the recent-ish GAL journals, Mike Doolin discusses his neck joint and in a seminar mentions that a blind tester of his classical with adjustable neck could not tell the difference between a classical with tradional neck joint. From memory, I think he takes a question from the floor and discusses this point.
Dom
- Dave White
- Blackwood
- Posts: 452
- Joined: Mon Nov 12, 2007 3:10 am
- Location: Hughenden Valley, England
- Contact:
James,James Mc wrote:
He demonstrated this to me by giving me a stethoscope and having me listen to the sound on the neck, top of the soundboard and side next to the heal while he played his personal guitar. He then had me do it again while he played a cheap no brand guitar with a bad neck joint. The difference in the amount of sound and vibration in the upper body of his guitar was remarkable.
So that was the only difference between the two guitars then? Make a new neck for the no brand guitar with a perfect fit and re do the stethoscope test and what do you think would have happened compared with the hand made guitar?
Sorry to sound so harsh but I think the solid neck contact impact on sound thing is way overdone. I've said this before about steel strings but suspect it's true about nylon as well - when we get "Star Trek" technology and can firmly "attatch" a neck to a body using a force that means it doesn't touch the body at all (electro magnetic?) with just a small air gap, and concentrate on bracing the box for maximum delivery of the strings energy and tonal shaping then the guitar will sound amazing.
Interesting design - there was a classical guitar with adjustable neck joint posted on the MIMF a little while back.
Dave White
[url=http://www.defaoiteguitars.com]De Faoite Stringed Instruments[/url]
[url=http://www.defaoiteguitars.com]De Faoite Stringed Instruments[/url]
- Tom Morici
- Blackwood
- Posts: 103
- Joined: Thu Nov 01, 2007 5:46 pm
- Location: Montana, USA
- Contact:
Craig,
In response to your last comment to me in regards to the 3/8" steel rod
in the neck heel. (Rick's design) I thought of the weight first and the tooling to accurately drill and tap those holes second.
I was trained as a machinist in my early teenage years, so drilling and tapping the holes is easy for me. Tooling helps. Most luthiers are more
woodworkers than metalworkers.
Your brass ferrule that you made on a drill press shows you can do this
type of metalwork.
I still feel you have stayed on track to keep this a simple as possible,
using as many common parts as possible allows everyone to build the design. Having someone with a lathe to make the ferrule, adds to the simplicity for those that don't care to make there own parts.
So far so good.
James,
I find your simple adjuster clever, Im sure it is obvious the hole to mount
it as shown would be tricky. I do find it "food for thought" and it did give
me an idea of a cam style adjuster. I think it would be cool to have the adjustment screw accessed in the heel cap. Thanks for the input.
I think the necks role in tone as more of a substain factor, I view vibration
in the neck as an energy loss. If the neck adds to tone, in most case I find
it amplifys certain notes and mutes others. CF bars installed in the neck help to balance the tone. At least that is what I have noticed.
Tom
In response to your last comment to me in regards to the 3/8" steel rod
in the neck heel. (Rick's design) I thought of the weight first and the tooling to accurately drill and tap those holes second.
I was trained as a machinist in my early teenage years, so drilling and tapping the holes is easy for me. Tooling helps. Most luthiers are more
woodworkers than metalworkers.
Your brass ferrule that you made on a drill press shows you can do this
type of metalwork.
I still feel you have stayed on track to keep this a simple as possible,
using as many common parts as possible allows everyone to build the design. Having someone with a lathe to make the ferrule, adds to the simplicity for those that don't care to make there own parts.
So far so good.
James,
I find your simple adjuster clever, Im sure it is obvious the hole to mount
it as shown would be tricky. I do find it "food for thought" and it did give
me an idea of a cam style adjuster. I think it would be cool to have the adjustment screw accessed in the heel cap. Thanks for the input.
I think the necks role in tone as more of a substain factor, I view vibration
in the neck as an energy loss. If the neck adds to tone, in most case I find
it amplifys certain notes and mutes others. CF bars installed in the neck help to balance the tone. At least that is what I have noticed.
Tom
-
- Blackwood
- Posts: 311
- Joined: Sun Jan 13, 2008 10:22 am
- Location: Santa Cruz, Ca.
- Contact:
This neck joint thing is so fraught with myth and "old wives' tales" it isn't funny anymore. Nobody who has played a 100 year old Howe Orme believes all the malarky anymore about dovetails and lot's of surface contact and all that. The guitars blow away practically any instrument of that vintage with three tiny points of contact between neck and body. That's what I learned in my earliest years as a luthier. I also learned to pay attention to the guitars, not necessarily those who talked about them who may have good hands but a poor understanding of the physics of sound production.
Too many luthiers get all up in their heads about this stuff. They talk and write and ponder and never get down to really experiencing what's going on.
I don't even want to make steel string acoustic guitars with non-adjustable neck joints anymore. I don't see any advantage to a set neck design other than to perhaps overcome a minority objection to seeing hardware...and that comes mostly from luthiers who are the last people on earth likely to be my clients. And for those folks, there are a ton of options other than me.
Too many luthiers get all up in their heads about this stuff. They talk and write and ponder and never get down to really experiencing what's going on.
I don't even want to make steel string acoustic guitars with non-adjustable neck joints anymore. I don't see any advantage to a set neck design other than to perhaps overcome a minority objection to seeing hardware...and that comes mostly from luthiers who are the last people on earth likely to be my clients. And for those folks, there are a ton of options other than me.
Rick Turner
Guitar Maker, Experimenter, Diviner
www.renaissanceguitars.com
www.d-tar.com
Guitar Maker, Experimenter, Diviner
www.renaissanceguitars.com
www.d-tar.com
- Tom Morici
- Blackwood
- Posts: 103
- Joined: Thu Nov 01, 2007 5:46 pm
- Location: Montana, USA
- Contact:
Rick,
Let me start by saying I have a respect for your contributions.
I admit I am biased, I am in my 39th year and "cut my teeth" as a
repairman. Handling vintage builds may be the best education a luthier
may ever have. I did reach a level of respect that by the 80's I would only accept vintage builds brought to my shop. By choice I ran a non-public shop my clients where dealers and collectors of vintage instruments
We differ in many respects, your exposure in the luthiery community, is far beyound anything I would ever aspire to. It does surprise me that
when I play "man on the street" and ask countless guitar players if they have heard of Rick Turner, the answer for the most part has been no.
When I ask luthiers the same question, the answer for the most part has been yes. This is my personal experience.
When I read the threads in instrument forums, I tend to accept your input
as experience based. You have been there done that, and respect your opinon as having a value that should never be ignored.
Your neck adjustment system may be the best method that there is, but
once we accept that there is only one, we lose the ability to grow.
I feel that education should only end when we are laid to rest.
Let the ideas flow, even you with your vast knowledge and experience
may learn something.
I will say again, I do have the deepest respect for your experienced input,
and am glad that you do take the time to share that with others.
Most builders with your experience don't.
Thank You!
Tom
Let me start by saying I have a respect for your contributions.
I admit I am biased, I am in my 39th year and "cut my teeth" as a
repairman. Handling vintage builds may be the best education a luthier
may ever have. I did reach a level of respect that by the 80's I would only accept vintage builds brought to my shop. By choice I ran a non-public shop my clients where dealers and collectors of vintage instruments
We differ in many respects, your exposure in the luthiery community, is far beyound anything I would ever aspire to. It does surprise me that
when I play "man on the street" and ask countless guitar players if they have heard of Rick Turner, the answer for the most part has been no.
When I ask luthiers the same question, the answer for the most part has been yes. This is my personal experience.
When I read the threads in instrument forums, I tend to accept your input
as experience based. You have been there done that, and respect your opinon as having a value that should never be ignored.
Your neck adjustment system may be the best method that there is, but
once we accept that there is only one, we lose the ability to grow.
I feel that education should only end when we are laid to rest.
Let the ideas flow, even you with your vast knowledge and experience
may learn something.
I will say again, I do have the deepest respect for your experienced input,
and am glad that you do take the time to share that with others.
Most builders with your experience don't.
Thank You!
Tom
-
- Blackwood
- Posts: 311
- Joined: Sun Jan 13, 2008 10:22 am
- Location: Santa Cruz, Ca.
- Contact:
Mine is not necessarily the best, but it works; it's easy; and it's got a long, long track record behind it...not my own track record, by the way, I speaking of the Howe Orme guitars I love so much which, for their day, were a step above and beyond the Martins of that era (OK, just my opinion!). My own design work is hugely influenced by my repair experience. I try to make guitars that are easy to adjust in every way necessary for guitar players, have features that will hopefully greatly reduce or postpone many of the stress related repairs I've dealt with over the years, and of course sound good. There are some basic weaknesses with the way guitars...especially steel string guitars...are made. We can move forward and design past these weaknesses that weren't even known of when the bulk of the early steel string guitars were made. We have a huge advantage in seeing how these guitars change over the course of 50 to 75 years, and not all the changes are for the better. We have some absolutely wonderful materials to work with now that are very complementary to wood, and the main of these are the carbon fiber composites that are like wood you can design yourself.
I personally do not see any point in pretending that we are stuck in 1933 and are trying to make the next perfect Golden Era Martins. There are plenty of folks doing that...Borges, TJ Thompson, Huss and Dalton, SCGC, Collings, and yes, even CF Martin. So I'm an advocate of not hiding anything if doing so reduces it's ease of use and effectiveness. I want to make great musical tools.
As for my own professional reputation, yeah, I'm kind of a cult-known luthier. Because much of my earlier work was under a different name than my own, and because I've jumped around from one type of instrument to another, dabbling in electronics, electrics, basses, acoustics, ukes, etc. along the way, it is luthiers who tend to come across my ramblings more than players.
Thanks for putting up with me here...with more and more of my future bound to my love of a Tassie girl, I'll earn the right to be here on this forum!
I personally do not see any point in pretending that we are stuck in 1933 and are trying to make the next perfect Golden Era Martins. There are plenty of folks doing that...Borges, TJ Thompson, Huss and Dalton, SCGC, Collings, and yes, even CF Martin. So I'm an advocate of not hiding anything if doing so reduces it's ease of use and effectiveness. I want to make great musical tools.
As for my own professional reputation, yeah, I'm kind of a cult-known luthier. Because much of my earlier work was under a different name than my own, and because I've jumped around from one type of instrument to another, dabbling in electronics, electrics, basses, acoustics, ukes, etc. along the way, it is luthiers who tend to come across my ramblings more than players.
Thanks for putting up with me here...with more and more of my future bound to my love of a Tassie girl, I'll earn the right to be here on this forum!
Rick Turner
Guitar Maker, Experimenter, Diviner
www.renaissanceguitars.com
www.d-tar.com
Guitar Maker, Experimenter, Diviner
www.renaissanceguitars.com
www.d-tar.com
-
- Blackwood
- Posts: 311
- Joined: Sun Jan 13, 2008 10:22 am
- Location: Santa Cruz, Ca.
- Contact:
Aside from her, what I have to watch out for is the products of the Lark Distillery in Hobart! Lou plays there practically every Friday evening with one of her bands, Coyote Serenade. I'll be there Friday the 11th, by the way, so if any of you happen to be in the neighborhood, pop on in.
Rick Turner
Guitar Maker, Experimenter, Diviner
www.renaissanceguitars.com
www.d-tar.com
Guitar Maker, Experimenter, Diviner
www.renaissanceguitars.com
www.d-tar.com
G'day Rick,
Try as I might , I 'm having touble understanding your idea posted previously, regarding losing the upper bolt.
If I'm understanding you correctly ( and I'm pretty sure I'm not ) you have the yaw/intonation screws adjustable externally.
I'm thinking these two screws to be seldom ,if ever adjusted once the guitar has had final setup, so would be quite happy for these adjustments to be made from within the guitar and leave the outside of the heel with minimalist interuption by way of adjustment screws. As I say ,I've probably got this all wrong .
Could you explain it a little clearer so that we can understand and see it clearly . A little plan would be very helpful.
Cheers , Craig
Try as I might , I 'm having touble understanding your idea posted previously, regarding losing the upper bolt.
If I'm understanding you correctly ( and I'm pretty sure I'm not ) you have the yaw/intonation screws adjustable externally.
I'm thinking these two screws to be seldom ,if ever adjusted once the guitar has had final setup, so would be quite happy for these adjustments to be made from within the guitar and leave the outside of the heel with minimalist interuption by way of adjustment screws. As I say ,I've probably got this all wrong .
Could you explain it a little clearer so that we can understand and see it clearly . A little plan would be very helpful.
Cheers , Craig
-
- Blackwood
- Posts: 311
- Joined: Sun Jan 13, 2008 10:22 am
- Location: Santa Cruz, Ca.
- Contact:
The "yaw/intonation" screws thread into inserts in the face of the heel below the fingerboard, and they're counterbored (spot faced) into the heel face to minimize the gap. The faces of the head bear against the upper side outside the neck block and right below the binding. I'll be inlaying a metal bearing plate at that point. So with one on each side of the heel, they become the pivot points and the yaw and intonation adjusters, totally accessible from the outside of the instrument. This is practically pure Howe-Orme here in function and access. The difference is that I do not use these for tilt adjustment, but rather use the cap screw going through the steel dowel in the heel which goes into the brass shouldered insert in the neck block. The Howe-Ormes have a fixed pin hinge-like arrangement at the heel cap that locks the heel cap to the guitar body; that does not allow overall in and out movement of the neck.
I'm a guy who doesn't even like through-the-sound-hole truss rod adjustment. I've got too many years at the repair bench dealing with crap that just makes working on instruments difficult. I like as much as possible to be accessible to the client or future luthier from the outside of the instrument and without requiring any loosening of strings to see exactly what the adjustments are doing. To me this is as basic as wanting access to sparkplugs on a car engine...without needing special tools. I've heard of exotic cars where you practically have to take the engine out to change plugs. Yeah, beautiful lines and a $5,000.00 tuneup...
I'm a guy who doesn't even like through-the-sound-hole truss rod adjustment. I've got too many years at the repair bench dealing with crap that just makes working on instruments difficult. I like as much as possible to be accessible to the client or future luthier from the outside of the instrument and without requiring any loosening of strings to see exactly what the adjustments are doing. To me this is as basic as wanting access to sparkplugs on a car engine...without needing special tools. I've heard of exotic cars where you practically have to take the engine out to change plugs. Yeah, beautiful lines and a $5,000.00 tuneup...
Rick Turner
Guitar Maker, Experimenter, Diviner
www.renaissanceguitars.com
www.d-tar.com
Guitar Maker, Experimenter, Diviner
www.renaissanceguitars.com
www.d-tar.com
Rick, in your system then, you just have the upper screws as pivots and the one lower adjustment screw to hold the neck in place, if I'm getting the picture.
I'm assuming that the neck doesn't want to tend to slide up the body with just the one point fixing the neck to the body? This is the impression that I always held regarding the upper bolt. It's not really holding the neck to the body, because string tension is doing that. More of a stabilizing anchor point.
I'm assuming that the neck doesn't want to tend to slide up the body with just the one point fixing the neck to the body? This is the impression that I always held regarding the upper bolt. It's not really holding the neck to the body, because string tension is doing that. More of a stabilizing anchor point.
- matthew
- Blackwood
- Posts: 1192
- Joined: Mon Oct 08, 2007 1:16 pm
- Location: Sydney, Inner West
- Contact:
I have ONE 6mm bolt holding my double bass neck in its mortise. I play the hell out of it and it doesn't tend to ride up in the mortise. Anyway, even if it did, it would only go so far before the single bolt would stop it. If I had a butted neck, I can see that it might have a yaw problem.
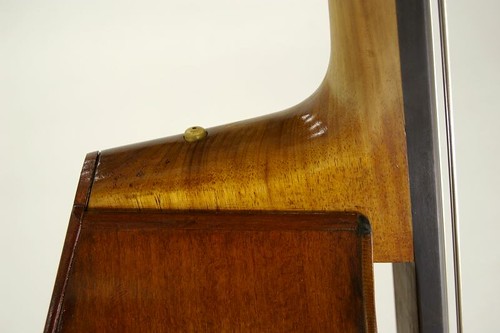
the brass thing you can see is a bit of rounded brass rod used to plug the hole where the hex bolt sits. There's a small hole in the tip; you fish it out with a paperclip when you wnt to remove the neck.
The 5" high tensile bolt screws into a simple brass threaded nut screwed into the bottom of the neck block.
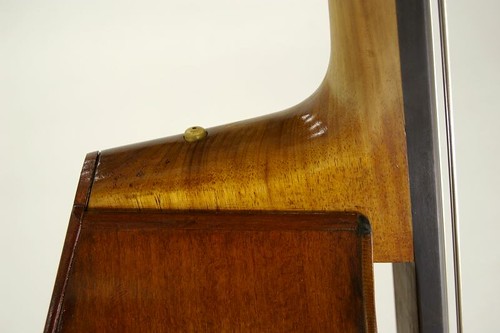
the brass thing you can see is a bit of rounded brass rod used to plug the hole where the hex bolt sits. There's a small hole in the tip; you fish it out with a paperclip when you wnt to remove the neck.
The 5" high tensile bolt screws into a simple brass threaded nut screwed into the bottom of the neck block.
-
- Blackwood
- Posts: 311
- Joined: Sun Jan 13, 2008 10:22 am
- Location: Santa Cruz, Ca.
- Contact:
Correct, there is one bolt holding against the string tension. Why would the neck ride up and shift?
Here's the thing...as I said it's really easy to get all up in your head, over intellectualizing and spun out imagining ways this won't work. Just build one. Build one your way, build one my way, do whatever, but stop thinking so much and let your hands get to work and just build the damned things and learn first hand what works and what doesn't. If Thomas Edison hadn't tried about 1,000 different things for light bulb filaments, we'd still be reading by gaslight... There's a point where all this discussion has to be identified as what it is...talk... Where the rubber meets the road is in building guitars, not talking about them. Nothing ventured, nothing gained.
Here's the thing...as I said it's really easy to get all up in your head, over intellectualizing and spun out imagining ways this won't work. Just build one. Build one your way, build one my way, do whatever, but stop thinking so much and let your hands get to work and just build the damned things and learn first hand what works and what doesn't. If Thomas Edison hadn't tried about 1,000 different things for light bulb filaments, we'd still be reading by gaslight... There's a point where all this discussion has to be identified as what it is...talk... Where the rubber meets the road is in building guitars, not talking about them. Nothing ventured, nothing gained.
Rick Turner
Guitar Maker, Experimenter, Diviner
www.renaissanceguitars.com
www.d-tar.com
Guitar Maker, Experimenter, Diviner
www.renaissanceguitars.com
www.d-tar.com
-
- Blackwood
- Posts: 311
- Joined: Sun Jan 13, 2008 10:22 am
- Location: Santa Cruz, Ca.
- Contact:
I have to agree with what Rick said.
I do a lot of R&D work (I'm an R&D scientist after all) most of what I do these days is chemical engineering. I've found that sitting at a desk and visualising your way through problems will only get you so far.
Getting into the lab (or workshop) and getting started is the best way to solve these types of problems. Get started and a solution will usually present itself as you work.
Works for me anyway.
I do a lot of R&D work (I'm an R&D scientist after all) most of what I do these days is chemical engineering. I've found that sitting at a desk and visualising your way through problems will only get you so far.
Getting into the lab (or workshop) and getting started is the best way to solve these types of problems. Get started and a solution will usually present itself as you work.
Works for me anyway.
I disagree stongly there Rick.
Good planning saves a mountain of leg work. If you don't want to be a part of that process, then that's fine too. You have merely copied a system , whereas we are inventing one. A big difference !
If I had built the very first plan I proposed , I'd be disappointed about now. Our mini 'Think Tank" seems to be working out just fine, with some able to point out flaws to the design and others suggesting better alternatives. All in all , we should be able to finalize a design that all of us agree on as being suitable. . We will carry on for as long as it takes to reach that goal. More brains at work = more knowledge and ideas
If you want to earn the right to be a part of our forum ,as you stated in your previous post, and/or be more a part of the Aussie community in general, then I strongly suggest a change in your arrogant attitude .That's one personality trait us Aussie/ Kiwi folk find very hard to handle. I'm sorry if that seems a harsh statement Rick , but it is actually intended as a helpful and friendly suggestion.
Now ! ,, lets get back to adjustables !
Cheers , Craig
Good planning saves a mountain of leg work. If you don't want to be a part of that process, then that's fine too. You have merely copied a system , whereas we are inventing one. A big difference !
If I had built the very first plan I proposed , I'd be disappointed about now. Our mini 'Think Tank" seems to be working out just fine, with some able to point out flaws to the design and others suggesting better alternatives. All in all , we should be able to finalize a design that all of us agree on as being suitable. . We will carry on for as long as it takes to reach that goal. More brains at work = more knowledge and ideas
If you want to earn the right to be a part of our forum ,as you stated in your previous post, and/or be more a part of the Aussie community in general, then I strongly suggest a change in your arrogant attitude .That's one personality trait us Aussie/ Kiwi folk find very hard to handle. I'm sorry if that seems a harsh statement Rick , but it is actually intended as a helpful and friendly suggestion.
Now ! ,, lets get back to adjustables !

Cheers , Craig
-
- Blackwood
- Posts: 311
- Joined: Sun Jan 13, 2008 10:22 am
- Location: Santa Cruz, Ca.
- Contact:
Well, I did plan, and I studied some old guitars with adjustable neck joints. I added my own spin, but didn't get all hung up about it, and it works. It's not that I don't plan; it's that I don't let planning stop me from doing hands-on three dimensional sketching in wood. What I see here is an awful lot of drawing and chatting and it still looks overly complicated to me...for instance that upper bolt. Looks good on paper or the screen. But it's as useless at teats on a boar...
Look, in my system you've got a three way adjustable tripod...two jack screws up under the fingerboard, one nearer the heel cap. The stresses on it are out of balance because of the leverage on the neck from string pull.
There's a single screw in tension just above the jack screw by the heel cap. In practice because you've got compression from leverage on the two upper jack screws and the lower one is wanting to come away from the body, that lower one is just there to lock against the single angle adjustment screw which is where the true action adjustment comes from.
This system is just too easy, I guess. Not complicated enough for lutherie!
Look, in my system you've got a three way adjustable tripod...two jack screws up under the fingerboard, one nearer the heel cap. The stresses on it are out of balance because of the leverage on the neck from string pull.
There's a single screw in tension just above the jack screw by the heel cap. In practice because you've got compression from leverage on the two upper jack screws and the lower one is wanting to come away from the body, that lower one is just there to lock against the single angle adjustment screw which is where the true action adjustment comes from.
This system is just too easy, I guess. Not complicated enough for lutherie!
Rick Turner
Guitar Maker, Experimenter, Diviner
www.renaissanceguitars.com
www.d-tar.com
Guitar Maker, Experimenter, Diviner
www.renaissanceguitars.com
www.d-tar.com
Thanks for your reply Rick,
My design also works on a very simple tripod system. Couldn't get much easier. The difference being , that mine is more aesthetically pleasing IMO . and doesn't require an engineer to fabricate. The hardware parts are also easly shelf bought . A plan that the average luthier can adopt with ease.
Each builder is of course free to choose which system they prefer.
I do appreciate your skilled and experienced input though Rick
Cheers , Craig
My design also works on a very simple tripod system. Couldn't get much easier. The difference being , that mine is more aesthetically pleasing IMO . and doesn't require an engineer to fabricate. The hardware parts are also easly shelf bought . A plan that the average luthier can adopt with ease.
Each builder is of course free to choose which system they prefer.
I do appreciate your skilled and experienced input though Rick
Cheers , Craig
- matthew
- Blackwood
- Posts: 1192
- Joined: Mon Oct 08, 2007 1:16 pm
- Location: Sydney, Inner West
- Contact:
Worrying about over-intellectualising a problem is perfectly OK; no-one is obliged to read or participate in the discussion.
But it's clear some people here enjoy applying their intellect in a collective way, and are not too time-pressured to have to worry about an instant outcome.
Alternatively, they ARE time pressured by other things (like a day job) and application of intellect via the forum is an enjoyable, practical and possibly fruitful pastime!
I could be wrong, but I think most of us here are making instruments because it's fun. Talking and thinking about it is fun. Making a buck from it is a bonus.
But it's clear some people here enjoy applying their intellect in a collective way, and are not too time-pressured to have to worry about an instant outcome.
Alternatively, they ARE time pressured by other things (like a day job) and application of intellect via the forum is an enjoyable, practical and possibly fruitful pastime!
I could be wrong, but I think most of us here are making instruments because it's fun. Talking and thinking about it is fun. Making a buck from it is a bonus.
-
- Blackwood
- Posts: 311
- Joined: Sun Jan 13, 2008 10:22 am
- Location: Santa Cruz, Ca.
- Contact:
Ahhh, so I'm in the minority as a pro builder here? Hmmm... Well, being a pro does push a certain level of practicality to the forefront for me. I like elegant, simple solutions that are fairly easy to do in a small, boutique production environment and that serve the clients well. I like to design around all the problems I've seen as a professional guitar repairman...and that is really a major key to how I think as a designer. I would urge anyone who really wants to build guitars to do as much repair as possible. The lessons learned are invaluable... Until you learn what goes wrong with "traditional" guitar designs, you can't really move forward with new ones without really putting yourself at risk of either reinventing the wheel or just repeating the same old things that don't work. Also, doing repair work puts you in touch with real musicians, pro and amateur, on a regular basis. You learn how they think, talk, and deal with their instruments (and that may horrify you to some degree). You get a lot of practice doing things like setups and fret mills that you may only do once or twice a year as a hobby builder. You'll have to work on guitars that you may personally disdain, yet are real tools for their owners, and you can learn a certain humility from that as you gain chops working on them.
What this all boils down to is that terrible slogan, "Just do it." You can talk guitars to death, and while you are someone out there is building yet another one. You learn a lot more from the ones you build than from the ones you talk about...
What this all boils down to is that terrible slogan, "Just do it." You can talk guitars to death, and while you are someone out there is building yet another one. You learn a lot more from the ones you build than from the ones you talk about...
Rick Turner
Guitar Maker, Experimenter, Diviner
www.renaissanceguitars.com
www.d-tar.com
Guitar Maker, Experimenter, Diviner
www.renaissanceguitars.com
www.d-tar.com
- matthew
- Blackwood
- Posts: 1192
- Joined: Mon Oct 08, 2007 1:16 pm
- Location: Sydney, Inner West
- Contact:
Well ... that's not quite what i said, although it may well be true. It would surprise me to find any forum worldwide where the majority of members are pro builders. N'est-ce pas?Rick Turner wrote:Ahhh, so I'm in the minority as a pro builder here? Hmmm...
"Just do it" is all very well, and I'm not disagreeing with it as a useful principle. And we ALL like elegant, simple solutions as you describe.
But hey, are you proposing that all we should post here are pictures of our builds and WIPs and slapping each other on the back? What a boring and pointless place it would be if "just do it" becomes the standard by-line whenever ideas are thrown around!
Perhaps pro builders don't get the same fun out of talking about what they do after a while. I dunno.
This thread - although it is rapidly digressing into an off topic debate about the value of intellectualising - has been for me one of the most interesting yet posted here. Intellectual or not. And I think something good will come out of it.
I say, lets get back to the thread, and let those who want to discuss the ideas get on with discussing them, and those that think its a waste of time and much better to "just do it" ... do just that.
Anything wrong with that?
back on topic now please. Anyone got a mock up of the latest version?
Who is online
Users browsing this forum: No registered users and 90 guests