ANZLF Adjustable Neck Joint Group Discussion
There is no doubt whatsoever that Doolin makes a beautiful guitar that really pushes the limits of what a traditional instrument can evolve into. When looking at an external adjuster on a guitar like that, it looks right at home, and in fact I would expect it, being on such an innovative instrument.
I guess it comes down to using your sense of aesthetics, or what will a potential customer think. I'll go way out on a limb and say that you won't find too many people accepting of an external adjusting screw on copy of a vintage (choose you favorite builder). But conversely, build something with a modern look, and make it a feature, then this could become very well accepted, and even expected in years to come.
I guess it comes down to using your sense of aesthetics, or what will a potential customer think. I'll go way out on a limb and say that you won't find too many people accepting of an external adjusting screw on copy of a vintage (choose you favorite builder). But conversely, build something with a modern look, and make it a feature, then this could become very well accepted, and even expected in years to come.
I see the exposed adjuster aesthetic issue as now being resolved . It could be made to look like an obvious adjuster yet pleasing to the eye , as in Mike Doolins new version , or as a strap button . The builder can have that choice. Paul B came up with a strap button resolve earlier in this thread . Take a look !. It leaves the centre of the button to expose the adjusting socket. I suggested that button could even be made of wood to match the bindings.
Dennis my thinking on the Goltz method of using a spring washer means there is play in the system. A yank on the neck could easily temporarally flatten out the spring washer, giving the whole system a certain spongyness.
I intend my design to utilize Dave's adjusting top set screws with the top barrell and bolt in between them ( and in line with them.) One difference than Dave's though in that I want these adjusting set screws into a metal thread. ( As I already mentioned in an earlier post on this thread )
I would also like to point out and MAKE VERY CLEAR : The design I have come up with is NOT a Mike Doolin design ,as a few here have inferred.
I have no idea how his captured lower screw system works and it seems no other members here do either. On that basis , my system can't be a direct copy of his. I came up with my captured screw system with my own 'grey matter' . Chances are that his captured screw method is completley different than my own.
I am incredibly grateful to those who have suggested improvements on the system and also to those who can see a possible flaw in it. I am particularly grateful to Allen for having enough faith in the version to take the time and trouble to make up a more full on mock -up of my invention.
I say 'my invention ' although I prefer to think of it as a system developed with the help of my good fair dinkum mates here on the ANZLF, and that's "fair dinkum"
Here it is once again :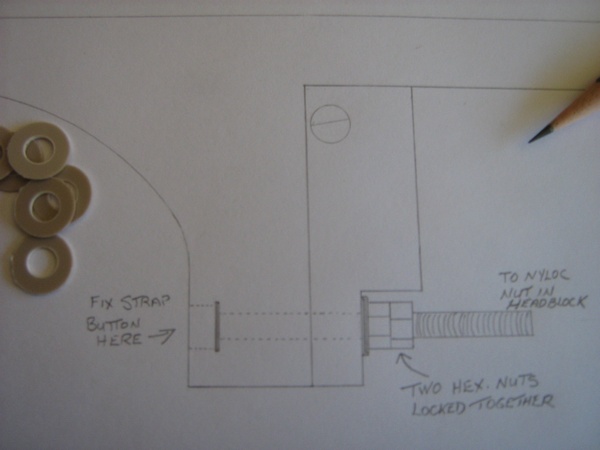
Cheers , Craig
Dennis my thinking on the Goltz method of using a spring washer means there is play in the system. A yank on the neck could easily temporarally flatten out the spring washer, giving the whole system a certain spongyness.
I intend my design to utilize Dave's adjusting top set screws with the top barrell and bolt in between them ( and in line with them.) One difference than Dave's though in that I want these adjusting set screws into a metal thread. ( As I already mentioned in an earlier post on this thread )
I would also like to point out and MAKE VERY CLEAR : The design I have come up with is NOT a Mike Doolin design ,as a few here have inferred.
I have no idea how his captured lower screw system works and it seems no other members here do either. On that basis , my system can't be a direct copy of his. I came up with my captured screw system with my own 'grey matter' . Chances are that his captured screw method is completley different than my own.
I am incredibly grateful to those who have suggested improvements on the system and also to those who can see a possible flaw in it. I am particularly grateful to Allen for having enough faith in the version to take the time and trouble to make up a more full on mock -up of my invention.
I say 'my invention ' although I prefer to think of it as a system developed with the help of my good fair dinkum mates here on the ANZLF, and that's "fair dinkum"

Here it is once again :
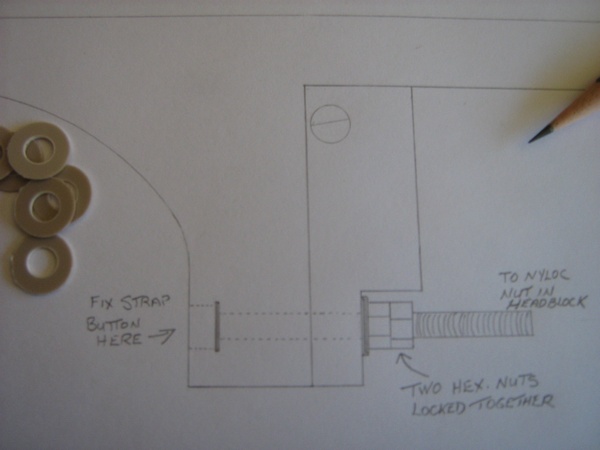
Cheers , Craig
Last edited by Craig on Sat Mar 08, 2008 9:09 pm, edited 1 time in total.
Well, the prototype was knocked up today. And while I didn't spend heaps of time on it, more to the point, it was something quick and nasty, just to test the concept.
This shows the joint fully snugged up.
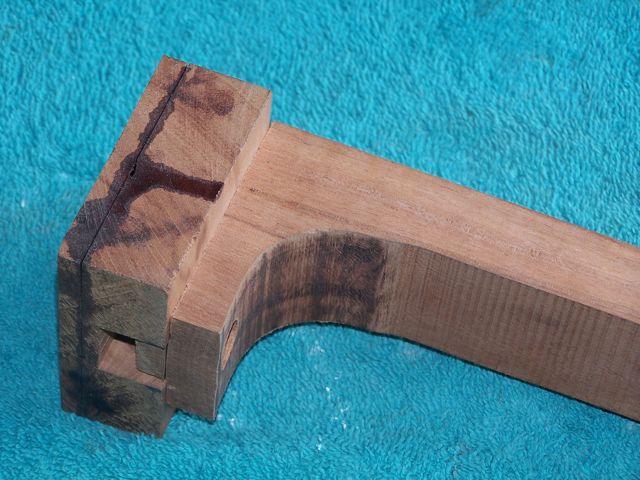
This shows the joint with 1/2 turn of the adjusting screw. I got this much adjustment without touching the upper bolt.

This is with 1 1/2 turns of the adjusting screw. I did have to let the upper bolt off by 1/4 turn to allow this much adjustment without it feeling like I was forcing things.
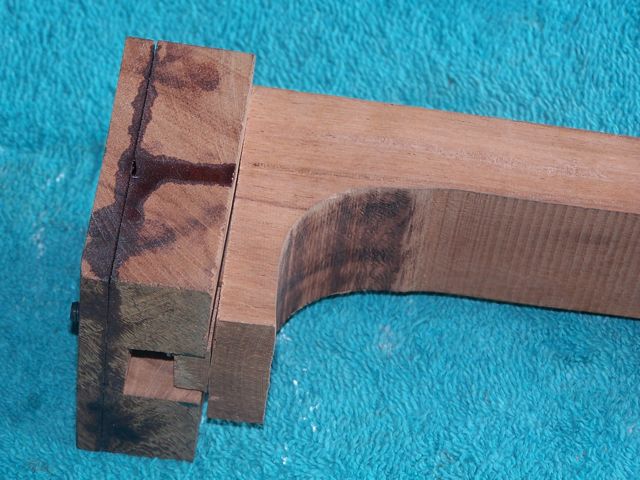
I've used a nyloc nut that has been epoxied in place.
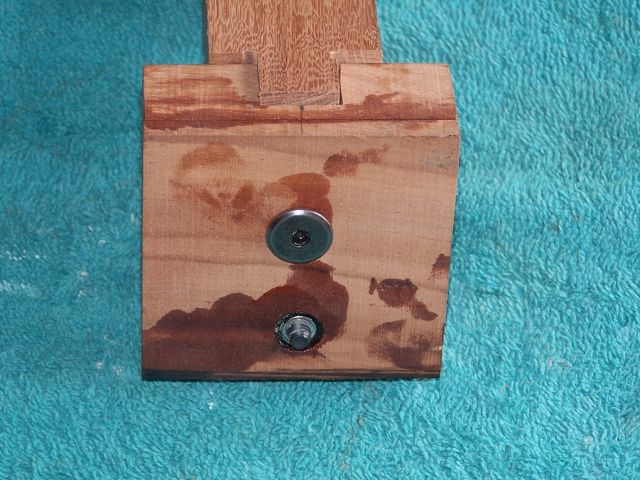
The adjuster bolt is a cap head screw.
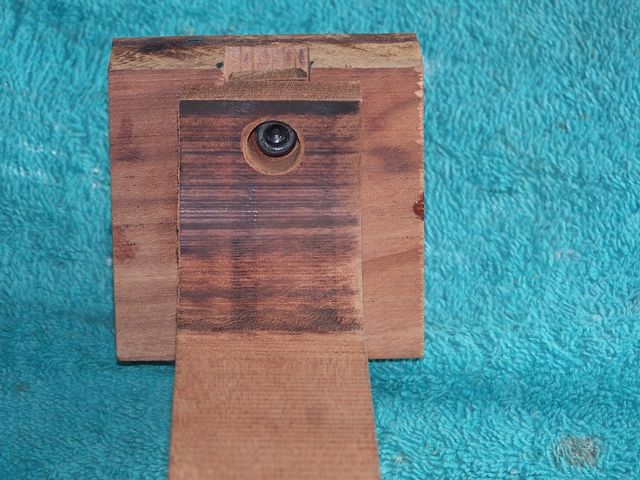
Standard barrel nut and the adjuster screw takes off on Craig's idea. Instead of using 2 nuts that lock each other, and potentially will come loose, I used another nyloc nut and a couple of steel washers to help give a bit of slip. I don't have any of those slippery plastic/nylon ones and I do think that they may be an improvement. I stuffed it up a bit by cutting off all the tenon and then realizing that the treads didn't go far enough up the screw to be able to thread the nyloc nut all the way on, so I had to use part of the off cut as a spacer. Not pretty, but it does the job.
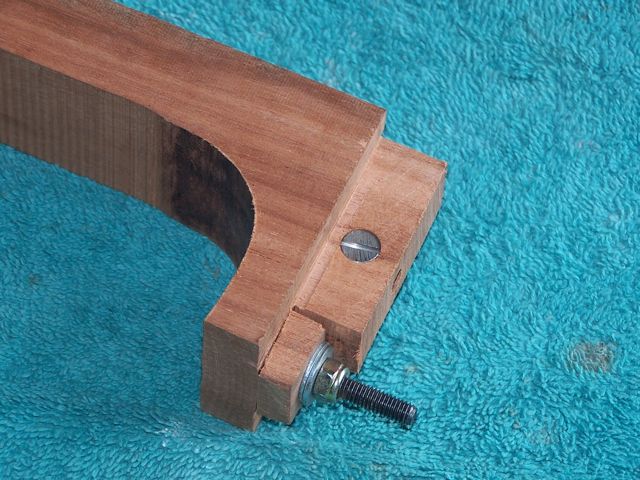
My impressions are that it works brilliantly. In fact it quite surprised me. Rock solid and easy to adjust. There is a potential weak spot in the nyloc nut being epoxied into the neck block. If I could find one with a large integrated washer, this would give a much better surface area to glue in. I come across them now and then at work, and I'll be sure to keep them when I see some more.
I would still add the two set screws to adjust yaw, but the lower adjuster is so rigid (as long as the nut that is epoxied in the neck block stays put) that you don't need the lower set screw.
Also, I laid out the bolts to allow a 20 mm deep fret board extension. I just didn't cut the neck block for it as I didn't think that it would affect the results, and I was keen on getting this finished.
This shows the joint fully snugged up.
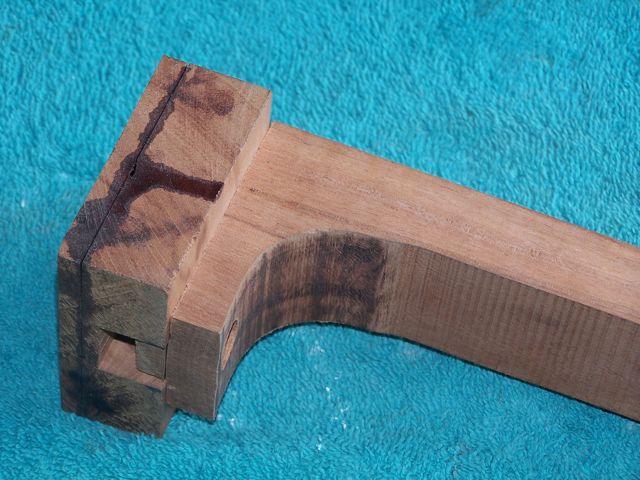
This shows the joint with 1/2 turn of the adjusting screw. I got this much adjustment without touching the upper bolt.

This is with 1 1/2 turns of the adjusting screw. I did have to let the upper bolt off by 1/4 turn to allow this much adjustment without it feeling like I was forcing things.
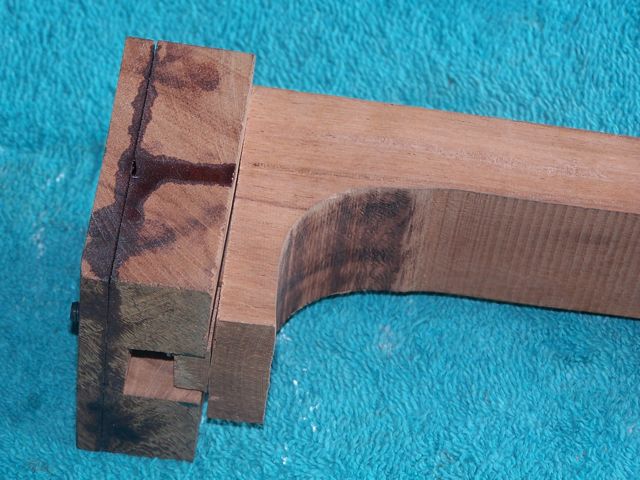
I've used a nyloc nut that has been epoxied in place.
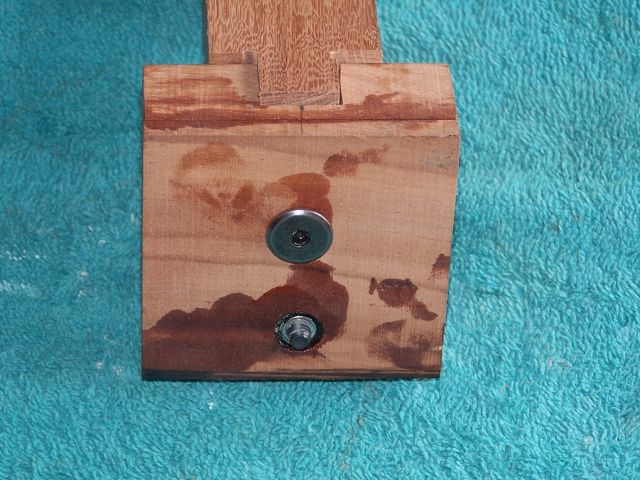
The adjuster bolt is a cap head screw.
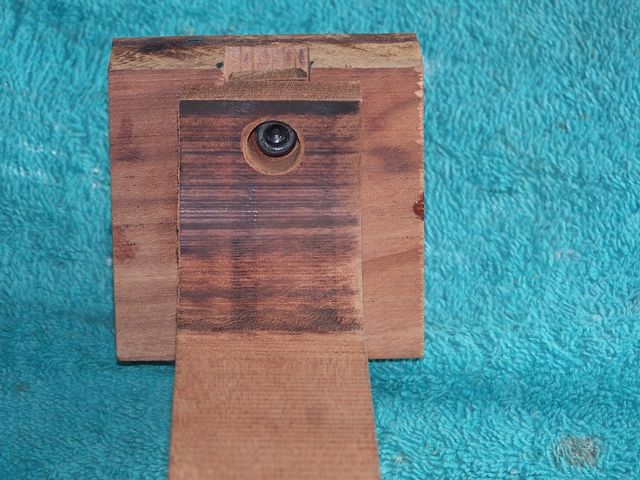
Standard barrel nut and the adjuster screw takes off on Craig's idea. Instead of using 2 nuts that lock each other, and potentially will come loose, I used another nyloc nut and a couple of steel washers to help give a bit of slip. I don't have any of those slippery plastic/nylon ones and I do think that they may be an improvement. I stuffed it up a bit by cutting off all the tenon and then realizing that the treads didn't go far enough up the screw to be able to thread the nyloc nut all the way on, so I had to use part of the off cut as a spacer. Not pretty, but it does the job.
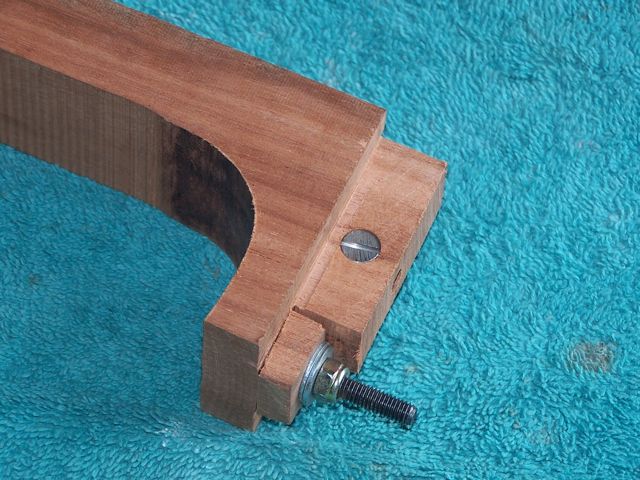
My impressions are that it works brilliantly. In fact it quite surprised me. Rock solid and easy to adjust. There is a potential weak spot in the nyloc nut being epoxied into the neck block. If I could find one with a large integrated washer, this would give a much better surface area to glue in. I come across them now and then at work, and I'll be sure to keep them when I see some more.

I would still add the two set screws to adjust yaw, but the lower adjuster is so rigid (as long as the nut that is epoxied in the neck block stays put) that you don't need the lower set screw.
Also, I laid out the bolts to allow a 20 mm deep fret board extension. I just didn't cut the neck block for it as I didn't think that it would affect the results, and I was keen on getting this finished.
Only problem I can see with it, is that it pivots up near the top of the neck (under the fretboard that isn't there). This is going to have a big effect on intonation, you can see the gap opening up at the bottom of the joint as adjustments were made, well, you're getting about 1/2 to 3/4 of that movement at the 14th or 12th (whatever you have sitting above that joint). The frets are moving towards the bridge as the gap at the tip of the heel increases.
What's needed is a joint that pivots at the fret top . You could adjust the neck till the cows come home and it won't affect intonation - if you can come up with a joint that works like that.
What's needed is a joint that pivots at the fret top . You could adjust the neck till the cows come home and it won't affect intonation - if you can come up with a joint that works like that.
OK, I see your point.
Now if the set screws are installed towards the top of the neck block, we can use these to adjust not only yaw, but also intonation as well...yes, no? We are however back to a point were if there is any drastic change needed in neck set, the strings are going to have to be slackened off to get your hand inside.
That shot of 1 1/2 turns was rather drastic. Just to show how much you could get out of the system. I don't think that you would need that much adjustment in real world conditions. I don't know how much you would need, and how much that would affect the intonation.
I would see this system as one that does a small tweak rather easily, and without actually building an instrument with it, I have no idea how it will work in the real world. Bigger minds than mine may be able to shed some more light.
I'm going back to my glass of wine now.

Now if the set screws are installed towards the top of the neck block, we can use these to adjust not only yaw, but also intonation as well...yes, no? We are however back to a point were if there is any drastic change needed in neck set, the strings are going to have to be slackened off to get your hand inside.
That shot of 1 1/2 turns was rather drastic. Just to show how much you could get out of the system. I don't think that you would need that much adjustment in real world conditions. I don't know how much you would need, and how much that would affect the intonation.
I would see this system as one that does a small tweak rather easily, and without actually building an instrument with it, I have no idea how it will work in the real world. Bigger minds than mine may be able to shed some more light.
I'm going back to my glass of wine now.

Allen,
That's bloody fantastic !. I can't begin to tell you how much I appreciate the effort you have put in here Allen. Thanks also for the pics etc.
If you had installed the top pivot set screws in place ( in line with the barrel bolt ), I'm sure the neck would pivot even more , without having to touch the top barrel screw. Even so , it appears to be able to move the neck's angle quite considerably. Especially when we are only talking a fraction of a millimeter type of adjustment required in most instances.
Did you find the heel/neck to move in a nice parrallel manor when being adjusted ? I'm sure the locking nuts or nyloc nut thing can be worked out.
Yes , my plan shows cutting only enough off the tenon to acccommodate the locking nut/s. I figure the more wood left there the better , and it still gives a full length tenon this way.
I'm absolutley wrapped in your findings Allen. A question ; How do you feel about the durability of Nyloc nuts ?. They would be easy enough to remove with a very hot thread , when they are embedded in epoxy , but I'm probably thinking of the worse scenario.
Onya Allen , Your a true mate, and stuck with it when I was starting to run cold.
I'm off now ,to do some geometry.
Cheers Craig
That's bloody fantastic !. I can't begin to tell you how much I appreciate the effort you have put in here Allen. Thanks also for the pics etc.
If you had installed the top pivot set screws in place ( in line with the barrel bolt ), I'm sure the neck would pivot even more , without having to touch the top barrel screw. Even so , it appears to be able to move the neck's angle quite considerably. Especially when we are only talking a fraction of a millimeter type of adjustment required in most instances.
Did you find the heel/neck to move in a nice parrallel manor when being adjusted ? I'm sure the locking nuts or nyloc nut thing can be worked out.
Yes , my plan shows cutting only enough off the tenon to acccommodate the locking nut/s. I figure the more wood left there the better , and it still gives a full length tenon this way.
I'm absolutley wrapped in your findings Allen. A question ; How do you feel about the durability of Nyloc nuts ?. They would be easy enough to remove with a very hot thread , when they are embedded in epoxy , but I'm probably thinking of the worse scenario.
Onya Allen , Your a true mate, and stuck with it when I was starting to run cold.
I'm off now ,to do some geometry.
Cheers Craig
Last edited by Craig on Sun Mar 09, 2008 9:33 pm, edited 2 times in total.
Dave White wrote:Craig,
The change in string length that adjusting around the top two pivots brings into play for the range of action height changes by adjusting the bottom screw(s) are so minute as to be "angels on the head of a pin" territory for this argumentative, obnoxious jerkThe average players fingers are more than capable of dealing with this - as you have to do anyway for different action settings. Play the higher settings with the same technique as the low and you will sharpen the notes slightly.
I love this place
I've just finished posting and see you have posted inbetween Paul, so I haven't had a chance to do the geometry yet. You can see what Dave has written above , and he is an experienced adjustable neck builder. Without doing the math , I can't see it a problem for the tiny amount of adjustment normally required. If a heap was required , then obviously an adjustment to the top pivet section could handle it.
Cheers , Craig
I drilled the holes so that everything was a pretty snug fit. The tenon is also reasonable snug. You could get a few degrees of yaw with the fit I have. It was just a bit of a guess.
Other than the neck pivoting, I didn't see any other movement in the system.
Nyloc nuts are pretty durable, but will loose some of their grab after repeated use. The one used as a lock nut next to the tenon would last ages. It's not having threads turned in and out of it. The one that is epoxied in the neck block is the one that potentially will wear out. But saying that, adjustments are only going to be in the region of 1 full turn max. And this isn't going to be happening all that often. This should last a very long time. It might not even require a nyloc nut for this system to work. I just used it as a safety measure to stop the adjuster from being able to back itself off.
Now that I think about it. The nyloc nut that snugs up next to the tenon puts enough tension on the adjuster that it's not going to be all that easy to move on its own. You could use a barrel nut in the neck block as well if you wanted to and get similar results.
Other than the neck pivoting, I didn't see any other movement in the system.
Nyloc nuts are pretty durable, but will loose some of their grab after repeated use. The one used as a lock nut next to the tenon would last ages. It's not having threads turned in and out of it. The one that is epoxied in the neck block is the one that potentially will wear out. But saying that, adjustments are only going to be in the region of 1 full turn max. And this isn't going to be happening all that often. This should last a very long time. It might not even require a nyloc nut for this system to work. I just used it as a safety measure to stop the adjuster from being able to back itself off.
Now that I think about it. The nyloc nut that snugs up next to the tenon puts enough tension on the adjuster that it's not going to be all that easy to move on its own. You could use a barrel nut in the neck block as well if you wanted to and get similar results.
- Tom Morici
- Blackwood
- Posts: 103
- Joined: Thu Nov 01, 2007 5:46 pm
- Location: Montana, USA
- Contact:
Here's one more idea to consider.
This takes the pressure off of the small allen head of the bolt, which
I believe would wear quickly.
This drawing is not to scale just a concept. I have tried to keep it simple
and clean looking. There is no reason a pair of nuts could not be used
in place of the pinned or soldered nut I show in my design.
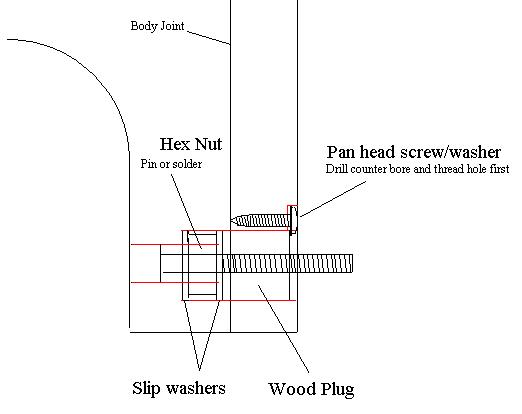
I hope this helps!
Tom
This takes the pressure off of the small allen head of the bolt, which
I believe would wear quickly.
This drawing is not to scale just a concept. I have tried to keep it simple
and clean looking. There is no reason a pair of nuts could not be used
in place of the pinned or soldered nut I show in my design.
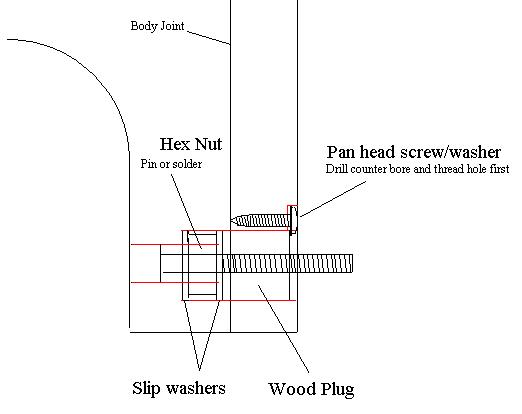
I hope this helps!
Tom
Hi Dom, Yep , I'm sure that would work , but you'd have to have this long adjusting rod with you and be peering through the soundhole getting it lined up on the bolt etc. Sounds like a bit of a hassle .
A quick tweak with an allen key seems a lot easier. I believe an allen head socket screw will handle the job just fine
Cheers , Craig
( EDIT ) Sorry Allen , we were posting at the same time

A quick tweak with an allen key seems a lot easier. I believe an allen head socket screw will handle the job just fine
Cheers , Craig
( EDIT ) Sorry Allen , we were posting at the same time


Allen , I'm concerned the Nyloc nut at the end of the tenon may move when turning the adjustment screw . What ,I'm trying to say is that because it is snugged up against the end of the tenon , that friction may grab the nyloc nut to undo it . I hope that made sense. I realise my slippery washers would lesson that possibility , but feel that the two locking nuts, as per my plan, may provide more insurance this doesn't occur.
What do ya reckon ?
Cheers, Craig
What do ya reckon ?
Cheers, Craig
This whole thing was assembled and disassembled a few times and the nyloc didn't move at all. As I said, the slippery washers I think would help, and if you got to the point of being worried about things moving, I suppose you could brush on some loctite then thread the nut down to where you wanted and be done with it.
You mean like a standard Maton truss rod adjustment tool which is just a 600mm screwdriver with a socket brazed on the end which you insert through the endpin hole to adjust the truss rod? Sounds perfectly acceptable to me.Craig L wrote:Hi Dom, Yep , I'm sure that would work , but you'd have to have this long adjusting rod with you and be peering through the soundhole getting it lined up on the bolt etc. Sounds like a bit of a hassle .
Cheers , Craig
( EDIT ) Sorry Allen , we were posting at the same time![]()
At least the neck would be adjustable to the ambiance, eg tropic wet, tropic dry, that's only twice a year. I think if you engineer for any more you are starting to let the tail wag the dog IMHO. Even with the inconvenience of having to pull the endpin to make an adjustment it is a far cry from what most instruments are offering out there.
Quite frankly I think that if your the sort of person who need to adjust the neck set with every swing of RH that occurs, you might be getting a little anal IMHO.
Cheers
Kim
G'day Kim,
Ooouuch !
.
Well , I do like everything "just so "
I guess that makes all the other adjustable neck makers anal as well.
I've never had a guitar I was able to adjust this way , but often thought of it being a good thing. Maybe it's just me , but when I pick-up my guitar to find the action is a bit higher than usual because it rained overnight or whatever , you just accept it , but maybe with a hint of dissapointment or frustration . To make a guitar with a consistant action regardless of climatic conditions , I see as a big plus, but only if that adjustment can be performed quickly and easily with no fuss. This system uses only a common allen key which could literally lower the strings in seconds.
Cheers ,Craig
Ooouuch !

Well , I do like everything "just so "

I guess that makes all the other adjustable neck makers anal as well.
I've never had a guitar I was able to adjust this way , but often thought of it being a good thing. Maybe it's just me , but when I pick-up my guitar to find the action is a bit higher than usual because it rained overnight or whatever , you just accept it , but maybe with a hint of dissapointment or frustration . To make a guitar with a consistant action regardless of climatic conditions , I see as a big plus, but only if that adjustment can be performed quickly and easily with no fuss. This system uses only a common allen key which could literally lower the strings in seconds.
Cheers ,Craig
- Dave White
- Blackwood
- Posts: 452
- Joined: Mon Nov 12, 2007 3:10 am
- Location: Hughenden Valley, England
- Contact:
You go to sleep and wake up in the morning and all this has appeared - just like Father Christmas!! Keep bringing it on!!
Some comments/observations.
Allen - Great stuff - there's nothing like a bit of prototyping to get the juices flowing. One thing I don't fully understand (and apllies I think to Tom's interesting idea) - if you have a hex/nyloc nut captured in the heel and the threaded insert in the neck block, when you turn the adjusting bolt it will be trying to move forward (or back) in the captured hex/nyloc nut as it turns and will move forward (or back) in the neck-block insert. I can see that it can't and this is the capture mechanism but won't you be partially stripping either the hex nut or bolt thread as you do the adjustment? If so you would need to know how long you could do this before you get slippage. Could be years or centuries but then again . . . With Craigs locking hex nuts they turn with the adjuster and the potential weak point is the washer they turn against and them staying locked as adjustment goes on. You need to simulate 160-180lbs constant string pull on the lower heel area plus the string vibration and players leverage on the neck to see what happens.
You do need the top pivot points as high up as you can get them but the neck extension can impact this and there is a bit of a trade off. You could use Rick's dadoed cf rods or you could make the neck extension less wide (as opposed to deep) which would give enough meat on the neck-block sides to go really high up but less support for the fretboard and maybe a loss of tone in notes played here.
Craig - I've been thinking more about the top pivot bolts in metal threads. You would need to check that under the string thrust and vibration of the strings that there would be no tenedency for them to unscrew over time. The slightest movement here and you are "screwed" so to speak. That's why I opted for the "belt and braces" method I pm'd you about.
Dom,
Mark Swanson does exactly this using Mike Doolin's old internal adjustment system- a huge long allen key and a rear access panel - a bit like James Herriot
An interesting sell to a paying customer.
One point about the internal sytem with the bottom bolt going into a barrel bolt in the neck tennon - this will swivel helping move with the geometry as you adjust. You probably have enough play in a threaded insert in the neck-block though.
Some comments/observations.
Allen - Great stuff - there's nothing like a bit of prototyping to get the juices flowing. One thing I don't fully understand (and apllies I think to Tom's interesting idea) - if you have a hex/nyloc nut captured in the heel and the threaded insert in the neck block, when you turn the adjusting bolt it will be trying to move forward (or back) in the captured hex/nyloc nut as it turns and will move forward (or back) in the neck-block insert. I can see that it can't and this is the capture mechanism but won't you be partially stripping either the hex nut or bolt thread as you do the adjustment? If so you would need to know how long you could do this before you get slippage. Could be years or centuries but then again . . . With Craigs locking hex nuts they turn with the adjuster and the potential weak point is the washer they turn against and them staying locked as adjustment goes on. You need to simulate 160-180lbs constant string pull on the lower heel area plus the string vibration and players leverage on the neck to see what happens.
You do need the top pivot points as high up as you can get them but the neck extension can impact this and there is a bit of a trade off. You could use Rick's dadoed cf rods or you could make the neck extension less wide (as opposed to deep) which would give enough meat on the neck-block sides to go really high up but less support for the fretboard and maybe a loss of tone in notes played here.
Craig - I've been thinking more about the top pivot bolts in metal threads. You would need to check that under the string thrust and vibration of the strings that there would be no tenedency for them to unscrew over time. The slightest movement here and you are "screwed" so to speak. That's why I opted for the "belt and braces" method I pm'd you about.
Dom,
Mark Swanson does exactly this using Mike Doolin's old internal adjustment system- a huge long allen key and a rear access panel - a bit like James Herriot

One point about the internal sytem with the bottom bolt going into a barrel bolt in the neck tennon - this will swivel helping move with the geometry as you adjust. You probably have enough play in a threaded insert in the neck-block though.
Dave White
[url=http://www.defaoiteguitars.com]De Faoite Stringed Instruments[/url]
[url=http://www.defaoiteguitars.com]De Faoite Stringed Instruments[/url]
Thanks for that Dave,
Regarding the upper set screw pivots : As I posted earlier ., I thought something like a little nyloc nut set into each side of the headblock ( heel side) might handle the task. I would use T- nuts , but as you say , they may let the setscrew threads move. .
An outer lock nut on the set screw would be ideal and a bit like your belt and braces thing Dave, but because the little blighter is buried in the headblock ,it would seem not possible.,,,,,,,,thinking,,
Howzabout sacking the set screws all together and use hex socket screws instead. These being easily long enough to go through the headblock. The thread remaining proud of the headblock containing a small nut to lock the thread in position against the headblock face.
,,,, Then again maybe the nyloc .
EDIT : I should of added : these screws going into T-nuts as they take up little room
Cheers mate, Craig
Regarding the upper set screw pivots : As I posted earlier ., I thought something like a little nyloc nut set into each side of the headblock ( heel side) might handle the task. I would use T- nuts , but as you say , they may let the setscrew threads move. .
An outer lock nut on the set screw would be ideal and a bit like your belt and braces thing Dave, but because the little blighter is buried in the headblock ,it would seem not possible.,,,,,,,,thinking,,
Howzabout sacking the set screws all together and use hex socket screws instead. These being easily long enough to go through the headblock. The thread remaining proud of the headblock containing a small nut to lock the thread in position against the headblock face.
,,,, Then again maybe the nyloc .
EDIT : I should of added : these screws going into T-nuts as they take up little room
Cheers mate, Craig
Last edited by Craig on Sun Mar 09, 2008 9:36 pm, edited 3 times in total.
Sorry Craig,
I am not panning the idea of an adjustable neck. In fact it was I who first suggest this as a solution to Allen when he mentioned the problems he was experiencing in NQ. Also, I need to mention that I really do support and applaud all your collective efforts to develop a better more simplistic system than what is currently available and will be watching closely as things unfold.
Having said that, I must question the point of having an adjustable neck that is sooo convenient for a player to adjust that they can quickly make an adjustment on the fly, when most, and I do mean most, seem to struggle to come to terms with the compounding effects that neck relief, intonation, neck angle and saddle height etc have upon setup and playability. I reckon if you give your average player yet another variable to contend with, you will run the real risk of confound them into accusations against your own skills as a builder. It only takes one penis fingered moron on a players forum to start slinging shit for it to adversely effect your reputation as a builder. This is sure to come sooner or later when one of your instruments finds it's way into the hands of a klutz who finds it easier to bad mouth you rather than face up to his or her own inadequacies.
Don't get me wrong, I certainly can see the the benefits of a good reliable adjustment system, but I also remain concerned about convenience being the main focus for another reason. Generally, I find that convenience is an engineered quality that comes at the prices of reliability in design. I personally would rather see a system which erred on the side of requiring a bit of commitment to the task from the person making the adjustment. Such as backing off the strings or pulling the endpin etc. At least this would introduce a bit of forethought as to whether or not an adjustment was really required at that point in time or if it was better to just wait for the settling of a large swing in RH and persevere. This then would avoid over use and abuse of the system and the inevitable introduction of yet another set of problems to contend with.
Cheers
Kim

I am not panning the idea of an adjustable neck. In fact it was I who first suggest this as a solution to Allen when he mentioned the problems he was experiencing in NQ. Also, I need to mention that I really do support and applaud all your collective efforts to develop a better more simplistic system than what is currently available and will be watching closely as things unfold.
Having said that, I must question the point of having an adjustable neck that is sooo convenient for a player to adjust that they can quickly make an adjustment on the fly, when most, and I do mean most, seem to struggle to come to terms with the compounding effects that neck relief, intonation, neck angle and saddle height etc have upon setup and playability. I reckon if you give your average player yet another variable to contend with, you will run the real risk of confound them into accusations against your own skills as a builder. It only takes one penis fingered moron on a players forum to start slinging shit for it to adversely effect your reputation as a builder. This is sure to come sooner or later when one of your instruments finds it's way into the hands of a klutz who finds it easier to bad mouth you rather than face up to his or her own inadequacies.
Don't get me wrong, I certainly can see the the benefits of a good reliable adjustment system, but I also remain concerned about convenience being the main focus for another reason. Generally, I find that convenience is an engineered quality that comes at the prices of reliability in design. I personally would rather see a system which erred on the side of requiring a bit of commitment to the task from the person making the adjustment. Such as backing off the strings or pulling the endpin etc. At least this would introduce a bit of forethought as to whether or not an adjustment was really required at that point in time or if it was better to just wait for the settling of a large swing in RH and persevere. This then would avoid over use and abuse of the system and the inevitable introduction of yet another set of problems to contend with.
Cheers
Kim
- Tom Morici
- Blackwood
- Posts: 103
- Joined: Thu Nov 01, 2007 5:46 pm
- Location: Montana, USA
- Contact:
Sorry Tom you are quite correct. I overlooked that.
I think that little pan head screw will be working hard , and it seems dangerously close to the edge of your plug hole. Two pan head screws, ( one either side of your plug hole would be better).
The thing is Tom , I don't think the adjusting screw's allen head (as per my plan ) will have problems with any wearing issues . It has a washer and slip washer between it and the wood surface of the heel. In any case , should there be any slack develop in that area ( and I'm sure there would be after initially bedding in ), That slack is so easily taken out via the two locking hex nuts. This keeps the system simple , strong and reliable without resorting to plugs , panheadscrews and a little plate to push the plug against your pinned or soldered nut. I'm hoping I'm understanding this correctly.
Simple ideas are usually the best ones , and they suit my simple mind
Cheers, Craig
I think that little pan head screw will be working hard , and it seems dangerously close to the edge of your plug hole. Two pan head screws, ( one either side of your plug hole would be better).
The thing is Tom , I don't think the adjusting screw's allen head (as per my plan ) will have problems with any wearing issues . It has a washer and slip washer between it and the wood surface of the heel. In any case , should there be any slack develop in that area ( and I'm sure there would be after initially bedding in ), That slack is so easily taken out via the two locking hex nuts. This keeps the system simple , strong and reliable without resorting to plugs , panheadscrews and a little plate to push the plug against your pinned or soldered nut. I'm hoping I'm understanding this correctly.
Simple ideas are usually the best ones , and they suit my simple mind


Cheers, Craig
Dave, there certainly is the potential for the nyloc nut on the adjuster screw to want to back off once it is under pressure from string pull. I really have no idea how adding 160 lbs. of pull against the joint will affect its adjustability.
As I said, this could possibly be rectified with a bit of loctite. I would see this as the weak link here. As for stripping threads, I suppose its possible, but I think that the nut backing off, or washers wearing out or the head of the cap screw wearing into the heel, are the most probable places were a failure will occur.
You could also use a plain nut and use a bit of solder to lock it in place, but then if using a nylon slip washer, you run the risk of getting things too hot and melting the washer.
As I said, this could possibly be rectified with a bit of loctite. I would see this as the weak link here. As for stripping threads, I suppose its possible, but I think that the nut backing off, or washers wearing out or the head of the cap screw wearing into the heel, are the most probable places were a failure will occur.
You could also use a plain nut and use a bit of solder to lock it in place, but then if using a nylon slip washer, you run the risk of getting things too hot and melting the washer.
I am a tinkerer and love doing adjustments on things, mucking around, testing different things, so like Craig think it would be cool to be able to easily set the action. I would do it every time I tuned if need be if it was easy enough. I do it on my electric guitars.
The reason I was thinking about hidden hardware was because a friend said he saw a taylor that had the bolts in the fingerboard and he was disgusted. He thought it was a sign of cheap production. This can be overcome of course with marketing, electric guitars are covered in bolts and people love them, ... anyway,.
Then my brain started thinking, (Note from author: this could go anywhere)
Where could you put the long tool.
In a special pocket in the case? boring
Inside a walking stick for the discerning gentleman guitar play?
In place inside the guitar...make it out of carbon...make it part of some internal bracing system...hey why not use a brace from neck-block to tail block, mmm...like those little neck-block to waist braces, mmm...drifting...make soundboard lighter...how about making a double top but with the radius opposed instead of nested so rather than a dish the top is like a discus, like a saucer with risers to keep it spaced and keep the structure stiff…spruce or balsa spacers…or foam...what about a glass reinforced foam top...like on the surfboards i used to make...surfboards very light and very strong and remember how resonent they use to sound...a surfboard guitar...
Dom
The reason I was thinking about hidden hardware was because a friend said he saw a taylor that had the bolts in the fingerboard and he was disgusted. He thought it was a sign of cheap production. This can be overcome of course with marketing, electric guitars are covered in bolts and people love them, ... anyway,.
Then my brain started thinking, (Note from author: this could go anywhere)
Where could you put the long tool.
In a special pocket in the case? boring
Inside a walking stick for the discerning gentleman guitar play?
In place inside the guitar...make it out of carbon...make it part of some internal bracing system...hey why not use a brace from neck-block to tail block, mmm...like those little neck-block to waist braces, mmm...drifting...make soundboard lighter...how about making a double top but with the radius opposed instead of nested so rather than a dish the top is like a discus, like a saucer with risers to keep it spaced and keep the structure stiff…spruce or balsa spacers…or foam...what about a glass reinforced foam top...like on the surfboards i used to make...surfboards very light and very strong and remember how resonent they use to sound...a surfboard guitar...
Dom
Who is online
Users browsing this forum: No registered users and 84 guests