ANZLF Adjustable Neck Joint Group Discussion
Yes it was my intention to have the strap button double as the adjusting nut Allen,as Dennis suggested in his above post. Only trouble is I haven't worked out how yet
I've just made a mock-up of version two with a bit of scrap wood about the size of a heel. I attached the screw and nuts through it to see how the screw felt when tensioned up etc. Keeping in mind it wasn't being held in a neck block mortice or being held by the upper barrel bolt ,,I placed a nyloc nut on the end which was then held in the vice . It turned very smoothly, but the 1/4 " thread itself is long enough to move about a bit. Too long for it's diameter me thinks . I'm thinking the set screw with the normal lower neck screw as in Daves and Doolin's would be much firmer as it has something to tighten against ,whereas this version has the heel being held in position by the shank of a 1/4 " thread,,,,,,suspended ,if you will. I realise it would appear a whole lot firmer on a full-on headblock with an upper neck bolt , but it's made me go a bit cold on the idea. Particularly after reading James' post above.
I'm afraid it's back to the drawing board
James, Thanks for your input. I too have done the Fender neck shim thing many times and I'm sure everyone here has. The idea of an adjustable neck is so that the guitarist has a consistant action regardless of climatic conditions . Some of us consider that to be an improvement in design . If we didn't try for improvements , we might all be driving Model T's still.We are just striving to make the instrument perform or behave better,,,and I might add ,having a bit of fun in doing so. The intention of an adjustable neck is not to compensate for a shonky build that will probably need a neck reset any time real soon, but rather , to improve the instruments playability with a cleverly designed simple little adjustment method. You have mentioned quite a few systems in your above post , but when put into practice on a guitar neck you will soon find that it ain't that simple . I know most of us would really appreciate you coming up with a great system that works well. I'm just a piano Tuner .With your engineering background , you just may have the simple
answer. You seem like you have already
James , adjusting the bridge hieght isn't the ideal way to change string height. Firstly , I've never come accross one on a flat top that I've really liked ,and I've done some of my limited brain storming on the subject as have loads of others . More importantly. it changes the string downbearing on the bridge. It makes more sense to alter the neck angle.
Cheers , Craig


I've just made a mock-up of version two with a bit of scrap wood about the size of a heel. I attached the screw and nuts through it to see how the screw felt when tensioned up etc. Keeping in mind it wasn't being held in a neck block mortice or being held by the upper barrel bolt ,,I placed a nyloc nut on the end which was then held in the vice . It turned very smoothly, but the 1/4 " thread itself is long enough to move about a bit. Too long for it's diameter me thinks . I'm thinking the set screw with the normal lower neck screw as in Daves and Doolin's would be much firmer as it has something to tighten against ,whereas this version has the heel being held in position by the shank of a 1/4 " thread,,,,,,suspended ,if you will. I realise it would appear a whole lot firmer on a full-on headblock with an upper neck bolt , but it's made me go a bit cold on the idea. Particularly after reading James' post above.
I'm afraid it's back to the drawing board
James, Thanks for your input. I too have done the Fender neck shim thing many times and I'm sure everyone here has. The idea of an adjustable neck is so that the guitarist has a consistant action regardless of climatic conditions . Some of us consider that to be an improvement in design . If we didn't try for improvements , we might all be driving Model T's still.We are just striving to make the instrument perform or behave better,,,and I might add ,having a bit of fun in doing so. The intention of an adjustable neck is not to compensate for a shonky build that will probably need a neck reset any time real soon, but rather , to improve the instruments playability with a cleverly designed simple little adjustment method. You have mentioned quite a few systems in your above post , but when put into practice on a guitar neck you will soon find that it ain't that simple . I know most of us would really appreciate you coming up with a great system that works well. I'm just a piano Tuner .With your engineering background , you just may have the simple
answer. You seem like you have already


James , adjusting the bridge hieght isn't the ideal way to change string height. Firstly , I've never come accross one on a flat top that I've really liked ,and I've done some of my limited brain storming on the subject as have loads of others . More importantly. it changes the string downbearing on the bridge. It makes more sense to alter the neck angle.
Cheers , Craig
- Bob Connor
- Admin
- Posts: 3115
- Joined: Mon Jul 09, 2007 9:43 pm
- Location: Geelong, Australia
- Contact:
Once you get this nailed down to something you think is workable, let me know what metal parts you need to make this work and what sort of metal you want it made from.
The bass player in our band is a fitter and turner (a bloody good one)
and can produce anything like this with absolute precision.
He made the press clamp for our Fox Bender out of stainless and it's a sensational piece of work. I'm building him a guitar in return for some precision templates and jigs so he'll whip some of these neck adjusters up for us to try for nix.
If you blokes can come up with something that you are all happy with I'm sure Rick will be able to produce these parts on an ongoing basis at a very reasonable cost.
Bob
The bass player in our band is a fitter and turner (a bloody good one)
and can produce anything like this with absolute precision.
He made the press clamp for our Fox Bender out of stainless and it's a sensational piece of work. I'm building him a guitar in return for some precision templates and jigs so he'll whip some of these neck adjusters up for us to try for nix.
If you blokes can come up with something that you are all happy with I'm sure Rick will be able to produce these parts on an ongoing basis at a very reasonable cost.
Bob
Thanks for that offer Bob. It could sure come in handy if we can do any good with a design . C'mon guys , thinking caps on ! I'm running on dry at the moment. ,,, Perhaps I was a bit rash in throwing in the towel on my version 2
In any case I think it's been fun so far. Great that we can add ideas for others .
Cheers , Craig


Cheers , Craig
- Dennis Leahy
- Blackwood
- Posts: 872
- Joined: Wed Oct 10, 2007 12:32 am
- Location: Duluth, MN, US
- Contact:
James Mc wrote:...there are so many ways it could be done it was making my head spin. ... Rollers with off center shafts.
I have been working on CAD drawings of adjustable neck joints a bit over the past few months, and two that I came up with are:Craig L wrote:... C'mon guys , thinking caps on !
1.) a variant of the sliding joint that Babicz uses. Crossdowel bolts pass through oval shaped holes in the neck block, allowing up and down movement. I had thought of a couple of ways to move the neck up or down on gear/track (similar to a drill press), but after thinking about the fact that this adjustment probably will be so infrequent, why add all that complexity - just loosen the bolts a bit, tap the neck up or down as needed, and tighten the bolts. One thing I discovered in my CAD drawings is that in spite of Babicz's claim, the neck movement DOES change the effective string length. So, the sliding surfaces of the neck heel and neck block need to be at a very slight angle - I think it was less than 1° - to get the string length to remain almost the same over the normal adjusting distance.
An improvement to option 1 would be that the sliding surfaces were arcs rather than planes, with the arc radius being exactly the distance from the saddle.
2.) a cam system (I think James may be thinking the same.) Draw a circle, then draw another circle within the first circle, but off-center. Extruded into 3D, you have a large roller, with offset smaller rollers sticking off of each face. The end of the neck tenon is drilled or ground out to fit the larger circle; the neck block has a recess for the smaller (cam) circle. Rotating the cam would not only raise or lower the neck, it would also maintain the nut to saddle string length. This (theoretically) would remove the need for upper setscrews to adjust the string length, to get the intonation correct. A cam would need to be created for each scale length. This should be easier to keep the intonation (string length) correct while changing the action height than the 3 setscrew method. The cam would be rotated on the side of the neckblock. Crossdowel bolts would still be used to lock the neck into place, once the adjustment is made. To make it easier to turn, you'd probably have to loosen the crossdowel bolts a bit, even if they have a spring washer beneath their head.
That cam system would probably require a degree of precision in fabricating the neck tenon and neck block that would be beyond many hand builders, but might be a viable option for production guitars or at least someone with CNC technology.
So there are a couple of other ideas. That said, I'm still leaning toward the 3 setscrew method, with a pair of crossdowels and bolts.
Dennis
Another damn Yank!
All this is starting to make my head hurt
For me at least without access to CNC, and really wanting to keep it that way, it's going to have to stay as simple as possible. While I like the idea of being able to do a quick neck adjustment without having to go through the sound hole, I also prefer the look of a slim heel, so the adjuster in a heel like that is going to look a bit out of place.
That said, I think that your idea is really quite good Craig. If I have time this weekend I'll try to build a full scale mock up and see what happens.

For me at least without access to CNC, and really wanting to keep it that way, it's going to have to stay as simple as possible. While I like the idea of being able to do a quick neck adjustment without having to go through the sound hole, I also prefer the look of a slim heel, so the adjuster in a heel like that is going to look a bit out of place.
That said, I think that your idea is really quite good Craig. If I have time this weekend I'll try to build a full scale mock up and see what happens.
Thanks for having that faith in my design Allen,and I sure would appreciate your doing a full on mock- up. As I said above , I may have tossed in the towel too early. A couple of things though mate. Firstly , I'm sure the adjuster can be disguised as a strap button , so that would rectify your concern of having it look out of place.
The other thing I found during my quick half arse mock-up , was that when I first put tension on the thread assembly with the locking nuts , and then turned the adjuster, the heel part started to move out of alignment. On closer inspection , I found a slight burr on one of the nut faces , which threw the whole system out of alignment when turned. I refaced the nut faces on my sandpaper/glass block and did the same with the washers. This seemed to haved fixed the problem. so be aware that all bearing surfaces have to be 'true' including the surface of the wood , as a neck block would be. Again, thanks for giving the system a fair trial and I'm very grateful.
Dennis, I'm in the same camp as Allen , in that I'd sooner have a very simple system with little hardware and the need for some sort of CNC to fabricate it all. This is only my opinion Dennis and ask that you not take any offence .The slotted neck bolt holes as James and yourself mention, is perhaps the most obvious solution. Sounds something like the Babicz system. If you forgo an over the top mechanical system to move the neck up and down ,and end up diving into the soundhole anyways, I 'm thinking that Dave's set screw system wins out because it can also alter the rake , yaw and string speaking length. You say your cam system would also require loosening the neck bolts before adjustment , so the player is still forced to slacken off the strings and making a quick dive through the sound hole.
My thoughts are that the ultimate system wouldn't require slackening of the strings to have to get through the soundhole. I'm sure that wouldn't be much of a hardship for us guitar builder types , but I'm thinking about folks ( guitarists ) who want to quickly lower their string height with out all the fuss . Obviously Doolin is thinking the same way with his new mystery external adjuster.
I'd just like to now recap;
1, Rick Turner's system also known as the Howe Orme system has proven to be functional and externally adjustable. It does however have nearly all the hardware exposed .Not a look everyone embraces.
2, Dave White's system based on Doolins old system demands slackening of the strings and entering the sound hole , but IMO is a fantastic system. Just a shame it's through the soundhole.
3, Dennis and James have a variety of untried systems which appear to require exacting machinery skills/equipment, some of which ( like the drill press idea) are a little over the top ( please , no offence intended guys
) this is only my opinion , others have the right to disagree.
4, The Babicz system. I have little understanding of it , but can't help thinking if there is enough slack in it to be able to move the neck up and down then there is ,,,,,,,,,slack in the system. But as I said , I have little understanding of it. I'd appreciate anyones knowledge on the subject
5, There is the new Doolins mystery external adjuster.
6, My as yet untried version 2 system , and I'm also trying to work on a heelless system when I get time
7, I'm betting there are other systems out there that I don't know of ??
I'm hoping to have not stepped on anyones toes here . If I have , my sincere opologies as it wasn't my intent. I find all input to be valuable. Sometimes others ideas can spark more food for thought.
It may be the case that it does become necessary to enter the soundhole when all other external adjuster ideas have proven fruitless, but lets give it our best shot.
Really looking forward to your findings Allen
Cheers, Craig
The other thing I found during my quick half arse mock-up , was that when I first put tension on the thread assembly with the locking nuts , and then turned the adjuster, the heel part started to move out of alignment. On closer inspection , I found a slight burr on one of the nut faces , which threw the whole system out of alignment when turned. I refaced the nut faces on my sandpaper/glass block and did the same with the washers. This seemed to haved fixed the problem. so be aware that all bearing surfaces have to be 'true' including the surface of the wood , as a neck block would be. Again, thanks for giving the system a fair trial and I'm very grateful.
Dennis, I'm in the same camp as Allen , in that I'd sooner have a very simple system with little hardware and the need for some sort of CNC to fabricate it all. This is only my opinion Dennis and ask that you not take any offence .The slotted neck bolt holes as James and yourself mention, is perhaps the most obvious solution. Sounds something like the Babicz system. If you forgo an over the top mechanical system to move the neck up and down ,and end up diving into the soundhole anyways, I 'm thinking that Dave's set screw system wins out because it can also alter the rake , yaw and string speaking length. You say your cam system would also require loosening the neck bolts before adjustment , so the player is still forced to slacken off the strings and making a quick dive through the sound hole.
My thoughts are that the ultimate system wouldn't require slackening of the strings to have to get through the soundhole. I'm sure that wouldn't be much of a hardship for us guitar builder types , but I'm thinking about folks ( guitarists ) who want to quickly lower their string height with out all the fuss . Obviously Doolin is thinking the same way with his new mystery external adjuster.
I'd just like to now recap;
1, Rick Turner's system also known as the Howe Orme system has proven to be functional and externally adjustable. It does however have nearly all the hardware exposed .Not a look everyone embraces.
2, Dave White's system based on Doolins old system demands slackening of the strings and entering the sound hole , but IMO is a fantastic system. Just a shame it's through the soundhole.
3, Dennis and James have a variety of untried systems which appear to require exacting machinery skills/equipment, some of which ( like the drill press idea) are a little over the top ( please , no offence intended guys

4, The Babicz system. I have little understanding of it , but can't help thinking if there is enough slack in it to be able to move the neck up and down then there is ,,,,,,,,,slack in the system. But as I said , I have little understanding of it. I'd appreciate anyones knowledge on the subject
5, There is the new Doolins mystery external adjuster.
6, My as yet untried version 2 system , and I'm also trying to work on a heelless system when I get time


7, I'm betting there are other systems out there that I don't know of ??
I'm hoping to have not stepped on anyones toes here . If I have , my sincere opologies as it wasn't my intent. I find all input to be valuable. Sometimes others ideas can spark more food for thought.
It may be the case that it does become necessary to enter the soundhole when all other external adjuster ideas have proven fruitless, but lets give it our best shot.
Really looking forward to your findings Allen
Cheers, Craig
- Dennis Leahy
- Blackwood
- Posts: 872
- Joined: Wed Oct 10, 2007 12:32 am
- Location: Duluth, MN, US
- Contact:
Craig, unless you specifically call me an asshole (or arse hole) with no smilie icon
to break the tension, please don't worry about offending me. I'm honestly not defending any of my ideas as good ideas - just some stuff that sprang up in my mind.
That cam idea is the one that I suspect would need (or at least greatly benefit from) CNC capability. It would probably also require someone to machine up the cam piece from metal, with some way to get a tool into the cam and rotate it. If it is a viable idea, it would probably require some big factory to get behind the idea.
The sliding joint could easily be accomplished by hand builders. (By the way, I think Babicz uses some slippery plastic for the "friction" surface, which is why it will go up and down when the captured bolt is turned. Babicz's patent document says "metal or plastic", so maybe it is lapped metal.) I'm no patent attorney, but I would think that a sliding joint without the lower captured bolt would not infringe on Babicz's patent.
From a player's perspective, I do like the concept of the external adjuster, at least for guitars that have a central soundhole. (I'm convinced that I should move the soundhole to one side of the upper bout to get more of the top vibrating. With an offset soundhole, you don't have to slack the strings.
)
For the external adjuster idea:
I would think you'd need to abandon the typical furniture bolt used with crossdowels, as the head is just too big. Maybe a stepped design where the beginning was 5mm and threaded and the last 50mm was 6mm and unthreaded. That would put the unthreaded portion tightly into a 6mm hole through the neck heel. (To reduce play and vibration.)
Maybe use a nylon washer at the bolt head as well as at the nuts.
I would think the strap button would need to be a custom metal tube, threaded on the exterior to go into the wood. The threaded portion OD would have to be slightly bigger than the bolt head it was hiding. I know there is a version of endpin jack that is also a strap button, so I would think along those lines. I'll tell you what - if the strap button could be made aesthetically pleasing, I could warm up to the whole external adjustability concept.
============================
Regardless what you do, I know by experience that you have to keep in mind the string length, or when you alter the action, the intonation will be off - to your ear, not just to a strobe tuner. So, whatever you do you may want to consider that, and utilize setscrews at the top if you cannot resolve that function with other engineering.
Dennis

That cam idea is the one that I suspect would need (or at least greatly benefit from) CNC capability. It would probably also require someone to machine up the cam piece from metal, with some way to get a tool into the cam and rotate it. If it is a viable idea, it would probably require some big factory to get behind the idea.
The sliding joint could easily be accomplished by hand builders. (By the way, I think Babicz uses some slippery plastic for the "friction" surface, which is why it will go up and down when the captured bolt is turned. Babicz's patent document says "metal or plastic", so maybe it is lapped metal.) I'm no patent attorney, but I would think that a sliding joint without the lower captured bolt would not infringe on Babicz's patent.
From a player's perspective, I do like the concept of the external adjuster, at least for guitars that have a central soundhole. (I'm convinced that I should move the soundhole to one side of the upper bout to get more of the top vibrating. With an offset soundhole, you don't have to slack the strings.

For the external adjuster idea:
I would think you'd need to abandon the typical furniture bolt used with crossdowels, as the head is just too big. Maybe a stepped design where the beginning was 5mm and threaded and the last 50mm was 6mm and unthreaded. That would put the unthreaded portion tightly into a 6mm hole through the neck heel. (To reduce play and vibration.)
Maybe use a nylon washer at the bolt head as well as at the nuts.
I would think the strap button would need to be a custom metal tube, threaded on the exterior to go into the wood. The threaded portion OD would have to be slightly bigger than the bolt head it was hiding. I know there is a version of endpin jack that is also a strap button, so I would think along those lines. I'll tell you what - if the strap button could be made aesthetically pleasing, I could warm up to the whole external adjustability concept.
============================
Regardless what you do, I know by experience that you have to keep in mind the string length, or when you alter the action, the intonation will be off - to your ear, not just to a strobe tuner. So, whatever you do you may want to consider that, and utilize setscrews at the top if you cannot resolve that function with other engineering.
Dennis
Another damn Yank!
- Dennis Leahy
- Blackwood
- Posts: 872
- Joined: Wed Oct 10, 2007 12:32 am
- Location: Duluth, MN, US
- Contact:
Craig, hit the link I provided above. Sign up (free) and you can view the PDF file (with drawings.)Craig L wrote:...The Babicz system. I have little understanding of it , but can't help thinking if there is enough slack in it to be able to move the neck up and down then there is ,,,,,,,,,slack in the system. But as I said , I have little understanding of it. I'd appreciate anyones knowledge on the subject
Dennis
Another damn Yank!
You guys have got me thinking about this now, as if I didn't have enough to do
If you used a cam, you might be able to adjust it through a sound port in the upper bout. So you'd have the best of both worlds, internal adjustment without going in through the soundhole.
Ok, so maybe I haven't been thinking about it too hard

If you used a cam, you might be able to adjust it through a sound port in the upper bout. So you'd have the best of both worlds, internal adjustment without going in through the soundhole.
Ok, so maybe I haven't been thinking about it too hard

Dennis , don't get me started on soundholes/soundboards etc. It's a huge subject of mine and I've been giving it great thought for years now. Definatley another thread topic , but please not now !
The screws I have here are 6 mm. hex socket head. Their head size is about that in my drawing 9.5 mm. I think. Their shank is tapered down to make the thread . The screw becomes the same diameter full length. The problem is they need have a longer thread than the 25 mm. shelf bought variety. I thought I could make the thread longer but maybe the shank has to be reduced in diameter before hand. I'l see if longer thread 3" ( 75mm.) hex socket screws are available at Bearfast , but up here in the bush , I have my doubts.
For my half arse mock-up, I had to use Imperial thread ,as it's all I had handy with a long enough thread. I'm sure the finer thread of the metric screws would have behaved better.
Yes I have put the slippery washers under the screw head ( with machine washer ) and also the locking nuts ( with machine washer)
As to the change in string length when altering the neck angle :.With the tiny amount of adjustment that may be required after the guitar is 'run in ' and well set up ,I can't see that being a huge problem , but maybe I'm wrong here . How much do the strings gain in length when say you lower the strings around half a millimeter over the twelfth fret ?
Paul ! you mad Scientist ! You have it in a nut shell. That sounds a fantastic solution . Maybe you could even turn yourself a nice wooden one to match your bindings !.. I turn little things like that by chucking it in my drill press and use a file
Works well !
Oh ! and thanks for the Babicz Link Dennis

The screws I have here are 6 mm. hex socket head. Their head size is about that in my drawing 9.5 mm. I think. Their shank is tapered down to make the thread . The screw becomes the same diameter full length. The problem is they need have a longer thread than the 25 mm. shelf bought variety. I thought I could make the thread longer but maybe the shank has to be reduced in diameter before hand. I'l see if longer thread 3" ( 75mm.) hex socket screws are available at Bearfast , but up here in the bush , I have my doubts.
For my half arse mock-up, I had to use Imperial thread ,as it's all I had handy with a long enough thread. I'm sure the finer thread of the metric screws would have behaved better.
Yes I have put the slippery washers under the screw head ( with machine washer ) and also the locking nuts ( with machine washer)
As to the change in string length when altering the neck angle :.With the tiny amount of adjustment that may be required after the guitar is 'run in ' and well set up ,I can't see that being a huge problem , but maybe I'm wrong here . How much do the strings gain in length when say you lower the strings around half a millimeter over the twelfth fret ?
Paul ! you mad Scientist ! You have it in a nut shell. That sounds a fantastic solution . Maybe you could even turn yourself a nice wooden one to match your bindings !.. I turn little things like that by chucking it in my drill press and use a file

Oh ! and thanks for the Babicz Link Dennis
- Dennis Leahy
- Blackwood
- Posts: 872
- Joined: Wed Oct 10, 2007 12:32 am
- Location: Duluth, MN, US
- Contact:
When I did a CAD "mock-up" of my guitar's adjustable neck joint (using Grant Goltz's joint, minus the spring washer), I think I remember that the maximum string length change would be slightly under .004" (about .1mm) in length. I guessed that I would not be able to hear the difference. I found out I was wrong.Craig L wrote: As to the change in string length when altering the neck angle :.With the tiny amount of adjustment that may be required after the guitar is 'run in ' and well set up ,I can't see that being a huge problem , but maybe I'm wrong here . How much do the strings gain in length when say you lower the strings around half a millimeter over the twelfth fret ?
First, a quick disclaimer or two... I have only built one guitar. And (talk about dumb arse) when I glued the bridge down, I misplaced it. That meant that the 6mm wide saddle was filed back as far as I could go, to try to get the intonation exactly correct. I got it really close on all strings, close to "dead-on" on some strings (by ear - I don't have a strobe tuner.) So, my starting point was not *perfect*.
OK, so a few weeks ago, I noticed the action had gotten a bit high, and worse, I really noticed that the intonation was off. So, I dropped the action down relatively low (back to the original action, maybe lowered the action by .75mm), and there was a vast improvement in intonation.
So, I'm convinced that I do need to modify the plan for future builds, and so far, the upper setscrews seem like the way to go.
By the way, I had hoped to get another guitar done before I "whack it off" (the bridge, that is), refinish the top and reglue the bridge in the correct position. It will be nice to actually get the benefits of a 6mm wide (new) saddle!
Dennis
Another damn Yank!
Hey Craig... I'm an active greenie based in North Queensland, I have a death threat file an inch thick, so no don't ever worry about offending me.
Throwing up ideas so others can shoot them down is the best alternative to building extensive prototype. When I have some time over the weekend I'll sketch out an idea for a simple scissor jack based system with the adjustment bolt hidden under the heal cap.
Throwing up ideas so others can shoot them down is the best alternative to building extensive prototype. When I have some time over the weekend I'll sketch out an idea for a simple scissor jack based system with the adjustment bolt hidden under the heal cap.
Dennis ,
My intentions for the external adjuster would be to tweak the action height when required. I think I'm like most guitarists in that when my ideal action ( in my case 2.4 mm. above the twelfth fret on the 6 th string ) ,gets raised by humidity changes to say 2.65 mm. , I really notice it and am generally pissed off
. That's .25 mm. we are talking about ,and I have found that a common figure in my neck of the wood anyway. . and doesn't seem a whole lot to lower the strings.
I 've also been thinking about the geometry of the whole thing If I were to have my pivot pins as high as I can on the heel as intended , and considering that arc , to lower or raise the action or tweak it just a little , I can't see that putting the intonation out enough to even be concerned about.I maybe wrong here
We have just gone through a summer of heaps of rain . Rained nearly every day . High humidity ( 70's and 80's ) for about two months . My guitars with their 2.4 mm. action went to a 3 mm. action. That's at extremes I suppose. I have seen these same figures on my guitars repeat them selves time and againduring the wet seasons . In such a case where this humidity was expected to last a while , I can't see too much hardship in getting into the soundhole and adjusting the top pivot set screws ( Should and IF that becomes necessary ). Nearly all the time though ,I could easily get away with just a quick tweak.
BTW the 6mm. screws I have are 5.85 mm. diameter. A 15/64 bit is 5.95 mm. which is getting closer to keeping the screw snug in the heel hole and thereby firming up the system.
G'day James, Geez I'd hate to have a death threat file on me
, particularly an inch thick
I take your point of throwing up ideas to be shot down by others , but so far I have found these great guys to be more productive help than look at it with sceptical eyes. I don't want to be here defending a design , but rather, accept the sound suggestions they put forward. At the end of the day , it'll either work or it won't work. It also puts the design as not mine alone ,but something we all worked on together , and I reckon that's fantastic mateship and loads of fun . Besides ,many brains , more knowledge.
I'm really keen on keeping this design SIMPLE. An engineering feat will have to take a back seat as it probably is beyond what most of us casual builders can achieve. Besides most brilliant designs are quite basic.
Cheers to all you guys, Craig
My intentions for the external adjuster would be to tweak the action height when required. I think I'm like most guitarists in that when my ideal action ( in my case 2.4 mm. above the twelfth fret on the 6 th string ) ,gets raised by humidity changes to say 2.65 mm. , I really notice it and am generally pissed off

I 've also been thinking about the geometry of the whole thing If I were to have my pivot pins as high as I can on the heel as intended , and considering that arc , to lower or raise the action or tweak it just a little , I can't see that putting the intonation out enough to even be concerned about.I maybe wrong here
We have just gone through a summer of heaps of rain . Rained nearly every day . High humidity ( 70's and 80's ) for about two months . My guitars with their 2.4 mm. action went to a 3 mm. action. That's at extremes I suppose. I have seen these same figures on my guitars repeat them selves time and againduring the wet seasons . In such a case where this humidity was expected to last a while , I can't see too much hardship in getting into the soundhole and adjusting the top pivot set screws ( Should and IF that becomes necessary ). Nearly all the time though ,I could easily get away with just a quick tweak.
BTW the 6mm. screws I have are 5.85 mm. diameter. A 15/64 bit is 5.95 mm. which is getting closer to keeping the screw snug in the heel hole and thereby firming up the system.
G'day James, Geez I'd hate to have a death threat file on me



I take your point of throwing up ideas to be shot down by others , but so far I have found these great guys to be more productive help than look at it with sceptical eyes. I don't want to be here defending a design , but rather, accept the sound suggestions they put forward. At the end of the day , it'll either work or it won't work. It also puts the design as not mine alone ,but something we all worked on together , and I reckon that's fantastic mateship and loads of fun . Besides ,many brains , more knowledge.
I'm really keen on keeping this design SIMPLE. An engineering feat will have to take a back seat as it probably is beyond what most of us casual builders can achieve. Besides most brilliant designs are quite basic.
Cheers to all you guys, Craig
Last edited by Craig on Sun Mar 09, 2008 9:26 pm, edited 2 times in total.
- Dave White
- Blackwood
- Posts: 452
- Joined: Mon Nov 12, 2007 3:10 am
- Location: Hughenden Valley, England
- Contact:
That Mike Doolin is a real clever cookie isn't he
You guys crack me up sometimes - agonising over having an allen bolt head peeking at you from inside the heel but quite happy to cover it up with a strap button which is visually "proper and accepted". When you are in adjustable neck territory and with paying customers then I think that you have already left "traditional cosmetics" way behind - after all there is the neck set into a pocket and free floating fingerboard extension. In some ways I like the "in your face" proud to show it cosmetics of Rick's take on the Howe-Orme system. I think reliability and ease of adjustability will be key things.
It's not a big deal for me to loosen the strings and bolts to adjust - it reminds me that I need to change the strings, the biggest bang for buck in changing a guitars tone for the better. This would be intimidating for most players though - and a bit dangerous as you wouldn't want them loosening neck bolts at random.
I think that swapping ideas here is fantastic and is a great part of the evolution/invention pool - most of what I do in my building has come from places like this or looking at websites and guitars of builders I admire. I love the sharing attitude of the building community - which probably comes from the fact that almost nobody makes any money doing it and does it for pure love and joy
After a time though, the only way to progress is to prototype, build. observe and adapt - the wonderful feedback loop. Oh and of course, if you are that way inclined, share with other builders
On a personal rant note, the thing that pisses me off most is when other builders fob me off with the "I've built more than you've had hot dinners" and don't address fundimental issues/questions. I have one of these brewing in a Baritone post on the OLF at the moment. When I get into these a lot of people think I'm an argumentative, obnoxious jerk when in fact I'm just stubborn and want to hear reasoned arguments. Then again . . . they may be right about me

You guys crack me up sometimes - agonising over having an allen bolt head peeking at you from inside the heel but quite happy to cover it up with a strap button which is visually "proper and accepted". When you are in adjustable neck territory and with paying customers then I think that you have already left "traditional cosmetics" way behind - after all there is the neck set into a pocket and free floating fingerboard extension. In some ways I like the "in your face" proud to show it cosmetics of Rick's take on the Howe-Orme system. I think reliability and ease of adjustability will be key things.
It's not a big deal for me to loosen the strings and bolts to adjust - it reminds me that I need to change the strings, the biggest bang for buck in changing a guitars tone for the better. This would be intimidating for most players though - and a bit dangerous as you wouldn't want them loosening neck bolts at random.
I think that swapping ideas here is fantastic and is a great part of the evolution/invention pool - most of what I do in my building has come from places like this or looking at websites and guitars of builders I admire. I love the sharing attitude of the building community - which probably comes from the fact that almost nobody makes any money doing it and does it for pure love and joy

After a time though, the only way to progress is to prototype, build. observe and adapt - the wonderful feedback loop. Oh and of course, if you are that way inclined, share with other builders

On a personal rant note, the thing that pisses me off most is when other builders fob me off with the "I've built more than you've had hot dinners" and don't address fundimental issues/questions. I have one of these brewing in a Baritone post on the OLF at the moment. When I get into these a lot of people think I'm an argumentative, obnoxious jerk when in fact I'm just stubborn and want to hear reasoned arguments. Then again . . . they may be right about me

Dave White
[url=http://www.defaoiteguitars.com]De Faoite Stringed Instruments[/url]
[url=http://www.defaoiteguitars.com]De Faoite Stringed Instruments[/url]
One concern I have with putting the adjustment point at the bottom of the heel is that it seems like doing so could create a weak point. This is a narrow area of timber with cross grain, would putting it here create a situation where a knock on the neck could crack the timber at the adjustment point??
Here's some pix of the Taylor joint.
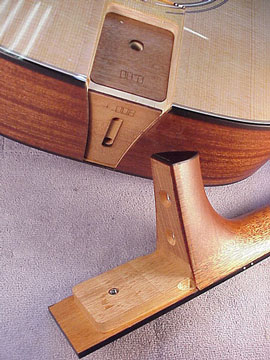
Everything is CNC'd to a relativly close tolerance so one doesn't see many small luthiers using it (especially Sam! She's really small... pleeease don't send your husband again
)
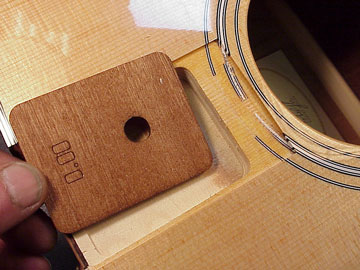
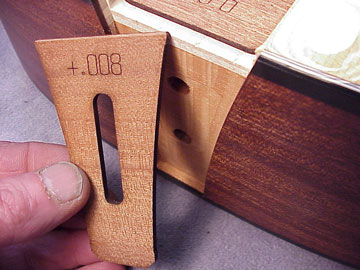
The double spacers allow intonation to be adjusted in bringing the neck up to proper level.
Intonation is a real problem in the pivot type adjusters. The Doolin system takes this into account and probably the best I've seen for a custom builder! Yes, a few thou makes a difference, the cosine error adds up fast believe it or not!
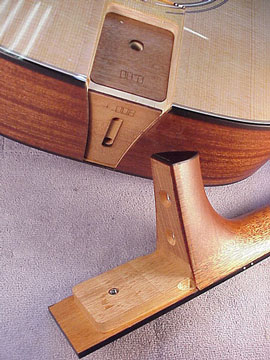
Everything is CNC'd to a relativly close tolerance so one doesn't see many small luthiers using it (especially Sam! She's really small... pleeease don't send your husband again


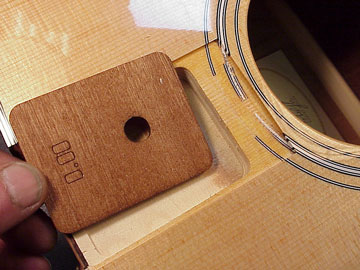
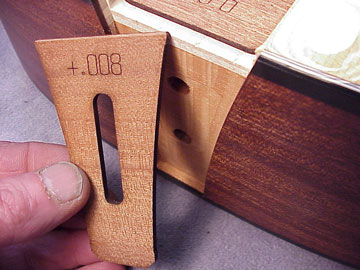
The double spacers allow intonation to be adjusted in bringing the neck up to proper level.
Intonation is a real problem in the pivot type adjusters. The Doolin system takes this into account and probably the best I've seen for a custom builder! Yes, a few thou makes a difference, the cosine error adds up fast believe it or not!
G'day Dave,
Sounds like you've just come out of a battle
I don't think we have ever had a " I've built more guitars than you've had hot dinners "bullshit thing here on the ANZLF. As an administrator , I couldn't see me tolerating it either. I'll bet the others guys feel the same way.
Hey Dave, we don't think you're an Argumentative obnoxious jerk mate
I don't know that a guitar with a floating fretboard looks all that different visually than a glued down extension to the average person,but an exposed screw may get noticed more. It's just aesthetics , but why not make it look as slick as possible. I don't see that as us being funny
James , I see that point in the heel as a well supported area because of the clamping affect the hardware is doing.
Cheers Craig
Sounds like you've just come out of a battle

Hey Dave, we don't think you're an Argumentative obnoxious jerk mate


I don't know that a guitar with a floating fretboard looks all that different visually than a glued down extension to the average person,but an exposed screw may get noticed more. It's just aesthetics , but why not make it look as slick as possible. I don't see that as us being funny

James , I see that point in the heel as a well supported area because of the clamping affect the hardware is doing.
Cheers Craig
Last edited by Craig on Sun Mar 09, 2008 9:42 pm, edited 1 time in total.
Sorry Billy , I was posting the same time as yourself.
I'll have a closer look at the geometry Billy , and thanks for that. As I said above , I see the external adjuster as a tweaker , whereas the internal pivet pins can handle major changes.
Just had another thought ,,,, I've got plenty of tie wire here . Howzabout a Cobb and Co. hitch ! . A twist to the left to lower the action and a twist to the right to raise it. People wouldn't be left guessing what country it was made
.
I'll have a closer look at the geometry Billy , and thanks for that. As I said above , I see the external adjuster as a tweaker , whereas the internal pivet pins can handle major changes.
Just had another thought ,,,, I've got plenty of tie wire here . Howzabout a Cobb and Co. hitch ! . A twist to the left to lower the action and a twist to the right to raise it. People wouldn't be left guessing what country it was made


.
- Dave White
- Blackwood
- Posts: 452
- Joined: Mon Nov 12, 2007 3:10 am
- Location: Hughenden Valley, England
- Contact:
Craig,
It's not really bullshit, it's more about avoiding factually supporting a point of view. If Lance had said "Your soundclip sucks and is so flabby sounding that it is the best evidence to support Dave B's argument and ..." then sort of fair dinkum as you'd say. I'd then ask why he doesn't use 220lb string tension on his normal guitars.
About the floating fretboard - some people who are used to glued down one's won't contemplate a floating one unless they can get it to pass a candle test
I actually think that you can make adjustable neck joint guitars an aesthetic in their own right rather than trying to hide it and Mike Dollin's take looks very elegant aesthetically to me - which is why you were cracking me up:

Every one has a different take on "aethetics" though which is a good thing. Functionally I'm not sure that I'd want the strap pressure to be bearing on such a crucial part of the system and - as I think Allen was suggesting - you'd have to have the strap button centre hollow so that you could adjust with it in place. Otherwise the player has something else to unscrew and potentially loose
Dennis,
The change in string length that adjusting around the top two pivots brings into play for the range of action height changes by adjusting the bottom screw(s) are so minute as to be "angels on the head of a pin" territory for this argumentative, obnoxious jerk
The average players fingers are more than capable of dealing with this - as you have to do anyway for different action settings. Play the higher settings with the same technique as the low and you will sharpen the notes slightly.
Billy,
As to the top pivot points, Mike Doolin (on his old system) used to superglue them in place when they were set as he didn't want them to budge, so they are not adjusters on his system. I have found other ways to make them secure but still adjustable but this is fiddly and requires more hardware. Rick T's is as simple as they come and all adjustable.The Taylor NT system is more a way of doing easy CNC based neck resets when required. You could keep changing shims to allow for humidity changes and adjust action height but you would need to keep removing the strings AND the neck to do this - not a KISS player thing so I wouldn't "technically" call it an adjustable neck system as such.
I love this place
It's not really bullshit, it's more about avoiding factually supporting a point of view. If Lance had said "Your soundclip sucks and is so flabby sounding that it is the best evidence to support Dave B's argument and ..." then sort of fair dinkum as you'd say. I'd then ask why he doesn't use 220lb string tension on his normal guitars.
About the floating fretboard - some people who are used to glued down one's won't contemplate a floating one unless they can get it to pass a candle test


Every one has a different take on "aethetics" though which is a good thing. Functionally I'm not sure that I'd want the strap pressure to be bearing on such a crucial part of the system and - as I think Allen was suggesting - you'd have to have the strap button centre hollow so that you could adjust with it in place. Otherwise the player has something else to unscrew and potentially loose

Dennis,
The change in string length that adjusting around the top two pivots brings into play for the range of action height changes by adjusting the bottom screw(s) are so minute as to be "angels on the head of a pin" territory for this argumentative, obnoxious jerk

Billy,
As to the top pivot points, Mike Doolin (on his old system) used to superglue them in place when they were set as he didn't want them to budge, so they are not adjusters on his system. I have found other ways to make them secure but still adjustable but this is fiddly and requires more hardware. Rick T's is as simple as they come and all adjustable.The Taylor NT system is more a way of doing easy CNC based neck resets when required. You could keep changing shims to allow for humidity changes and adjust action height but you would need to keep removing the strings AND the neck to do this - not a KISS player thing so I wouldn't "technically" call it an adjustable neck system as such.
I love this place

Dave White
[url=http://www.defaoiteguitars.com]De Faoite Stringed Instruments[/url]
[url=http://www.defaoiteguitars.com]De Faoite Stringed Instruments[/url]
- Dennis Leahy
- Blackwood
- Posts: 872
- Joined: Wed Oct 10, 2007 12:32 am
- Location: Duluth, MN, US
- Contact:
I guess that the one thing about the external adjustment screw is that I find it visually jarring. In a way, it looks amateurish or like a mistake to me. Oh, I know it is small, and compared to something like an onboard preamp sticking out through a guitar side, it is really nothing at all. I'm admitting it is a prejudice - and I'm trying to get over it. If I live long enough, I may sell a guitar or two, but I have no plans to become a professional luthier. So, I'm thinking in terms of my own aesthetic, not the buying public. With the buying public in mind, I suppose a luthier could easily offer buyers two different solutions on custom guitars: internal or external adjustment. Let them decide. Then, (as of this moment), what I would offer is a setscrew in wood, external or internal, their choice.
I know this is not where most of you guys would buy setscrews but go to McMaster Carr, type in setscrew, and take a look at the one with the "extended point."

I'd be willing to bet a brick of Velveeta cheese that with somewhere in the range of 19mm to 25mm of thread going through wood, the setscrew will stay in place. (I'd epoxy in a small piece of metal for the opposing surface, like Fleishman and Doolin.)
If you were convinced that the setscrew going through wood would eventually cause problems, then instead you could drill a larger hole, and epoxy in an internally threaded metal sleeve (like a coupling nut) for the setscrew.
The neck would still be secured with with crossdowels and furniture bolts, but if you add a spring washer

under the head of the bolts, not cranking the bolt so tightly that the washer fully flattens, then you should be able to make a minor setscrew adjustment without loosening the furniture bolts. A tiny dab of Loctite or other thread locking goo on the crossdowel should keep the furniture bolt from spinning due to vibration, even though it is not fully cranked down. The spring washer would have to be chosen carefully - strong enough to resist flattening due the string pull but weak enough to allow a turn of the setscrew to expand or compress it a tiny bit.
Floating Fingerboards:
Yes, the floating fingerboard is part of the equation, both in terms of engineering and aesthetics. Following Grant Goltz's lead, I made my fingerboard extension nearly touching the top. (As a funny aside, both Grant and I shipped a guitar to Wm. Cumpiano, as part of a contest thingy, for his critique. He was too busy hating my guitar for it's departure from tradition to make mention of the fingerboard at all, but he did wag a finger at Grant for not properly gluing down his fingerboard extension. He had no clue that he was looking at a pair of guitars with adjustable necks.)
Anyway, I did not have an upper transverse brace in my guitar (to try to get more of the top active), and found that if I set the neck so the fingerboard extension was just a few thousandths above the top, that I got buzzing during some vigorous playing. So, for me, the fingerboard extension had to be lifted. That forces me to look at the aesthetic, and now wonder if an obvious gap makes more sense aesthetically.
Dennis
I know this is not where most of you guys would buy setscrews but go to McMaster Carr, type in setscrew, and take a look at the one with the "extended point."

I'd be willing to bet a brick of Velveeta cheese that with somewhere in the range of 19mm to 25mm of thread going through wood, the setscrew will stay in place. (I'd epoxy in a small piece of metal for the opposing surface, like Fleishman and Doolin.)
If you were convinced that the setscrew going through wood would eventually cause problems, then instead you could drill a larger hole, and epoxy in an internally threaded metal sleeve (like a coupling nut) for the setscrew.
The neck would still be secured with with crossdowels and furniture bolts, but if you add a spring washer

under the head of the bolts, not cranking the bolt so tightly that the washer fully flattens, then you should be able to make a minor setscrew adjustment without loosening the furniture bolts. A tiny dab of Loctite or other thread locking goo on the crossdowel should keep the furniture bolt from spinning due to vibration, even though it is not fully cranked down. The spring washer would have to be chosen carefully - strong enough to resist flattening due the string pull but weak enough to allow a turn of the setscrew to expand or compress it a tiny bit.
Floating Fingerboards:
Yes, the floating fingerboard is part of the equation, both in terms of engineering and aesthetics. Following Grant Goltz's lead, I made my fingerboard extension nearly touching the top. (As a funny aside, both Grant and I shipped a guitar to Wm. Cumpiano, as part of a contest thingy, for his critique. He was too busy hating my guitar for it's departure from tradition to make mention of the fingerboard at all, but he did wag a finger at Grant for not properly gluing down his fingerboard extension. He had no clue that he was looking at a pair of guitars with adjustable necks.)
Anyway, I did not have an upper transverse brace in my guitar (to try to get more of the top active), and found that if I set the neck so the fingerboard extension was just a few thousandths above the top, that I got buzzing during some vigorous playing. So, for me, the fingerboard extension had to be lifted. That forces me to look at the aesthetic, and now wonder if an obvious gap makes more sense aesthetically.
Dennis
Another damn Yank!
That's OK just don't let it happen again!Craig L wrote:Sorry Billy , I was posting the same time as yourself.






I agree about the Doolin system I think it's addresses quite well the total problem of adjustble necks. I don't "like" the adjust screw being easily viewable but it ain't a deal breaker, better to see the adjuster than not to have one at all!
I looked into this quite heavily a couple of years ago and think part of the fasination with it is, it seems to be an easy goal to obtain but really isn't considering string length imperatives.
I like the Taylor sytem for it's accuracy but in a place that requires adjustment with high humidity extremes it's not as easy to get too as Doolins that's for sure!
Who is online
Users browsing this forum: No registered users and 3 guests