Page 1 of 2
First overseas commissions completed.
Posted: Sat Jul 11, 2009 4:44 pm
by Allen
You might have seen a few progress pictures of these 2 guitars in other threads. They were completed this past week, and I'm very please at how they've turned out.
I was given some fairly firm guidelines as to what was wanted. This included East Indian Rosewood, German Spruce tops. Cocobolo bindings, Ebony fretboard and bridge. Herringbone purfling, and absolutely no bwb purfs.
Nut width and neck profile were also a bit out of the norm,and the closest specs I could find were the 1930's Martin 000 neck profile. It's said to be the fingerpickers neck of choice, and I must say that it fits my larger hand much better than a 1 3/4 width nut.
The instruments were to be fairly conservative in design and appearance. The only difference between the two is the scale length, and internal bracing to accommodate same.
As usual, the finish in Mirotone 3220 over WEST Systems epoxy pore filler. 5 coats thinned 50/50, rubbed back after a week, and another 5 coats. Buffed after 2 weeks. Then a final gloss up after I got all the set up done a week later.
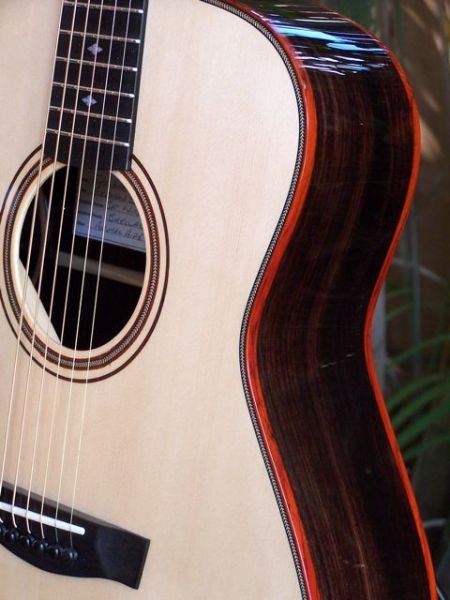
Posted: Sat Jul 11, 2009 5:03 pm
by Bob Connor
Bloody beautiful Allen.
If they were mine they'd be going straight in the pool room.
Much difference in the sound given the different scales?
Posted: Sat Jul 11, 2009 5:15 pm
by Allen
The highest praise an Aussie can give. Thanks Bob.
The Auditorium (24.9" scale)has a lot more bottom end than the Orchestral (25.4" scale). The Orchestral has a nice clear voice, that really seems to carry. I took them both into my favorite music shop today, looking for some cases to ship in. They gave them a play, and said that they're my best sounding guitars yet..
I'm going to get Alan to do some recordings for me next weekend. Will post some samples when I have them.
Posted: Sat Jul 11, 2009 5:36 pm
by sebastiaan56
Very, very nice Allen. I look forward to the sound clips.
Congrats on getting paid for doing it as well!
Posted: Sat Jul 11, 2009 6:19 pm
by ozziebluesman
Super looking guitar there Allen. Congratulations on such fine workmanship. I look forward to a play shortly.
Cheers
Alan
Posted: Sat Jul 11, 2009 7:11 pm
by J.F. Custom
Beautiful Allen.
Very clean, crisp work. Great to hear
you are happy with the results too.
I always find finishing an instrument and seeing it go to be a strange experience. It's like you have put so much time and effort into each aspect of it that it has become part of you - that which you then have to let go of. At the same time, I'm chomping at the bit and inspired to start the next project... or is that finish the other half dozen? All the time, it's what you're working toward so you know it's coming, but it's still hard, yet we go back for more, again and again. Cognitive dissonance of a luthier.
Cheers,
Jeremy.
Posted: Sat Jul 11, 2009 8:10 pm
by Taffy Evans
Terrific Allen, as always. Everything comes together well and they look great, and to have a great sound too so early in their life must be pleasing also.
Great work.
Posted: Sat Jul 11, 2009 8:21 pm
by Dominic
Nice work Allen. What do you think it was that you did this time around to mprove the tone from previous guitars? What kind of of bracing did you use and what did you do to tune the plates.
Cheers
Dom
Posted: Sat Jul 11, 2009 9:05 pm
by Allen
I got Kent Everetss voicing DVD's and followed his method. Kept more wood in the tops than I have previously. and scalloped the braces without tapering them into triangular shapes. The X-brace is also very forward shifted compared to previous builds.
His theory, as far as I can discern is that you want a top to have some wood in it so that it has some room to develop. It's also the first time that I've used German Spruce, but I've got no idea if that has made a difference.
First off, I kept thining the top and giving it the "wobble" test, as in Robbie O'brian's video. I'm guessing he learnt this from Kent. When it sounds like a piece of sheet metal that is getting flexed, then stop thinning. Or if it has reached your limit for how thin you're willing to go, then stop.
One top was taken down to .130" the other to .125".'
Then the bracing is scalloped and top is tap tested to get a long, ring, that has an initial attack, then returns but more subtle. What surprised me is that if you listen carefully it does work that way when the braces get to a certain profile.
Finally, after binding, the outer edge of the lower bout is thinned a bit.
I also kept the sides and back thicker, wanting them to be very stiff, with the solid linings. Taking a bit of advice from Dave White about making the box heavier.
Posted: Sat Jul 11, 2009 10:39 pm
by Ricardo
Allen, Your workmanship look s excellent! I would love to hear a sound clip, will you be posting one?
Posted: Sat Jul 11, 2009 11:20 pm
by Lillian
They are beautiful Allen. Eye candy. Sounds like I have another DVD to order. Thanks for sharing.
Posted: Sat Jul 11, 2009 11:38 pm
by Dave White
Allen,
Congratulations on your commission - a really tasy looking pair of guitars there. It's nice to watch your building skills progress with each instrument and with Bob/Dave to paraphrase Collin Welland from the "Chariots of Fire" year - "Watch out - the Ozzies are coming!!".
I really agree about making instruments with a view to where the sound will be a year or so down the track as things settle and mature compared with the "instant hit" (they still sound great from new) and also to leaving tops thicker than many builders do in the centre, which is one firm base for building the mids/trebles in my view.
Well done again.
Posted: Sat Jul 11, 2009 11:58 pm
by Hesh1956
Re: First overseas commissions completed.
Posted: Sun Jul 12, 2009 12:49 am
by John Maddison
Allen wrote: ... the closest specs I could find were the 1930's Martin 000 neck profile.
Allen
Are these profiles displayed somewhere in cyber_web_land?
Exquisite work, as always btw
Cheers
Posted: Sun Jul 12, 2009 2:18 am
by Rick Turner
Very, very nice.
A thought...stiff back and sides makes for a guitar that projects forward, hence the guitar is loud to an audience, but not so much for the player. That can actually make for a hard sell...guitar players want to really feel enveloped, especially if they are primarily living room players, and that first impression can make or break a sale.
I've taken the stiff back and sides thing to an extreme just this side of going to a Smallman-style laminated back. To give something back to the player, I put in side ports. Seems to give the best of both worlds to player and audience.
However, I now ask potential clients how they intend to use the guitar. If they are primarily home-bound livingroom players or they just play at small parties, I'll go thin with back and sides to give more of that lush warmth to the player. You can also build a smaller guitar that has bottom end for the player that way. "0" and "00" guitar sizes can be amazing in a small room when build lightly. That I really learned from some mid 18th Century Martins and my 1890s Howe Ormes.
Posted: Sun Jul 12, 2009 6:06 am
by Localele
They look great Allen.And as always it is a pity they can't hang around and be played in a bit more to see how they develop.
Posted: Sun Jul 12, 2009 6:32 am
by Allen
John, you can get
neck templates from Tracey at Luthier Supplies.
Hesh, the nut is 46 mm wide or 1 13/16'. And making them shinny is easy. Taking the pictures so that you don't just see glare is far more difficult.
I wasn't sure about the bindings going with the IRW, but I'm pleased with how the colors play off of each other. It was rather different to build to someone else's taste. In one sense it's frustrating in that I think something else would look better, but liberating in that I don't have to worry too much about it, as it's what the customer wants.
Posted: Sun Jul 12, 2009 8:40 am
by Nick
Bob I'd like to request an emoticon whereby it's jaw drops
all the way to the floor, & I'll take two thanks.

Very smooth Mr McFarlen! beautiful, clean execution and the finish is Gaaaaawwwgeous. I like your blending of the neck profile into the headstock volute area, looks a very smooth & comfortable place for the hand.
I got some West System for laminating my CF/spruce braces together, looks like I now know how I'm going to pore fill it

Posted: Sun Jul 12, 2009 9:17 am
by Paul B
Awesome, beautiful work.
The Coco and EIR look great together, gonna have to try that combo at some point.
Can't wait to hear what they sound like.
Posted: Sun Jul 12, 2009 9:58 am
by Dominic
Allen, Kent's DVD is good isn't it. The first one I made after watching it all was so much better sounding than previous attempts. Just gives some context to tuning so you kind of know where you are going.
I have an OM and 2 L-00s currently being made following the tips in the dvd and I have high hopes for them both. Boxes sound very lively.
Cheers
Dom
Posted: Thu Jul 16, 2009 5:25 pm
by James Mc
Hi Allen
First… great looking guitars! I love the clean classic look and that head shape works so well with it.
I was wondering how you found building for someone who had firm ideas on what they wanted compared to building when you have all the creative power? As someone who only builds for fun and gives them as gifts, I think it would be an interesting challenge to build to a set of requirements onther than what I though would work best (well I sold the last one but that doesn't count, as it was unintentional… sold it by accident).
Cheers
James
Posted: Thu Jul 16, 2009 6:37 pm
by Allen
It's a bit daunting in a way James. Obviously the client has pretty firm ideas about some aspects that needed to be as spot on as I could make them. And I'm hoping that I pulled them off. Some things like nut width, scale and what not are pretty easy, you just need to be sure of the measurements, and believe me, I checked them far more than twice.
The aesthetics though are something else. I'd have never thought of using the Cocoblolo with IRW Even when I had them laying on the bench together would I have thought that they'd work, but I'm glad that this was insisted upon. I'd never have used the Cocobolo in the rosette, and after using it, I'd never use it again. It's a total pain in the arse to use in those dimensions, and in spruce. It bleeds color like nothing I've ever come across, and it's the one thing that I'm not too proud of on these instruments.
Then there is the uncertainty that the instrument will have the sound and playability and all kind of other things that I don't want to worry about when a client has plunked down hard cash up front. Much different when you build for the pure joy of it, and if someone picks up an instrument and loves the way it plays and sound.
There is also a difference to how I feel when I'm out in the shed working away. While there is a great deal of pride and satisfaction that someone want to pay you for your work, it's just a bit of a different mind set to going out and puttering away without a dead line.
Posted: Thu Jul 16, 2009 11:07 pm
by Kim
Allen,
These are wonderful looking guitars. They have simple elegance and ooze class, has anyone ever mentioned that you do a pretty good finish job
Well done mate, we wait with baited breath for the sound files, mak'em long ones please Alan, we all love the way you play.
Cheers
Kim
Wow
Posted: Fri Jul 17, 2009 1:02 am
by Corky Long
What a beautiful pair of guitars.... Gives me something to shoot for. Congratulations.
Posted: Fri Jul 17, 2009 2:50 am
by Stephen Kinnaird
Dadgum, those are lovely.
It's all been said, but let me just pile on, Allen: beautiful work!
As picky as your customer was, did he specify that the herringbone in the rosette run counter closckwise?
If not, how did you choose the direction?
(Anal question, I know, but hey--that's what we are, right?)
Congrats,
Steve