How to us hide glue for attaching large plates?
How to us hide glue for attaching large plates?
Ok, I'm not to bad at using hide glue for braces, and linings, but I'm unsure how you would go about glueing a top or back to a guitar using hide glue. I don't think that it's going to make an instrument any better than using Titbond, nor will it be easier, but I'd like to know how to do it.
It's obviously possible, as I've heard of several people doing it, and would really like to know the "secret" to gluing large pieces such as this. As far as I know the viola family of instruments is built almost exclusively with hide glue, and cello's and basses come to mind when glueing large plates with hide glue.
How about it? Any one able to point me in the right direction?
It's obviously possible, as I've heard of several people doing it, and would really like to know the "secret" to gluing large pieces such as this. As far as I know the viola family of instruments is built almost exclusively with hide glue, and cello's and basses come to mind when glueing large plates with hide glue.
How about it? Any one able to point me in the right direction?
- ozziebluesman
- Blackwood
- Posts: 1529
- Joined: Wed Oct 10, 2007 9:12 am
- Location: Townsville
- Contact:
G'day Allen,
I glued mine using Titebond in sections. I started with the neck section and glued it up first. Then I glued the section to the waist and from the waist to the end block last. Like you I had no idea how to go about gluing the top or back in one session. That's my two bobs worth. Richard may have the expertise here!
Cheers
Alan
I glued mine using Titebond in sections. I started with the neck section and glued it up first. Then I glued the section to the waist and from the waist to the end block last. Like you I had no idea how to go about gluing the top or back in one session. That's my two bobs worth. Richard may have the expertise here!
Cheers
Alan
Allen my friend I admire you for wanting to improve your HHG chops!
The folks that use HHG to glue plates generally will do one or both of two things.
First, since clamping has to happen very quickly, they jig-up with a press or some other system that can be in place with appropriate clamping pressure in 45 seconds give or take a bit.
I have seen pictures of Lowden's rig which is a press that is lowered by a large wheel. Others use a guitar shaped caul that is placed over the plate and then weighted down. The caul only applies pressure to the rim area of the plate.
The second thing that I have seen people do is slightly change the viscosity of the HHG so that it forms more of a bead when applied, slightly jells on the outside sealing in the wet glue in the bead. Once the bead is mashed down the wet, hot glue gets free and forms the bond.
Colin, if I recall has attached plates with HHG and hopefully he will weigh in here. Colin also knows the story about how some of the Spanish builders would set guitars on fire to attach plates with HHG.
The folks that use HHG to glue plates generally will do one or both of two things.
First, since clamping has to happen very quickly, they jig-up with a press or some other system that can be in place with appropriate clamping pressure in 45 seconds give or take a bit.
I have seen pictures of Lowden's rig which is a press that is lowered by a large wheel. Others use a guitar shaped caul that is placed over the plate and then weighted down. The caul only applies pressure to the rim area of the plate.
The second thing that I have seen people do is slightly change the viscosity of the HHG so that it forms more of a bead when applied, slightly jells on the outside sealing in the wet glue in the bead. Once the bead is mashed down the wet, hot glue gets free and forms the bond.
Colin, if I recall has attached plates with HHG and hopefully he will weigh in here. Colin also knows the story about how some of the Spanish builders would set guitars on fire to attach plates with HHG.
I could be wrong here, but doesn't Colin use Fish Glue for gluing backs on. I know that's what I used, and it went great. Put glue on the linings and back braces, dropped the back on and put on the go-bars.
Waddy
Build Albums 12 done - 1 in process
Clip for #1 Barrios' "Una Limosna por el Amor de Dios" - Not me playing
Build Albums 12 done - 1 in process
Clip for #1 Barrios' "Una Limosna por el Amor de Dios" - Not me playing
I did used to do it with hide. Do it in a warm room and warm the parts with a hair dryer, put the glue on with a squeezee bottle, back plate on and rapid application of go bars. With practice, which is the secret, it can be done fairly easily. Playing the hairdyer on the edge as you put the bars on slightly softens the glue. However, I'm getting too old for all that rushing about, fish glue does the job just as well and allows a more leisured approach. Fish dries just as hard and crystalline as HHG, it's another of the gelatin glues. I now use HHG for braces and bridge and fish for everything else (except for restoration work and lutes where I still use HHG for everything including attaching plates).
How they used to do it in Spain in the 19th century. Well, they put the HHG onto the rim and the back braces (braces were inlet into the lining and the back was glued to braces and rim) then they wiped alcohol onto the back plate above the rim and braces and set fire to the alcohol. The heat from the burning alcohol softened the glue and they quickly roped the back down. I still haven't had the courage to try it yet, but one day.....
Colin
How they used to do it in Spain in the 19th century. Well, they put the HHG onto the rim and the back braces (braces were inlet into the lining and the back was glued to braces and rim) then they wiped alcohol onto the back plate above the rim and braces and set fire to the alcohol. The heat from the burning alcohol softened the glue and they quickly roped the back down. I still haven't had the courage to try it yet, but one day.....
Colin
"In 1969, I gave up alcohol and women, worst 20 minutes of my life." George Best.
Thanks for the response's. If anyone is keen on doing a video demo of attaching a spruce top with the alcohol method. It'd be a must see for sure.
I lay awake last night pondering this.
What about brushing hide glue onto both surfaces and letting it partially dry. Position the plates and then use steam to heat the joint , partially rehydrate the glue, and then clamp down as you worked your way around the rim. I was thinking about running a hose from the steam nozzle on a cappuccino machine and directing it into the joint.

I lay awake last night pondering this.
What about brushing hide glue onto both surfaces and letting it partially dry. Position the plates and then use steam to heat the joint , partially rehydrate the glue, and then clamp down as you worked your way around the rim. I was thinking about running a hose from the steam nozzle on a cappuccino machine and directing it into the joint.
- Rod True
- Siberian Tiger
- Posts: 234
- Joined: Thu Sep 27, 2007 10:18 am
- Location: Abbotsford, BC Canada
The last guitar I finished I glued the top on with HHG. It was the first time I tried HHG and honestly it really wasn't a big deal.
First thing you want to do is do several test runs (minus the glue of course) pretend that you are applying the glue, put the plate on (make sure it self aligns first with the braces to the linings), put a caul on top like the one in the picture and add the go-bars. It's amazing how quick you can get all the go-bars on. Once you get the proceedure down to 45-50 seconds have at it.
And remember if it doesn't work out, just warm up the edge with the hair drier and clamp it down again.
I wouldn't use steam at all as it could change the moisture level of the HHG and weaken it.
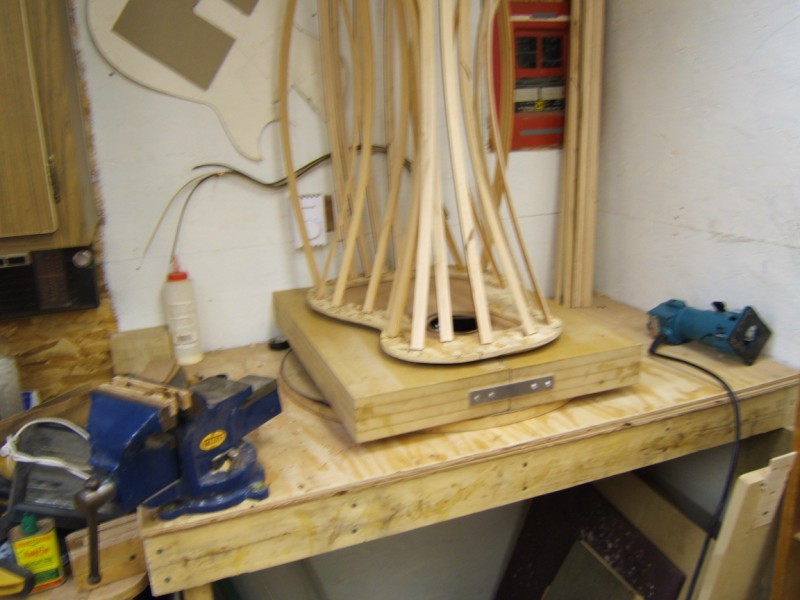
First thing you want to do is do several test runs (minus the glue of course) pretend that you are applying the glue, put the plate on (make sure it self aligns first with the braces to the linings), put a caul on top like the one in the picture and add the go-bars. It's amazing how quick you can get all the go-bars on. Once you get the proceedure down to 45-50 seconds have at it.
And remember if it doesn't work out, just warm up the edge with the hair drier and clamp it down again.
I wouldn't use steam at all as it could change the moisture level of the HHG and weaken it.
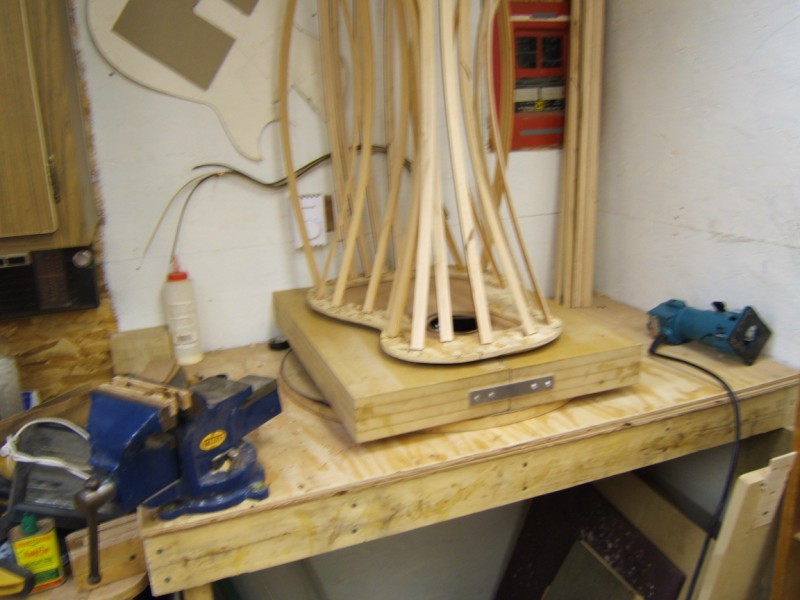
"I wish one of the voices in your head would tell you to shut the hell up." - Warren De Montegue
- matthew
- Blackwood
- Posts: 1192
- Joined: Mon Oct 08, 2007 1:16 pm
- Location: Sydney, Inner West
- Contact:
I prime both surfaces with hide glue. then position the top on the sides and clamp lightly all around. I loosen three clamps at a time and work in a bit of hot hide glue on a thin palette knife blade, then clamp tight and loosen the next few clamps, working my way around.
Even a knife dipped in hot water will be enought to remelt the glue into the joint.
MT
Even a knife dipped in hot water will be enought to remelt the glue into the joint.
MT
Thanks Rod and Matthew. My RH control room gets to a really balmy 40+ C, so I'm going to have lots more working time than most people will get. I'm going to give it a go. As the Weisenborn has a fair bit more glueing area, Matthews method sounds like it will be easier to do, and I don't have a go-bar deck that is large enough to handle it.
Matthew - is that just a thin coat of HHG at first ?I prime both surfaces with hide glue. then position the top on the sides and clamp lightly all around. I loosen three clamps at a time and work in a bit of hot hide glue on a thin palette knife blade, then clamp tight and loosen the next few clamps, working my way around.
I'll have to try this method on my next basketcase mando - resto ( I just picked up a set of ancient violin spool clamps so I am keen to get the pongy ol' HHG bubbling again and get medieval on it. )
I know the go-bars would be quicker in the heat of the moment than the fiddly lil' clamps though ...
AP
Probably a stupid question but if using HHG for fixing a top/back to sides is such a major operation then what is the advantage of doing it this way over using Titebond?
I know some of you will say ease of undoing the glue joint but Ive undone Titebond back/side joints on one of my guitars twice and didnt have too many problems.
I know some of you will say ease of undoing the glue joint but Ive undone Titebond back/side joints on one of my guitars twice and didnt have too many problems.
- Bob Connor
- Admin
- Posts: 3132
- Joined: Mon Jul 09, 2007 9:43 pm
- Location: Geelong, Australia
- Contact:
As I said in my initial post. I don't think for a second that one glue is any better than the other for this operation. It's just a pig headed stubbornness of wanting to learn how to do it. You never know when the skill might come in handy. Perhaps for something totally unrelated. Nothing more.
Same could be said about going with the dovetail neck joint over a bolt on mortise / tenon.
Same could be said about going with the dovetail neck joint over a bolt on mortise / tenon.
The advantage for the luthier of using either HHG or Fish glue over Titebond or the other aliphatic resins is that because HHG and Fish are gelatin based glues they form hard crystal structures on dryng which are relatively non-damping compared to titebond. Also as they dry they contract pulling the joints closer together.kiwigeo wrote:Probably a stupid question but if using HHG for fixing a top/back to sides is such a major operation then what is the advantage of doing it this way over using Titebond?
I know some of you will say ease of undoing the glue joint but Ive undone Titebond back/side joints on one of my guitars twice and didnt have too many problems.
In the factory situation, the aliphatics are the obvious production answer and will produce you a perfectly acceptable result. Even for the custom luthier they will do a good and acceptable job, however is acceptable good enough? HHG and Fish are capable of producing superior results, isn't that what custom building is all about?
Colin
"In 1969, I gave up alcohol and women, worst 20 minutes of my life." George Best.
- Bob Connor
- Admin
- Posts: 3132
- Joined: Mon Jul 09, 2007 9:43 pm
- Location: Geelong, Australia
- Contact:
I think it's also horses for courses Colin.
According to Al Carruth, whose research I follow with great interest, very little string energy gets transmitted to the back through the sides.
So the benefit of using HHG in this situation is doubtful.
I do use HHG, however, when I feel that it will contribute the the tone of the instrument ie braces and bridge.
According to Al Carruth, whose research I follow with great interest, very little string energy gets transmitted to the back through the sides.
So the benefit of using HHG in this situation is doubtful.
I do use HHG, however, when I feel that it will contribute the the tone of the instrument ie braces and bridge.
- matthew
- Blackwood
- Posts: 1192
- Joined: Mon Oct 08, 2007 1:16 pm
- Location: Sydney, Inner West
- Contact:
I prime the surfaces first to make sure I get a good thin line of glue all round, sometimes allow to dry even, and sand flat again. a bit like a pore-filling process and I think it helps to have glue already in there to wick the hot glue in.
I find HHG is very forgiving and glues tight like nobody's business. invisible glue line if your joint is a good fit. If it gells before you have things in place, you just need to reheat it/rewet it/brush a little more hot glue on. Cleanup is a dream. I see no disadvantage with it, it is nontoxic and enviro friendly, and I have no need even to try titebond.
I find HHG is very forgiving and glues tight like nobody's business. invisible glue line if your joint is a good fit. If it gells before you have things in place, you just need to reheat it/rewet it/brush a little more hot glue on. Cleanup is a dream. I see no disadvantage with it, it is nontoxic and enviro friendly, and I have no need even to try titebond.
- matthew
- Blackwood
- Posts: 1192
- Joined: Mon Oct 08, 2007 1:16 pm
- Location: Sydney, Inner West
- Contact:
OK, so when you strike a chord and you feel the body vibrating against your tum ... where do those vibrations come from? Last nights dinner??bob wrote:According to Al Carruth, whose research I follow with great interest, very little string energy gets transmitted to the back through the sides..
Surely it depends on how rigid you build your body?
- Bob Connor
- Admin
- Posts: 3132
- Joined: Mon Jul 09, 2007 9:43 pm
- Location: Geelong, Australia
- Contact:
Al built a guitar he called 'the corker'. Essentially it had a heap of sound ports in it which he blocked with corks while testing. As he removed more corks the sound pressure levels of the air inside the body went down and so did the activity of the back. Which lead him to believe that the sides had little to do with transference of vibrations to the back plate and it was the coupling of resonances or frequencies inside the of the box, and the interplay of the frequencies of the top and back which contributed the most to the vibrating back.matthew wrote:OK, so when you strike a chord and you feel the body vibrating against your tum ... where do those vibrations come from? Last nights dinner??bob wrote:According to Al Carruth, whose research I follow with great interest, very little string energy gets transmitted to the back through the sides..
Surely it depends on how rigid you build your body?
An area of much conjecture I know but there hasn't been that much research done in this area.
Al Carruth is probably leading the reasearch in this field.
OK Bob, on your next guitar let me see you mount the back and top plates using rubber gaskets, if damping at this joint is unimportant.
I'm afraid there is a lot of mis-placed pseudo-science being applied in luthiery now, take a scientific principle, apply it to a system for which it isn't designed and doesn't fit and call it 'left brain luthiery'.
Mario is right, it's all in the details.
But what do I know, I've only been a professor of geophysics for over twenty years, specialising in the transmission of energy through materials.
Colin
I'm afraid there is a lot of mis-placed pseudo-science being applied in luthiery now, take a scientific principle, apply it to a system for which it isn't designed and doesn't fit and call it 'left brain luthiery'.
Mario is right, it's all in the details.
But what do I know, I've only been a professor of geophysics for over twenty years, specialising in the transmission of energy through materials.
Colin
"In 1969, I gave up alcohol and women, worst 20 minutes of my life." George Best.
I was just reading through an old "Hide Glue - How To" that I've had for years.
It has a few different things about how to modify hide glue for different purposes, but the one that caught my attention was the addition of either urea or salt to the mix to make liquid hide glue.
I'm also wondering if this is what has been done to Titebond's liquid hide glue. The salt being a preservative, helping with the self life, but as it ages it looses it's glueing ability, to the point of being totally useless as it approaches it's expiry date?
It has a few different things about how to modify hide glue for different purposes, but the one that caught my attention was the addition of either urea or salt to the mix to make liquid hide glue.
Colin, have you heard of this before, and will it do anything to the working strength of the glue, as long as it's used right away?To make liquid (room temperature) glue add approximately 5
table spoons of urea (or 3 tablespoons of salt) for each cup of dry glue.
I'm also wondering if this is what has been done to Titebond's liquid hide glue. The salt being a preservative, helping with the self life, but as it ages it looses it's glueing ability, to the point of being totally useless as it approaches it's expiry date?
- graham mcdonald
- Blackwood
- Posts: 472
- Joined: Thu Oct 25, 2007 11:57 am
- Location: Canberra
- Contact:
Colin,
If you are unaware of Al Carruth's work in the area of stringed instrument acoustics, I suggest that you check out the publications of the Catgut Acoustic Society and other scientific journals where Al has published widely over many years before you so cavalierly dismiss him as 'misplaced pseudo-science'. In the area of guitars, he is one of perhaps half a dozen people in the world who has a proper understanding of what is happening in terms of the physics of what is going on.
Allen
Forget about the urea modified animal glue (such as the Franklins stuff). From all reports it ends up as an adhesive of usefulness somewhere between spirit gum and flour & water paste.
cheers
graham
If you are unaware of Al Carruth's work in the area of stringed instrument acoustics, I suggest that you check out the publications of the Catgut Acoustic Society and other scientific journals where Al has published widely over many years before you so cavalierly dismiss him as 'misplaced pseudo-science'. In the area of guitars, he is one of perhaps half a dozen people in the world who has a proper understanding of what is happening in terms of the physics of what is going on.
Allen
Forget about the urea modified animal glue (such as the Franklins stuff). From all reports it ends up as an adhesive of usefulness somewhere between spirit gum and flour & water paste.
cheers
graham
Graham McDonald
http://www.mcdonaldstrings.com
http://www.mcdonaldstrings.com
Who is online
Users browsing this forum: No registered users and 299 guests