I bent the sides on a hot pipe, as I don't have a bending mold for an OM and I thought I could use the practice. Surprisingly easy to bend by hand. As you can see I wanted to stretch my building skills some more and I' going to give the Ryan style arm rest a go. So far so good. No disasters yet. I reckon the only difficult part to it now is going to get the bindings to look good.
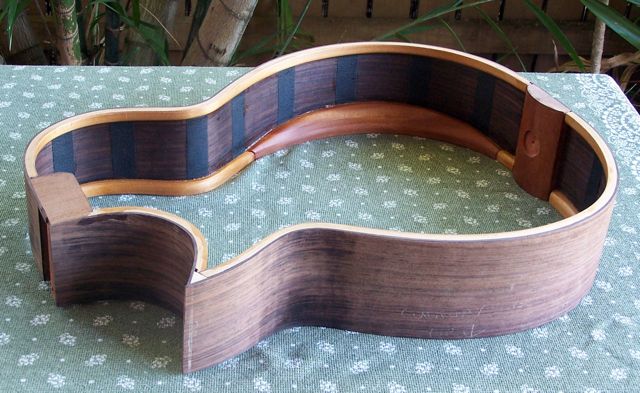
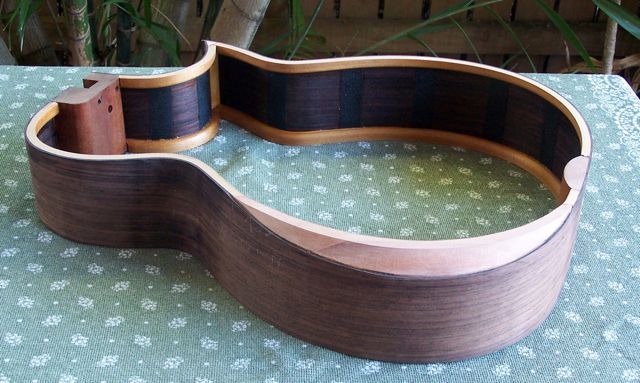
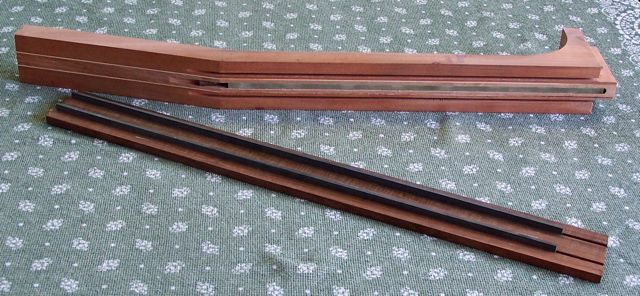
The fret board has been slotted 1/8 " for the CF rods to help support the fret board over the body, as Rick Turner does. This one is going to get a revision of the adjustable neck I used on the last one. Not shown is the back that I managed to get inlayed and braced. It's in the go-bar deck drying, but you've all seen a braced back, haven't you
