new member
new member
Hi All,
Found this site a week or so ago and have enjoyed taking a look.
I have an interest in resophonic guitars,and anything a bit different like cigar box's, tins etc made into instruments.Have made a few crude but usably instruments that I use at gigs.
Would like to show a pic of my first metal body reso build but can't work out how to post a picture? help!
Also, starting to dabble neck making fist efforts have been reasonable with
Vic ash for a tenor guitar, with a tea tin for the body.this project currently under way.
Found some cheap Karri at a junk/recycle yard near me would it be suitable for neck wood?
Thanks.
Found this site a week or so ago and have enjoyed taking a look.
I have an interest in resophonic guitars,and anything a bit different like cigar box's, tins etc made into instruments.Have made a few crude but usably instruments that I use at gigs.
Would like to show a pic of my first metal body reso build but can't work out how to post a picture? help!
Also, starting to dabble neck making fist efforts have been reasonable with
Vic ash for a tenor guitar, with a tea tin for the body.this project currently under way.
Found some cheap Karri at a junk/recycle yard near me would it be suitable for neck wood?
Thanks.
Cheers Luke
- sebastiaan56
- Blackwood
- Posts: 1279
- Joined: Sun Oct 28, 2007 5:23 am
- Location: Blue Mountains
- Bob Connor
- Admin
- Posts: 3132
- Joined: Mon Jul 09, 2007 9:43 pm
- Location: Geelong, Australia
- Contact:
Luke, Karri may be a little hard to work with but is a fine instrument timber, I've made a few fretboards from recycled planks of the stuff. It has a beautiful red glow to it and it's just one of those WA timbers that ring profoundly when tapped even in a rough sawn plank.
Should be fine for a neck timber on a smaller instrument where weight isn't a big issue ... Good luck.
Should be fine for a neck timber on a smaller instrument where weight isn't a big issue ... Good luck.
Hi all and thanks for your responses.
Shall now upload a pic of my fist steel body resonator guitar.
The body and internals were built by me (Cone from beard)
the neck was a $35 by now on ebay and it was very reasonable.
The hole job was an experiment that I have been thinking about for a while and it has turned out really well for my first effort.
I am very pleased with the tone and volume the guitar puts out the hole job cost under $300 in parts spent.
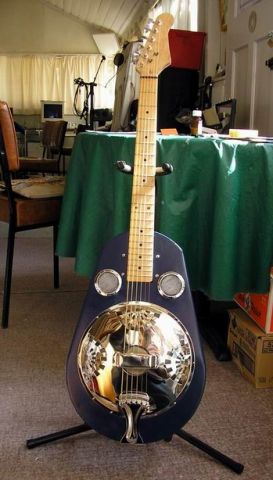
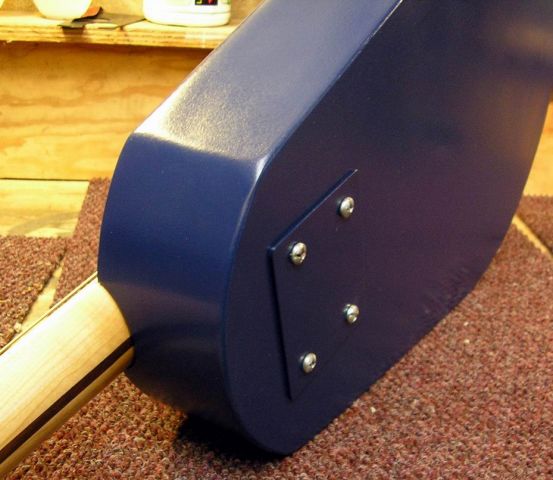
Shall now upload a pic of my fist steel body resonator guitar.
The body and internals were built by me (Cone from beard)
the neck was a $35 by now on ebay and it was very reasonable.
The hole job was an experiment that I have been thinking about for a while and it has turned out really well for my first effort.
I am very pleased with the tone and volume the guitar puts out the hole job cost under $300 in parts spent.
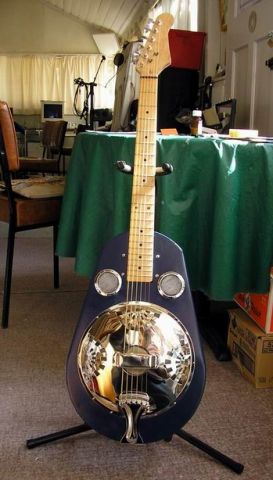
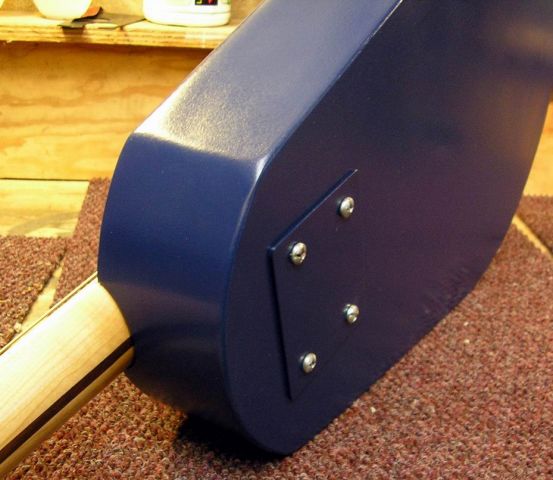
Cheers Luke
- sebastiaan56
- Blackwood
- Posts: 1279
- Joined: Sun Oct 28, 2007 5:23 am
- Location: Blue Mountains
A couple of questions Luke,
What is the body made of, Metal? What is the finish, Im personally not into the glass surface look and I like what you have done. I also like the way you have managed the cost, I know people who would spend $300 on the right piece of tonewood....
Sebastiaan
What is the body made of, Metal? What is the finish, Im personally not into the glass surface look and I like what you have done. I also like the way you have managed the cost, I know people who would spend $300 on the right piece of tonewood....
Sebastiaan
make mine fifths........
Thanks for the interest folks.
To answer Sebastiaan's questions.
The body is 1.2mm mild steel I am a sheet metal worker buy trade so metal was always an easy option for me.
The finish is simple spray can enamel. I used auto spray putty to give it a nice surface to paint over.
The neck block and tail block are Qld maple neck stick piece of Vic Ash.
Shall post some pics of construction if you like as there are a few surprises
that might make the pro guitar builders cringe.
But have to do that later have to run now.
To answer Sebastiaan's questions.
The body is 1.2mm mild steel I am a sheet metal worker buy trade so metal was always an easy option for me.
The finish is simple spray can enamel. I used auto spray putty to give it a nice surface to paint over.
The neck block and tail block are Qld maple neck stick piece of Vic Ash.
Shall post some pics of construction if you like as there are a few surprises
that might make the pro guitar builders cringe.
But have to do that later have to run now.
Cheers Luke
Have some pics of my construction of my reso thought it might be of interest.
Firstly this was an experiment I had a rough idea as to my methods and build ideas but you learn as you go.
I have never seen a reso made with a bolt on neck like mine.There are of course electric reso's and the National versions look way cool but for me a reso guitar has to have a speaker box of sorts for that sound.
As a blues/roots musician I have always preferred the biscuit bridge metal body tone over spider bridge wood body instruments.
The shape of my instrument came about as the easiest way to build it. The shape is similar to a chain guard you might see on a machine look a conveyor belt. Simple to make, but also something different from the standard shape.
As it was my first didn't want to spend to much if it turned out a dud so I tried to keep the costs down.
The neck has been a great buy and has handled the heavy strings it is nice and chunky, got the neck first.
Than made the neck block and body.
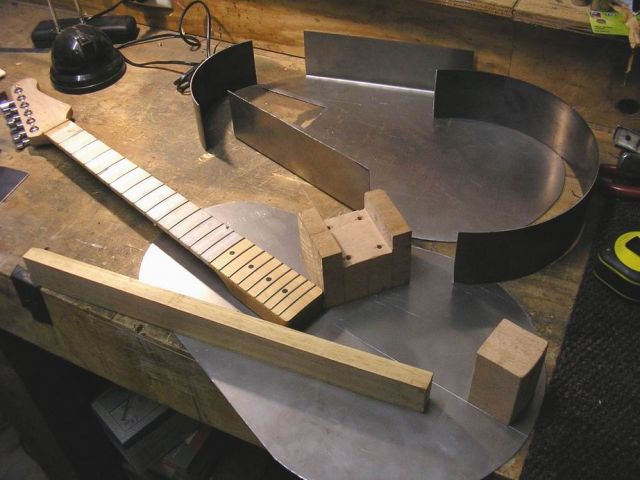
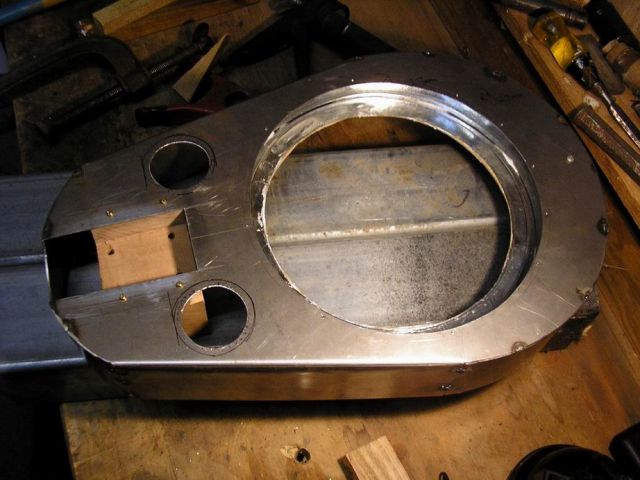
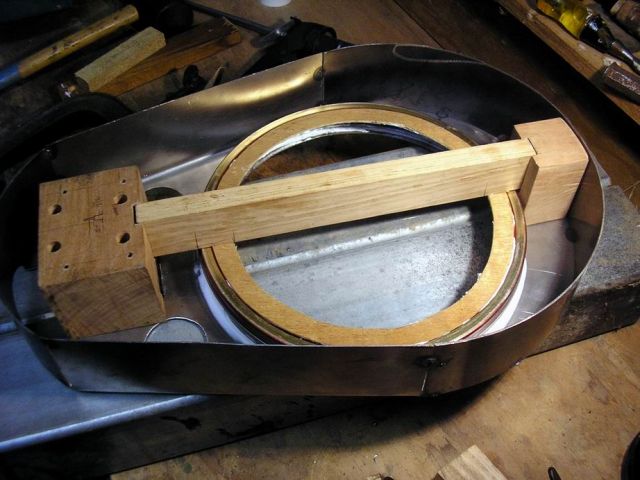
Firstly this was an experiment I had a rough idea as to my methods and build ideas but you learn as you go.
I have never seen a reso made with a bolt on neck like mine.There are of course electric reso's and the National versions look way cool but for me a reso guitar has to have a speaker box of sorts for that sound.
As a blues/roots musician I have always preferred the biscuit bridge metal body tone over spider bridge wood body instruments.
The shape of my instrument came about as the easiest way to build it. The shape is similar to a chain guard you might see on a machine look a conveyor belt. Simple to make, but also something different from the standard shape.
As it was my first didn't want to spend to much if it turned out a dud so I tried to keep the costs down.
The neck has been a great buy and has handled the heavy strings it is nice and chunky, got the neck first.
Than made the neck block and body.
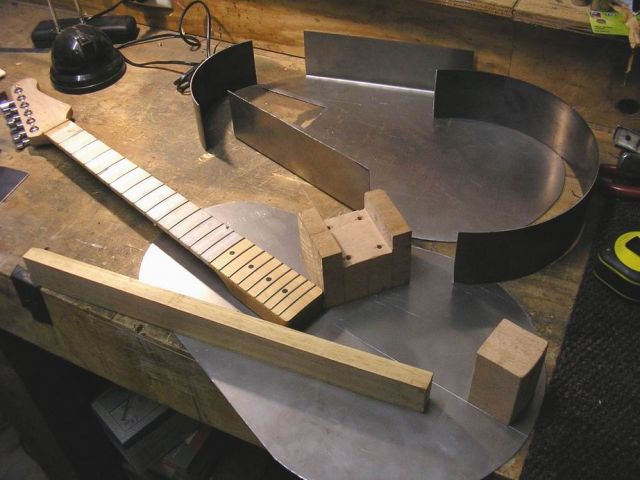
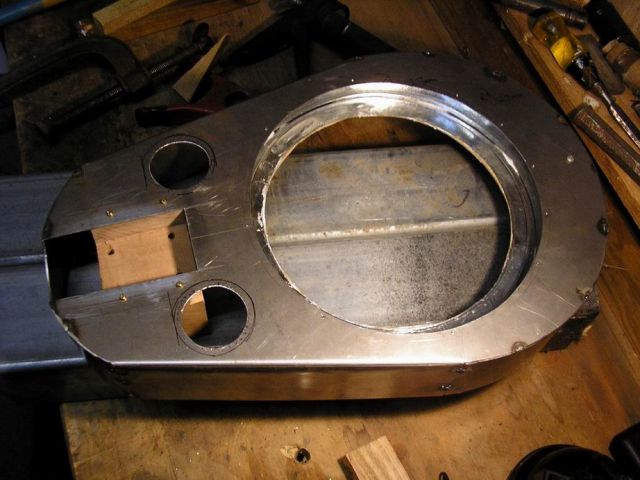
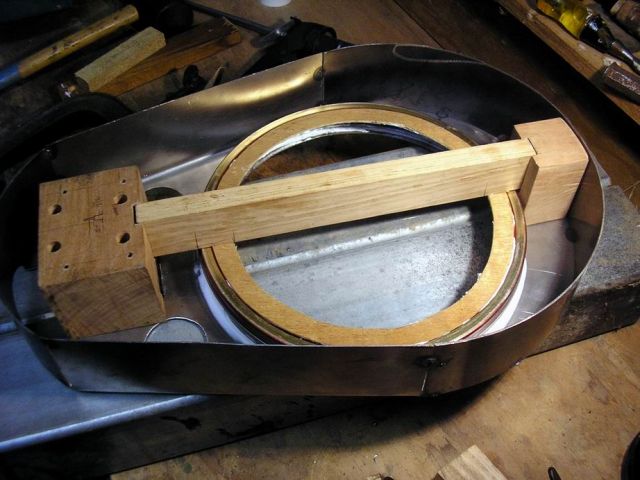
Cheers Luke
The sound well is made from a biscut tin lid it had the center cut out and than I formed a stirp of metal 25mm and glued it in to make the sound well.
A ply ring was glued to the base for added strength and stiffness as a biscuit tin is quite thin.
The sound well was glued to the body with a product called tool box made by fuller.Great stuff and cheap and it works saved the hassle of welding and any problems with heat distortion. I used some auto gasket paper between the cone and sound well base and I think it has made a big difference.
I was so impressed with this stuff I deiced not to fully weld up the body.
I just welded some good tacks than ran a bead of the tool box inside the seams of the body.
It has worked a treat and the joins are very good and no heat problems.
There is more glue than there is welding.
You wouldn't know unless i told you.
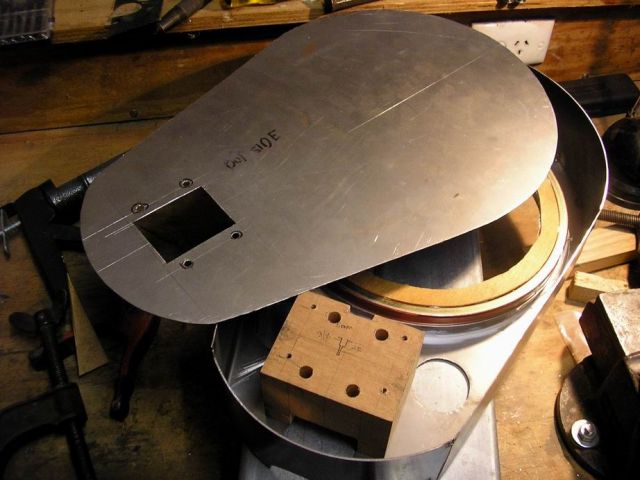
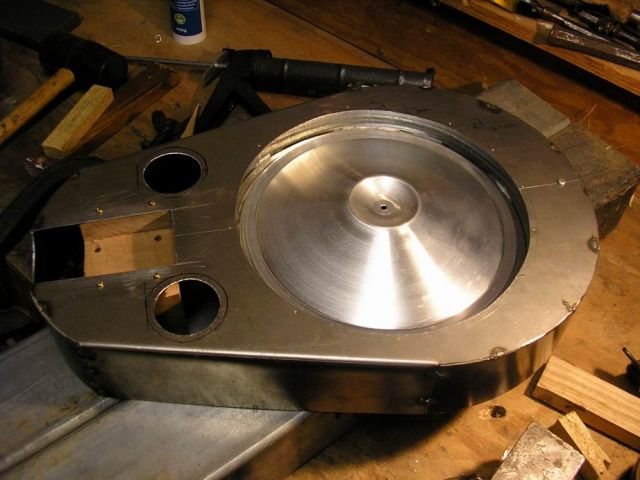
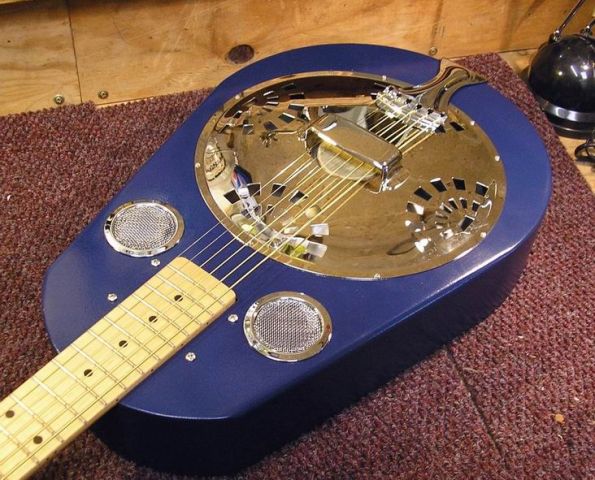
My next one shall have a few modifications it was a fun experiment and the results have been better than I hoped. Very proud to have an instrument that I can afford and that was not made in some Asian country where folks can't be getting paid properly,and it sounds cool.
thanks for taking a look its been a buzz to show it off thanks.
A ply ring was glued to the base for added strength and stiffness as a biscuit tin is quite thin.
The sound well was glued to the body with a product called tool box made by fuller.Great stuff and cheap and it works saved the hassle of welding and any problems with heat distortion. I used some auto gasket paper between the cone and sound well base and I think it has made a big difference.
I was so impressed with this stuff I deiced not to fully weld up the body.
I just welded some good tacks than ran a bead of the tool box inside the seams of the body.
It has worked a treat and the joins are very good and no heat problems.
There is more glue than there is welding.
You wouldn't know unless i told you.
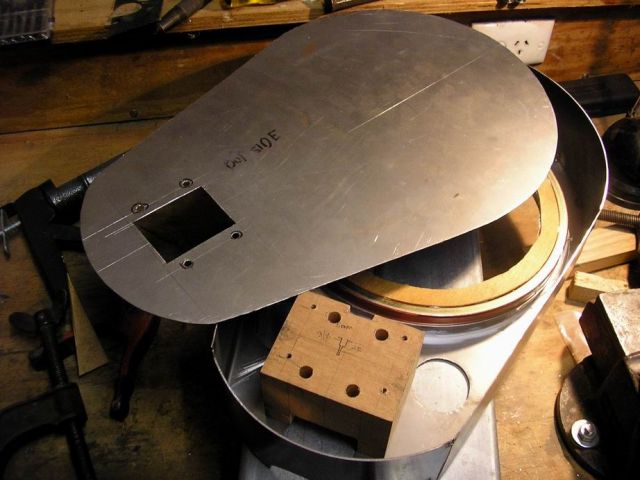
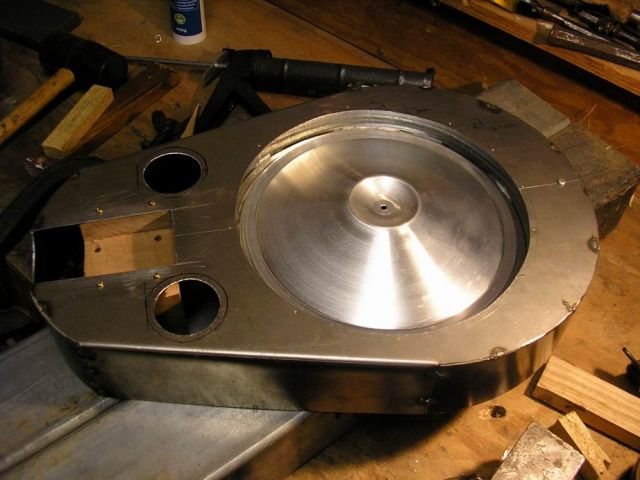
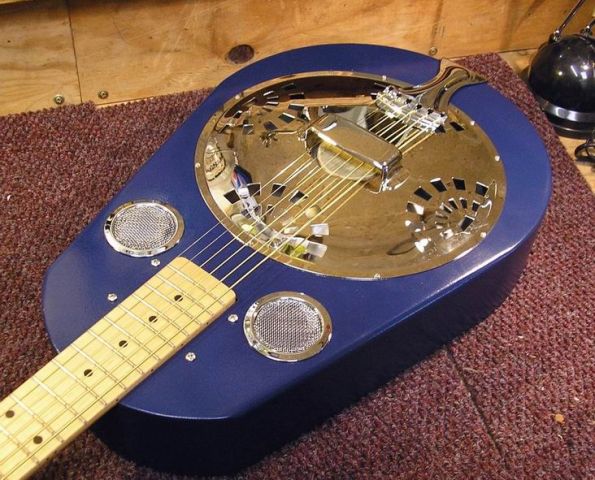
My next one shall have a few modifications it was a fun experiment and the results have been better than I hoped. Very proud to have an instrument that I can afford and that was not made in some Asian country where folks can't be getting paid properly,and it sounds cool.
thanks for taking a look its been a buzz to show it off thanks.
Cheers Luke
Luke, I edited your post so that the photo's didn't span across the screen. Makes it easier to view and read your post.
That's a really interesting project. Thanks for posting the pictures. Good use of glue as well.
In my trade many of the parts of a automobile are now glues together and they hold better than welds. The joins stand up far better in crash tests, so if you have to use this instrument to work your way through a bar fight, it's always good to know that it's not going to fly apart.
That's a really interesting project. Thanks for posting the pictures. Good use of glue as well.
In my trade many of the parts of a automobile are now glues together and they hold better than welds. The joins stand up far better in crash tests, so if you have to use this instrument to work your way through a bar fight, it's always good to know that it's not going to fly apart.

Who is online
Users browsing this forum: No registered users and 143 guests