Storing Tone Wood
- ozziebluesman
- Blackwood
- Posts: 1529
- Joined: Wed Oct 10, 2007 9:12 am
- Location: Townsville
- Contact:
Storing Tone Wood
Hi everyone,
Over the past few months i have been buying some tone wood sets and tops and resawing some tone wood also. The Norfolk Pine has just been resawn and will be very usable. I managed to get one set free from the tanalising treatment.
I won't be using this wood all at once and would like some advice on storing it in the correctly.
How do you store your wood?
I live in Townsville which is considered the dry tropics. The relative humidity levels are not extremely high usually. This years wet season is not what we normally experience and is very wet so humidity levels are quite high. I do have a humidity box where the RH levels are controlled but there is no air flow in there and it is full up with my guitar building projects at present.
I have seen a few pics of your workshops and i notice tone wood stored with what looks like wedges or round pieces of wood between the plates. Is this the process called stickering?
Anyway, i am very interested in your ideas and if you have some pics please post.
Cheers
Alan
Over the past few months i have been buying some tone wood sets and tops and resawing some tone wood also. The Norfolk Pine has just been resawn and will be very usable. I managed to get one set free from the tanalising treatment.
I won't be using this wood all at once and would like some advice on storing it in the correctly.
How do you store your wood?
I live in Townsville which is considered the dry tropics. The relative humidity levels are not extremely high usually. This years wet season is not what we normally experience and is very wet so humidity levels are quite high. I do have a humidity box where the RH levels are controlled but there is no air flow in there and it is full up with my guitar building projects at present.
I have seen a few pics of your workshops and i notice tone wood stored with what looks like wedges or round pieces of wood between the plates. Is this the process called stickering?
Anyway, i am very interested in your ideas and if you have some pics please post.
Cheers
Alan
- ozziebluesman
- Blackwood
- Posts: 1529
- Joined: Wed Oct 10, 2007 9:12 am
- Location: Townsville
- Contact:
All the wood that I've acquired has been well seasoned, so I haven't bothered with sealing the ends, though some of the pieces that I've bought have come with end sealer.
I sticker and keep them in the spare bedroom with the ceiling fan on low just to keep the air moving. When I'm thinking about starting to build something new, or when I've got something in the process of being built and RH is critical, I will turn on the dehumidifier at least a week before I start to build, and by the time I get ready to brace it's been in controlled RH for 3-4 weeks.
There are probably better ways to handle this, (like move to a drier climate) but I figure that if this guitar is going to have to live in the wet tropics, it's going to have to go through all kinds of humidity swings, so it might as well get use to it.
I sticker and keep them in the spare bedroom with the ceiling fan on low just to keep the air moving. When I'm thinking about starting to build something new, or when I've got something in the process of being built and RH is critical, I will turn on the dehumidifier at least a week before I start to build, and by the time I get ready to brace it's been in controlled RH for 3-4 weeks.
There are probably better ways to handle this, (like move to a drier climate) but I figure that if this guitar is going to have to live in the wet tropics, it's going to have to go through all kinds of humidity swings, so it might as well get use to it.

I made up some frames with a piece of 2x1 pine on the bottom and put 2 long threaded rods about 18" long and 12 apart on each end. 3 of these go on the bottom then my stack with stickers like Martin. I can put another 2x1 over the bolts on top of my stack and clamp it down if I need to and it makes carrying the whole bundle real easier for moving around and it is easy to slide out the bits you want without stuffing up your nice neat pile. The long bolts also give me something to push my sticker sticks up against and keep it all nice and lined up and the stack won't fall over.
For sides it is wide enought to do two rows next to each other and i just add another frame in the middle to give it plenty of support. I adapted this idea from something i saw on the Taylor web site. It appeals to my sense of order and burning need to have things square.
Dom
For sides it is wide enought to do two rows next to each other and i just add another frame in the middle to give it plenty of support. I adapted this idea from something i saw on the Taylor web site. It appeals to my sense of order and burning need to have things square.
Dom
I wouldn’t be too worried about humidity when storing your timbers. I’ve got a (perfect) German spruce set that has sat wrapped in hessian on the top of a wardrobe in a backyard shed since I inherited in 88. It would have been cut at least twenty years before I got it and it is still perfect. Also, I suspect that changes in humidity during storage could actually help tops open up faster.
- Bob Connor
- Admin
- Posts: 3132
- Joined: Mon Jul 09, 2007 9:43 pm
- Location: Geelong, Australia
- Contact:
Variations in temperature and humidity will certainly season wood and this is probably why a lot of the Spanish builders store their wood in their roof spaces. Stinking hot during the day, cool in the late afternoon with the possibility of some cold night.
The wood gets used to all manner of weather variations whic certainly should make it more resilient down the track.
I don't see how that will affect a guitar "opening up" quicker James.
I've yet to meet any luthier who can explain this this phenomenon.
Plenty of theories but no proof.
That is unless you know something that the rest of us don't.
Bob
The wood gets used to all manner of weather variations whic certainly should make it more resilient down the track.
I don't see how that will affect a guitar "opening up" quicker James.
I've yet to meet any luthier who can explain this this phenomenon.
Plenty of theories but no proof.
That is unless you know something that the rest of us don't.

Bob
This was a tip posted by Dave Freeman some years ago in one of the GAL Red Books. Ive used this method for some of my wood but find the masonite sticker method alot quicker.
Dominic wrote:I made up some frames with a piece of 2x1 pine on the bottom and put 2 long threaded rods about 18" long and 12 apart on each end. 3 of these go on the bottom then my stack with stickers like Martin. I can put another 2x1 over the bolts on top of my stack and clamp it down if I need to and it makes carrying the whole bundle real easier for moving around and it is easy to slide out the bits you want without stuffing up your nice neat pile. The long bolts also give me something to push my sticker sticks up against and keep it all nice and lined up and the stack won't fall over.
For sides it is wide enought to do two rows next to each other and i just add another frame in the middle to give it plenty of support. I adapted this idea from something i saw on the Taylor web site. It appeals to my sense of order and burning need to have things square.
Dom
Being that I am an international tonewood embezzler by trade and make my bread and butter by luring unsuspecting forum members into group buys and then pissing off with their wood. It is very important for me that i remain highly mobile. After all, one never does know in this game when those angry villagers armed with their silly pitchforks will come storming up the driveway.....again!
To address this problem and keep your wood, errrmmm sorry that should be MY wood, in tip top shape until I get a chance to move it on, I came up with the Larkim Transportable Wood Press or, as we call it in the trade, the LTWP
.
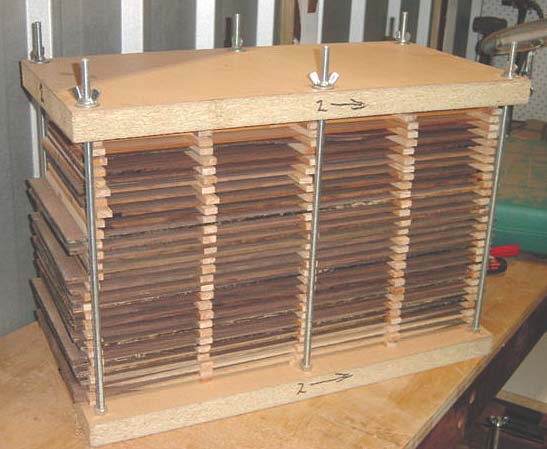
Here are a few of the suckers (sorry, no offence intended) lined up ready for the getaway
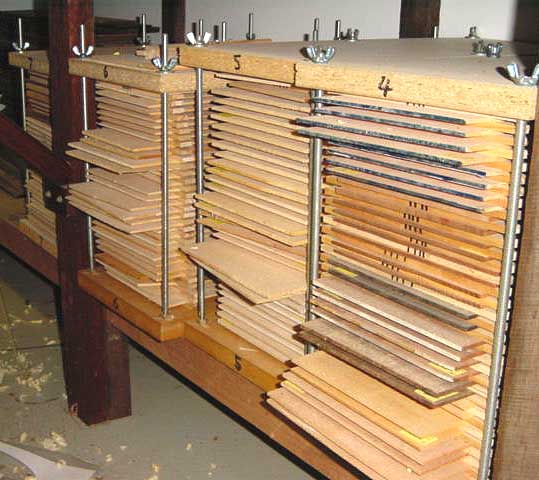
Anyhow, happy sailing, I know I will be
Thank your mother for the rabbits.
Kim
To address this problem and keep your wood, errrmmm sorry that should be MY wood, in tip top shape until I get a chance to move it on, I came up with the Larkim Transportable Wood Press or, as we call it in the trade, the LTWP

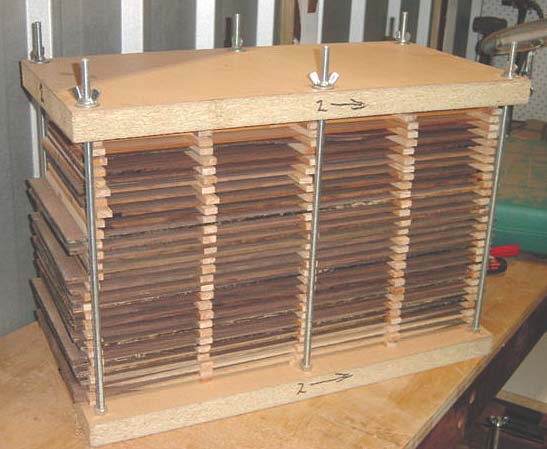
Here are a few of the suckers (sorry, no offence intended) lined up ready for the getaway

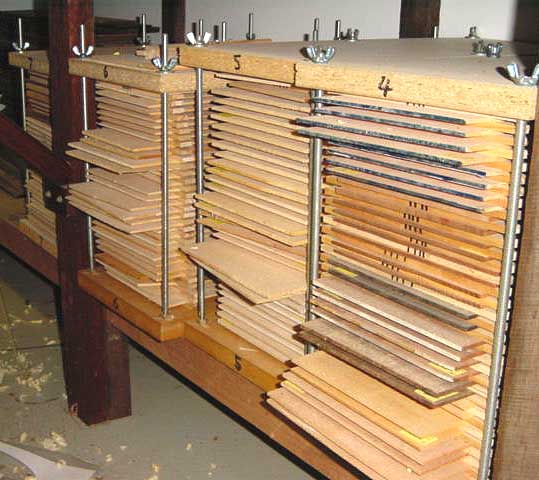
Anyhow, happy sailing, I know I will be

Thank your mother for the rabbits.

Kim
Yeh Bob... ‘opening up’ is a phenomenon that I've experienced, but don’t understand (and I’ve only noticed it in spruce). I met a third generation luthier in Mexico who stored his cut spruce in a rack screwed to the top of his fridge, when I asked why he told me that the vibration helped them to break in faster. One of the things I like about building wooden instruments is that science doesn't come into it, it is all theory, feel and opinion.
My theory (and it is only a theory) is that something changes in the structure of the timber much like what happens to metal becoming softer or harder from being worked (bent or heated). So I figure anything that supplies gentle movement to a spruce top in storage (including expansion and contraction of the timber due to humidity) could maybe help and if not, well it ain’t going to hurt.
My theory (and it is only a theory) is that something changes in the structure of the timber much like what happens to metal becoming softer or harder from being worked (bent or heated). So I figure anything that supplies gentle movement to a spruce top in storage (including expansion and contraction of the timber due to humidity) could maybe help and if not, well it ain’t going to hurt.
- Bob Connor
- Admin
- Posts: 3132
- Joined: Mon Jul 09, 2007 9:43 pm
- Location: Geelong, Australia
- Contact:
I've heard of some people putting their guitars in front of a stereo speaker and blasting Bob Marley in to them to try and get the same effect.
My feeling is that it'll open up quicker if you simply play the thing - lots and hard.
One reason that those pre war Martins sound so good is that they've had a lot of playing, generally by Bluegrass musos who aren't generally known for their light touch.
Bob
My feeling is that it'll open up quicker if you simply play the thing - lots and hard.
One reason that those pre war Martins sound so good is that they've had a lot of playing, generally by Bluegrass musos who aren't generally known for their light touch.

Bob
- Bob Connor
- Admin
- Posts: 3132
- Joined: Mon Jul 09, 2007 9:43 pm
- Location: Geelong, Australia
- Contact:
- Bob Connor
- Admin
- Posts: 3132
- Joined: Mon Jul 09, 2007 9:43 pm
- Location: Geelong, Australia
- Contact:
Kim, Bob, You guys have no idea of how jealous I am right now...
I've been using the yellow plastic 'tongue' that comes on the side of yellow tongue flooring chipboard, and a couple of thin MDF sticks on my much, much more modest tonewood collection.

I've been using the yellow plastic 'tongue' that comes on the side of yellow tongue flooring chipboard, and a couple of thin MDF sticks on my much, much more modest tonewood collection.
- If God had intended us to drink beer, He would have given us stomachs. - David Daye.
- The mouth of a happy man is filled with beer. -
- The mouth of a happy man is filled with beer. -
Ok, ok...your wood is fine I was just kidding.
On a more serious note, I feel that allowing your tonewood, particularly the hardwoods, to be exposed to all of the seasonal changes in temperature and RH is a very good thing. That is why I built my wood presses.
By having the wood well stickered in the press, it will remain flat yet can expand and contract with the varying conditions. After all, this is kind of what will happen when you finally glue the stuff up into a guitar, it will move, but it will also be constrained at the same time.
Also, it is worth considering that wood tends to move a lot more, even when kiln dried, when it is more fresh sawn. As it ages it settles down and stabilise. By keeping the wood in the press and exposing it to the elements so to speak, I hope to use up a lot of that youthful exuberance before I finally build with it. A fine craftsman by the name of Grant Goltz bought this to my attention on luthierforum and it just seems to make so much sense.
Grants thought, if I recall correctly in my words are, that the lignin or, amorphous hemicellulose-lignin matrix in the wood becomes progressively less active with age. Or that once the wood has been cut, the lignin only has so much volatility or big movements, before it finally sets and begins to constrain the board into a more stable form even when exposed to larger swings of RH and temperature. This is the essence of truly seasoned timber as per old school.
Hope that makes sense 4U.
Cheers
Kim

On a more serious note, I feel that allowing your tonewood, particularly the hardwoods, to be exposed to all of the seasonal changes in temperature and RH is a very good thing. That is why I built my wood presses.
By having the wood well stickered in the press, it will remain flat yet can expand and contract with the varying conditions. After all, this is kind of what will happen when you finally glue the stuff up into a guitar, it will move, but it will also be constrained at the same time.
Also, it is worth considering that wood tends to move a lot more, even when kiln dried, when it is more fresh sawn. As it ages it settles down and stabilise. By keeping the wood in the press and exposing it to the elements so to speak, I hope to use up a lot of that youthful exuberance before I finally build with it. A fine craftsman by the name of Grant Goltz bought this to my attention on luthierforum and it just seems to make so much sense.
Grants thought, if I recall correctly in my words are, that the lignin or, amorphous hemicellulose-lignin matrix in the wood becomes progressively less active with age. Or that once the wood has been cut, the lignin only has so much volatility or big movements, before it finally sets and begins to constrain the board into a more stable form even when exposed to larger swings of RH and temperature. This is the essence of truly seasoned timber as per old school.
Hope that makes sense 4U.
Cheers
Kim
- Bob Connor
- Admin
- Posts: 3132
- Joined: Mon Jul 09, 2007 9:43 pm
- Location: Geelong, Australia
- Contact:
You've just got to keep buying the odd bit here and there when the missus isn't looking and you'll be surprised how quickly you can build up a stash Joel.
The OLF swap meet is a great place to pic up some bargains and sensational wood.
I think we should all make a concerted effort and have a cunning plan in place for the next one.
We should be able to combine shipping and save a few bucks as well.
Bob
The OLF swap meet is a great place to pic up some bargains and sensational wood.
I think we should all make a concerted effort and have a cunning plan in place for the next one.
We should be able to combine shipping and save a few bucks as well.
Bob
I find bashing my newly built instruments against the walls of my workshop opens them up very quickly.bob wrote:I've heard of some people putting their guitars in front of a stereo speaker and blasting Bob Marley in to them to try and get the same effect.
My feeling is that it'll open up quicker if you simply play the thing - lots and
- Colonial Tonewoods
- ANZLF Approved Supplier
- Posts: 33
- Joined: Fri Jan 11, 2008 12:00 am
- Location: Virginia, United States
- Contact:
One little thing to add about wood storage.
For dense woods like EIR, Bocote, Cocobolo, ebony, I would suggest you seal the ends if you have not. For less dense wood like mahogany, walnut, koa, you really don't need to seal the ends.
When you sticker wood place the outer most stickers 3/4" in and then space the others in 3" intervals.
As for wood opening up...best thing I've found to open up a guitar is play the hell out of the thing.
For dense woods like EIR, Bocote, Cocobolo, ebony, I would suggest you seal the ends if you have not. For less dense wood like mahogany, walnut, koa, you really don't need to seal the ends.
When you sticker wood place the outer most stickers 3/4" in and then space the others in 3" intervals.
As for wood opening up...best thing I've found to open up a guitar is play the hell out of the thing.
- ozziebluesman
- Blackwood
- Posts: 1529
- Joined: Wed Oct 10, 2007 9:12 am
- Location: Townsville
- Contact:
Here is an interesting article written by ANZLF member Rick Turner; "instant vintage" sound in guitars by blasting them over a giant speakerbob wrote:I've heard of some people putting their guitars in front of a stereo speaker and blasting Bob Marley in to them to try and get the same effect.
My feeling is that it'll open up quicker if you simply play the thing - lots and hard.
Timber Tech's shaker table is like a heavy-duty loudspeaker with a 7,500-watt amplifie
http://www.acousticguitar.com/gear/advi ... tion.shtml
Not something easily rigged up in the usual workshop I would think! The article is from 1997, but as far as I know none of the big factories or top builders are having their instruments "shaken" this way before they send them out (yet). Perhaps they ARE doing it, but if not I wonder why not? Why would they NOT do it if the results really are as good as the article suggests? Rick, if you are reading this, do you have an opinion?
On the issue of storing wood; whenever I receive some new guitar wood I write the date, species and who I got it from on it, then put it on the bottom of the pile with stickers (the rosewood pile, the spruce pile etc). My stickers are 15 mm(?) spruce that I rip on the table saw. The sets on top of the pile I've had for many years and should be nice and stable by the time I get around to using it. I store everything in my humidity controlled workshop, where I try to keep the RH between 40-50% all year. I don't have a safe, dry place where I can stores it out of the shop, but I guess it makes sense that letting the wood get exposed to changes in temp and RH will make it more stable over time.
As I understand it, the main advantage of baking guitar tops in an oven, to bone dry (like Taylor and Collins and others do) is that it makes them more stable by "pre-shrinking" the wood structure. Even though wood is hygroscopic it never ‘fully recovers’ from the process, and it will not move as much with changes in the RH in the future. Unfortunately my European sized oven is not big enough to accept normal guitar plate wood so I rely on age…
Arnt Rian,
Norway
Norway
Kim, thank you. Thank you so much. I showed Sweetie your, ahem, small collection of wood there and received a kiss and the pronouncement of "I'm so glad you have better restraint then Kim"
Now if my small pile grows and it gets noticed, well Kim, your name is going to be a common sound in our happy home.
Now if my small pile grows and it gets noticed, well Kim, your name is going to be a common sound in our happy home.
Hi Kim, just love the set up you have for storing and drying sets.
cheers Bob,
cheers Bob,
Kim wrote:Being that I am an international tonewood embezzler by trade and make my bread and butter by luring unsuspecting forum members into group buys and then pissing off with their wood. It is very important for me that i remain highly mobile. After all, one never does know in this game when those angry villagers armed with their silly pitchforks will come storming up the driveway.....again!
To address this problem and keep your wood, errrmmm sorry that should be MY wood, in tip top shape until I get a chance to move it on, I came up with the Larkim Transportable Wood Press or, as we call it in the trade, the LTWP.
Here are a few of the suckers (sorry, no offence intended) lined up ready for the getaway![]()
Anyhow, happy sailing, I know I will be![]()
Thank your mother for the rabbits.![]()
Kim
Thanks Bob,Tigermyrtle wrote:Hi Kim, just love the set up you have for storing and drying sets.
cheers Bob,
It is handy because I can keep an inventory on my PC of what set is where. If I am looking for some macassar ebony for instance I know it's number and the spreadsheet tells me all I need to know about the set from initial cost to dimensions, any feature or incursion, who supplied it and when and that it's in press 9 so I can go straight to it when I want to use it.
Also I can quickly move the stash out of the way as required, this can be handy if you need some extra room for a particular project. Also, curse the thought, but just imagine a fire for instance

Cheers
Kim
Hi Kim, well i must say that you are very well organized,
i wish you would come over and sort out my shed, my problem is i am too busy salvaging timber to do anything else, but i have made up my mind to enrol in the next course Rick Turner will be doing in Tasmania. cheers Bob,
i wish you would come over and sort out my shed, my problem is i am too busy salvaging timber to do anything else, but i have made up my mind to enrol in the next course Rick Turner will be doing in Tasmania. cheers Bob,
Kim wrote:Thanks Bob,Tigermyrtle wrote:Hi Kim, just love the set up you have for storing and drying sets.
cheers Bob,
It is handy because I can keep an inventory on my PC of what set is where. If I am looking for some macassar ebony for instance I know it's number and the spreadsheet tells me all I need to know about the set from initial cost to dimensions, any feature or incursion, who supplied it and when and that it's in press 9 so I can go straight to it when I want to use it.
Also I can quickly move the stash out of the way as required, this can be handy if you need some extra room for a particular project. Also, curse the thought, but just imagine a fire for instanceat least if you where around you could get the stuff out quick if it all stays together when your running with it. But the main incentive for putting these together is the fact that we have also been looking at selling up where we live ATM for quite some time now, so as I have acquired the wood, I have kept building more of these presses to help take some of the headache out of the move.
Cheers
Kim
Tigermyrtle wrote:but i have made up my mind to enrol in the next course Rick Turner will be doing in Tasmania. cheers Bob,
Excellent news Bob, ike pretty much knows everything and you could do a lot worse than having him guide you through the process. Only thing is that once you get the bug, you will find yourself procrastinating a good deal more when it comes time to part with the wood because you will be wanting to hoard it all to yourself.
Better start building some of those presses now fella

Cheers
Kim
Who is online
Users browsing this forum: No registered users and 73 guests