Joining Question
- needsmorecowbel
- Blackwood
- Posts: 974
- Joined: Sun Oct 04, 2009 7:48 pm
- Location: Melbourne
Joining Question
Good evening saw this and was scratching my head a little:
http://www.lenaweelutherie.info/page6/p ... age18.html
I would have thought that utilising only tape and a weight/ clamps for joining the soundboard plates on the centre seam would not be ideal as the tape wouldn't provide enough sideways/ lateral pressure on the board (i would presume). In Cumpiano's book he uses 4 clamps and 4 chocks to tap the two plates together and utilises a clamp/ weighted object to keep the centre seem down instead of bending up/ pitching up.
I have no experience in joining plates so any suggestions would be much appreciated regarding clever/ inventive/ fairly foolproof ways to do it...I imagine Titebond would be sufficient a glue to glue the plates together with...I have 2 bottles of the stuff that i bought new but they have a fairly pungent odor of PVA which i always thought was a sign that it had gone off. Please correct me if i am wrong about that.
Stu
http://www.lenaweelutherie.info/page6/p ... age18.html
I would have thought that utilising only tape and a weight/ clamps for joining the soundboard plates on the centre seam would not be ideal as the tape wouldn't provide enough sideways/ lateral pressure on the board (i would presume). In Cumpiano's book he uses 4 clamps and 4 chocks to tap the two plates together and utilises a clamp/ weighted object to keep the centre seem down instead of bending up/ pitching up.
I have no experience in joining plates so any suggestions would be much appreciated regarding clever/ inventive/ fairly foolproof ways to do it...I imagine Titebond would be sufficient a glue to glue the plates together with...I have 2 bottles of the stuff that i bought new but they have a fairly pungent odor of PVA which i always thought was a sign that it had gone off. Please correct me if i am wrong about that.
Stu
- ozziebluesman
- Blackwood
- Posts: 1529
- Joined: Wed Oct 10, 2007 9:12 am
- Location: Townsville
- Contact:
Re: Joining Question
G'day Stu,
I've been using this method for joining tops and backs for sometime now with good results. You have to make sure the seam is absolutely a perfect fit with no gaps. If the plate joining edges are perfect you only need minimal force to make a good join. Hide glue will give you a superior glue joint although Titebon is used by many builders. I use the tape you can buy form Stu Mac for this job. It is strong and sticks very well. Care is needed when taking it off to so you don't damage the surface especially spruce.
Titebond usually has very little smell so I would be wary of using what you have. Others may have more experience and can advice you better.
Cheers
Alan
I've been using this method for joining tops and backs for sometime now with good results. You have to make sure the seam is absolutely a perfect fit with no gaps. If the plate joining edges are perfect you only need minimal force to make a good join. Hide glue will give you a superior glue joint although Titebon is used by many builders. I use the tape you can buy form Stu Mac for this job. It is strong and sticks very well. Care is needed when taking it off to so you don't damage the surface especially spruce.
Titebond usually has very little smell so I would be wary of using what you have. Others may have more experience and can advice you better.
Cheers
Alan
"Play to express, not to impress"
Alan Hamley
http://www.hamleyfineguitars.com/
Alan Hamley
http://www.hamleyfineguitars.com/
- needsmorecowbel
- Blackwood
- Posts: 974
- Joined: Sun Oct 04, 2009 7:48 pm
- Location: Melbourne
Re: Joining Question
Are the plates usually down to (roughly speaking) the correct thickness when you join them? Or do you yourself use a plane once the plates are joined?
- ozziebluesman
- Blackwood
- Posts: 1529
- Joined: Wed Oct 10, 2007 9:12 am
- Location: Townsville
- Contact:
Re: Joining Question
You can do it either way. I like to join the tops and backs before thicknessing. I use a shooting board and a good plane. Then I have some sandpaper glued to an old spirit level and get the join perfect. My thickness sander is wide enough to sand a joined plate. The shooting board is a great tool and easy to make.
Cheers
Alan
Cheers
Alan
"Play to express, not to impress"
Alan Hamley
http://www.hamleyfineguitars.com/
Alan Hamley
http://www.hamleyfineguitars.com/
Re: Joining Question
Joint the plate then thickness. You can clean up each side first so you can double check the book match and joint on a shared grain line, it also helps keep things nice and flat when you do actually glue them together. But the main thing to pay attention to is that the joint itself 'candles' well (held up to a powerful light..(the sun is a good one), and shows no light between the planed edges when held up together)
If your PVA smells like vinegar, throw it in the bin because its rat shit.
Cheers
Kim
If your PVA smells like vinegar, throw it in the bin because its rat shit.
Cheers
Kim
- needsmorecowbel
- Blackwood
- Posts: 974
- Joined: Sun Oct 04, 2009 7:48 pm
- Location: Melbourne
Re: Joining Question
Well it's funny i bought this titebond from an online store in Melb and he said he'd check the batch because i kicked up a bit of a fuss...but the second one he sent out smelt just as bad as the first. I compared it to the one i had out in my corrugated iron shed for the past 8 months and it didn't smell as bad but i didn't want to risk it. Not quite vinegar but well on the way..
Cheers Alan, Kim
Cheers Alan, Kim
- needsmorecowbel
- Blackwood
- Posts: 974
- Joined: Sun Oct 04, 2009 7:48 pm
- Location: Melbourne
Re: Joining Question
and of course if you join them before reducing the thickness you can eliminate any glue staining that may have occurred...
- needsmorecowbel
- Blackwood
- Posts: 974
- Joined: Sun Oct 04, 2009 7:48 pm
- Location: Melbourne
Re: Joining Question
What would you suggest using as a the base for the neck wood if i am going to use a Indian Rosewood Fretboard? I like maple necks but they would be very heavy for acoustic necks.
- ozziebluesman
- Blackwood
- Posts: 1529
- Joined: Wed Oct 10, 2007 9:12 am
- Location: Townsville
- Contact:
Re: Joining Question
Stu, I use Queensland Maple for neck material as if dried correctly, it is a very stable wood. There are plently of other woods suitable for necks.
Cheers
Al
Cheers
Al
"Play to express, not to impress"
Alan Hamley
http://www.hamleyfineguitars.com/
Alan Hamley
http://www.hamleyfineguitars.com/
Re: Joining Question
Stu, I used a qld maple neck on one archtop, and rock maple on another.
You really notice the significant weight increase of the rock maple, but boy does it feel good!
You really notice the significant weight increase of the rock maple, but boy does it feel good!
Craig
I'm not the sharpest tool in my shed
I'm not the sharpest tool in my shed
Re: Joining Question
I use the tape method with Hot Hide Glue
Works great and gives me invisible joins, can't ask for more.
I just tidy up the surface on the raw boards with the thickness sander and make sure they are the same thickness before joining, but bring them down to thickness after joining.
Works great and gives me invisible joins, can't ask for more.
I just tidy up the surface on the raw boards with the thickness sander and make sure they are the same thickness before joining, but bring them down to thickness after joining.
Re: Joining Question
Tape tent method for me as well. You just have to make sure that the joint is light tight. With a HHG the joint pulls together even tighter as it dries.
I use a fair bit of Qld. Maple for uke necks. Mostly Mahogany for guitar necks simply because that's what the market expects.
I use a fair bit of Qld. Maple for uke necks. Mostly Mahogany for guitar necks simply because that's what the market expects.
- needsmorecowbel
- Blackwood
- Posts: 974
- Joined: Sun Oct 04, 2009 7:48 pm
- Location: Melbourne
Re: Joining Question
Cheers guys, it will be my first acoustic guitar build...i was planning to do an archtop first but slapped myself in the face whilst saying "Dammit Man get yourself together"
I've heard the veritas planes are good...Stanley??


Got the Back and Sides and Spruce top from Tim Spittle (and photos)
Stu
I've heard the veritas planes are good...Stanley??


Got the Back and Sides and Spruce top from Tim Spittle (and photos)
Stu
Last edited by needsmorecowbel on Mon Mar 14, 2011 7:44 pm, edited 1 time in total.
Re: Joining Question
Beautiful set Stu, but that is what we have come to expect from Tim @ Australian Tonewoods
Nothing wrong with old Stanley planes, but you do need to read up on how to get them in tune and give them the time they deserve. Then they will reward you back for a very long time. If you have more cash, then a Veritas will work well right from the box.
Cheers
Kim

Nothing wrong with old Stanley planes, but you do need to read up on how to get them in tune and give them the time they deserve. Then they will reward you back for a very long time. If you have more cash, then a Veritas will work well right from the box.
Cheers
Kim
- needsmorecowbel
- Blackwood
- Posts: 974
- Joined: Sun Oct 04, 2009 7:48 pm
- Location: Melbourne
Re: Joining Question
Well i didn't do any woodworking in school so i would only have a rough idea of how to properly use one like a seasoned carpenter
would definitely give it a go though,
Stu
would definitely give it a go though,
Stu
- needsmorecowbel
- Blackwood
- Posts: 974
- Joined: Sun Oct 04, 2009 7:48 pm
- Location: Melbourne
Re: Joining Question
Something like that would do pretty much everything in terms of joining i would imagine:
http://www.carbatec.com.au/veritas-beve ... ane_c19943
http://www.carbatec.com.au/veritas-beve ... ane_c19943
Re: Joining Question
Hey Stu,
Watch this vid, it shows how to 'tune' a plane. You then need to make sure you know how to 'hone' a plane which includes lapping the back of the blade to get it flat and shiny because that is the only way to get a 'sharp' blade. Get these steps right and 'using' a plane is a breeze, ignore them and you will really struggle to make the tool useful at all.
youtu.be/
Spend a bit of time on youtube. They have hundreds of tutorials for this kind of stuff. After you know how to tune a plane, search youtube for "scary sharp" and that should reveal a simple way for you to get a really good edge going on your chisels and planes...you need that or you will be behind the 8 ball all the way.
Cheers
Kim
Watch this vid, it shows how to 'tune' a plane. You then need to make sure you know how to 'hone' a plane which includes lapping the back of the blade to get it flat and shiny because that is the only way to get a 'sharp' blade. Get these steps right and 'using' a plane is a breeze, ignore them and you will really struggle to make the tool useful at all.
youtu.be/
Spend a bit of time on youtube. They have hundreds of tutorials for this kind of stuff. After you know how to tune a plane, search youtube for "scary sharp" and that should reveal a simple way for you to get a really good edge going on your chisels and planes...you need that or you will be behind the 8 ball all the way.
Cheers
Kim
- J.F. Custom
- Blackwood
- Posts: 779
- Joined: Fri May 01, 2009 9:13 pm
- Location: Brisbane
- Contact:
Re: Joining Question
Hey Stu.
The "new" Stanleys have nothing on their old counterparts with respect to quality, but will do in a pinch. You will just have to put in the effort to "tune" them and set them up. Whether the end result was worth the time and effort over the savings is a harder call. The older ones were good but may still require work and may not save you much either as they can fetch high prices due to "collectable" status now.
Certainly that Veritas would do the job - what a swish bit of kit.
Unfortunately I don't have one of those... But I can't complain - the Terry Gordon (HNT Gordon) I have works beautifully. 
Also with respect to the glue as mentioned above, Titebond is certainly proficient for the job but it should not smell as you describe. It has a subtle smell usually but not one you would describe as offensive or wrinkle your nose at say. Sounds like yours is off and I'd err on the side of caution too.
And I'll second Kim's comment too, what a fine Blackwood set! Got to be happy with that.
Good luck.
Jeremy.
The "new" Stanleys have nothing on their old counterparts with respect to quality, but will do in a pinch. You will just have to put in the effort to "tune" them and set them up. Whether the end result was worth the time and effort over the savings is a harder call. The older ones were good but may still require work and may not save you much either as they can fetch high prices due to "collectable" status now.
Certainly that Veritas would do the job - what a swish bit of kit.


Also with respect to the glue as mentioned above, Titebond is certainly proficient for the job but it should not smell as you describe. It has a subtle smell usually but not one you would describe as offensive or wrinkle your nose at say. Sounds like yours is off and I'd err on the side of caution too.
And I'll second Kim's comment too, what a fine Blackwood set! Got to be happy with that.

Good luck.
Jeremy.
- needsmorecowbel
- Blackwood
- Posts: 974
- Joined: Sun Oct 04, 2009 7:48 pm
- Location: Melbourne
Re: Joining Question
I do like the reversible nature of the HHG
Re: Joining Question
That's some really fine blackwood for a first build. What sort of top are you going to go on it?
- needsmorecowbel
- Blackwood
- Posts: 974
- Joined: Sun Oct 04, 2009 7:48 pm
- Location: Melbourne
Re: Joining Question
Lutz spruce for the top and just ordered the Indian Rosewood fingerboard last night. Probably going to go with a mahogany neck as you suggested. I'm just looking forward to giving it a fair crack and i don't really have a time restraint on it. The wood choice is a tad bit ballsy but it's all learning. Don't want to try anything really fancy with the rosette or bindings (maybe a blackwood binding on the back and a curly maple binding around the top if my confidence is not shattered by this point haha). I might take the advice from Cumpiano's book and do a free assembly to insure that i don't get lazy as i possibly could with a mold and to insure there is no stress in the sides. Might even chuck a veneer on the headstock if it is going to plan. I'm thinking of going all quarter sawn spruce bracing/ kerfing. What would you suggest as a bridge brace wood Allen? Any thoughts of suggestions are always welcomed
Stu
Stu
- Nick
- Blackwood
- Posts: 3642
- Joined: Thu Feb 26, 2009 11:20 am
- Location: Christchurch, New Zealand
- Contact:
Re: Joining Question
Nice bit of Blackwood, you will just have to photograph this build (warts an' all)...I just loooooove Blackwood and Archtops aren't that hard as a first build just have to be methodical. But this will do just fine! 

"Jesus Loves You."
Nice to hear in church but not in a Mexican prison.
Nice to hear in church but not in a Mexican prison.
Re: Joining Question
You are going to want to put a head stock veneer on for sure. An off cut from the Blackwood you have would most likely do the trick. Helps tie everything together besides strengthening the head stock. Hides the scarf joint if you go that way. Also helps hold the nut in place. On most head stocks I also use a back strap. Hides the scarf joint and the ears that I glue on to get the width for the head stock, besides making the thing about as stiff as possible.
For a bridge patch there are all kinds of suitable candidates. Indian Rosewood is one of the traditional ones. But there are many others. My rule of thumb is that if you can drop it on the tiles and it goes ping instead of thud, then it's going to be a contender.
You can't go wrong with spruce for bracing. Linings too, but these aren't so critical. They can be almost anything, as they are used mostly to increase the glueing surface for top and back, especially when a chunk of them get routed away for bindings.
Not too sure about having different bindings on the top to the back. But those things are down the track. You don't have to decide about trim until you get to that point.
You do want to think about the color pallet you are working with, and it's probably best to not add too many different woods just because you can. Successful design comes with not throwing everything at the viewer, but using a limited arsenal well. At least that's been my experience.
Just a thought about bindings. If those sides are deep enough, you can always get the bindings from them. They are sometimes called "Stealth bindings" because you install them in the same place as they were cut off. Add a bwb purling between them and the side and you've got a really slick looking guitar.
For a bridge patch there are all kinds of suitable candidates. Indian Rosewood is one of the traditional ones. But there are many others. My rule of thumb is that if you can drop it on the tiles and it goes ping instead of thud, then it's going to be a contender.
You can't go wrong with spruce for bracing. Linings too, but these aren't so critical. They can be almost anything, as they are used mostly to increase the glueing surface for top and back, especially when a chunk of them get routed away for bindings.
Not too sure about having different bindings on the top to the back. But those things are down the track. You don't have to decide about trim until you get to that point.
You do want to think about the color pallet you are working with, and it's probably best to not add too many different woods just because you can. Successful design comes with not throwing everything at the viewer, but using a limited arsenal well. At least that's been my experience.
Just a thought about bindings. If those sides are deep enough, you can always get the bindings from them. They are sometimes called "Stealth bindings" because you install them in the same place as they were cut off. Add a bwb purling between them and the side and you've got a really slick looking guitar.
- needsmorecowbel
- Blackwood
- Posts: 974
- Joined: Sun Oct 04, 2009 7:48 pm
- Location: Melbourne
Re: Joining Question
Cheers Allen i was more thinking the maple would provide a smooth transition between the two as not to have too great a contrast between the spruce and the black wood. It is a good point thought with such a lovely array of timbers to choose from you have got to avoid making a patchwork guitar haha...
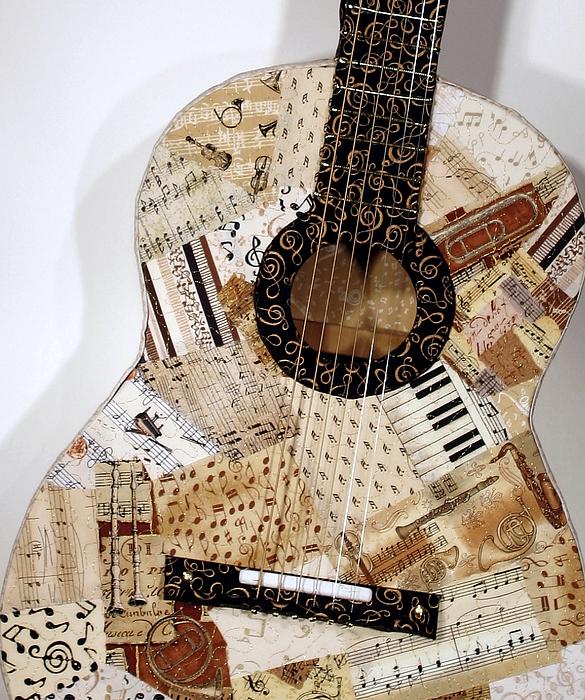
Stealth binding is a genius idea by the way. Too bad there is no ninja rating on the forums
Stu
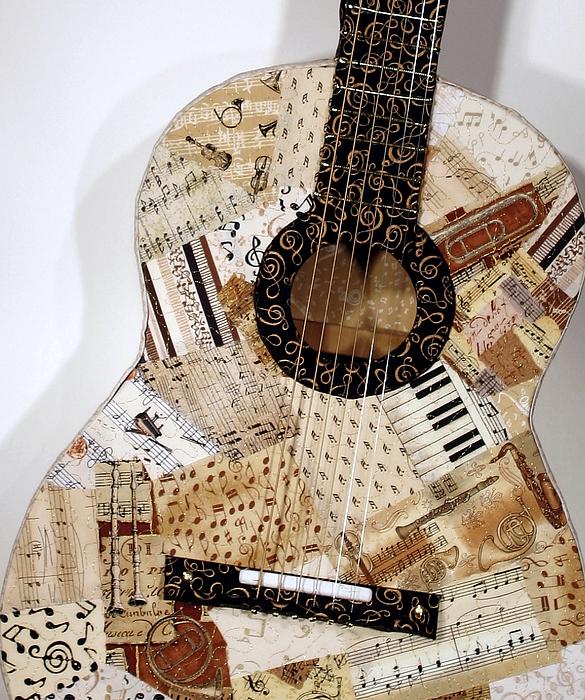
Stealth binding is a genius idea by the way. Too bad there is no ninja rating on the forums
Stu
Re: Joining Question
Not my idea. I think it was Hesh that I first saw use the term.
Who is online
Users browsing this forum: Google and 149 guests