I second the advice on Bruce R. Hoadley's "Understanding Wood" its old, but 'facts' are timeless
On a side note. As mentioned above a lot of these small diameter desert woods have little moisture to lose. Even when cut green they feel 'cool' rather than wet like most other woods.
I knew and old bloke who, until he passed away, use to supplement his pension by making wall clocks and plaques. He had a mate who he used to go prospecting with years earlier who still lived out in the goldfields of WA. Each trip to Perth, his mate would drop in a few small logs of mulga and gimlet and they would simply stack them on a pallet inside half an old corrugated iron water tank.
The old bloke had a horizontal bandsaw, the kind used for metal work. He also had a cradle welded up from angle iron to hold the logs that were all app 150 to 200mm through. When he needed to make a batch of clocks, he would load a log into the cradle and start slicing off rounds from the end, bark, sapwood, the lot, at around 19mm. I don't know how much wastage he got through end checks, but I do know that none of the logs were sealed on the ends during storage as I seen some with the ends right off the chainsaw that were inside his shed ready for slicing.
He gave me a small log of mulga from that lot which I took home and sealed with plumbers glue. A year or so later I resawed it for fretboards etc and there was next to no checking. Once opened up though, the wood was found to have lots of knots and branch junctions etc so very little 'clean' wood came from the exercise. But its beautiful wood all the same so I continued the resaw. I am glad I did because even with all the faults, the 8 to 12mm thick slices I kept have remained surprisingly stable even after 5 years.
I know that many will say that you should not use such wood for the fretboard of a guitar for fear it will impart a bend or twist in the neck, but I disagree. First of all because as mentioned above, regardless of the knots and other issues, the wood is in fact quite stable. This is great the thing about really dense wood, it takes a long time to lose what little moisture it has to give up, but it also reacts very slowly to changes in RH because it can't take up moisture from the atmosphere that quickly either.
This means that such wood by its nature has greatly reduced extremes of movement, ie; it could take days of even weeks for malga to reach equilibrium if it were taken from a relatively dry climate, to a moist tropical climate. So under normal circumstances, where the wood is only exposed to the normal RH swings that occur within its own environment, it hardly has a chance to move at all, because no sooner does the RH rise, than it falls again. So dense woods such as mulga do not have enough time to respond to these swings and more often than not, RH changes will occur around them whilst they remain quite stable suspended somewhere in the middle.
The other thing to consider about the effects of wood in tension, is that movement and the force associated with that movement, is directly related to how 'thick' the wood is..i.e. thicker wood = more reactive fibres and therefore, more force to worry about. But a fretboard 'before' processing with a radius, is only 6mm thick, and then many slots are cut into it to a depth which leaves the section with the structural integrity of kerfed lining.....not much force left in that regardless of the knots and yes, it can be argued that the slots are then filled with fret wire reintroducing much of the lost integrity once the board is glued to the neck. But to my mind, the reactive fibres have still been cut which reduces their capacity to work as one to twist and buckle the fretboard.
Case at hand, I made this mulga fretboard and glued it onto a guitar a few years back. It has lots of 'reactive' wood, knot shadows, branch incursions (have a look at the wood between 1st and 2nd fret), sap wood, even the bindings are full of knots, but the neck of the guitar to which that FB is glued remains as solid as a rock.
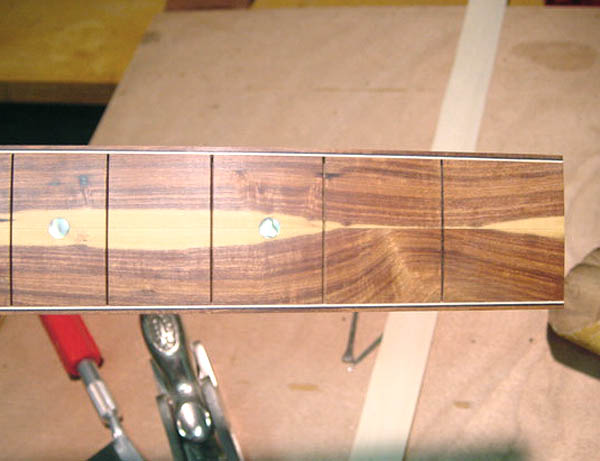
- nut end.jpg (58.55 KiB) Viewed 22668 times
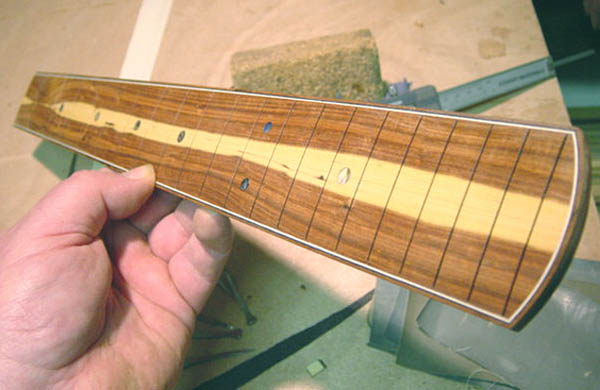
- angle_full.jpg (60.97 KiB) Viewed 22668 times
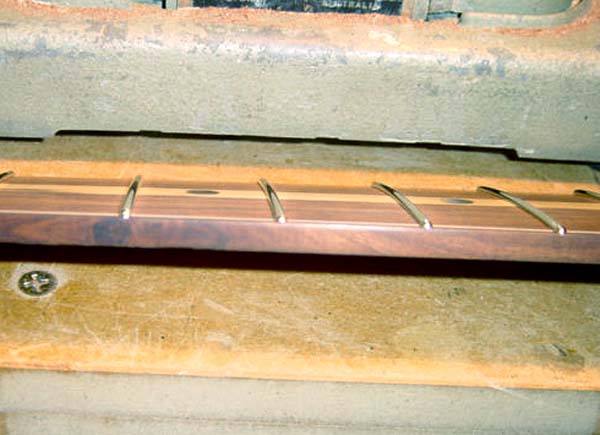
- sideclose.jpg (57.65 KiB) Viewed 22668 times
My point here is that whilst we should 'consider' good wood working principals when selecting materials, we also need to look closely at the 'actual' consequences of those principals in relation to the job at hand. Considering the relatively thin cross sections with which we work, the risk of being overly pedantic about perfection in grain uniformity is that we will miss out on using some truly spectacular woods.
Cheers
Kim