Here’s an interesting project for me. Customer brought in this nice old bass, found in an attic.
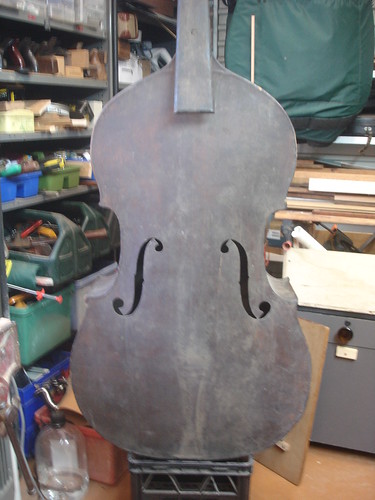
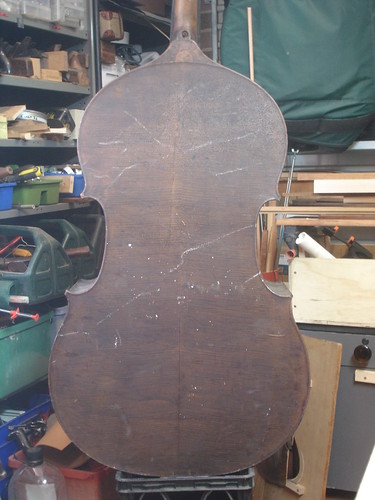
The button carving below and the outline is typical of French basses from the mid- late 1800's. This one has no immediately apparent makers mark or label. Another mystery bass!
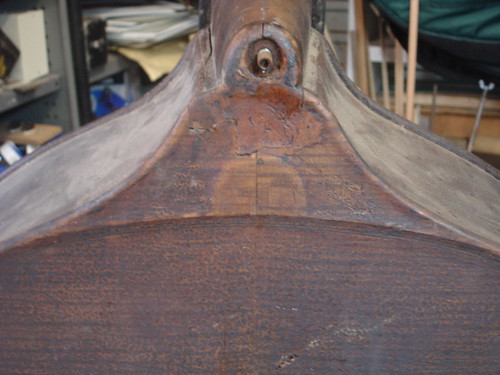
The Scroll has snapped off just below the nut and this will mean a scroll graft repair for sure.
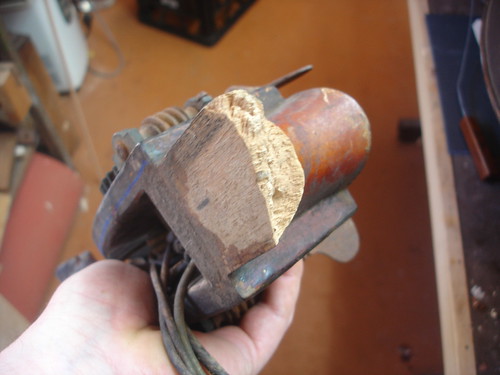
Nice big scroll, looks original, four pegs and a very crusty set of gut strings. This was never a three-stringer. Also the volute has been broken off above the top tuner at some point and repaired but not in a very satisfactory way.
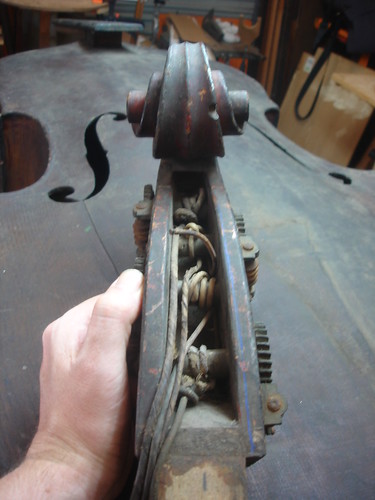

The Scroll gives an idea of the original red-brown varnish which on the rest of the instrument has deteriorated into a pobbly mess. I suspect it was a spirit varnish because of the brittleness of what is remaining, but the heat of the attic has shrunken and denatured whetever was there originally. There are a few spots on the top where the colour shows through. I think the ground is intact and I may be able to keep this by carefully scraping the crud off the surface then cleaning, when it’s time to refinish. That’s a long way off yet.
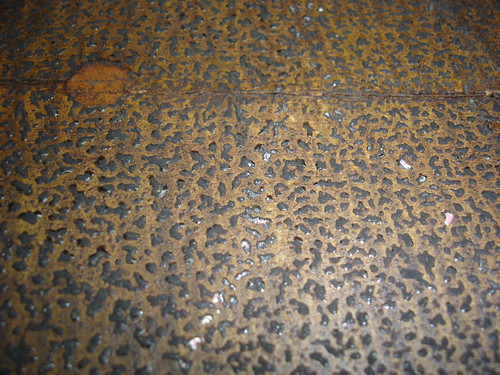
There are about ten cracks in the top ranging from these long ones to the usual short cracks near the FF tabs. And a nasty sound post crack that will come together OK but require an inlaid patch.
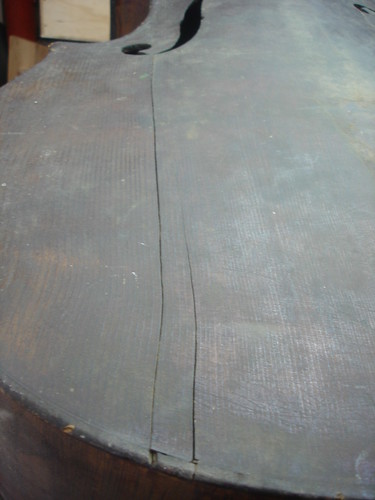
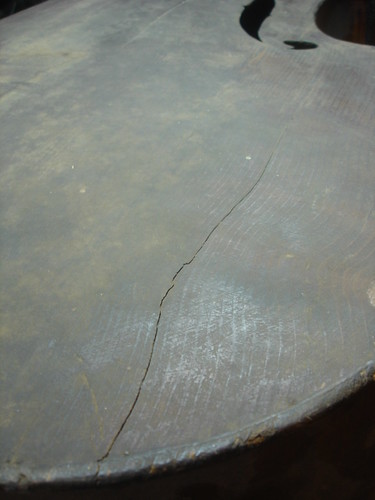
Corners are worn but repairable. This is the worst one.
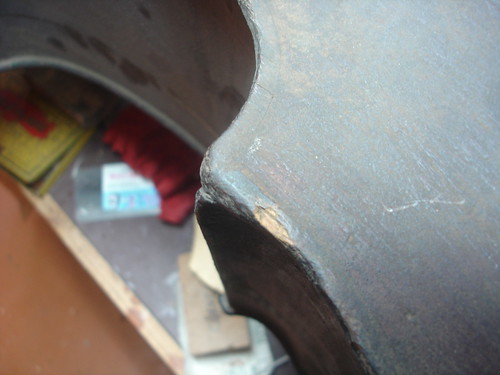
Inside the top block looks like a bit of a mess, and I think I can see a dowel AND a coachbolt and a split.
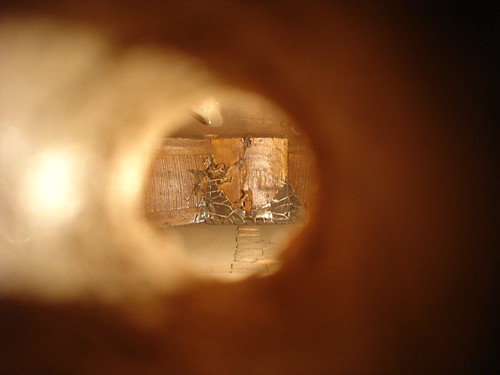
The single wide centre brace is typical of French basses but has split in several places and will likely need to be replaced. Not looking forward to that one. The back seam has shrunken and there is one crack as shown but other than that the back is in good condition.
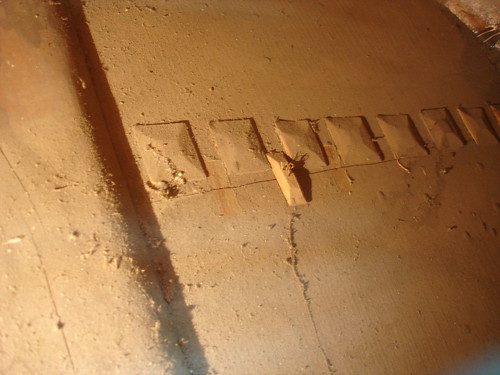
First evidence of home repairs – a weird flat fingerboard held on with a bolt. And some pine blocks underneath, nailed in

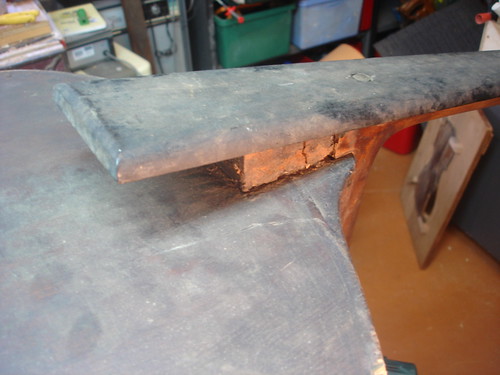
Neck heel badly damages, evidence of both professional and home repairs. You can see evidence of a dowel plug on the right near the button.
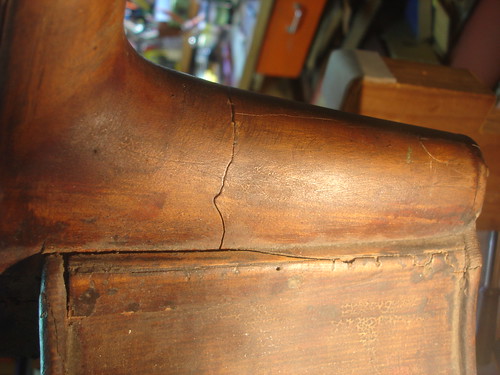
The ribs have numerous cracks, some repaired, but all the wood is there … and it is lovely wood, as per the back.

Next step is to open up the instrument to have a look inside.
Removing the top went OK until I hit these nails in the lower and upper bouts.
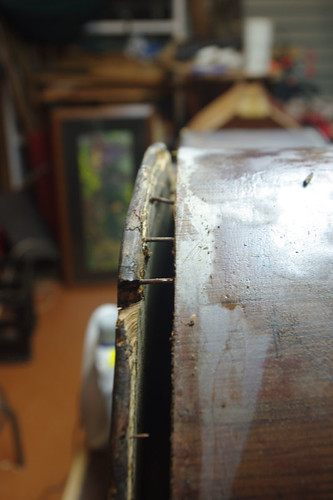
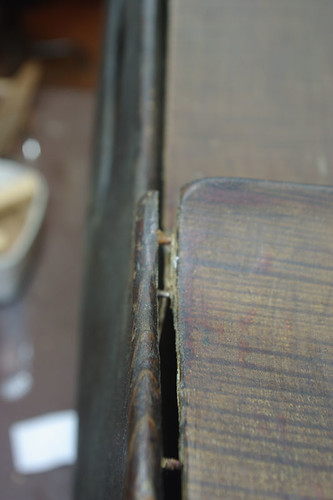
The bolt holding the neck together came out with a little persuasion.

As I thought, the bolt had several companions!
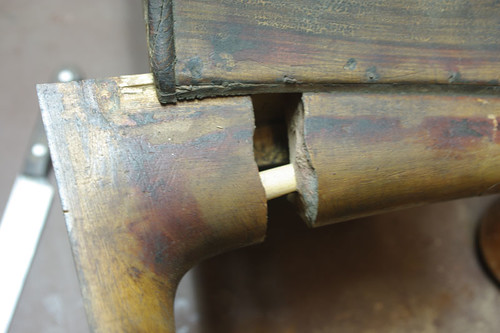
Top off, time to take a closer look:
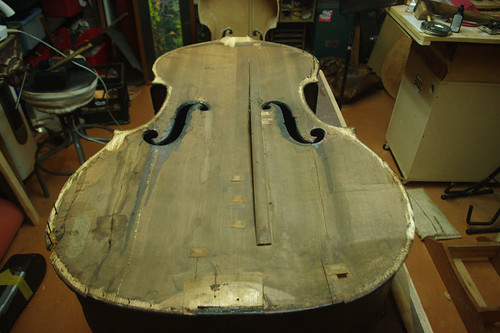
Ugly piece of work.
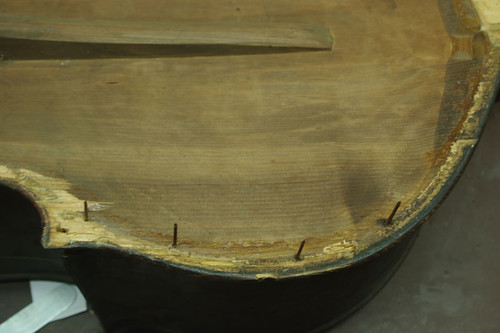
Bottom block area shows previous repairs as you’d expect from a bass of this age.
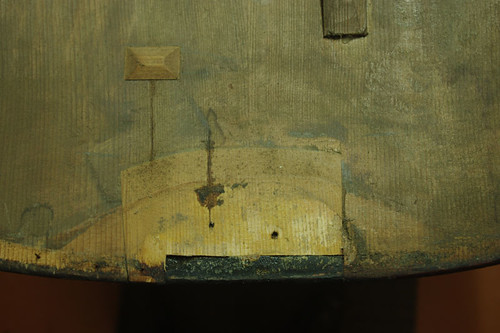
Top block similar
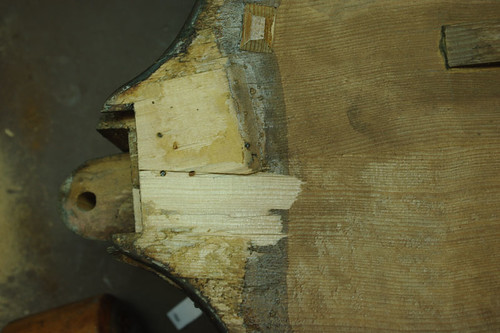
here’s one of the nastier cracks and edge damage caused by nails and putty! I was interested by what looked like a signature across the linen strip, but once cleaned it appears just a zigzag mark with a pencil. So we know for sure the bass was repaired by Zorro.
There seems to be some kind of orange primer used at some point; perhaps its a ground?

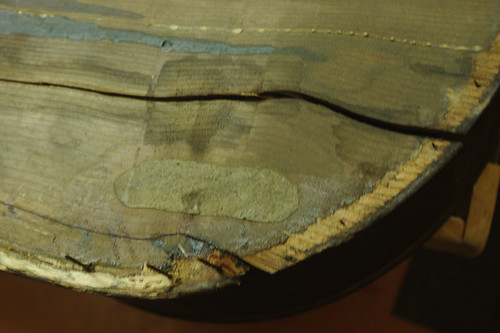
Common cracks here. You can see the glue beads of an old white-glue repair on the RHS
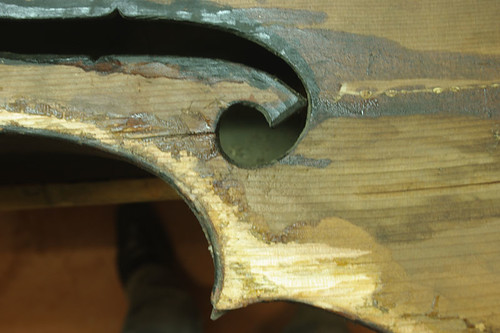
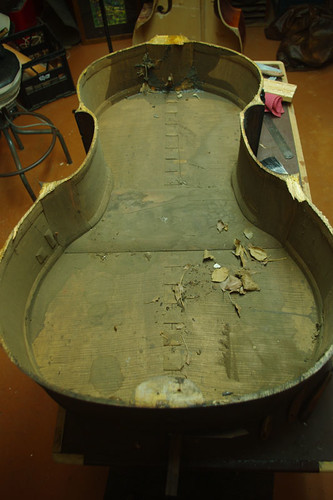
Inside the top block – can see splits, and yes, a failed dowel repair PLUS a coach-bolt PLUS a whole load of black resinous stuff, probably resorcinol or something like that.

Some successful repairs. Look at how thick the C bout linings are on the right hand side! They are really well made, and the centre brace sits very snugly up against them.
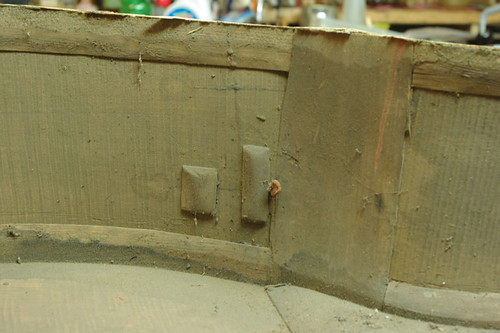
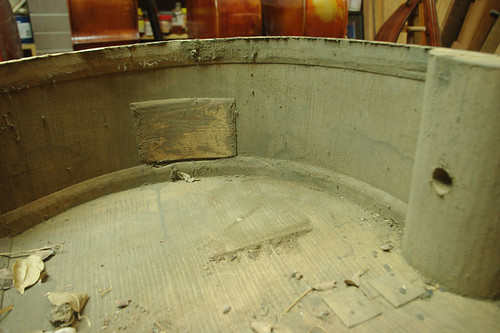
And some failed ones that I’ll have to redo. But look at how smooth and well-made the blocks are!
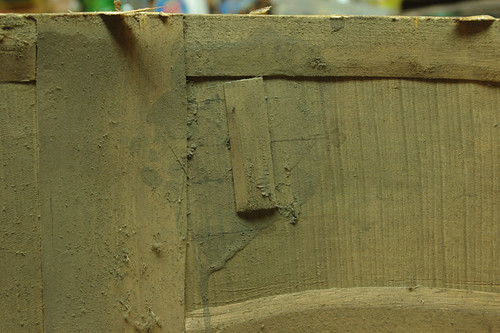
These were put in from through the FF holes I think.
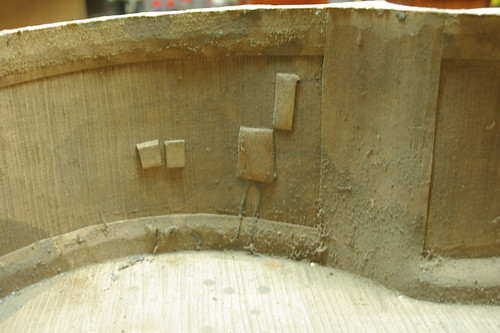
The mortise still has the back of the heel firmly attached. I’m not going to worry too much about this as I have to replace the whole block anyway.
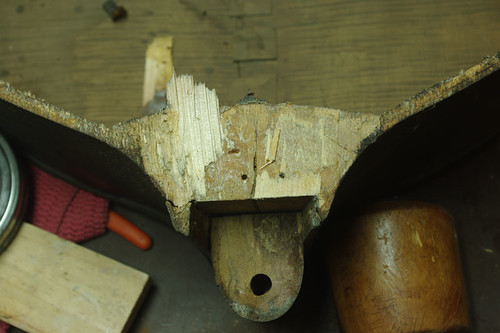
Altogether, this heel had one wooden dowel from back of heel diagonally down into the block, which obviously failed, and which was followed by a coachbolt through the same hole and down into the block at another angle. I reckon THIS is what split the block. Then another dowel through from front to back, (probably through the button) which obviously failed, so this was followed by a threaded rod right through from button through to the rustic fingerboard! Here’s a summary of the ironwork I’ve removed from this patient to date:
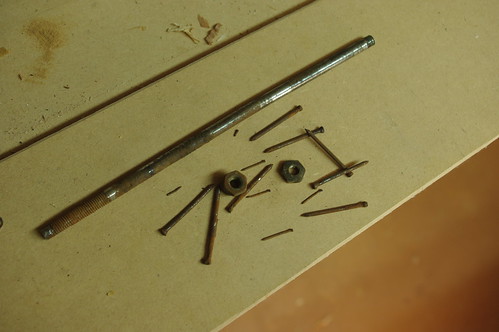
I had a look to see if the tuners had any identifying marks, but nothing exciting to report. Some of the brass plates are worn at the bearings, but the brass cogs, spindles and the worm gears are perfectly fine. We’ll have to decide whether its worth getting the bearings rebuilt, rebushed or just get new tuners. I’m not a metalworker. Any suggestions?
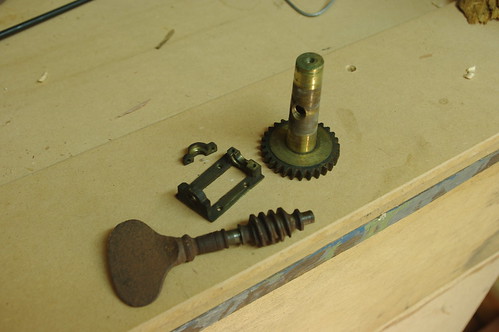
Here’s another bit of fun for later

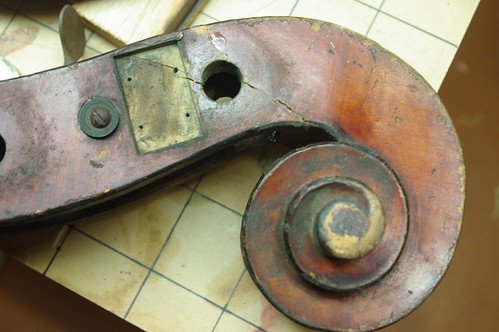
I started gluing some of the newer and cleaner cracks first, and cleaning up glueing edges.

My “in situ” lamp is very useful.
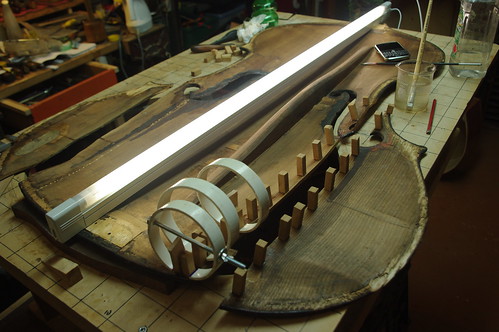
Here’s a horrible mess to clear up. Nails didn’t help at all.

Here’s a closeup of one of the crack edges. The wider part is where the crack sits just below the FFs and the thinner part - about 6-7mm - is the lower bout.
I have had to break the longer cracks right open in order to properly clean the gluing surfaces, which are contaminated with varnish and dust and goo. And what looks like read lead paint in places!
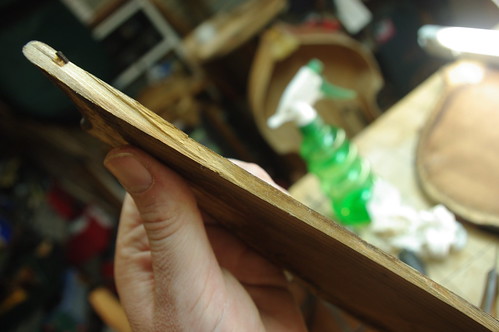
This is a dry run of the first big crack clamping setup. It gets tricky near the FFs where the wood has twisted under bridge pressure. It’s going to be interesting getting this to clamp up tightly.
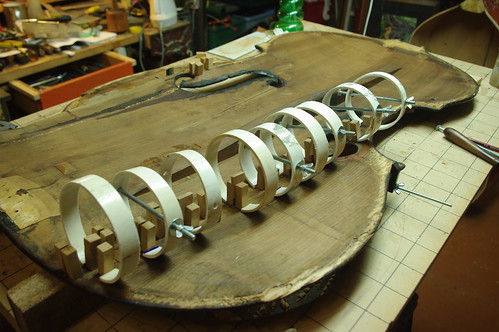
The top is glueing together quite well. This is the first long crack after the turrets are removed and before cleanup and cleating. Looks a mess, but actually the repair is good.
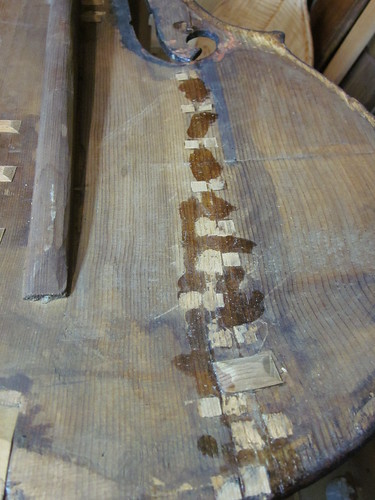
This is the view from the other side, there were two parallel cracks but they've come together quite neatly! The wood is beginning to show through too, after some cleaning with warm water.
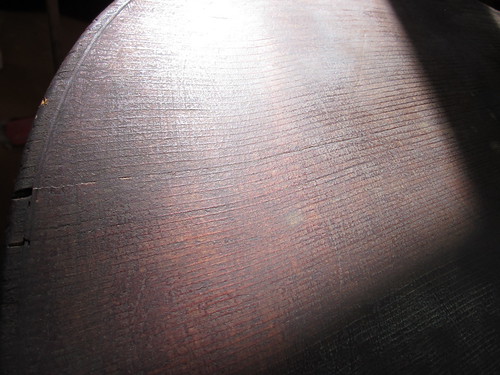
Here's the second long crack gluing. You can see the soundpost crack too; I mark the path of each crack with a chinagraph marker so I know exactly where I have to cleat later. Sometimes the glue line is virtually invisible.

This is one of the previous repairs, done quite well, but I don't like square cleats so I'll probably remove them and replace with diamond ones.
The bass-bar on this bass is exactly parallel with the centre seam.

This is a view of the soundpost crack. nasty.
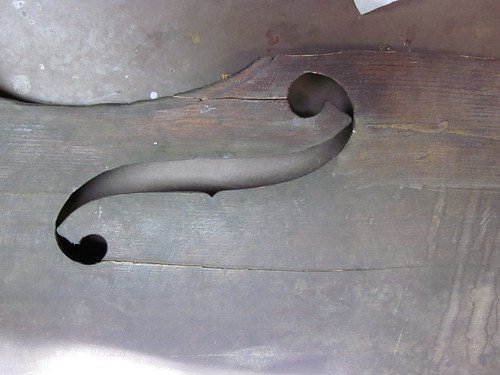
The corners were badly worn and needed restoration.
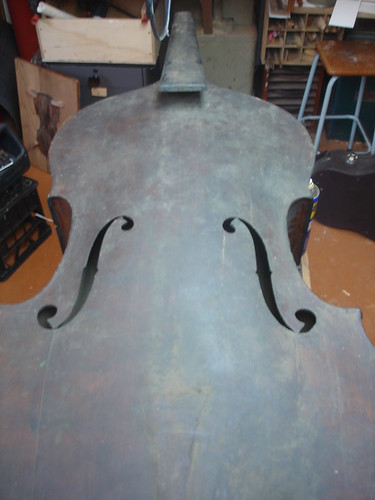
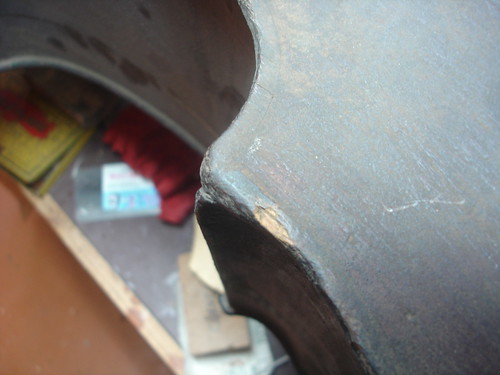
After gluing most of the belly cracks (I found a few more) I had a go at repairing the corners with the nice repair wood I got from Martin, but i wasn't happy with the result, as the grain really didn't match. The grain on this bass top is very wide at the flanks, and wavy. So I tried using a reed-by-reed technique i discovered online a week ago.
I cut away a part of the damaged wood along the grain line, then glued in a single piece of wide grain spruce. Then trimmed it back, and then added another.
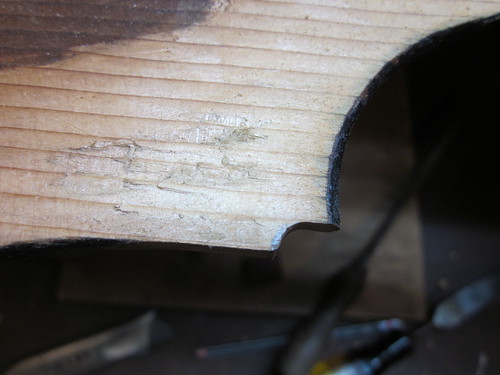
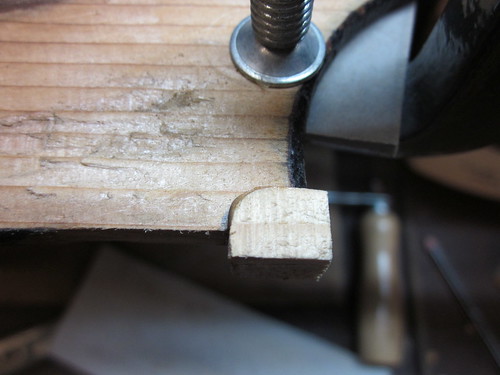
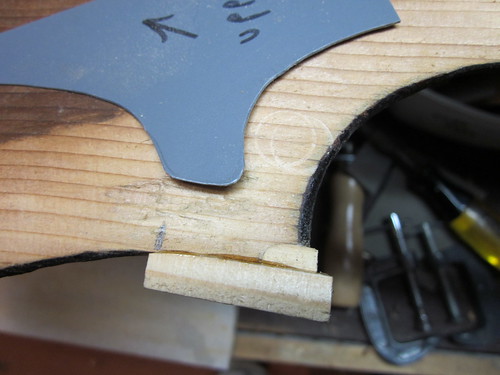
This last picture is only a little larger than lifesize. The grain is about 5-6mm
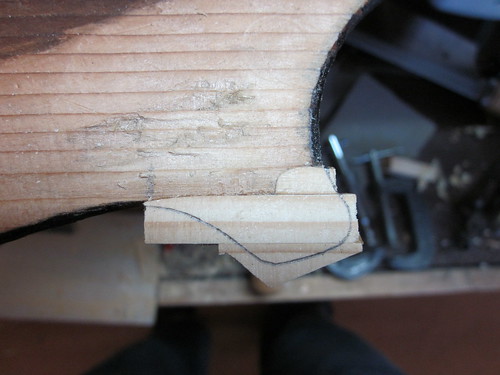
I'm working from the back here but i check the front to make sure the grain lines are reasonably straight. They will be covered in a dark varnish, but with purfling repaired they will look much better.
I addition, these corners - and a lot of the edges - will get a half-edging repair. so what you see above will be covered with perhaps 2-3mm of tighter grained spruce, which will be better for gluing to the blocks! ---
This is a previous repair to the block area of the lower bout
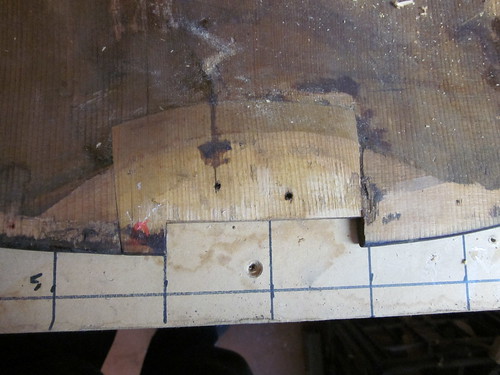
However, cracks have developed along one side and i don't like the previous repair or the nail holes so I'm removing the old repair and replacing with new wood.

I've removed all but the last 2mm of the top wood and tapered the edges inwards so that the patch fits tightly and the repair edge doesn't align with any grain. I've lost a bit of the very brittle purfling near the saddle but this was falling away anyway.
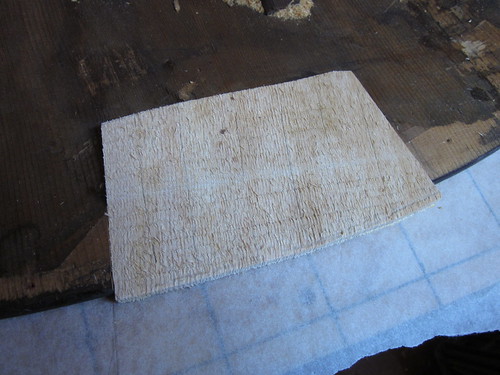
That's the patch glued in. Still has to be planed flat.
There was a similar problem up the top end. 2" nails through the top had made a nasty mess and a fair bit of wood had come away when removing the top from the block. And a previous repair. You can see my first exploratory gouge to see whether I could do an inlay patch, but nup. Had to go further to make sure the repair was sound.
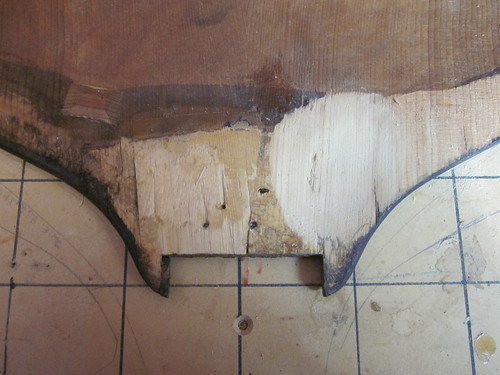
I had to remove only enough spruce till I got to reasonably sound wood. I filled the nail holes with sawdust and hide glue from the back; i'll do a better repair from the front, later.
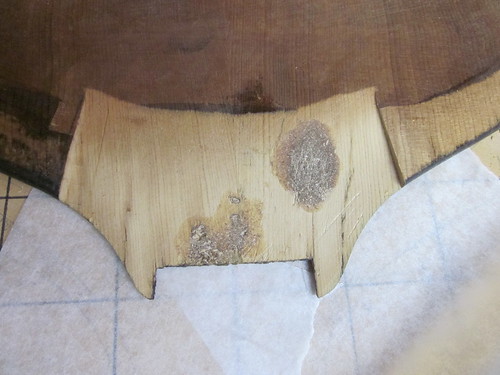
here's the patch glued in, waiting to be trimmed back.
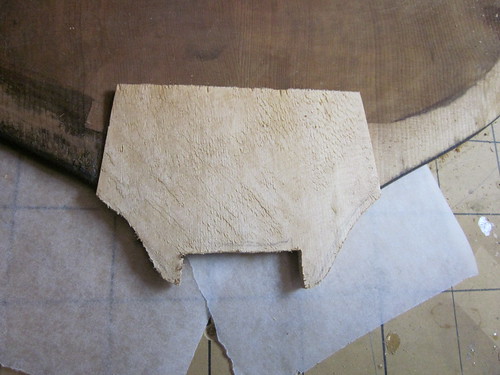
This is what nails do to the edge! I've planed back the crumbly chipped edge back to clean wood.

closer, you can see what this spruce is like. Wavy, wide-grained, with a few brittle knotty bits at the flanks like this

or this bit of repeated trauma which has pulverised the spruce under the varnish. I have to plane back as far as i dare then do the rest with glue and new spruce edging.
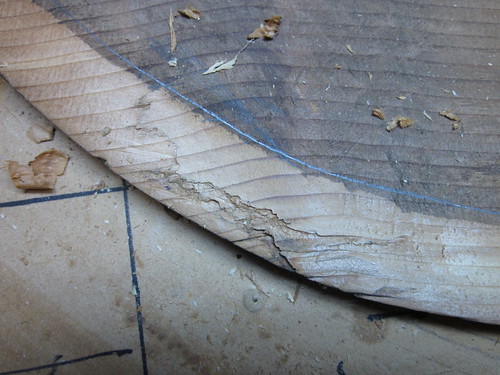
This new spruce is much nicer to deal with and will properly strengthen the original edges. It will glue better, too.
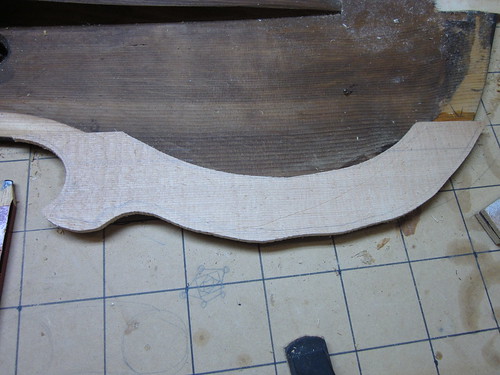

The wood is brittle and knotty in spots all around the edges; this is a weak point, has cracked before, and even to plane it down I need to wet it down and use a very sharp blade. LOVING the new HNT Gordon!
Here it is after thinning the edge carefully, with (I think) a piece of the famous arsewipe kermode spruce, ready for patching. Other than the staining, it's fine repair wood!
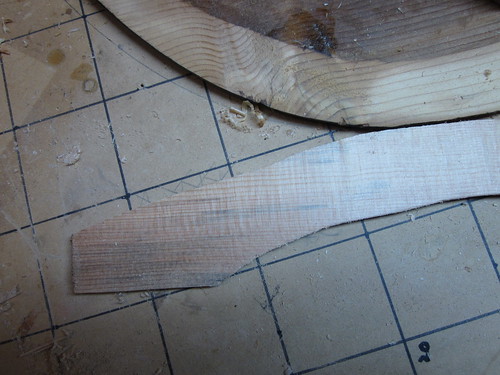
You never have too many clamps.
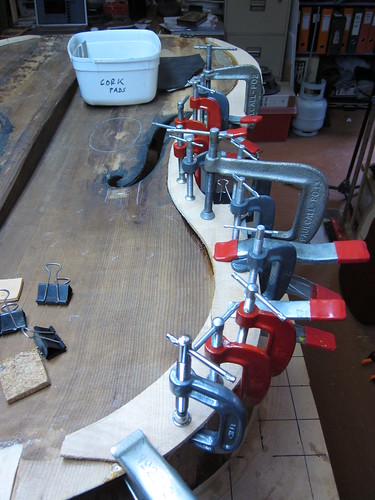
After the hide glue has dried, the edges are carefully trimmed and blended into the original top shape, and then thinned to the original 8mm. Sounds easy, eh!
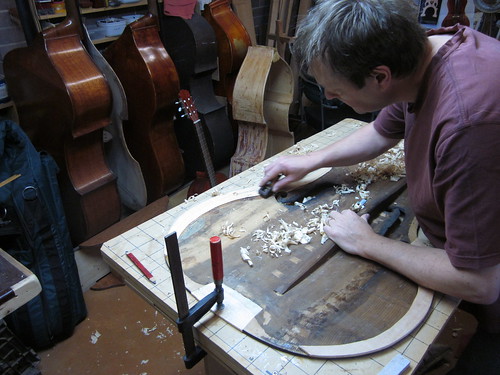
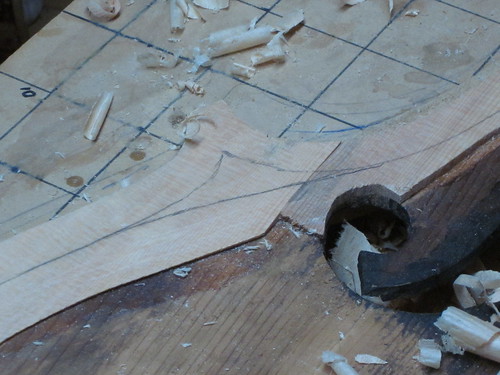

I like this shot:
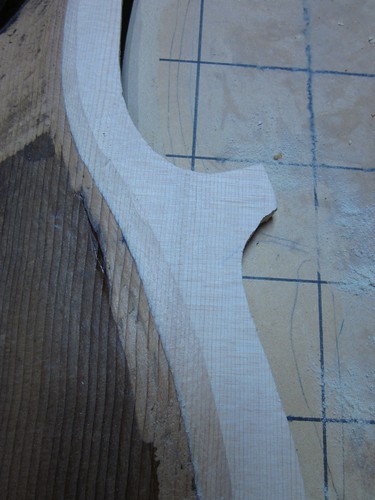
A view of the plate edges.
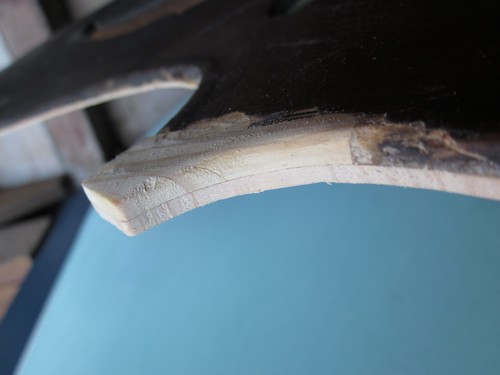
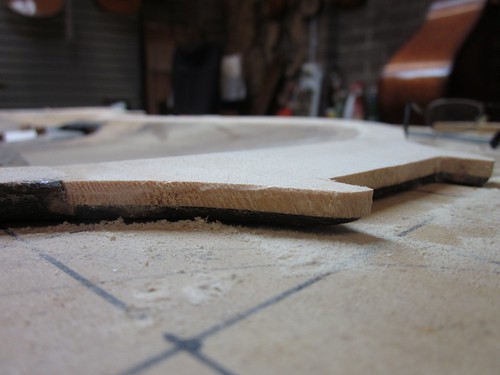
I have not worked on shaping the edges yet. And i'm going to have to sweat over the purfling in the corners
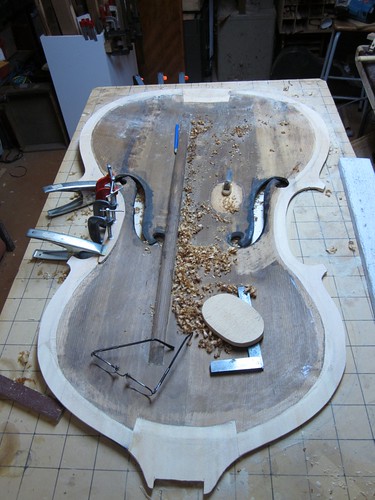
This is where we started:
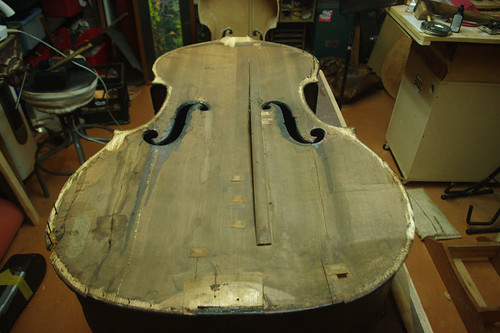
Next job is the soundpost patch. Remember this great big soundpost crack?
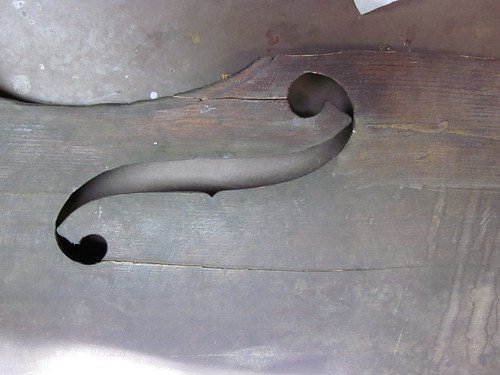
I glued it up well, but if this isn't reinforced properly the glued-up crack will just bust again when the pressure's on. So, working from the back, I make an oval patch from spruce and trace around it, then start hogging out a bit of a hole.
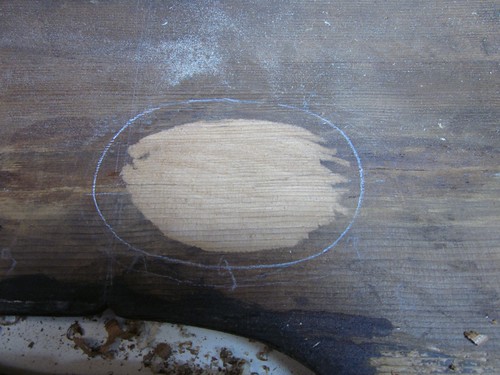
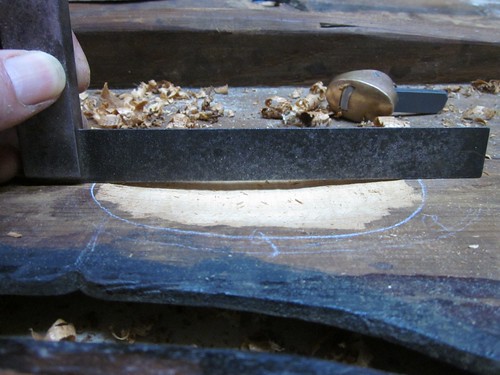
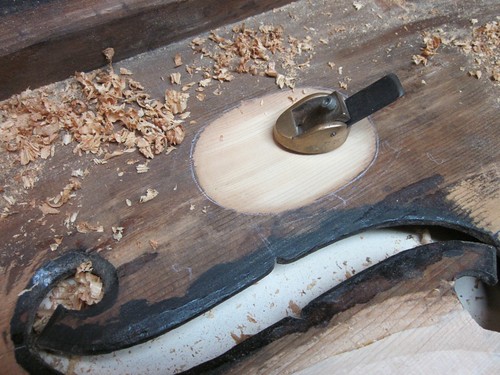
Mustn't get carried away ...
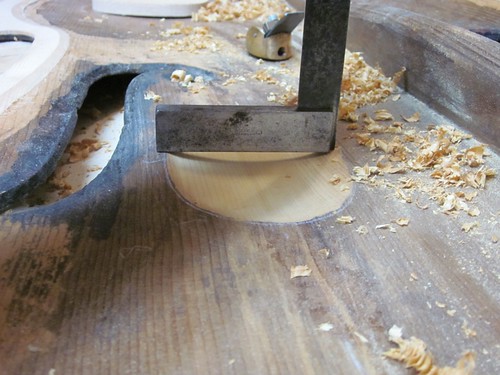
I like this next pic, because it shows up the depth - around 2-3mm - of the darkening of the wood due to age! Someone who has done this on many more basses that I have could probably date the thing looking at the colour alone! You can see the original crack entering at the left and a slightly darker area where it is glued. I think the right depth and shape of the curved bed is important.
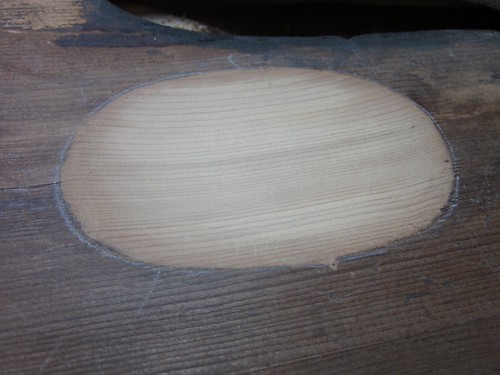
Next step is to spot glue some guides for the patch to make sure it always goes back exactly in the same spot. There a many ways to do this, and this is the way i'm doing it this time! The grain of the patch is slightly offset from the grain in the top.
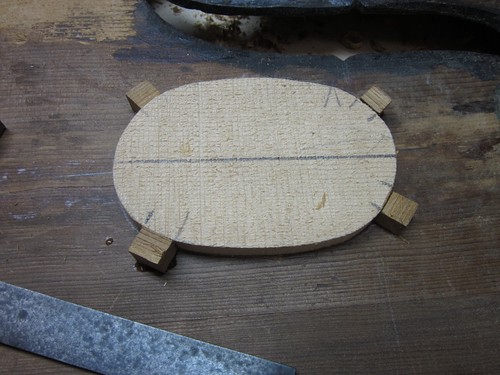
---
The soundpost inlay patch is shaping up well. So I'll finish it off and glue it inplace
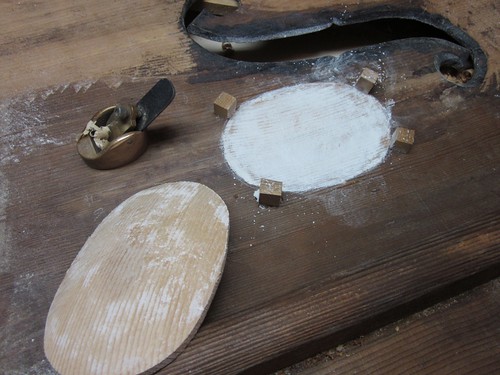
The bassbar is intact, well glued and solid. It is placed exactly parallel with the grain of the top, which is usually a no-no. I haven't yet decided whether to replace it or leave it. Here's the patch just before gluing in:
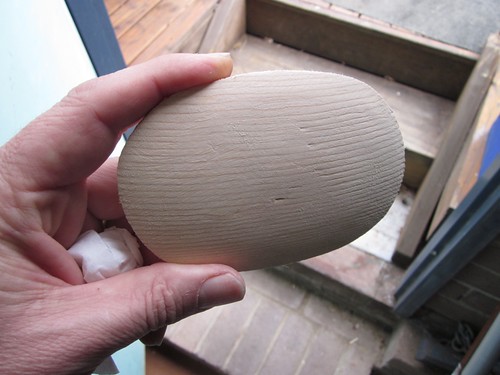
And here's the patch glued in and trimmed:
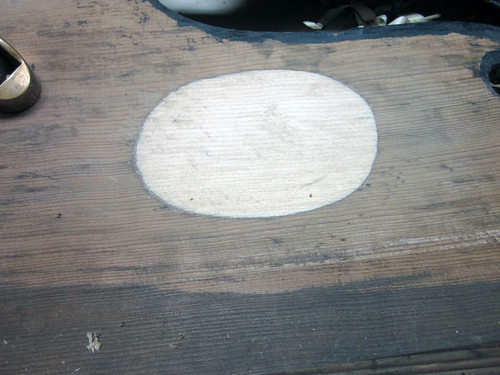
You can see how nicely it fits at the edges. I'm pretty happy how it turned out

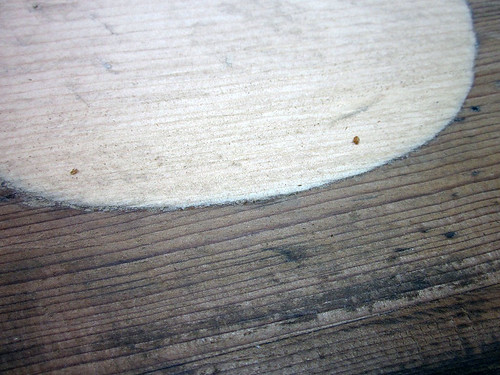
I decided that I *would* shave the thin dark layer off the surface of the wood, at least as far as the bass bar, and I'm glad that i did. These patches look as if they are reinforcing the main centre glue line.
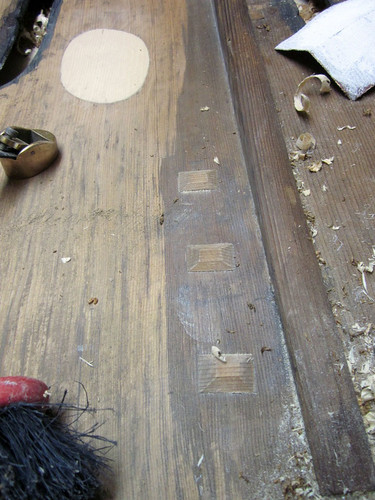
But when the dark layer is removed, it's very clear that there's another previous crack there that I couldn't see before (see next pic). It's a bit of a pity to remove the dirt/patina, but going back to clean wood is going to allow me to make better repairs, and as the purpose is to result in a functional bass, I think the decision is sensible.
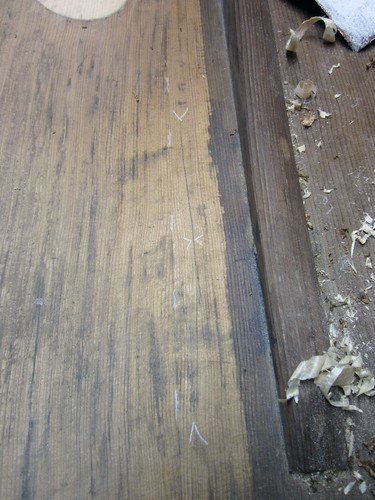
This is a nice view of repaired top to date.
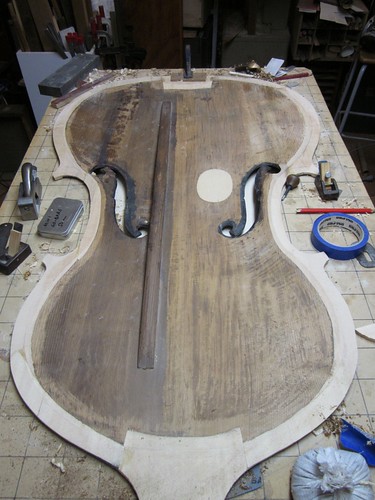
We've made it from here:
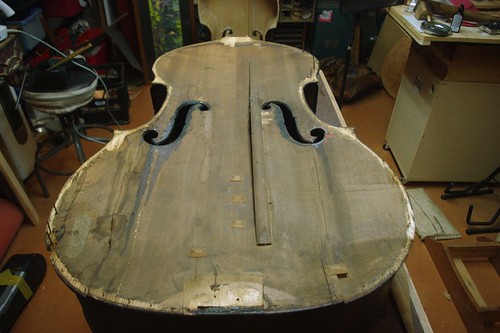
to here:
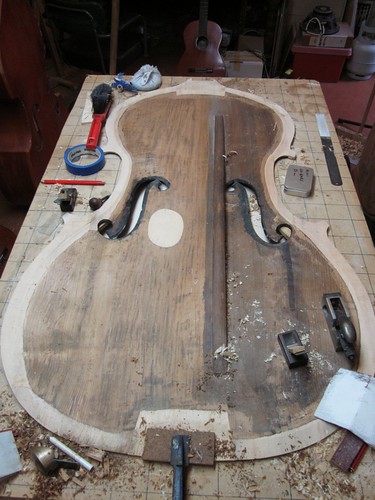
And I really MUST do something about getting a consistent colour-balance! I wondered whether or not to remove the internal patina, scraping the nice old dark surface back to clean wood. Eventually I made a judgement that it would be better to shave a very thin layer off and make sure I make good glue repairs, than leaving it there for the looks only. The wood is still darkened with oxidation, and there is no doubt about the age of the instrument.
Here you can clearly see what I'm doing.
On the left hand side is the colour of the wood as the bass came to me. Yes it is oxidised but also has traces of old glue and no doubt tobacco smoke and other muck. You can clearly see the white new wood i have added, and then the areas I have scraped back to clean old wood in the foreground. I've left, for the moment, a strip alongside the bass bar. If I decide to leave the bar, I'll leave the dark strip as well. If I decide to replace the bar, I'll probably scrape it back too.
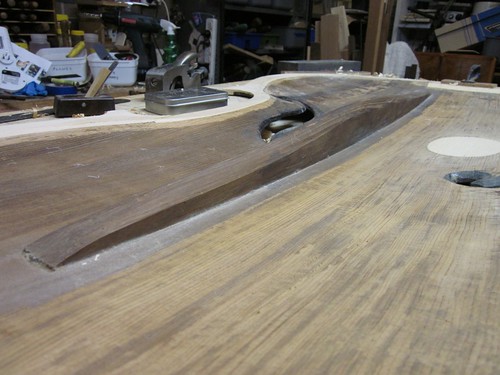
33.5Hz

45Hz
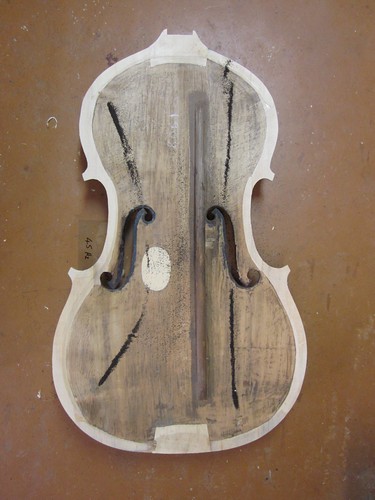
77Hz
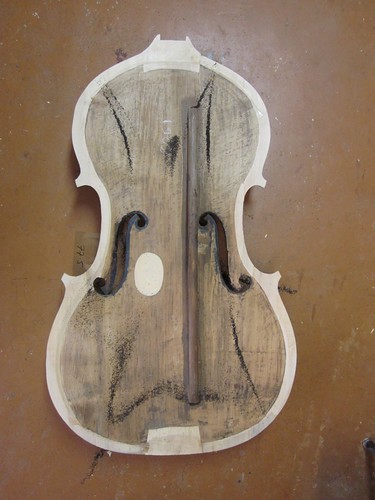
98Hz
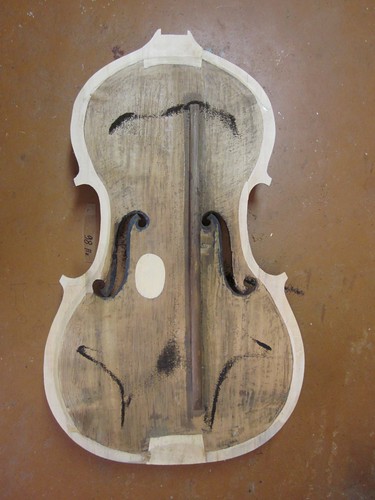
119Hz
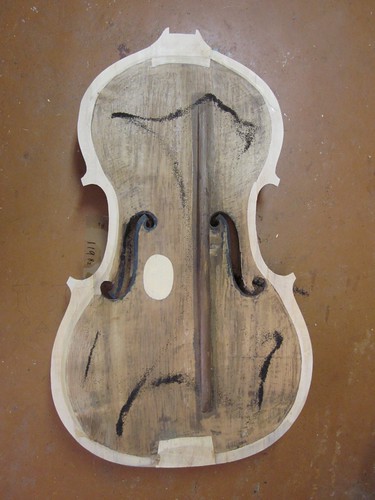
the plate weighs 1908g. For me the Chladni patterns are merely a way of measuring in a pictorial way the flexibility of a plate. The plates all exhibit these "modes" of resonance to one degree or another. The lower the frequency at which the modes appear, the more flexible the plate and vice versa. Each mode means something slightly different, for example the first mode is a twisting mode where at this frequency the top and bottom bouts are oscillating in opposite directions. In the second mode they are moving in the same direction, and the centre of the plate is "pumping" the other way. Third and fourth modes are complex interactions between the first, second and fifth modes. The fifth mode shows the nodes of resonance where the plate is flexing longitudinally.
Obviously the wood is stiffer this way so the frequency is higher.
On their own the patterns mean little. However when you have a number of different plates measured this way you can start to analyse and make some educated guesses as to what and why. For me, luthiery isn't a science; it is a series of educated hunches, and the better your hunches the better you are as a luthier.
What I glean from the fact that the lowest modes are at a higher frequency that the modes on the other basses I have measured, is that this plate is still quite stiff. I already knew this from feeling the plate, but how much i might try to lighten or un-stiffen the plates is a matter of following a hunch, and the more information I have the better the hunch will be..