I really enjoy reading the threads of peoples builds, so hopefully this will be of interest too.
I built my first two acoustic guitars side by side. I found that I really liked swapping between them, they were usually at slightly different stages but not so far apart that I had forgotten the things I'd learnt on the one before, so when I ended up with a reduced set of plans for the OM I am now about to start for yours truly, I decided to build them both at once.
I'm going for the mould method this time, so job No1 was to build those. Thanks to all tutorials on this site, this is the result so far.
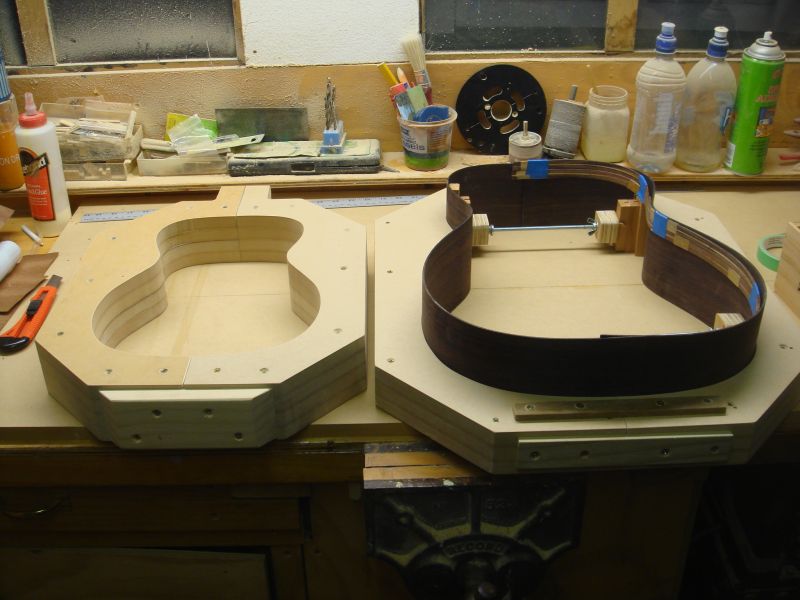
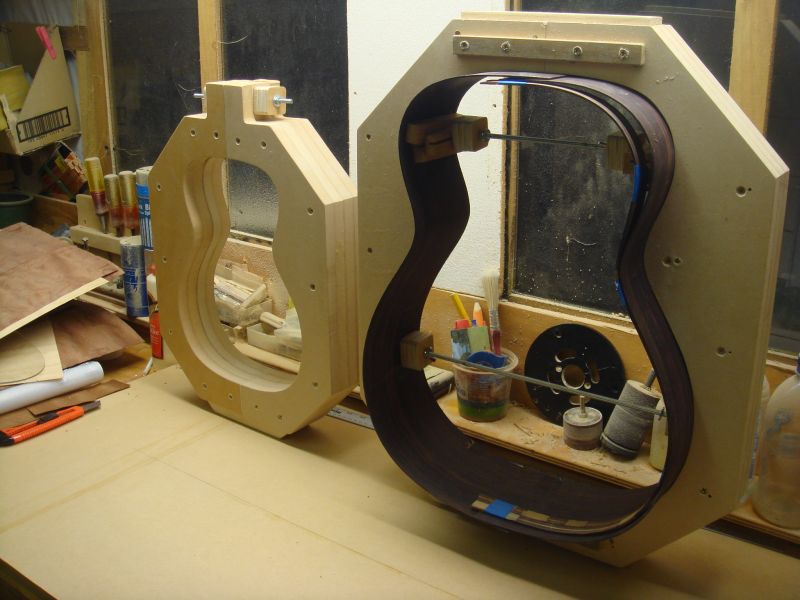
I am going to put a couple more layers on the OM mould to make it deeper, but I will screw them on so I can remove them if I need to, to get at kerfing etc,
The rosewood sides are sitting in the OM mould. I have a master grade redwood top and spruce bracey bits for inside, ebony fretboard and bridge. The neck is an LMI premade bolt-on jobbie, so I am cheating a bit there.
Mini-me on the left, is going to be built out of odds and sods lying around the workshop and anything I can lay my hands on. The latest idea was to use veneer laminate for back and sides for this little beauty. It is currently awaiting the outcome of experiment No2 with laminating veneer.
Here is the result of experiment No 1 - not entirely successful!!
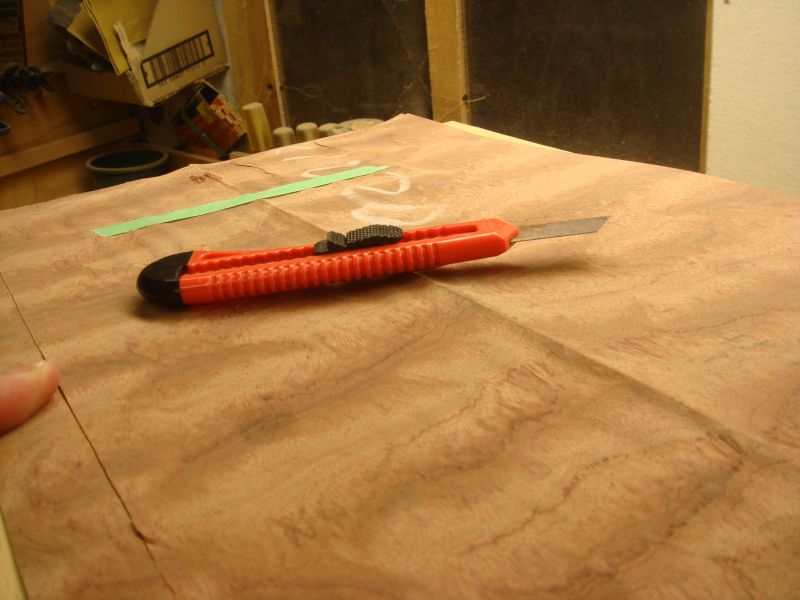
I'll have a go with epoxy (Thanks again Tim!) and attempt a laminate rather than faux plywood. If that doesnt work I will have to have a go at bending some sides, which to date I have been too chicken to attempt.
I think this will all take a while, as I should be doing a Martin in mid to late August and taking off into the Pacific for work for about 4 weeks, then my daughter gets married in October and I suppose I'll have to come out of the shed for that, so it will be a case of luthierus muchus interruptus.
Thanks for looking, comments and suggestions always welcome.
BTW, supposing the veneer results don't improve, does anyone know where I can get tonewood in New Zealand? It hurts to pay as much for the postage as the tonewood costs
Cheers and thanks for looking
Richard