archtops?
Histring, I also made an archtop for my first build.
It can be done.....but go slow.
You don't need all the tools, but there are some you must have (you'll work it out - or ask here)
I didn't bother with using 2nd rate tonewood as I never intended the guitar to be a 'practice build', but then I never intended to build more than one.
Fool that I am, now I'm hooked.
Don't expect the first to be perfect.
Mine wasn't.
But it IS uniquely mine.
It IS more than just 'playable' and it IS the first guitar I reach for when I want to play.
(It's also the first most friends reach for when visiting).
Good Luck & above all - Enjoy It.
It can be done.....but go slow.
You don't need all the tools, but there are some you must have (you'll work it out - or ask here)
I didn't bother with using 2nd rate tonewood as I never intended the guitar to be a 'practice build', but then I never intended to build more than one.
Fool that I am, now I'm hooked.
Don't expect the first to be perfect.
Mine wasn't.
But it IS uniquely mine.
It IS more than just 'playable' and it IS the first guitar I reach for when I want to play.
(It's also the first most friends reach for when visiting).
Good Luck & above all - Enjoy It.
Wow, what a welcoming group
............many thanks to all.
Kim,
I followed your suggestion and contacted Tim, he advised that he may be able to help but is away at the moment, will get back to me after the 18th.
Craig,
Any advice re tools, etc., you wish to pass on will be greatly appreciated.
Just for the record, working with timber doesn't phase me, I have built the odd drum shell............catch is, I can't play the things to save myself, however, I have been playing the guitar since '62.
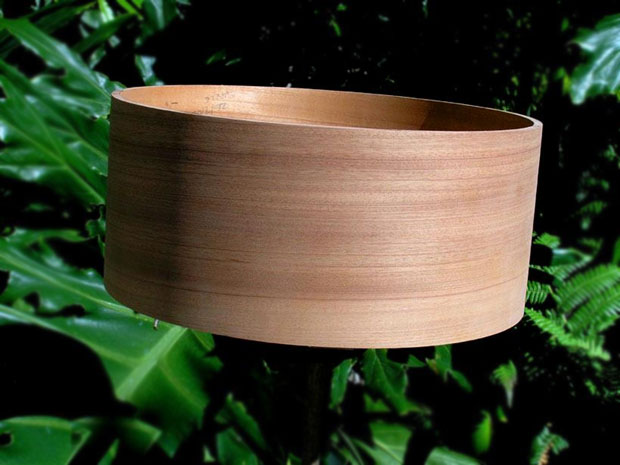
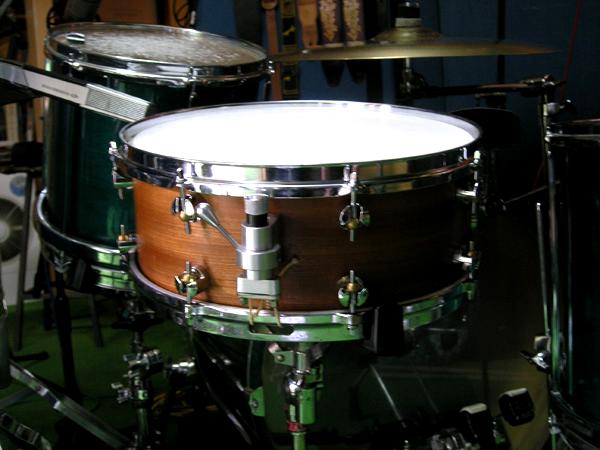
Apologies for posting stringless instruments
and for anyone who's interested, that shell is multiple plies (veneers) of Sapele.

Kim,
I followed your suggestion and contacted Tim, he advised that he may be able to help but is away at the moment, will get back to me after the 18th.
Craig,
Any advice re tools, etc., you wish to pass on will be greatly appreciated.
Just for the record, working with timber doesn't phase me, I have built the odd drum shell............catch is, I can't play the things to save myself, however, I have been playing the guitar since '62.

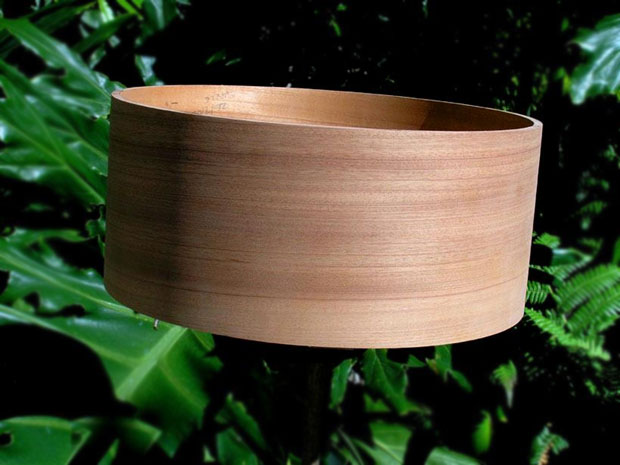
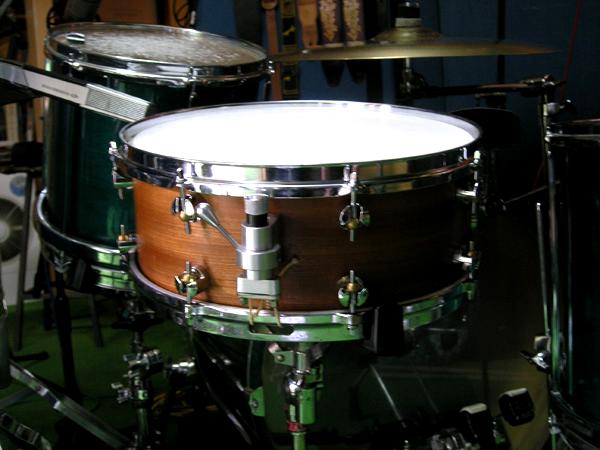
Apologies for posting stringless instruments

Music creates a kind of pleasure which human nature cannot do without.
wormy guitar
holy shite, that wormy guitar is the coolest thing ive ever seen.......ever. Is that from our bob connor or another bob? If so is it for sale. I think there should be a discount as the timber is probably not exactly master grade. Just kidding. I am into alternative art work and that thing is so very cleverly made. im gob smacked which dosn't happen much. Well done to whoever built it and what great vision.
The thread seems to be popular and it is interesting to see that there is healthy discussion in the area. I dont want to sell the archtop i will make, i think they are a very classy looking instrument but i havn't played one yet. Would love one in my collection.
Also, What is so expensive about the final product apart from the ridiculously expensive wedges for the soundboard? Is the time involved more than an acoustic guitar or not really. Sounds like a silly question but i really dont know on this one. Thanks for your help
The thread seems to be popular and it is interesting to see that there is healthy discussion in the area. I dont want to sell the archtop i will make, i think they are a very classy looking instrument but i havn't played one yet. Would love one in my collection.
Also, What is so expensive about the final product apart from the ridiculously expensive wedges for the soundboard? Is the time involved more than an acoustic guitar or not really. Sounds like a silly question but i really dont know on this one. Thanks for your help
The "Wormy Wood" is made by Teredo worms, actually a mollusk. Any wood that is left in the ocean along the Pacific Northwest Coast, and probably elsewhere is infested with these things.
The maker is Robert Benedetto
The maker is Robert Benedetto
- Nick
- Blackwood
- Posts: 3642
- Joined: Thu Feb 26, 2009 11:20 am
- Location: Christchurch, New Zealand
- Contact:
Hi String- Nice job with the shell! Do you make many? I used to hit the skins and lurrrrv wooden shells especially Piccolo's, the chrome shells just aint 'got it' as far as I'm concerned, the kit I had came with a chrome shell snare but that soon went and was replaced with a wooden shell. How did/do you cut the bearing edges, also I don't recognise the hardware, is it a generic brand or one of the known makers? Funny thing with drum hardware, it's the makers signature.
Xray- As Allen pointed out, that worm riddled archtop was made by the Master himself as one of his few personally made commissions. If I remember rightly, at the time it was worth US$28,000 and had a buyer before a plane even hit the wood. The Spruce was a bit that Brent Cole over at Alaska Specialty Woods gave Bob B about 20 years ago thinking it an interesting piece but didn't think it would be turned into the masterpiece it ended up as.
As far as your question on cost is concerned,it very much depends on where you are aiming to take your building.If you're making an archtop just for yourself or friends then you're only looking at the cost of the woods & materials to complete it (your out of pocket expenses) and are building more for the enjoyment of gluing bits of wood together. If however, somebody else is paying for it then your time has to be brought into the equation, I kept a record of the hours on my first build which totaled up to about 150. Even the basic factory built models over here in NZ are costing NZ$3500 with alot fewer hours to build, my basic archtop (Sitka top, Big leaf Curly maple back & sides & Tobbacco burst) is only $500 more. For that, someone is buying an instrument that has been made with the final voice of the guitar being the primary goal, the top has been voiced, back recurved to respond to it's best. I somehow suspect that factory produced models don't get quite the same focus, braces are mass produced, tops are carved all exactly the same on a machine & the same with backs, standard recurves are carved in and the guitar given a nice shiny, sparkling coat of paint. I'm not saying that this is a bad thing,they are focussed on mass production and it wouldn't be economically viable for them to spend alot of time on each individual guitar.
Bob Benedetto charges so much because of his name, you are buying 30+ years of experience, he makes only a very few per year (market ain't flooded with them so each one is different & collectable) & you are buying an instrument that is special and plays that way.
Xray- As Allen pointed out, that worm riddled archtop was made by the Master himself as one of his few personally made commissions. If I remember rightly, at the time it was worth US$28,000 and had a buyer before a plane even hit the wood. The Spruce was a bit that Brent Cole over at Alaska Specialty Woods gave Bob B about 20 years ago thinking it an interesting piece but didn't think it would be turned into the masterpiece it ended up as.
As far as your question on cost is concerned,it very much depends on where you are aiming to take your building.If you're making an archtop just for yourself or friends then you're only looking at the cost of the woods & materials to complete it (your out of pocket expenses) and are building more for the enjoyment of gluing bits of wood together. If however, somebody else is paying for it then your time has to be brought into the equation, I kept a record of the hours on my first build which totaled up to about 150. Even the basic factory built models over here in NZ are costing NZ$3500 with alot fewer hours to build, my basic archtop (Sitka top, Big leaf Curly maple back & sides & Tobbacco burst) is only $500 more. For that, someone is buying an instrument that has been made with the final voice of the guitar being the primary goal, the top has been voiced, back recurved to respond to it's best. I somehow suspect that factory produced models don't get quite the same focus, braces are mass produced, tops are carved all exactly the same on a machine & the same with backs, standard recurves are carved in and the guitar given a nice shiny, sparkling coat of paint. I'm not saying that this is a bad thing,they are focussed on mass production and it wouldn't be economically viable for them to spend alot of time on each individual guitar.
Bob Benedetto charges so much because of his name, you are buying 30+ years of experience, he makes only a very few per year (market ain't flooded with them so each one is different & collectable) & you are buying an instrument that is special and plays that way.
"Jesus Loves You."
Nice to hear in church but not in a Mexican prison.
Nice to hear in church but not in a Mexican prison.
OK then.
For those new to archtops & those with an interest I'll post a pictorial of my first build.
Archtops arn't that hard
First work out your rough 'carve to' shape & drill holes to that depth
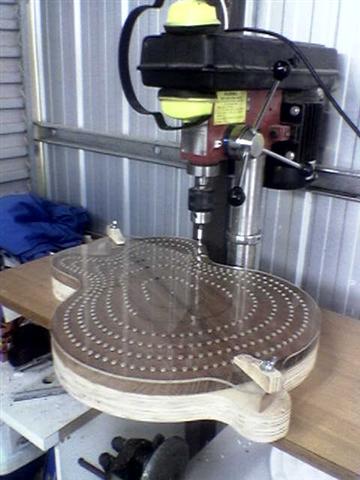
Get yourself a plane & start carving the outside.
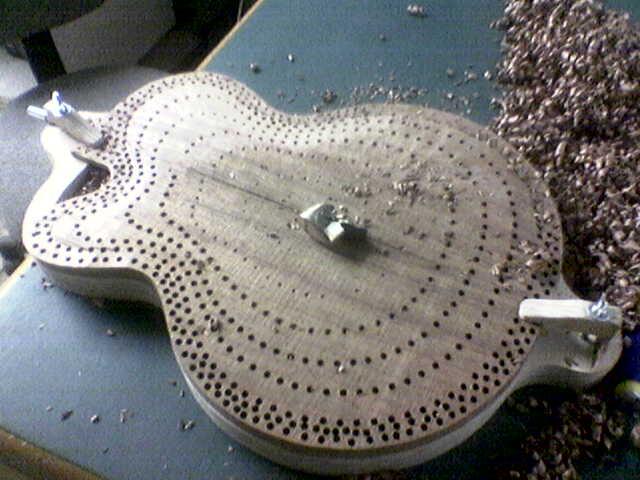
Eventually a shape will emerge
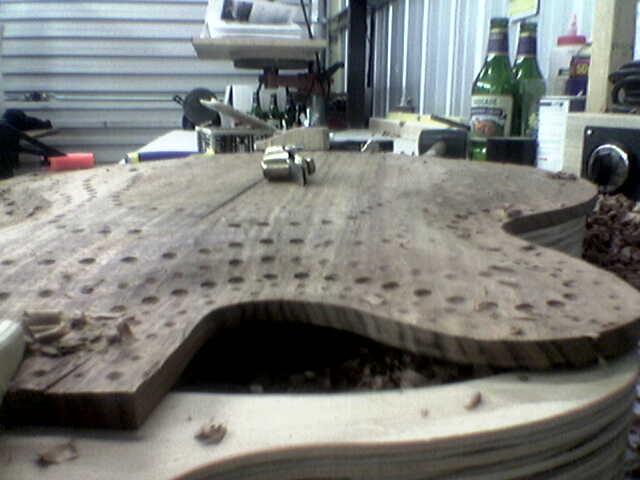
Flip it over & carve out the inside
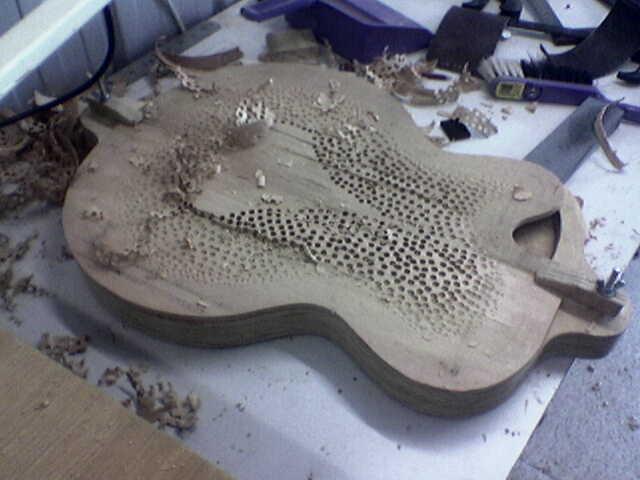
Get the topwood & start all over again......

Since this build I have bought the full size palm plane & discovered toothed blades
For those new to archtops & those with an interest I'll post a pictorial of my first build.
Archtops arn't that hard

First work out your rough 'carve to' shape & drill holes to that depth
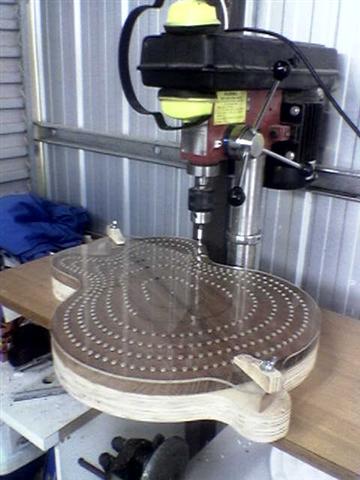
Get yourself a plane & start carving the outside.
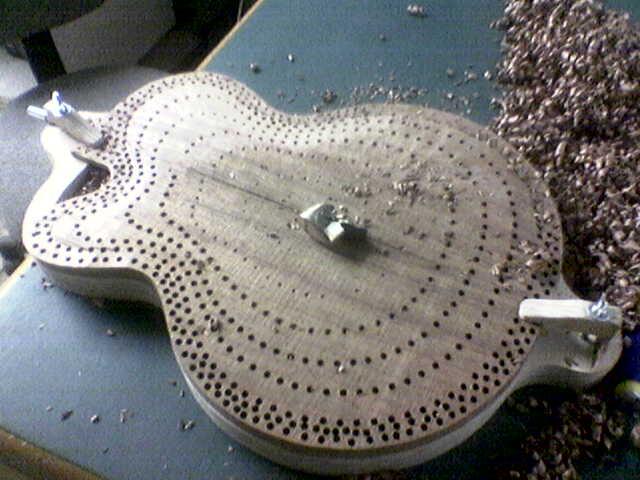
Eventually a shape will emerge
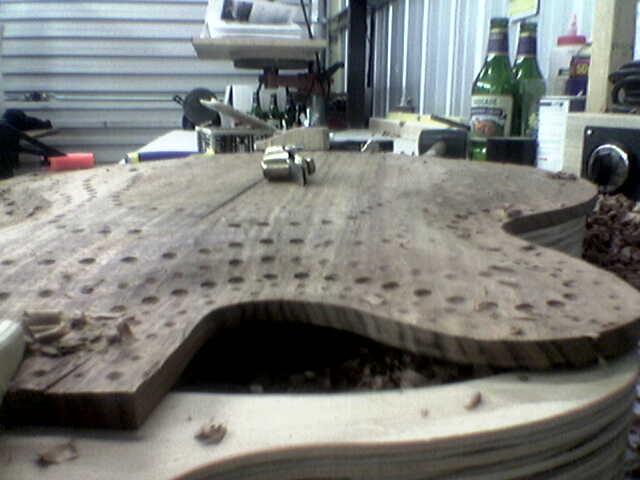
Flip it over & carve out the inside
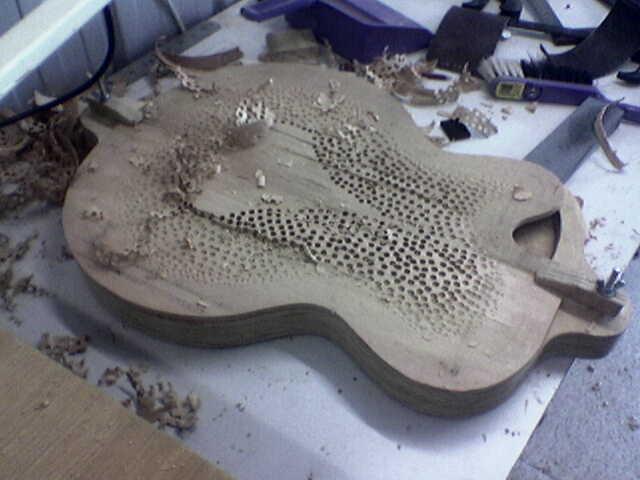
Get the topwood & start all over again......


Since this build I have bought the full size palm plane & discovered toothed blades

Figure out a way to thin the sides
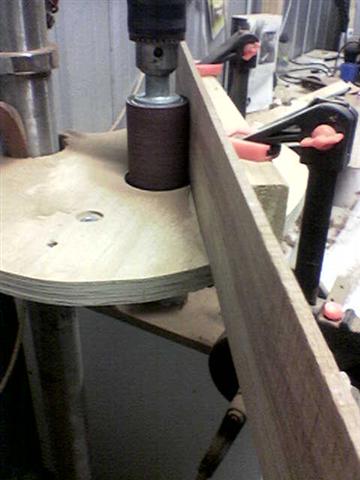
Bend the sides to shape (photo taken showing an offcut from the sides)
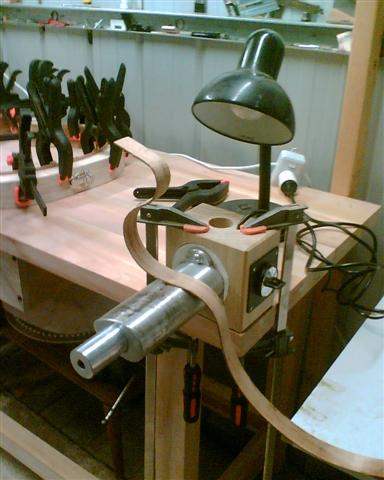
Stick sides in mold maintain shape
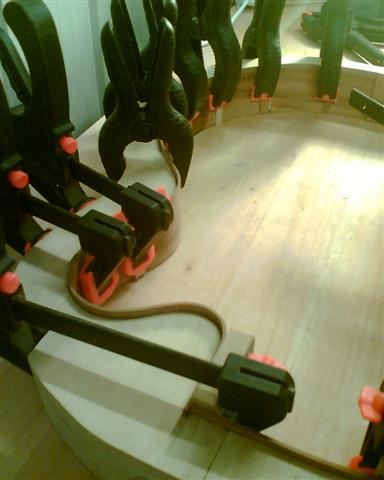
Add head block, tail block & linings

Level everything & glue on the Back.
Chuck on a hastily made label & give all a coat of sanding sealer.
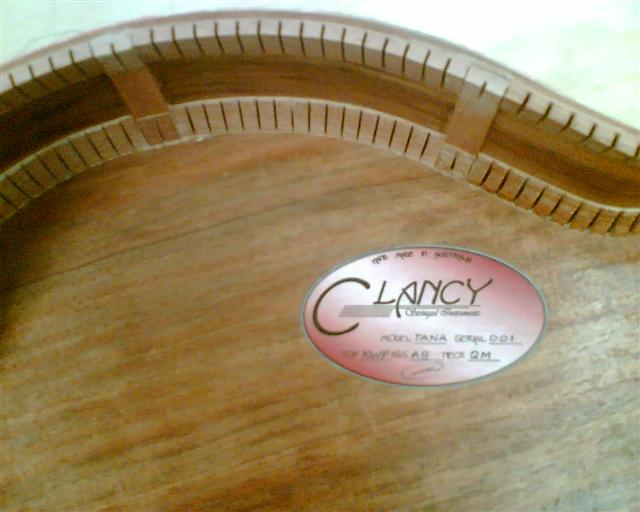
Glue on the top & voila - you have the box!
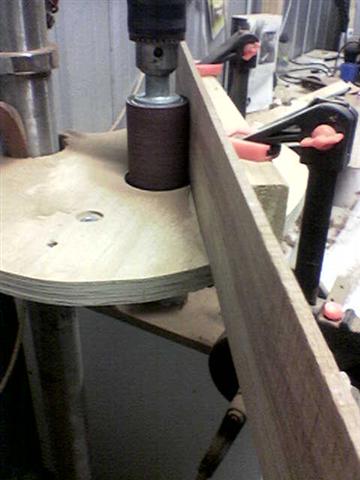
Bend the sides to shape (photo taken showing an offcut from the sides)
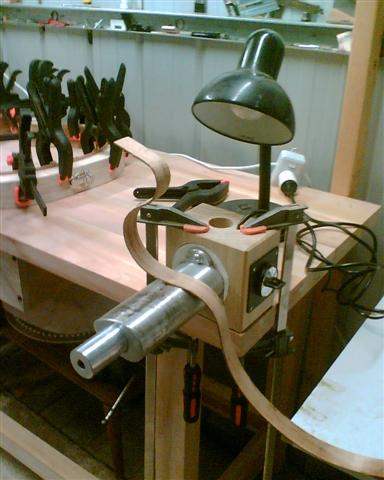
Stick sides in mold maintain shape
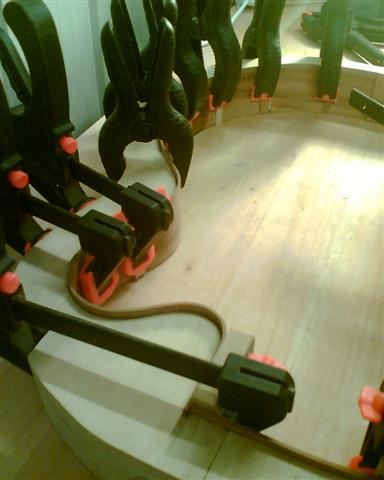
Add head block, tail block & linings

Level everything & glue on the Back.
Chuck on a hastily made label & give all a coat of sanding sealer.
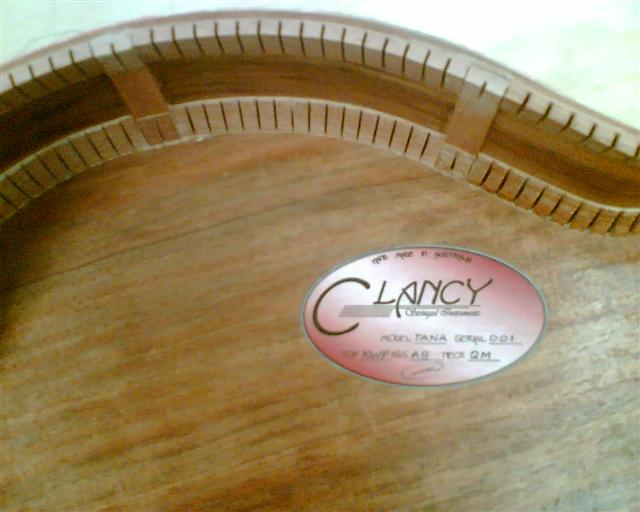
Glue on the top & voila - you have the box!
Now for the neck.
I didn't take many pics of this process for some reason (can't remember why)
It's a one-piece neck, cut to shape on a pissy little GMC bandsaw.
Truss rod slot cut with another pissy piece of GMC equipment (router).
First up, the dove tail join jigs for the neck & body
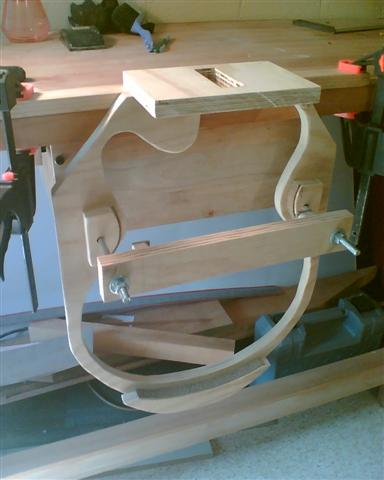
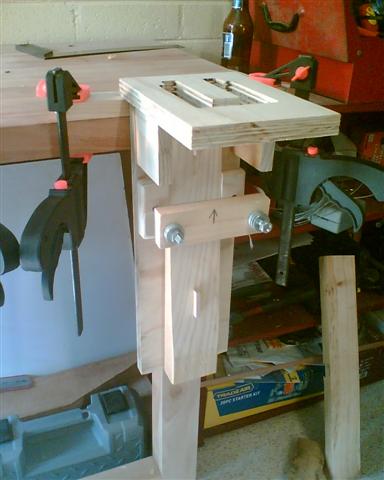
which gave the following results
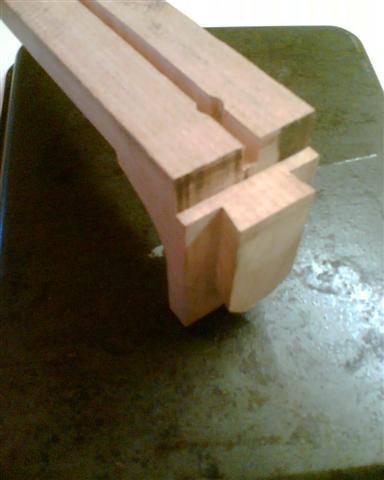
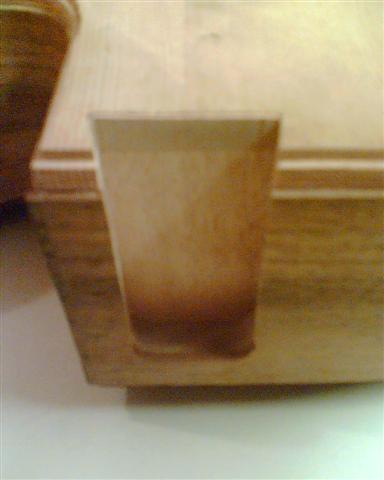
Home made single action truss rod with rubbery black tube cover
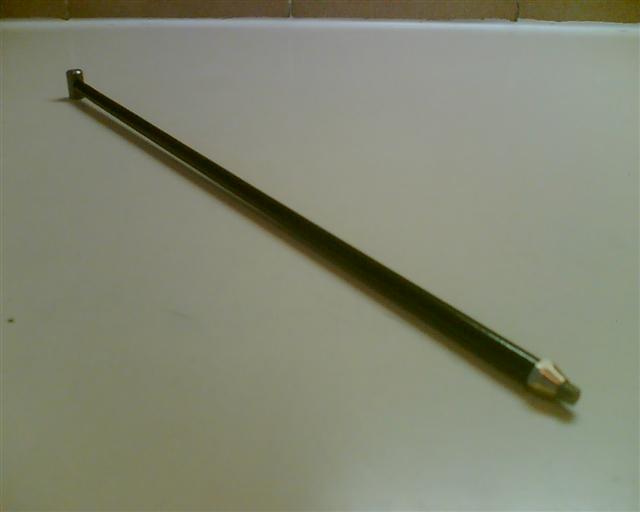
Insert into neck
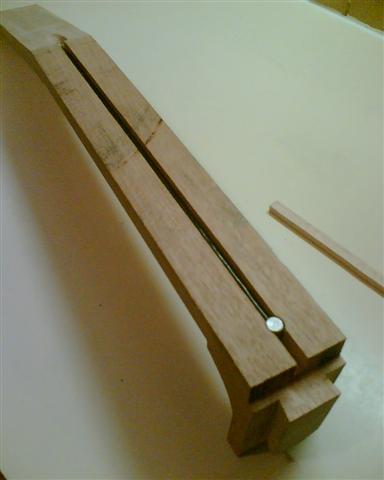
And cover
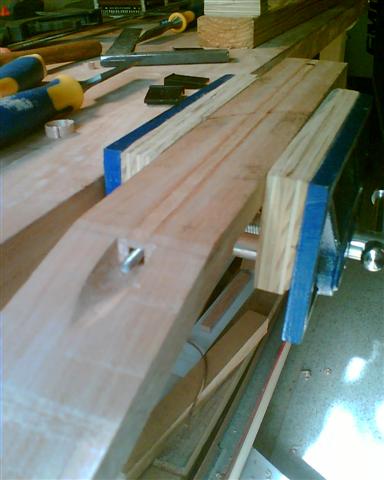
Add neck extension
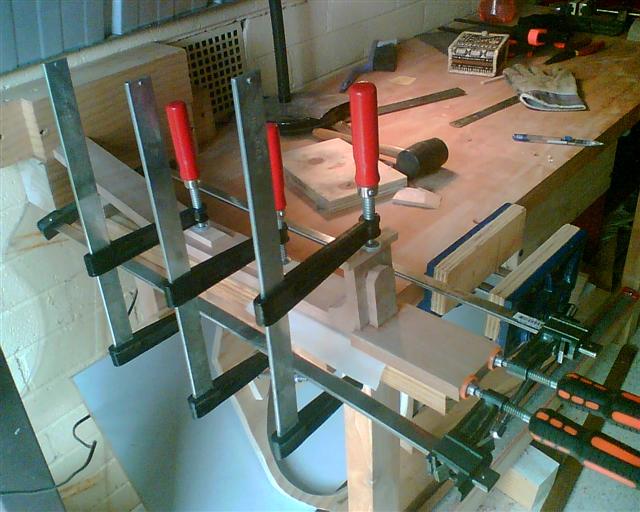
Slot fingerboard & shape fingerboard & glue to neck
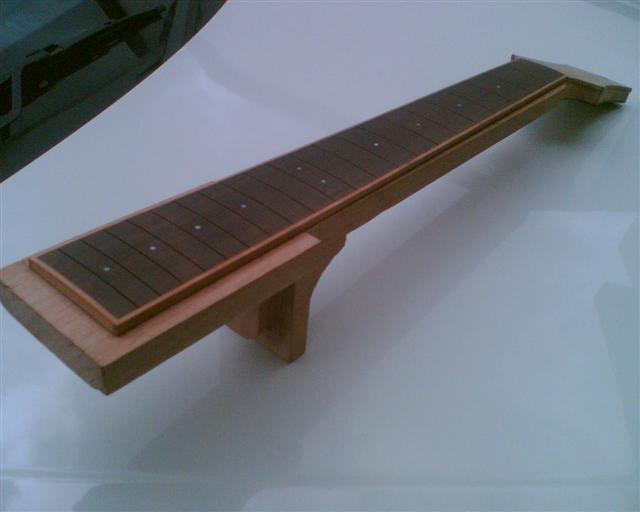
Add binding - it'll only take a minute or two
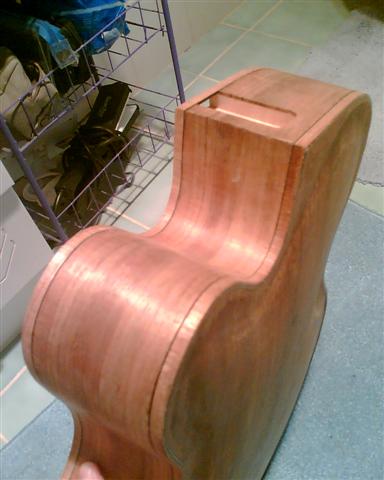
Trim everything up to fit & now you have something guitarish...
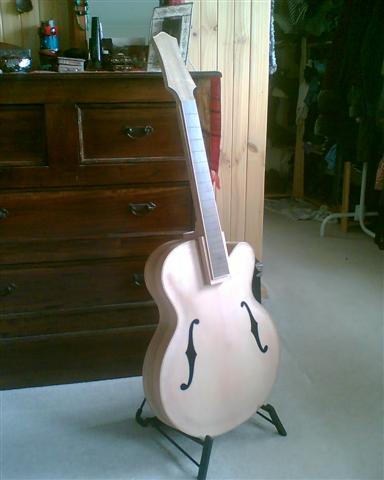
I didn't take many pics of this process for some reason (can't remember why)
It's a one-piece neck, cut to shape on a pissy little GMC bandsaw.
Truss rod slot cut with another pissy piece of GMC equipment (router).
First up, the dove tail join jigs for the neck & body
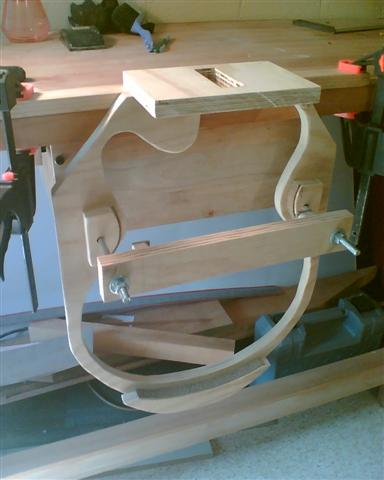
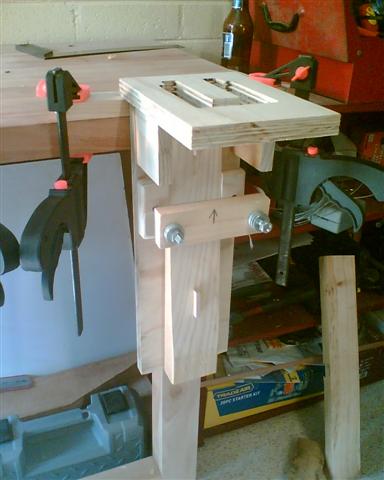
which gave the following results
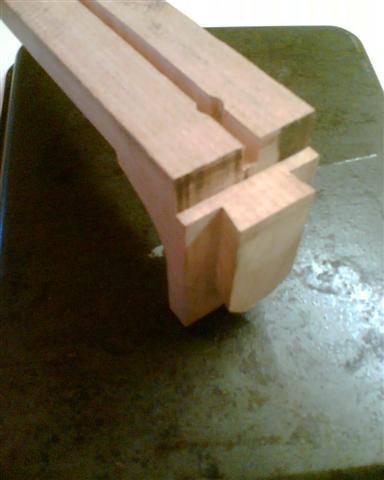
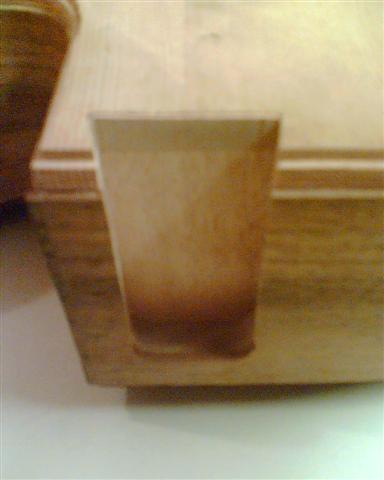
Home made single action truss rod with rubbery black tube cover
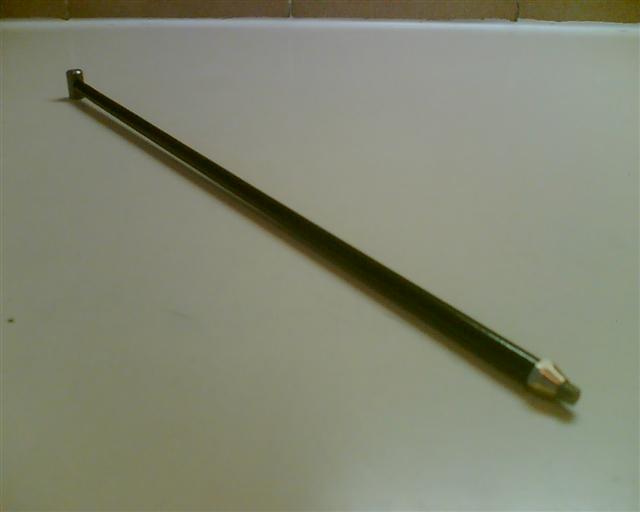
Insert into neck
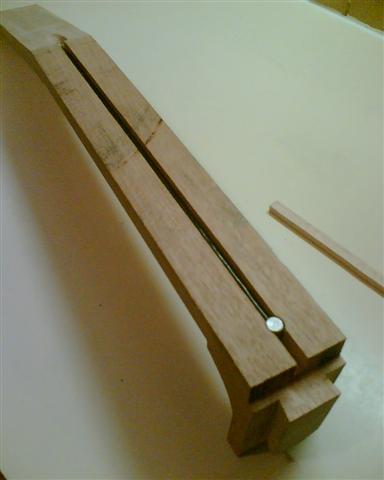
And cover
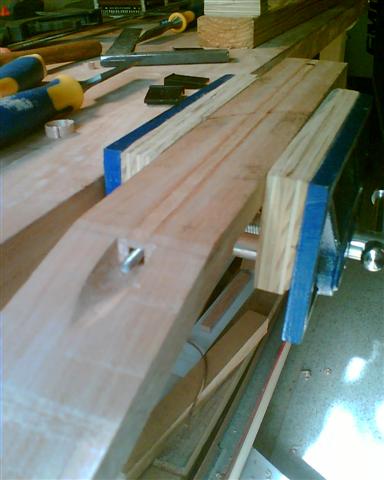
Add neck extension
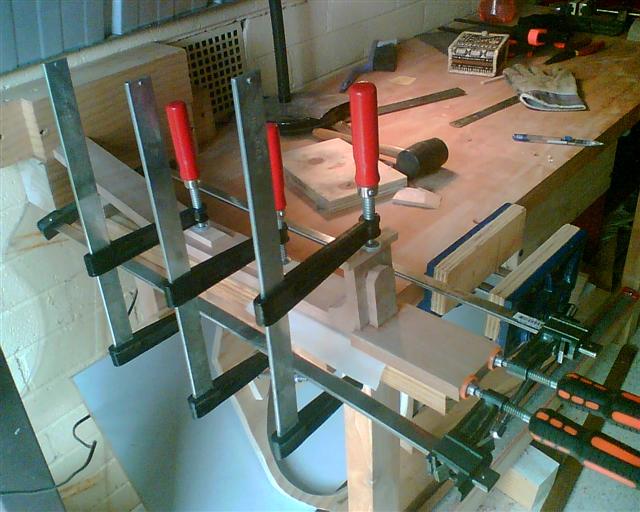
Slot fingerboard & shape fingerboard & glue to neck
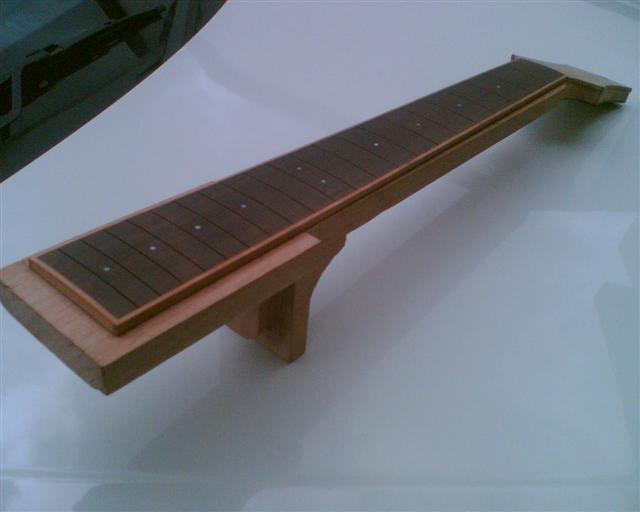
Add binding - it'll only take a minute or two

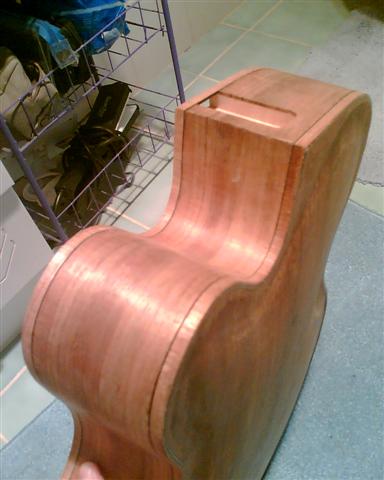
Trim everything up to fit & now you have something guitarish...
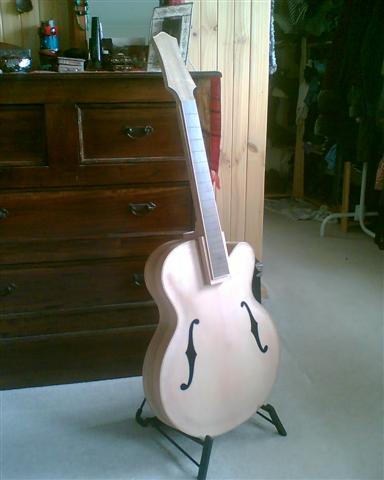
Clean up edges & sand, sand, sand.
Learn how to use a spray gun, close your eyes, point & squeeze.
Now sand that laquer.
Sand more.
Better just sand a bit more.
Now add all the little extras:
Tuners
Bridge
Tailpiece
Nut
Frets
Floating Fingerboard
Floating Kent Armstrong Pickup
AND IT"S DONE.
TOTAL BUILD TIME........ 2 YEARS!!!
To see results you can go to this old thread
viewtopic.php?t=1219
Hope this has encourage someone to try carving top & backs. I love it.
Learn how to use a spray gun, close your eyes, point & squeeze.
Now sand that laquer.
Sand more.
Better just sand a bit more.
Now add all the little extras:
Tuners
Bridge
Tailpiece
Nut
Frets
Floating Fingerboard
Floating Kent Armstrong Pickup
AND IT"S DONE.
TOTAL BUILD TIME........ 2 YEARS!!!
To see results you can go to this old thread
viewtopic.php?t=1219
Hope this has encourage someone to try carving top & backs. I love it.
So really just a piece of piss to make hey Criag? Don't know what all the fuss is about.
I've read Bob's book through several times, and tell myself to start one, but something else keeps coming up. It's in the gotta do pile though. Thanks for posting.
What did you do about tail piece and bridge? Did you make your own, or buy them?

I've read Bob's book through several times, and tell myself to start one, but something else keeps coming up. It's in the gotta do pile though. Thanks for posting.
What did you do about tail piece and bridge? Did you make your own, or buy them?
Nick,Nick O wrote:Hi String- Nice job with the shell! Do you make many? I used to hit the skins and lurrrrv wooden shells especially Piccolo's, the chrome shells just aint 'got it' as far as I'm concerned, the kit I had came with a chrome shell snare but that soon went and was replaced with a wooden shell. How did/do you cut the bearing edges, also I don't recognise the hardware, is it a generic brand or one of the known makers? Funny thing with drum hardware, it's the makers signature.
I haven't made any shells for a couple of years, just as I was redesigning molds, etc., nature intervened (the strory here http://www.recordingproject.com/bbs/vie ... hp?t=30325 ) and my garage/workshop became a storage area. A year ago, I re-entered the workforce, this has now allowed me to take on my "lutherie" interests and due to the products we're researching and now producing, future drum shells will not be made from timber but more about that later.
Re the drum hardware...........the snare strainer is from Trick Drums in the US, the tension lugs are "quick release" custom lugs from Todd Rathkamp (Rattrap Drums) also in the US. The bearing edges are done on a router table.
For anyone interested in drum building, there's heaps of info at either http://www.drumshed.org/forum/ (this was originally Ghostnote but changed name after a split within admin) or http://www.ghostnote.net/vbforum/ (this 2nd generation GN forum is quite active but seems to be home to a more redneck element

ChrisO

Music creates a kind of pleasure which human nature cannot do without.
It was after Craig bought his arch top around and let me play it, then showed me his setup that got me into it.
His guitar sounds great and really inspired me.
I also sat through all 9 1/2 hours of Bob B DVD to get me primed which is fantastic. Its so cool to see how these very experienced guys work. How they hold the plane, how they tape the f hole binding, All looks effortless.
Dom
His guitar sounds great and really inspired me.
I also sat through all 9 1/2 hours of Bob B DVD to get me primed which is fantastic. Its so cool to see how these very experienced guys work. How they hold the plane, how they tape the f hole binding, All looks effortless.
Dom
You can bomb the world to pieces,
but you can't bomb the world to peace!
but you can't bomb the world to peace!
- J.F. Custom
- Blackwood
- Posts: 779
- Joined: Fri May 01, 2009 9:13 pm
- Location: Brisbane
- Contact:
HOLY M'COW!!!Nick O wrote:One of Bob's creationsvandenboom wrote:It is interesting to read in Benedetto's book his view on all this. Stories of experienced builders using structural pine from their local Home Depot store and producing a great sounding archtop.
Worm infested top, goes to show it ain't necessarily the quality of the wood but how it's made.

I've seen some mishaps with a router but that is ridiculous. Note to all budding luthiers - Anyone with advanced Parkinson's disease should consider using templates...

Sorry in advance for any offense caused to any persons unfortunate enough to have this disability...

Is that like the modern art equivalent of a sound aperture? Perhaps why not to use a shotgun to create your soundhole? Anyways, they are some serious worm holes

Does however go to show that great wood does not equal a great guitar and vice versa. It's the builder and their ability to work, judge and compensate for the materials at hand that will ultimately make the guitar a great one or not so...
Jeremy.
The worms are very common in all the wood that is hauled in boom form up and down the B.C. coast. Drift wood all along the shore is just riddled with these holes.
When still in high school I worked afternoon and graveyard shift at the local saw, and pulp mill. One of the most disgusting jobs was to work on the slasher decks where wood that was unsuitable for lumber, was cut into blocks that would end up ground into long fibers that helped to make higher quality paper. Most of this wood was infested with Teredo worms.
I've never come across anything that smells worse than these things when they have been bisected by a very large saw blade. Even running over a dead wombat thats been peculating in the Aussie sun for 2 weeks, and splattering the undercarriage of your ute is a fresh summer breeze compared to these things.
Rookies that left their lunch boxes unattended would end up getting a Teredo worm sandwich courtesy of the old hands. Kind of put you off eating at work for several weeks afterwards.
When still in high school I worked afternoon and graveyard shift at the local saw, and pulp mill. One of the most disgusting jobs was to work on the slasher decks where wood that was unsuitable for lumber, was cut into blocks that would end up ground into long fibers that helped to make higher quality paper. Most of this wood was infested with Teredo worms.
I've never come across anything that smells worse than these things when they have been bisected by a very large saw blade. Even running over a dead wombat thats been peculating in the Aussie sun for 2 weeks, and splattering the undercarriage of your ute is a fresh summer breeze compared to these things.
Rookies that left their lunch boxes unattended would end up getting a Teredo worm sandwich courtesy of the old hands. Kind of put you off eating at work for several weeks afterwards.

- J.F. Custom
- Blackwood
- Posts: 779
- Joined: Fri May 01, 2009 9:13 pm
- Location: Brisbane
- Contact:
- rocket
- Blackwood
- Posts: 1210
- Joined: Thu Apr 30, 2009 8:43 pm
- Location: melbourne,, outer east
- Contact:
archtops
very nice craig, very nice indeed, obviously a benedetto instruction. they're a beautiful instrument aren't they. When i've got some more progress pics i'll stick'm on. Once again great pictorial, catch'ya.
- J.F. Custom
- Blackwood
- Posts: 779
- Joined: Fri May 01, 2009 9:13 pm
- Location: Brisbane
- Contact:
How...........Allen wrote:I've never come across anything that smells worse than these things when they have been bisected by a very large saw blade. Even running over a dead wombat thats been peculating in the Aussie sun for 2 weeks, and splattering the undercarriage of your ute is a fresh summer breeze compared to these things.
Rookies that left their lunch boxes unattended would end up getting a Teredo worm sandwich courtesy of the old hands. Kind of put you off eating at work for several weeks afterwards.
........
........
........
Pleasant.....?

Thanks once more Allen and so........ descriptive.
Remind me not to ask questions where I don't really want to know the answer ok? Mind you, just another reason to add to my book entitled 'Why I am Vegetarian" - Toredo worms; you can have 'em!

Jeremy.
Allen wrote: ................a dead wombat thats been peculating in the Aussie sun for 2 weeks.............
OMFG, that brings back some memories :spew ........and the smell hangs in the air for quite some distance around the corpse.

Music creates a kind of pleasure which human nature cannot do without.
Who is online
Users browsing this forum: No registered users and 290 guests