Here's my setup.
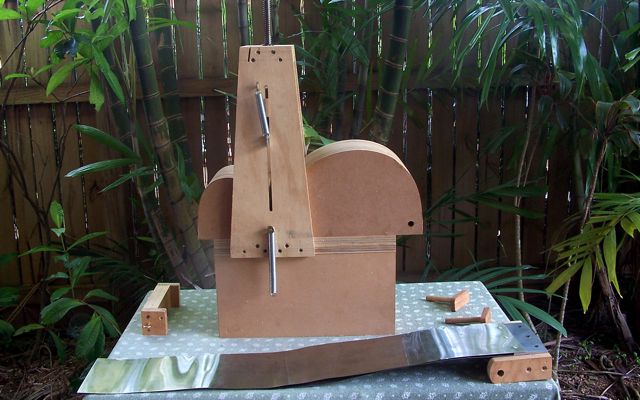
In the picture you can see a slightly modified Fox Style bender with my 000 bending form installed. The stainless slats that I use. The upper bout caul, and the wooden pegs that hold the lower bout in place.
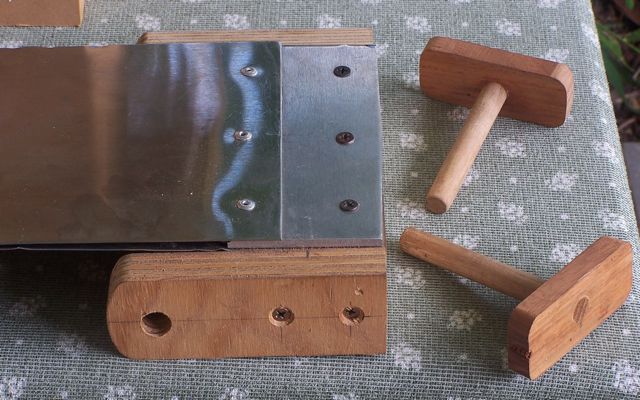
This is a close up of the butt end of the bending slats. I reference off of the butt, as it makes more sense to me to cut that square on the table saw, then cut the profile on my sides referenced from there. The sandwich of wood wrapped in craft paper and foil, along with heat blanket get slipped into the slats so that they end up tight and square against the spacer you can see holding the stainless slats apart. That spacer is positioned so that it's about 2 mm past the end of the bending form. That give me a little wiggle room with the thickness of the craft paper and alfoil that the sides are wrapped in.
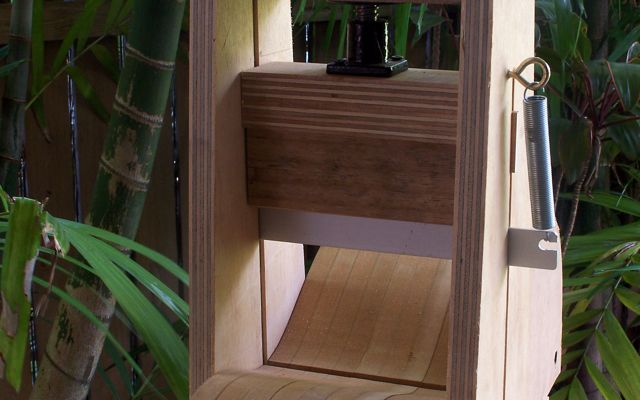
A detail shot of the tracks that are cut to guide the waist caul into the correct position. Veneer press screw to do the hard work.
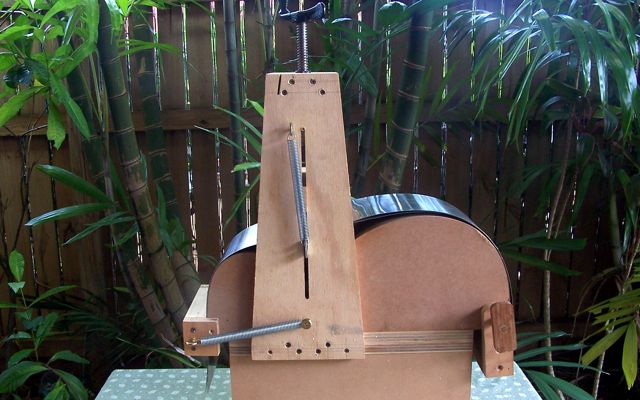
Heres the slats installed with the pegs to hold the butt in position, the upper bout caul in place. Now the only thing to do is screw down the waist caul.
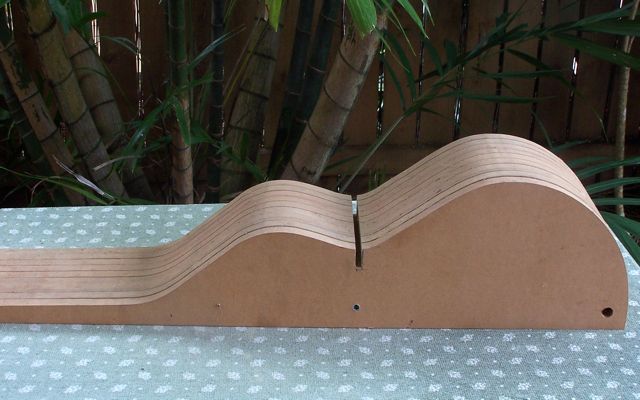
And finally a shot of my Weissenborn form. You can see a screw in insert at the lower waist position. There is one on each side of the form that the furniture screw with the spring that attaches to the upper bout caul hangs off of on the bender. This locates the bending form in the correct position, and stops things from moving around when your working.
From the time that the wood goes into the slats and is loaded into the bender, the entire process from there takes just 2 1/2 minutes. I turn on the heat blanket. Watch the digital themometer that I've slipped into the slats. 2 minutes later the temperature says 100 degrees C. I pull the lower bout down into position and push the wooden pegs in to hold it in place. Slide the upper bout caul around into position, then screw down the waist caul. All done in 30 seconds, and temperature reads around 150 - 160 degrees, so total is 2 1/2 minutes. I turn off the blanket and let everything cool down. I cycle the heat one more time to 150 degrees C. Let cool, then remove from bender.
Depending on the type of wood, their is some spring back, but all sides that I've done so far will slip into the mold. I like to get them in there without tension, so I usually give them a touch up on the bending iron. It's always been the waist that needs the extra attention. I suppose I could try and figure out how much I need to over bend this area but I'm too lazy to go to that much trouble. It's only a few minutes on the iron, and I still like doing that from time to time.