This was one of those…….
I present: Instrument #2 - irish bouzouki using Graham McDonalds book.
The aim of building the flat top irish bouzouki was to learn techniques that I hadn’t used building the carved archtop guitar, and practice & improve the common things like binding, fret work etc.
Here’s the (nearly) finished result.
B&S – Blackwood
Top – Bunya
Neck – Qld Maple
Binding – Qld Maple
Fretboard - Gidgee
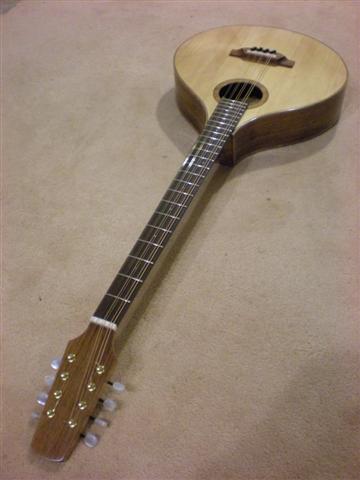
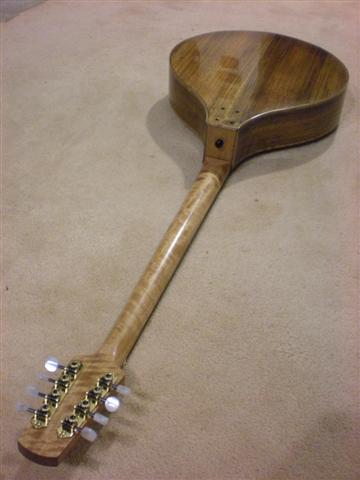
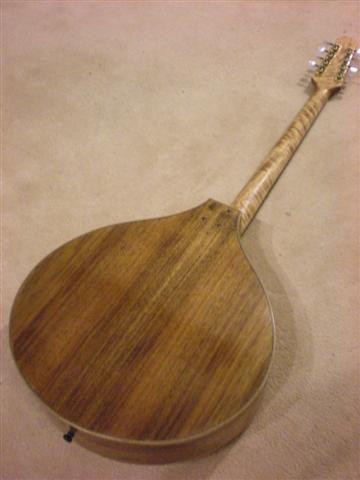
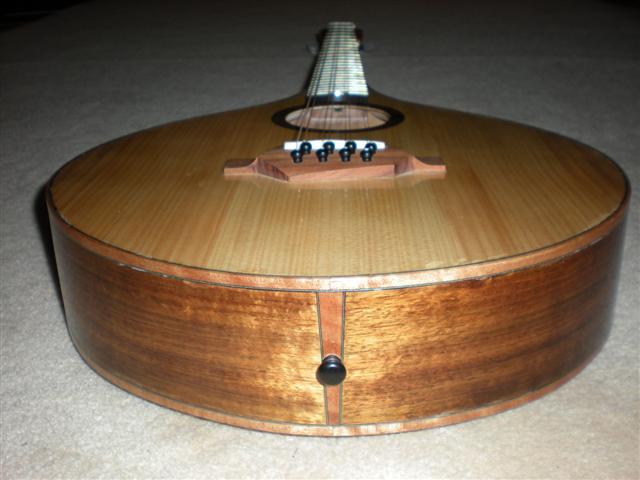
As I said, this project exceeded expectations – in the ‘new techniques required’ area!?!
The side bending went well. (I still hand bend on a hot pipe & enjoy it)
The sides were clamped in an adjustable workbench instead of a mold.
Good results joining the top & back & inlaying sound-hole rosette.
The soundboard bracing looked a bit of a challenge.
I made the radius dishes as per Graham’s instructions, pre sanded the curves & everything glued up nicely
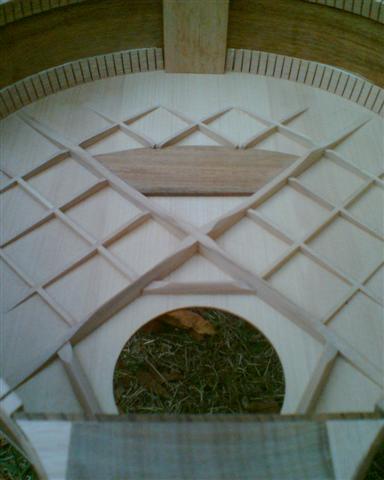
I had a few problems building the ‘hollow neck block’ for Graham’s removable neck design.
Got there in the end & put the body together. So far, so good.
Next came the routing for the binding. This was a disaster.
As I mentioned in a previous thread, the Bunya chipped & the Blackwood grains tore out.
Also, where the neck joins there is a section where there is virtually only side wood.
Now there is only binding. I’ll have to bog it all up sometime.
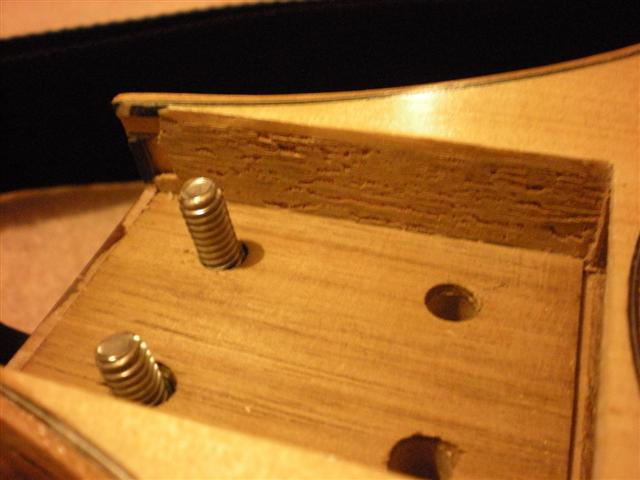
Unexpected New Technique #1:
I tried to tidy the binding channels up with a purfling knife & the brass cap compressed the wood outside the binding area. Sanded as much of that out as I dared.
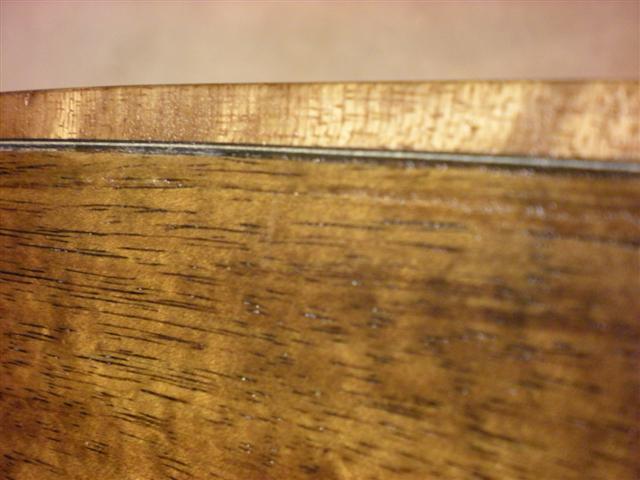
Unexpected New Technique #2:
Tried to invisibly fill the gaps with a mixture of epoxy & sanding dust.
This worked OK but the larger chips still show as different colour patches.
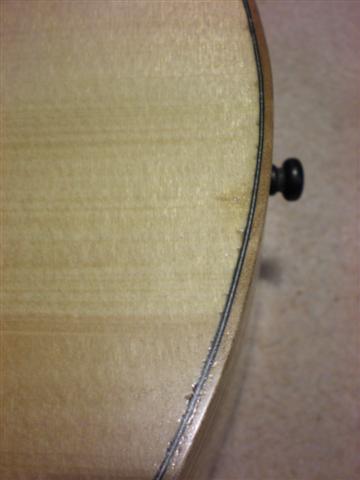
Unexpected New Technique #3:
I had sprayed the archtop guitar with nitro c at the local college but was unable to gain access this time, so I had to do it at home.
The kid’s grandparents had given them a bloody jumping castle a few years ago, which meant I had to go and buy a small (& cheap) compressor. At the time the best (cheap) thing for the job was a GMC oil less 6cfm thing.
The jumping castle has since been binned (I didn’t put the holes in it with this knife I’m holding, honest).
Anyway, I saw in Bunnings a HVLP gun for $65 and thought it might work.
So the bouzouki became the test piece. And it worked good enough for a backyard builder like me.
I didn’t spend much time trying to get it perfect. The blackwood really needed more pore filing & I didn’t put much effort into sanding flat.
But I honed the spraying skills on the bouzouki & did everything right on the archtop mandolin I’d made for a client (previous post as instrument #3)
The neck building went well, never having done the neck-head scarf joint before.
Now I know how, I’ll always use this method – even for archtop guitars instaed of the one piece (tradition can go blow)
Unexpected New Technique #4:
The neck is attached to the body via bolts that sit in the hollow neck block, aim upwards, & thread into inserts under the fingerboard.
Access to the bolts is from holes in the bouzouki back.
Not wanting to chip the back, I drill down until just the tip of the brad pint pocked out, turned the body over, & used the tiny point hole as my marker for drilling the other way.
Worked great for 3 of the 4 holes.
Oh, well. Now I get to practice my inlay techniques to tidy up the goof up.
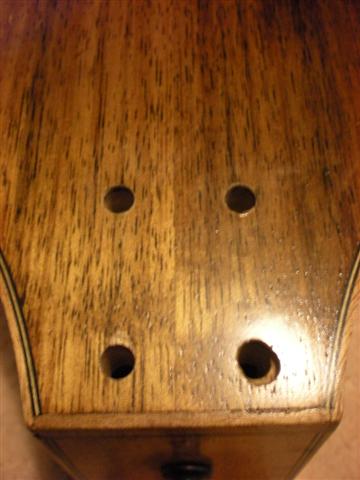
Now for the Bridge.
First time for a pin bridge.
Was making it the same as in the book when I had one of those whim’s and did something else.
Some like the shape, some don’t.
Had another whim (& dremel in hand) & did an ‘S’ type of intonation on the bone.
Now I’m having fun again.
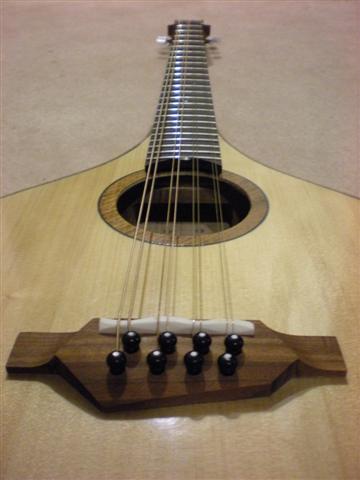
Time to put it all together!
Neck installation easy & solid but needs to be angled?
Check dimensions of bridge height – correct. OK, angle the neck then with an insert.
All good.
String up, tune, set up.
Sounds nice.
But.
What a horrible thing to play sitting down (it doesn’t have a waist).
Just thinking that I’d better get a strap for it when ‘CRACK’.
What was that.
Huh, bridge wings are separating from the soundboard.
De-tune & figure out why.
Unexpected New Technique #5:
Starting looking at the string tension.
Used the string weight values in graham’s book (had to guesstimate (my wife hates that word) some of them.
Found that I had around 83kg of tension using the current strings (12 16 24w 42w)
Calculated that I could reduce that to around 70kg using lighter strings (11 16 24w 36w).
Tightened up the strings again to re-create the gaps from the lifting.
Worked Titebond under the bridge.
Released the strings & clamped the bridge.
Left it for 3 days.
Clamps off & re-strung with lighter strings.
Sound’s good.
All good.
Then……Crack.
Again!
Now what?
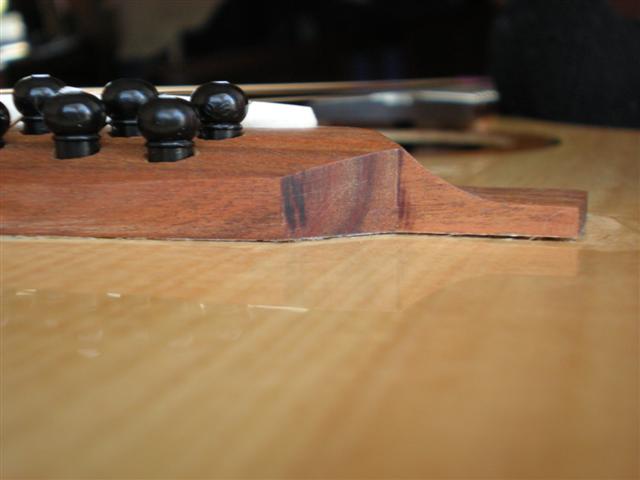
Unexpected New Technique #5???
So what do I do now.
Re-try again with Titebond?
Re-try with epoxy or super glue?
Try to remove the bridge, roughen up both gluing surfaces & glue back on?
Same as above but sand an arch into the bridge to match the soundboard arch?
Your wisdom & best guesses required.
In the mean time I’m leaving it strung up to see if
1/ The separation doesn’t increase
2/ The separation does increase (making it easier to remove the bridge if I choose)
3/ I can post a lovely picture of a catastrophic failure for you all to enjoy