Humidity and glueing
- Mark McLean
- Blackwood
- Posts: 1088
- Joined: Thu Apr 10, 2008 2:03 pm
- Location: Sydney
Humidity and glueing
I have some questions about the "rules" you all observe regarding work in times of high humidity. I have had a few weeks off work and time on my hands to get on with my next guitar - but constant 60-100% RH. You guys in the tropics are dealing with this all the time.
I think I understand the principle. Wood swells when it is humid; if you glue 2 pieces of swollen wood and they later dry out and shrink something might give. That is obviously a problem when the piece of timber in question is attached at 2 or more points - like a soundboard to the guitar sides. If it shrinks enough it will have to pull apart a joint or crack along the grain. But what about a join along one side only - like a brace to a top or back? If they expand and contract it won't necessarily stress the joint. Or am I missing a simple physical principle?
So, my question is this - what things are OK, and not OK, to glue up in high humidity?
And if I am making a guitar for myself or a local friend, and it is going to spend its life in the same humidity range, do I need to worry about it at all?
I think I understand the principle. Wood swells when it is humid; if you glue 2 pieces of swollen wood and they later dry out and shrink something might give. That is obviously a problem when the piece of timber in question is attached at 2 or more points - like a soundboard to the guitar sides. If it shrinks enough it will have to pull apart a joint or crack along the grain. But what about a join along one side only - like a brace to a top or back? If they expand and contract it won't necessarily stress the joint. Or am I missing a simple physical principle?
So, my question is this - what things are OK, and not OK, to glue up in high humidity?
And if I am making a guitar for myself or a local friend, and it is going to spend its life in the same humidity range, do I need to worry about it at all?
- DarwinStrings
- Blackwood
- Posts: 1877
- Joined: Thu Nov 13, 2008 10:27 pm
- Location: Darwin
Hi Mark
Have a read of this and it may help you make decisions about gluing.
http://ir.library.oregonstate.edu/dspac ... ng_ocr.pdf
Jim
Have a read of this and it may help you make decisions about gluing.
http://ir.library.oregonstate.edu/dspac ... ng_ocr.pdf
Jim
You can glue top and backs together on the seam, but glueing braces on at anything other than your desired working RH (somewhere between 40 - 50 %) is going to cause you all kinds of grief.
I've not had any trouble building the rims at varying RH, but once the rims are built, I do my best to get the braces glued, profiled and the box closed up as quick as I can. Everything stays in a small bedroom where I have my dehumidifier, and the RH stays in the 40 - 45 % range no matter how humid it gets outside.
To give you an idea right now Titebond will not dry out in my main work shop as it's just so bloody humid. A braced top taken from the dry room will turn itself inside out within 20 minutes.
When I want to work on a top or back, it comes out into the shop, where I work as efficiently as I can for 10 - 15 minutes, then the piece goes back to the "dry room". I then grab something else to work on and repeat this process until I get everything ready for the glue up of the box.
Closing the box takes place in the dry room, as humidity swings will make the top or back change dimension and force the sides out of square.
I've got to work like this, because the light is better in the shop, I'm allowed to make as much mess as I like without the wife threatening to kill me, and Le' Fridge is out there.
Once the box is closed, you're pretty well safe. Really wild swings in RH can effect fret boards, and necks, but the changes take place at a much slower rate that tops and back, owing to the size of the pieces.
I've not had any trouble building the rims at varying RH, but once the rims are built, I do my best to get the braces glued, profiled and the box closed up as quick as I can. Everything stays in a small bedroom where I have my dehumidifier, and the RH stays in the 40 - 45 % range no matter how humid it gets outside.
To give you an idea right now Titebond will not dry out in my main work shop as it's just so bloody humid. A braced top taken from the dry room will turn itself inside out within 20 minutes.
When I want to work on a top or back, it comes out into the shop, where I work as efficiently as I can for 10 - 15 minutes, then the piece goes back to the "dry room". I then grab something else to work on and repeat this process until I get everything ready for the glue up of the box.
Closing the box takes place in the dry room, as humidity swings will make the top or back change dimension and force the sides out of square.
I've got to work like this, because the light is better in the shop, I'm allowed to make as much mess as I like without the wife threatening to kill me, and Le' Fridge is out there.

Once the box is closed, you're pretty well safe. Really wild swings in RH can effect fret boards, and necks, but the changes take place at a much slower rate that tops and back, owing to the size of the pieces.
-
- Blackwood
- Posts: 115
- Joined: Tue Dec 09, 2008 1:15 pm
Allen, some very interesting observations. I have a similar situation to yours and can assemble critical joints and glue braces, etc, in a spare room in the house with a dehumidifier running.
What I'm still unsure of is just how quickly the various components like tops, backs, braces, necks and fretboards reacclimatise once I've finished the messy stuff in the workshop and I'm ready to put them all together inside. Obviously, larger parts like necks take longer than soundboards, but I still don't know to what degree. I've therefore taken a conservative approach (I think) and leave it until the next day to glue.
I began building guitars when I lived in Derby WA so I know full well the challenges your climate presents you with! Trying to build a first guitar in a sauna wouldn't have been much different.
What I'm still unsure of is just how quickly the various components like tops, backs, braces, necks and fretboards reacclimatise once I've finished the messy stuff in the workshop and I'm ready to put them all together inside. Obviously, larger parts like necks take longer than soundboards, but I still don't know to what degree. I've therefore taken a conservative approach (I think) and leave it until the next day to glue.
I began building guitars when I lived in Derby WA so I know full well the challenges your climate presents you with! Trying to build a first guitar in a sauna wouldn't have been much different.
It really defends on air circulation I've found. If I'm really in a hurry, I'll turn the ceiling fan on and this will really speed the acclimation up.
For a check, I've got my radius gauges for top and back. When I take the top and back out of the radius dish from having the braces glued on, I hold my radius template to the plate, and check to see how close it's held to the desired shape.
When I work on the plate I keep the radius template handy and constantly check it to gauge how the humidity is affecting it. Once it goes back into the dry room, it's a simple matter of using the same template to check the shape. When it's the same as it was coming from the dish originally, then it's equalized, and ready to go.
For a check, I've got my radius gauges for top and back. When I take the top and back out of the radius dish from having the braces glued on, I hold my radius template to the plate, and check to see how close it's held to the desired shape.
When I work on the plate I keep the radius template handy and constantly check it to gauge how the humidity is affecting it. Once it goes back into the dry room, it's a simple matter of using the same template to check the shape. When it's the same as it was coming from the dish originally, then it's equalized, and ready to go.
Pretty much the same deal here. I am near the coast so swings are not too bad. I have a small 3 x 2.4 mtr, insulated, lined and sealed room in the shed. The RH is controlled in that room using a self draining dehumidifier. The door to that room remains shut and the RH is kept at 40 - 50 % for about 2 weeks prior to a build.
All major wood removal task happen out in the shed proper, the components are then prep-ed, braces glued and calved in the RH controlled room and then the box is closed. Once the box is closed, the door to the room stays open with the DH switched off. The room may sound extravagant but was a conversion and an obvious thing to do.
The bonus is that I can take my time getting things done, which is a very good thing for someone like me
Cheers
Kim
All major wood removal task happen out in the shed proper, the components are then prep-ed, braces glued and calved in the RH controlled room and then the box is closed. Once the box is closed, the door to the room stays open with the DH switched off. The room may sound extravagant but was a conversion and an obvious thing to do.
The bonus is that I can take my time getting things done, which is a very good thing for someone like me

Cheers
Kim
- Mark McLean
- Blackwood
- Posts: 1088
- Joined: Thu Apr 10, 2008 2:03 pm
- Location: Sydney
Thanks for the advice, although it is a bit disheartening. Clearly this is an issue that I cannot ignore. I build in a 6x3 metre unlined shed and I doubt that I could maintain constant RH there. Bringing stuff into the house is not really an option. I work slowly, finding an hour or two once or twice a week - and sometimes going a couple of weeks without getting in there. I guess I am just going to need to be patient and do the critical building steps only when conditions are right. I have 2 hygrometers to measure RH (one digital, one "human hair hygrometer"), and there is always something else to do on the bad days! My workshop is not currently equipped with 'Le fridge'. I might need to do something about that.
Mark
Mark
Mark,
Don't get too disheartened, you can always make a vented RH controlled cabinet to store components in-between sessions. Essentially it is a large wooden box (think good quality old wardrobe sealed with duct tape). You run a 45w incandescent light bulb in the very bottom where you have the air intake ( in where the draws were before you pulled them out and made a ply flap for an access door) and bore a 2" hole just down from the top in the back panel for the exhaust.
You store your work somewhere in the middle. Moist air comes in at the base and is dried by the heat of the bulb. It rises up past your work and back out to the atmosphere, simple but effective.
Cheers
Kim
Don't get too disheartened, you can always make a vented RH controlled cabinet to store components in-between sessions. Essentially it is a large wooden box (think good quality old wardrobe sealed with duct tape). You run a 45w incandescent light bulb in the very bottom where you have the air intake ( in where the draws were before you pulled them out and made a ply flap for an access door) and bore a 2" hole just down from the top in the back panel for the exhaust.
You store your work somewhere in the middle. Moist air comes in at the base and is dried by the heat of the bulb. It rises up past your work and back out to the atmosphere, simple but effective.
Cheers
Kim
- Mark McLean
- Blackwood
- Posts: 1088
- Joined: Thu Apr 10, 2008 2:03 pm
- Location: Sydney
Kim
That is a great suggestion! I have enough space for it. It is council cleanup week around here this week and there is a lot of old furniture sitting on the kerbside waiting to be put to good use. I always scrounge for tools and timber so I will keep an eye out for something suitable. Failing that I'll pay a visit to Vinnies or some garage sales.
thanks
Mark
That is a great suggestion! I have enough space for it. It is council cleanup week around here this week and there is a lot of old furniture sitting on the kerbside waiting to be put to good use. I always scrounge for tools and timber so I will keep an eye out for something suitable. Failing that I'll pay a visit to Vinnies or some garage sales.
thanks
Mark
This is just the thread I was looking for ... I've put off my parlour project.
( I got this far and then realised I wasn't going to get a dry day for many months ... )
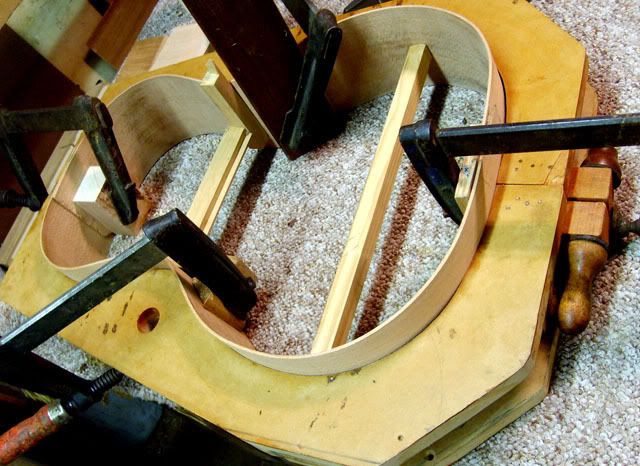
... ( not to mention spraying lacquer ) in sweaty disgust and have gone back to routing out slabs and necks for electrics and doing repairs and like everybody else it seems, making jigs ! It seems a safer use of my time ( in my first Brisbane summer for 17 years )
I have heard about 'cooking' parts before assembly but couldn't think of a practical way to achieve this in a typical 'under the house' latticework workshop under a Queenslander. I know it's not a longeterm solution, but like Mark I suppose I just need a short term fix for this first acoustic.
Allen I love the way your guitar becomes your RH meter :
( I got this far and then realised I wasn't going to get a dry day for many months ... )
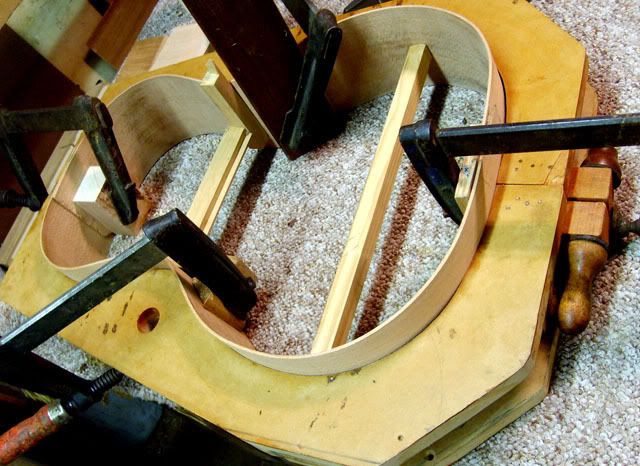
... ( not to mention spraying lacquer ) in sweaty disgust and have gone back to routing out slabs and necks for electrics and doing repairs and like everybody else it seems, making jigs ! It seems a safer use of my time ( in my first Brisbane summer for 17 years )
I have heard about 'cooking' parts before assembly but couldn't think of a practical way to achieve this in a typical 'under the house' latticework workshop under a Queenslander. I know it's not a longeterm solution, but like Mark I suppose I just need a short term fix for this first acoustic.
Allen I love the way your guitar becomes your RH meter :
Cheers APWhen it's the same as it was coming from the dish originally, then it's equalized, and ready to go.
i got a hot rod ford and a two dollar bill, and i know a place right over the hill ...
www.flickr.com/photos/harvesterworks
www.flickr.com/photos/harvesterworks
- graham mcdonald
- Blackwood
- Posts: 472
- Joined: Thu Oct 25, 2007 11:57 am
- Location: Canberra
- Contact:
A somewhat more expensive, but more reliable solution is to look around for a de-humidifier. They are small unit maybe 600mm tall 400mm wide x 300mm deep with something like a refrigerator coil and a bucket to catch the water that it condenses out of the air by chilling it on the coil. Some even have a knob to set the required humidity and instead of the bucket they can drain outside through a hose. New around $4-500 I think and can sometimes be found second hand. One will keep a whole room dehumidified if kept fairly well sealed, but a more economical way is to make a cupboard in the corner of a room twice the size of a go-bar deck. That will give you enough storage for current projects - and allow you to do all the vital gluing jobs in a controlled environment. I built one in Sydney years ago when we lived there and it made life so much easier. About 1200 x 1800 with a simple frame out of 4x2 covered with sisalation and some cheap panelling with a door that was reasonably airtight.
There will a few hundred dollars initial expense, but I would see something like that as essential as bandsaw for anyone who lives near the coast and wants to make expensive sawdust in any semi-serious fashion
Sitting here in Canberra where it currently 34° and 27%
graham
There will a few hundred dollars initial expense, but I would see something like that as essential as bandsaw for anyone who lives near the coast and wants to make expensive sawdust in any semi-serious fashion
Sitting here in Canberra where it currently 34° and 27%
graham
Graham McDonald
http://www.mcdonaldstrings.com
http://www.mcdonaldstrings.com
Thanks Graham,
I'll definitely be going that route when I return to my home and my 'real' workshop in Melbourne later this year. ( in time for a Melb winter
)
I'm not balking at the expense in the long term ( and I'm not about to give this game up any time soon
) The bandsaw comparison makes perfect sense to me.
I guess I have gotten away with a lot in Melbourne over the years and foolishly thought I'd get an acoustic put together this Christmas if I picked my days to work ( It doesn't work that way in Queensland ... )
Cheers, Anthony ( AP )
I'll definitely be going that route when I return to my home and my 'real' workshop in Melbourne later this year. ( in time for a Melb winter

I'm not balking at the expense in the long term ( and I'm not about to give this game up any time soon

I guess I have gotten away with a lot in Melbourne over the years and foolishly thought I'd get an acoustic put together this Christmas if I picked my days to work ( It doesn't work that way in Queensland ... )
Cheers, Anthony ( AP )
i got a hot rod ford and a two dollar bill, and i know a place right over the hill ...
www.flickr.com/photos/harvesterworks
www.flickr.com/photos/harvesterworks
I think my best lutherie investment last year was to build a 2x3m sealed and insulated room in my workshop with a dehumdifier running 24/7. I keep all my tonewoods and partially completed builds in there and also have a bench with a go-bar deck. It gets stinking hot on sunny days, but most of the time in Brisbane if the sun's out humidity will be around 50%, so I only need to venture into the controlled room when I need to get something.
I actually find I get a lot more done when there's miserable weather because there's no heat or nice sunny days to distract me.
I actually find I get a lot more done when there's miserable weather because there's no heat or nice sunny days to distract me.
I got a Delonghi dehumidifier from "The Good Guys" for $320. It' doesn't self drain, so you have to empty the bucket every day or so, but I like to go in every day and check on things anyway, so not that big of an inconvenience.
It is definitely a worth while investment if you're hoping to pursue building all year round. An as Richard said. It really does warm the room up. But it sure does give you a nice long open time on hot hide glue.
My dry room is regularly 38+++, but with the low humidity, it's actually much more comfortable to work in there than out in the shop. I guess I'm getting aclimatized to the tropical heat.
It is definitely a worth while investment if you're hoping to pursue building all year round. An as Richard said. It really does warm the room up. But it sure does give you a nice long open time on hot hide glue.

My dry room is regularly 38+++, but with the low humidity, it's actually much more comfortable to work in there than out in the shop. I guess I'm getting aclimatized to the tropical heat.

-
- Blackwood
- Posts: 115
- Joined: Tue Dec 09, 2008 1:15 pm
Just as inconvenient but not often mentioned as an issue are periods of low humidity.
It's pretty humid here in Perth at present, but there was a stretch a few weeks ago when the ambient RH was below 30% and I had to rely on the evaporative air-conditioning in the house in tandem with my dehumidifier to achieve a humidity level suitable for glueing. Depending on your circumstances, I can imagine that's not always available as an option.
I've tried a small mist-type vaporiser - the kind you run when your kids are suffering from a cold or croop - but found that the mist settled around the unit and wet everything.
Have any of you found a better alternative?
It's pretty humid here in Perth at present, but there was a stretch a few weeks ago when the ambient RH was below 30% and I had to rely on the evaporative air-conditioning in the house in tandem with my dehumidifier to achieve a humidity level suitable for glueing. Depending on your circumstances, I can imagine that's not always available as an option.
I've tried a small mist-type vaporiser - the kind you run when your kids are suffering from a cold or croop - but found that the mist settled around the unit and wet everything.
Have any of you found a better alternative?
Pete,
If the work area is small enough, 3 x 2.4 Mtr for instance, you will find that just breathing in the room without the DH running will bump things up very quickly.
Just a point on all this, we do not want to start getting too anal here, Torres never had a Delonghi. I feel that what we need more so than high, low, or medium RH, is 'stable' RH. The truth is that anywhere between 40% and 55% RH should be fine for most areas. Wood does move over that 15% buffer but surely this must be within serviceable tolerances or there would be no vintage guitars.
If I where building in the tropics and knew most of my instruments would be spending their time north of Capricorn, I would be concerned about gluing up with the RH at the lower end of that scale. All that expansion once exposed to the elements, while not near as catastrophic as shrinkage, must surely have an adverse effect on tone and change completely any efforts at voicing one had invested in the assembly room.
Like wise, one would not want to glue up at 55% when the ambient in your local area runs at 20%. I think to be safe we need to try and build within a 15% buffer of the median RH expected for our local area and that is the best we can do. Trying to shoot for a rock solid 46.2 is just an unnecessary impracticality we do not need to be dealing with.
(Mr one acoustic guitar under his belt
)
Kim
If the work area is small enough, 3 x 2.4 Mtr for instance, you will find that just breathing in the room without the DH running will bump things up very quickly.
Just a point on all this, we do not want to start getting too anal here, Torres never had a Delonghi. I feel that what we need more so than high, low, or medium RH, is 'stable' RH. The truth is that anywhere between 40% and 55% RH should be fine for most areas. Wood does move over that 15% buffer but surely this must be within serviceable tolerances or there would be no vintage guitars.
If I where building in the tropics and knew most of my instruments would be spending their time north of Capricorn, I would be concerned about gluing up with the RH at the lower end of that scale. All that expansion once exposed to the elements, while not near as catastrophic as shrinkage, must surely have an adverse effect on tone and change completely any efforts at voicing one had invested in the assembly room.
Like wise, one would not want to glue up at 55% when the ambient in your local area runs at 20%. I think to be safe we need to try and build within a 15% buffer of the median RH expected for our local area and that is the best we can do. Trying to shoot for a rock solid 46.2 is just an unnecessary impracticality we do not need to be dealing with.
(Mr one acoustic guitar under his belt

Kim
-
- Blackwood
- Posts: 115
- Joined: Tue Dec 09, 2008 1:15 pm
Kim, having turned worrying into an art form long ago, I reserve the right to "get anal" if I see fit.we do not want to start getting too anal here

I think you're probably right, so even when you're all fired up and in "luthier" mode, an ambient RH of 20% should stop you in your tracks.anywhere between 40% and 55% RH should be fine for most areas
With a dehumidifier and the luxury of evaporative air-conditioning, you can successfully manipulate your environment to suit, but as it's most often ducted and affects the entire household, those occasional dry, cold days are a particular problem. Management gets upset when the aircon fires up and she has to don the ski suit just so you can finish glueing those all-important top braces.
I was talking to a guitar-builder friend from my Derby days today and laughing about successfully completing my first guitar there having never heard of a hygrometer or a dehumidifier. It was too long ago to remember, but I can only guess that the critical glueing jobs took place in the dry season - blind luck indeed.
- ozziebluesman
- Blackwood
- Posts: 1529
- Joined: Wed Oct 10, 2007 9:12 am
- Location: Townsville
- Contact:
I've built four stringed acoustic instruments here in the tropics. I have a sealed box made from chipboard about the size of a small wardrobe. I use gel pack moisture absorbers in the box to maintain the box environment at 50% RH. These packs go in the oven when they change colour to be dried out ready for use again. The wood is stored in there prior to a build and the guitar mould and all go back in the box until the box is closed. I never glue over 55% RH but sometimes turn on the aircon that will control the environment in the whole house so I can glue up. On both weissenborns I had all the parts built ready to take advantage of April through to Oct when it is beautiful weather here and very little high humidity issues. At the moment I am preparing some concert ukulele's and two parlor size guitars ready to glue up and assemble in the better conditions through the dry season.
I plan to start building in my workshop area under the house roof line soon and I have planned a special area like Kim suggested with the vented controlled cabinet with light bulb as a permanent fixture in the workshop.
The last month it has been 75% RH and the past week 90% RH and bloody wet. Not so good for guitar building!
Just be like a good boy scout and "Be Prepared".
Cheers
Alan
Cheers
Alan
I plan to start building in my workshop area under the house roof line soon and I have planned a special area like Kim suggested with the vented controlled cabinet with light bulb as a permanent fixture in the workshop.
The last month it has been 75% RH and the past week 90% RH and bloody wet. Not so good for guitar building!
Just be like a good boy scout and "Be Prepared".

Cheers
Alan
Cheers
Alan
- Mark McLean
- Blackwood
- Posts: 1088
- Joined: Thu Apr 10, 2008 2:03 pm
- Location: Sydney
Thanks for all of the information. This has been a really useful thread and I am disheartened no longer. I am now going to find or build a cupboard big enough to hold my go-bar deck and use it as my "dry store". I'll adopt the lightbulb and/or moisture absorber technique and keep everything in good shape. Should be a fun project to put it together.
mm
mm
If you are wanting to get some Silica Gel beads at a reasonable cost, I got mine from ProSciTech. Good price and fast service.
If you've never seen them they look like little plastic beads. They are a bright indigo blue when they are dry, but turn pink when they become saturated with moisture. To revive them, you just warm them up to about 100 C to drive off the water. The color returns to blue and they are ready to use again. You can do this indefinitely.
I fill an old sock with them and keep one in each guitar case. To revive I spread the beads out on a baking sheet and put in the oven on low.
If you've never seen them they look like little plastic beads. They are a bright indigo blue when they are dry, but turn pink when they become saturated with moisture. To revive them, you just warm them up to about 100 C to drive off the water. The color returns to blue and they are ready to use again. You can do this indefinitely.
I fill an old sock with them and keep one in each guitar case. To revive I spread the beads out on a baking sheet and put in the oven on low.
- DarwinStrings
- Blackwood
- Posts: 1877
- Joined: Thu Nov 13, 2008 10:27 pm
- Location: Darwin
Well said Kim. I work at much higher than the "45s" that you southern mob work at, if I worked at 45 nothing would last through its first wet season.Kim wrote:
Like wise, one would not want to glue up at 55% when the ambient in your local area runs at 20%. I think to be safe we need to try and build within a 15% buffer of the median RH expected for our local area and that is the best we can do. Trying to shoot for a rock solid 46.2 is just an unnecessary impracticality we do not need to be dealing with.
Having said that I don't think my instruments would fair well in a cold dry place at all. The same goes for the opposite, instruments from "down south" fall apart up here. Makes for plenty of repair work but the looks on peoples faces when there new dream guitar (Australia made, not cheap) has lost a bridge or struts

Jim
-
- Blackwood
- Posts: 115
- Joined: Tue Dec 09, 2008 1:15 pm
After a disaster with a cracked top years ago, I rang the weather bureau and established that Perth's annual average humidity is 55%. Based on that advice, I built at 55% for some time after that with no problem, but currently aim for 45-50%.
What 's evident, however, is that seasonal variations make your mean humidity value pretty meaningless - a rough guide at best. In Perth, wet winter days can see us with RH as high as 90+%, while a hot dry spell can have it plummet to who knows what - I know it's been as low as 20% in my workshop this summer. Even over the course of a single day it can fluctuate a lot, falling in the afternoon when the temperature rises.
Granted, anyone who values their instruments isn't going to store them in the back shed, but it does highlight the fact that they are going to have to survive wide variations in humidity throughout their lifetime whether they live in the tropics or not.
I haven't gone down this route myself as I don't own instruments of any value, but storing guitars in a case with something like one of the Planet Waves units is probably the safest way to go. I'd certainly be recommending that - or maybe even including one - should I ever work up the nerve to sell my guitars.
What 's evident, however, is that seasonal variations make your mean humidity value pretty meaningless - a rough guide at best. In Perth, wet winter days can see us with RH as high as 90+%, while a hot dry spell can have it plummet to who knows what - I know it's been as low as 20% in my workshop this summer. Even over the course of a single day it can fluctuate a lot, falling in the afternoon when the temperature rises.
Granted, anyone who values their instruments isn't going to store them in the back shed, but it does highlight the fact that they are going to have to survive wide variations in humidity throughout their lifetime whether they live in the tropics or not.
I haven't gone down this route myself as I don't own instruments of any value, but storing guitars in a case with something like one of the Planet Waves units is probably the safest way to go. I'd certainly be recommending that - or maybe even including one - should I ever work up the nerve to sell my guitars.
Who is online
Users browsing this forum: Google and 304 guests