John,
The ICUT beam would no doubt weigh a 'little' more than the Durian brace originally fitted to the guitar however its of a similar dimension so there would not be that much in it. At the end of the day this brace not only replaces a standard UTB on a traditionally braced guitar, but also a more substantial neck block, and a neck heel as well, so I don't feel that weight is really a factor here.
One thing I will add is that at 3/4" or 19mm, this guitar had a ridiculously thick headstock. I did shave a little over a 1/16th from the back to thin it out a little and clean it up but could not take much more because to do so would have exposed too much of the capstans on the machines. Couple that with the fact that the machines themselves are quite heavy as they are solid steel, this thing was really over balanced toward the neck so the addition of some weight in the body, especially at the tail block was most welcome.
We move on...
This was all going along swimmingly but before I could fix the ICUT beam permanently into place, I had to know that I had the angle at the base of the neck block extension 'fairly' close to where it need to be. This meant that the now braced top, (minus the thin spruce transverse plate which is shown in the above images but was actually fitted last) had to be let into the sides. This would allow me to clamp the top in place and run a straight-edge along the neck surface to see where it sat in relation to the bridge position and then adjust accordingly.
This done it was time to get serious about the set up. I had already trimmed down the height of the veneers fitted to the side of the neck tenon so they could easily slide 'under' the lower surface of the top with a good bit of clearance. Now the ready fretted fretboard had to be glued onto the neck so that I could work out the fit between the upper surface of the top and the underside of the fretboard, any gaps here would look pretty shoddy and give the game away.
Fitting a fretboard to a neck blank is normally a pretty straight forward affair, but remember, the neck shaft on the pig is already shaped as too is the fretboard so there is no room for error. The way I approach this is to make a template of the FB. I do this by simply tracing around the fretboard on to some thin ply, and then carefully cutting out the ply to the line, and then sanding just past the line so I have an exact replica and the neck face and FB face is marked.
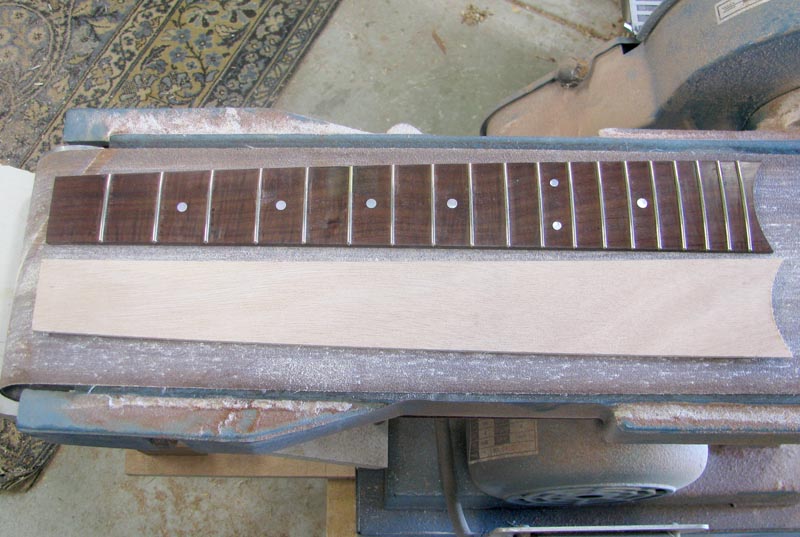
The replica is then fitted to the neck with the neck side down so it is exactly where it would need to be if it where the real FB, in this case with the nut end to a line representing the back of the nut, and the 13th fret position lining up with a corresponding mark on the neck blank. Once happy with the alignment, two shallow holes are drilled through the template and into the fretboard surface of the neck. The template is then carefully lifted from the neck surface and the FB side is then fitted to the fretboard and two more very shallow holes are drilled using the holes in the template as a guide. Dowels or pins which match the diameter of the holes are inserted into the neck, non water based glue is applied to avoid creating movement in the wood, the locator pins are aligned with their respective holes, and the joint is clamped.
With the fretboard now done the only other thing needed to finit the neck angle is a bridge. Once again I used Western Mayall for this component and did not venture too far from a standard Martin looking belly bridge so I could keep that traditional sort of look.
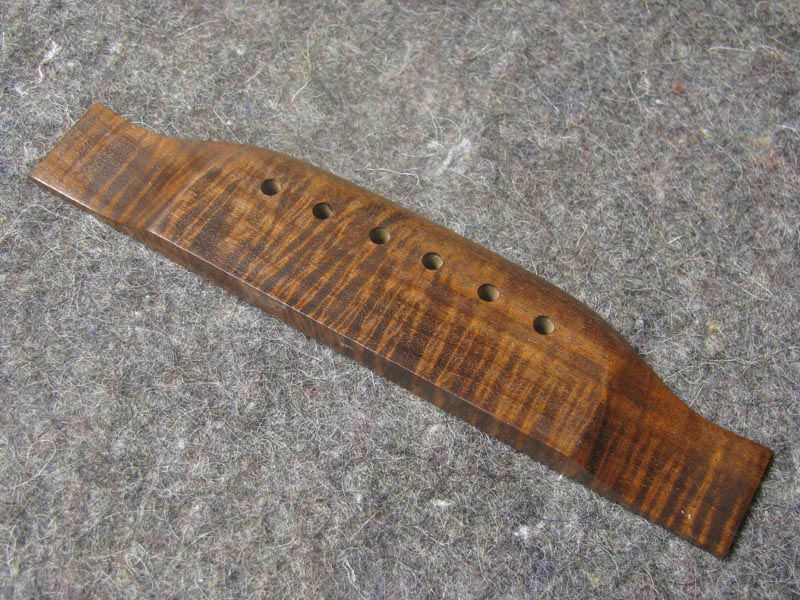
Once I had the bridge shaped and looking about right, it was then a matter of putting a radius on the bottom to match the guitar's top. The way I do this is simple. I hog off the worst of the wood with the belt sander being careful not to go too far, and then use a 25' dome sanding board to finish the job. I make the sanding dome out of MDF and shape it in the 25' radius sanding dish. I also shape the inside gluing caul for fitting the bridge using the same method. These dishes and a gobar deck are the roo's shoes and no guitar building workshop should be without them IMO.
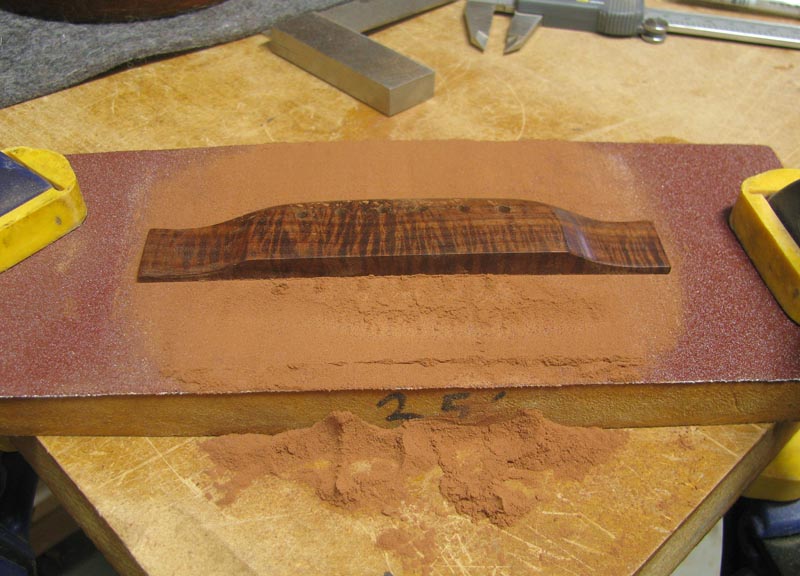
More soon...