Ken Parker Guitars
- matthew
- Blackwood
- Posts: 1193
- Joined: Mon Oct 08, 2007 1:16 pm
- Location: Sydney, Inner West
- Contact:
Re: Ken Parker Guitars
I don't think the tenon and neck is one piece. On all the pics you can see a sort of gasket or joint between them. Also the neck veneer - if it is that - is laid up impossibly neatly around such at 90degree joint. I think it's bolted on somehow. I think the tenon, and the mortise it slides in, are CF, the block being built up around a preformed CF socket.
Just speculatin', of course.
Just speculatin', of course.
Re: Ken Parker Guitars
In the image immediately above with the gold block, I see what you mean about the gasket at the neck and neck block Mathew but that could just be the way that the gold leaf is laid up. Downloaded this Image, the first link from Allen's post and then magnify. This looks like it 'may' be one peice and is the image I was referring to when I mentioned the feathering in.

Of course there is no reason why this part of the construction could not have been tackled in a number of ways and perhaps what we are seeing is MK1 and Mk2?
Cheers
Kim
Of course there is no reason why this part of the construction could not have been tackled in a number of ways and perhaps what we are seeing is MK1 and Mk2?
Cheers
Kim
Re: Ken Parker Guitars
If it helps, modern gliders are made of carbon fibre, and the wing spars for a 15m glider will be very little thicker than the block illustrated. They have to take at least 6 gravities in normal flight (say, 1.8 tonnes across the 15m span), and probably won't fail below 8 or 10 gravities.
If aerospace construction methods have been used, that block is distinctly over-engineered!
If aerospace construction methods have been used, that block is distinctly over-engineered!
Chris Reed
Re: Ken Parker Guitars
What I take from some of the articles I've read where Ken discusses his design is that the neck / riser assembly is made from Douglas Fir then layered with CF and a show veneer. The riser might be separate to start with (and probably is) but the laminations of CF and veneer make for a very strong joint.
The CF running from the neck and down the riser would account for that slight fillet that can be seen in those photos.
The CF running from the neck and down the riser would account for that slight fillet that can be seen in those photos.
- rocket
- Blackwood
- Posts: 1210
- Joined: Thu Apr 30, 2009 8:43 pm
- Location: melbourne,, outer east
- Contact:
Re: Ken Parker Guitars
If you look closely i think you'll see a winged Keel, i think that's the secret!




Like I said before the crash, " Hit the bloody thing, it won't hit ya back
www.octiganguitars.com
www.octiganguitars.com
Re: Ken Parker Guitars
xxxx
Last edited by Puff on Sun Nov 28, 2010 2:27 pm, edited 2 times in total.
- DarwinStrings
- Blackwood
- Posts: 1873
- Joined: Thu Nov 13, 2008 10:27 pm
- Location: Darwin
Re: Ken Parker Guitars
Does anybody know if Ken Parker has a second job as a mystery novelist?
Jim
Botanical names rock!
Jim
Botanical names rock!
Life is good when you are amongst the wood.
Jim Schofield
Jim Schofield
- J.F. Custom
- Blackwood
- Posts: 778
- Joined: Fri May 01, 2009 9:13 pm
- Location: Brisbane
- Contact:
Re: Ken Parker Guitars
OK, now I'll admit I'm getting a bit lost. As a side, I just read that his instruments weigh in at a very impressive 1.58kg (3.5lbs) completed unit! That is very light for an archtop guitar...
Jeff, I agree with both you and Dom in that the tenon of the neck would be inherently the weak point; what I was suggesting is that it should be able to be accounted for with design. Can you explain (preferably via a rough diagram!) what you have in mind when you say this though... "I would imagine there would be some sort of bolt fixing through the neck under the fingerboard into the tenon at the headstock side and at the bridge side." I'm not sure my visualization of this is the same as what you mean. I would assume there is still a truss rod in these necks for a start?
Kim - likewise, I'm not following what you mean in... "...CF foot which the riser block is attached to or part off. Like a one piece unit which is bonded to the underside of the top extending toward the back for a little way but also extending forward to meet the side right at the front of the guitar where it turns 90 degree, the strap button is probably used to lock the whole thing in place stabilizing the block and top so that the adjustment can work from the back." Diagram? In that last picture you added, do you think this is the carbon itself showing or another decorative finish? If the carbon, does it provide any clue as to how it is constructed with those more familiar to carbon?
Matthew - I don't think it would be impossible to lay the veneer this perfectly - A square hole matching the tenon could be cut in the veneer and act as a locating point before it is glued to the neck, possibly with vacuum. Of course, having not tried this, it is purely speculation and it may still yet be two pieces as you suggest.
Puff - Perhaps it is none of my business and you are welcome to say so if you feel, but why the deleted posts? I can't think of anything you said having been deemed offensive towards Ken Parker (possibly Kim though); nor anything that may be detrimental to your own work... Curious.
Allen - With respect to the Douglas Fir, if this is the case, do you think just a single carbon skin would make this neck joint strong enough? Particularly if the core of the tenon of the neck is a separately attached piece as you suggest? Two timber members joined in this fashion with just a carbon skin would still seem a bit risky to me? Perhaps I underestimate the strength carbon would give in this. Do you feel from your experience with carbon this would be adequate?
I've a good friend and colleague that has built in a similar fashion to that you mention Allen and I'm not aware of anyone else doing this. He has built at least two if not more, solid body guitars made wholly (that is, body and neck) of solid spruce with a carbon skin over the entire unit. He does not then skin in a timber veneer, preferring the Carbon look for these instruments. Pictures demonstrate it better, but they are very impressive - incredibly light, strong and resonant. The style allows him to build in access and contours that would be impractical otherwise.
Finally, if anyone is wanting to experiment, this company sells both Carbon tow and Aramid/Kevlar Tow in the thread counts usually used in luthiery. They also sell some cloth, tape, rod and tube. Just a local supplier as I believe some of you had bought overseas previously.
http://www.carbonfiber.com.au/
Cheers,
Jeremy.
Jeff, I agree with both you and Dom in that the tenon of the neck would be inherently the weak point; what I was suggesting is that it should be able to be accounted for with design. Can you explain (preferably via a rough diagram!) what you have in mind when you say this though... "I would imagine there would be some sort of bolt fixing through the neck under the fingerboard into the tenon at the headstock side and at the bridge side." I'm not sure my visualization of this is the same as what you mean. I would assume there is still a truss rod in these necks for a start?
Kim - likewise, I'm not following what you mean in... "...CF foot which the riser block is attached to or part off. Like a one piece unit which is bonded to the underside of the top extending toward the back for a little way but also extending forward to meet the side right at the front of the guitar where it turns 90 degree, the strap button is probably used to lock the whole thing in place stabilizing the block and top so that the adjustment can work from the back." Diagram? In that last picture you added, do you think this is the carbon itself showing or another decorative finish? If the carbon, does it provide any clue as to how it is constructed with those more familiar to carbon?
Matthew - I don't think it would be impossible to lay the veneer this perfectly - A square hole matching the tenon could be cut in the veneer and act as a locating point before it is glued to the neck, possibly with vacuum. Of course, having not tried this, it is purely speculation and it may still yet be two pieces as you suggest.
Puff - Perhaps it is none of my business and you are welcome to say so if you feel, but why the deleted posts? I can't think of anything you said having been deemed offensive towards Ken Parker (possibly Kim though); nor anything that may be detrimental to your own work... Curious.
Allen - With respect to the Douglas Fir, if this is the case, do you think just a single carbon skin would make this neck joint strong enough? Particularly if the core of the tenon of the neck is a separately attached piece as you suggest? Two timber members joined in this fashion with just a carbon skin would still seem a bit risky to me? Perhaps I underestimate the strength carbon would give in this. Do you feel from your experience with carbon this would be adequate?
I've a good friend and colleague that has built in a similar fashion to that you mention Allen and I'm not aware of anyone else doing this. He has built at least two if not more, solid body guitars made wholly (that is, body and neck) of solid spruce with a carbon skin over the entire unit. He does not then skin in a timber veneer, preferring the Carbon look for these instruments. Pictures demonstrate it better, but they are very impressive - incredibly light, strong and resonant. The style allows him to build in access and contours that would be impractical otherwise.
Finally, if anyone is wanting to experiment, this company sells both Carbon tow and Aramid/Kevlar Tow in the thread counts usually used in luthiery. They also sell some cloth, tape, rod and tube. Just a local supplier as I believe some of you had bought overseas previously.
http://www.carbonfiber.com.au/
Cheers,
Jeremy.
Re: Ken Parker Guitars
Yes, to avoid the truss rod I would imagine you would need to have a screw from the neck into each corner of the top of the tenon. I had forgotten about the truss rod.
I dont know if that's how he actually does it or not.
I dont know if that's how he actually does it or not.
Re: Ken Parker Guitars
Puff has deleted all of his post in response to a PM I had sent him requesting that he make no more comments of a personal nature to anyone in the open forum. He has been asked not to do this before by Bob and I reminded him of that in what I thought was a polite manner. I have since posted copy my message to Puff in the moderators forum as I wish to dispel any thought that I was heavy handed.
So that everyone is aware, I did not make my request on a personal level as a reaction to being particularly offended by Puff's comment that was directed at me, my skin is a little thicker than some. I made the request as an administrator of this forum wishing to keep the piece and avoid the inevitable trouble that personal comments within the open forum do cause. I did try to explain that to Puff in a open hearted and reasonable manner, but he has not taken my comments in the way I had intended them to be delivered (see what I mean Puff?) and instead has sent me a PM advising he will not be posting at the ANZLF again.
Hopefully we can now move on.
Cheers
Kim
So that everyone is aware, I did not make my request on a personal level as a reaction to being particularly offended by Puff's comment that was directed at me, my skin is a little thicker than some. I made the request as an administrator of this forum wishing to keep the piece and avoid the inevitable trouble that personal comments within the open forum do cause. I did try to explain that to Puff in a open hearted and reasonable manner, but he has not taken my comments in the way I had intended them to be delivered (see what I mean Puff?) and instead has sent me a PM advising he will not be posting at the ANZLF again.
Hopefully we can now move on.

Cheers
Kim
- DarwinStrings
- Blackwood
- Posts: 1873
- Joined: Thu Nov 13, 2008 10:27 pm
- Location: Darwin
Re: Ken Parker Guitars
I wonder if that tenon off the neck doesn't just slide up and down in a straight wooden mortise. provided the heal block grain orientation is parallel to the neck so that the tenon comes up against end grain that end grain would be pretty hard wearing and if it did wear a little over time due to constant adjustment you would only have to adjust the neck a little further away from the body to get the action you want. I may wear a little of that gold gilding off though. I also get the feeling that the CF around the tenon must extend into the neck in some way that avoids clashing with a truss rod.
Jim
Jim
Life is good when you are amongst the wood.
Jim Schofield
Jim Schofield
Re: Ken Parker Guitars
Here is a quote from one article that I was reading.
As far as my really limited experience goes with CF laminations, I don't doubt that the single layer layed up over that join would be very strong. Whether it's strong enough for steel string tension I really don't know.
And the link to the entire article hereThe most arresting detail of Parker's new work is his neck-to-body joint. The core of the neck is lightweight Douglas fir, which he covers with a thin veneer made of the same wood as the guitar's back and sides. Carbon fibers are sandwiched between these two elements and flow together at the end of the neck to form a square pin. The pin fits closely into the body's minimal neck block, and action height can be adjusted with a screw at the back of the body. This arrangement has many benefits. On a normal archtop, bridge height is adjustable to suit a player's action preference. But Parker believes that without the complexity of adjusters, he can make a better-sounding bridge, a simpler, lighter part that does a better job of delivering the complex energy of the strings to the top. "Having the action adjustable at the neck eliminates compromises," he says, "and I can make a bunch of bridges to see which works best—make them hollow to reduce weight. I've got some options." Because there is no heel and the cutaway is extended toward the center of the guitar, players have unprecedented access to the upper reaches of the fretboard. The neck can be easily removed, so Parker can build a different neck (for a different scale, a baritone, a seven-string, etc.) for any guitar body and players can switch between them as they like.
As far as my really limited experience goes with CF laminations, I don't doubt that the single layer layed up over that join would be very strong. Whether it's strong enough for steel string tension I really don't know.
Re: Ken Parker Guitars
Thanks for that link Allen
Unfortunately that description of the joint is very journalistically vague. And probably deliberately so.
Maybe there is some sort of curved flange on top of the riser tenon, fixed to the neck and hidden by the veneer.
Only guessing at this stage.
Unfortunately that description of the joint is very journalistically vague. And probably deliberately so.
Maybe there is some sort of curved flange on top of the riser tenon, fixed to the neck and hidden by the veneer.
Only guessing at this stage.
- DarwinStrings
- Blackwood
- Posts: 1873
- Joined: Thu Nov 13, 2008 10:27 pm
- Location: Darwin
Re: Ken Parker Guitars
I thought the article was suggesting something like the drawing on the left but I was guessing it would be more like the one on the right. The black being the C.F.
Jim
Jim
Life is good when you are amongst the wood.
Jim Schofield
Jim Schofield
Re: Ken Parker Guitars
My take of a few of the descriptions I've read (all a little bit vague) is that it was like the one on the left Jim.
-
- Blackwood
- Posts: 775
- Joined: Tue Aug 27, 2013 6:36 pm
- Location: North East Victoria
Re: Ken Parker Guitars
I have read some of this old post re Ken Parker designs from 2010. Here is a link to a luthier who is doing a similar neck adjuster, complete with pics. Also note the CF stiffener on the fingerboard extension..http://www.martinkeithguitars.com/const ... ails.shtml#
-Ross
-Ross
"Everything I say on the topic is based solely upon inexperience and assumption!"
- christian
- Blackwood
- Posts: 338
- Joined: Wed Oct 20, 2010 10:31 am
- Location: Bay of Islands NZ
- Contact:
Re: Ken Parker Guitars
Interestingly enough my friend is bringing his guitar and Ken over to meet me tomorrow! So if there is something particular that you want to know flick
me through some questions.
Christian.
me through some questions.
Christian.
Why does the eye see a thing more clearly in dreams than the imagination when awake?
Leonardo da Vinci
www.christiandruery.com
Leonardo da Vinci
www.christiandruery.com
-
- Blackwood
- Posts: 775
- Joined: Tue Aug 27, 2013 6:36 pm
- Location: North East Victoria
Re: Ken Parker Guitars
Hi there Chris...I had a look at your website..I like your cored bracing, your Black Mamaku rosettes! Lovely workmanship! (But I am a little concerned re the bandsaw without the guard fitted!)
Well, to take you up on your offer, I would like to know Ken Parkers bracing ideas, and of course more details on the neck adjuster and the neck building process...cheers! Ross
Well, to take you up on your offer, I would like to know Ken Parkers bracing ideas, and of course more details on the neck adjuster and the neck building process...cheers! Ross
"Everything I say on the topic is based solely upon inexperience and assumption!"
- slowlearner
- Blackwood
- Posts: 389
- Joined: Tue Jan 10, 2012 8:43 pm
- Location: Hawkesbury, NSW
Re: Ken Parker Guitars
Well I've been think about this neck attachment. Needed to do something similar for a long scale 6 string bass (36" scale). Here's my current design to allow for adjustment in both action and break angle.

It's ERW tube with threaded inserts.

It's ERW tube with threaded inserts.
Pete
- Nick
- Blackwood
- Posts: 3628
- Joined: Thu Feb 26, 2009 11:20 am
- Location: Christchurch, New Zealand
- Contact:
Re: Ken Parker Guitars
How do your cap screws work Pete? Are they threaded in the block on your outer tube and just push the inner tube up or are you threading into the inner tube?
"Jesus Loves You."
Nice to hear in church but not in a Mexican prison.
Nice to hear in church but not in a Mexican prison.
- slowlearner
- Blackwood
- Posts: 389
- Joined: Tue Jan 10, 2012 8:43 pm
- Location: Hawkesbury, NSW
Re: Ken Parker Guitars
There's a threaded block welded into the end of the inner tube. The screws wind the inner tube up and down in the outer tube. Sorry, will have to fix the drawing to make that clearer.
Pete
- Nick
- Blackwood
- Posts: 3628
- Joined: Thu Feb 26, 2009 11:20 am
- Location: Christchurch, New Zealand
- Contact:
Re: Ken Parker Guitars
Don't apologise! Just as long as you know what's going on.slowlearner wrote:There's a threaded block welded into the end of the inner tube. The screws wind the inner tube up and down in the outer tube. Sorry, will have to fix the drawing to make that clearer.

So how are the screws 'captured' in the block on the outer tube?
"Jesus Loves You."
Nice to hear in church but not in a Mexican prison.
Nice to hear in church but not in a Mexican prison.
- slowlearner
- Blackwood
- Posts: 389
- Joined: Tue Jan 10, 2012 8:43 pm
- Location: Hawkesbury, NSW
Re: Ken Parker Guitars
^ I'll weld in a piece of thick steel plate with a threaded hole cut in it.
Pete
Re: Ken Parker Guitars
Just my two-penneth folks - if I was laying up a fir and CF neck I'd make it an I-beam variation. Two layers of CF flat material above and below a fir central section, with a thinner piece, say 4 or 5mm outside of those. Much easier to lay up, easier to lay up the cf onto the square "heel," easier matching up the edge to the fretboard.
Or you could embed a threaded insert into the fir to bolt the heel into. Lots of options.
Then you'd carve it like a regular neck, then veneer it. It would be stiff, but not so stiff the truss rod would be rendered useless.
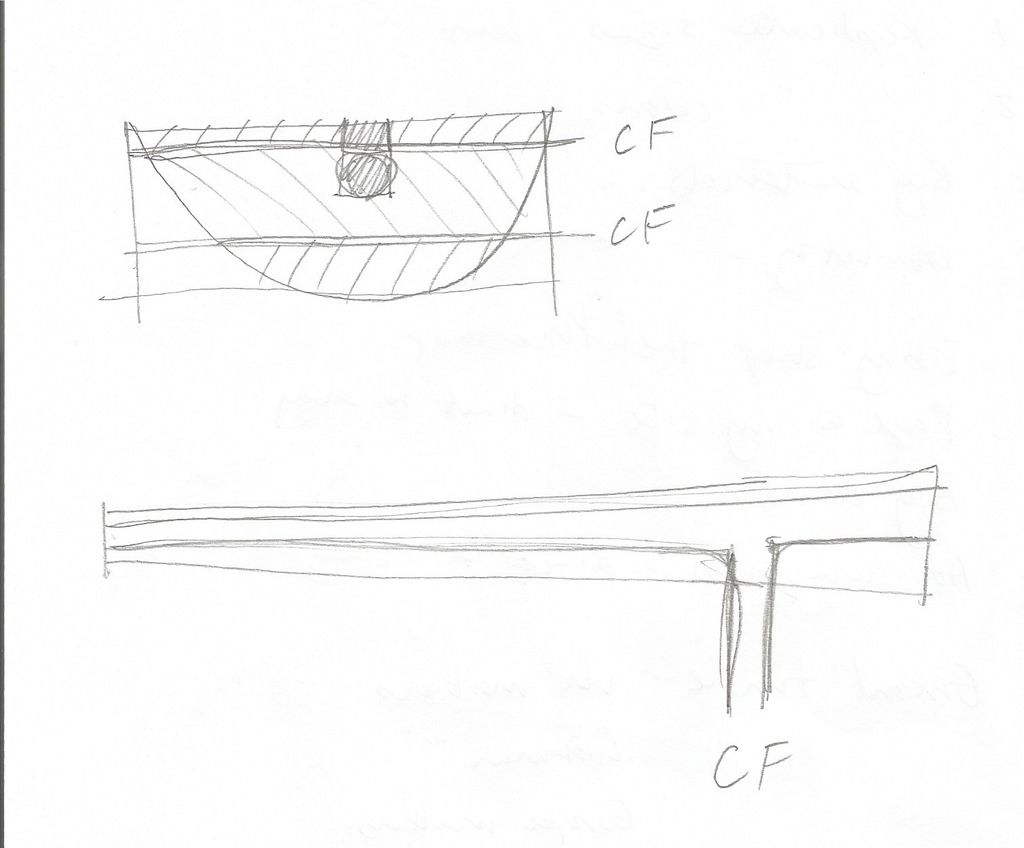
Or you could embed a threaded insert into the fir to bolt the heel into. Lots of options.
Then you'd carve it like a regular neck, then veneer it. It would be stiff, but not so stiff the truss rod would be rendered useless.
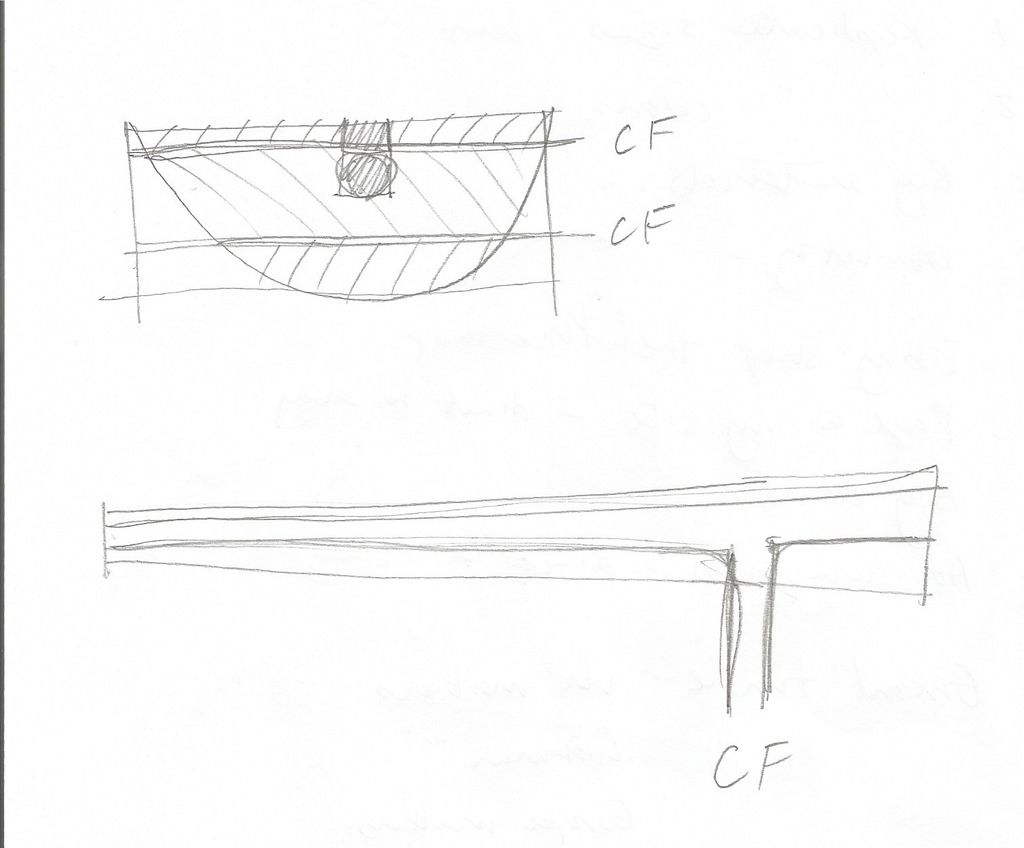
Who is online
Users browsing this forum: No registered users and 59 guests