I have been working my way up toward the more interesting aspects of this guitar. Building jigs and forms is not my favorite thing and if there are templates, bending forms and molds available I will happy give the fine people who make them my business. Like the harp ukulele I made I am in the situation where I need to make the entire set of templates, molds and bending forms. Thank goodness for the copying shop, I made copies of the plans, cut them up, glued them to the plywood or Plexiglas and went to work with my band saw and sanders.
This last week I made my first scarf joint neck blank. I have been cutting necks out of single pieces of wood. I have sort of been scared of the joint as I can not cut a straight line on the band saw. Luckily my kids bought me a miter guide for my band saw. I could not cut a 15° with it but I cut some plywood at a 45 degree angle allowing to set and hold my scarf angle. It actually worked and I got a clean cut. Here are pictures of the process, including my bone headed screw up.
First I used my jointer plan to square the wood,
Then I cut a 45° angle to use as a guide for the miter. Just to be sure I made a test scarf cut on some scrap plywood
Not sure what I was afraid of the cut when as good as it could on the bandsaw and I just need ot to do a little clean up. I lined up the cut angled pieces and clamp them with a sacrificial piece of MDF, and planed the gluing surface of the joints clean and flat
I used my shooting board and some clamps to hold the joint in place and really glued it with some heavy duty clamps.
I had a big block for the heal so I cut it into two heel blanks. Here again I planed the surfaces flat and used some real clamps to glue the heel on the neck.
Here is where the bone head maneuver came in to play. I very carefully set up the router table for a truss rod slot right up the center of the neck blank. Then proceed to start the route before tightening the router table fence. Oh well. I cut a strip of mahogany planed it and shaped it to fit in the miss-cut slot. It fit in so nicely that I just wicked in some CA. I reset the table a made a proper slot. No one will see this fix, unless they are changing the fret board in the future for a repair.
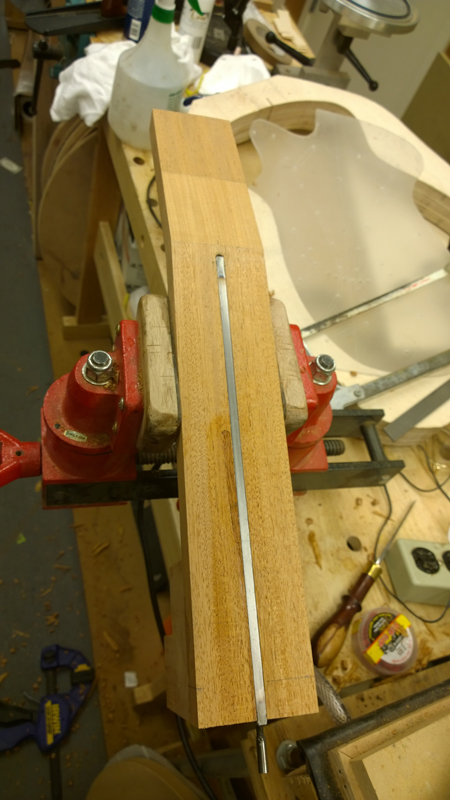
.
I also installed an extra amboyna rosette I made as an option for a previous guitar.
To insure proper bridge and sound hole alignment, and given that I need to drill the peg holes early in the bracing process. I used the template to drill some of the peg holes and the center of the rosette.
I did not do any fancy measurements I just used the router and it fine adjustment to sneak up of the slot I need for the rosette and a couple of thin bwb purflings.
All and all uneventful
I routed the sound hole such that it should be close to dropping out when the top is the correct thickness.
Once very close to the proper thickness I made a 3 mill mylar to cover for the top to protect it during bracing.
I spent the rest of the weekend preparing to do the top bracing. The last photo shows why I need to drill the peg holes so early; the main braces passes between two peg holes.
